What it is about
In this article, we provide a comprehensive explanation of TPM (Total Productive Maintenance) and explain its added value for companies - especially with reference to the Operations1 software solution. The following questions are addressed in the post:
- What is TPM (Total Productive Maintenance)?
- The 8 fields of action of TPM
- What are the advantages and disadvantages of TPM on the shopfloor?
- How can TPM be implemented?
- Operations1 as a standard software solution for TPM
What is TPM (Total Productive Maintenance)?
Anyone working in production, especially in maintenance, cannot get past the term Total Productive Maintenance, or TPM for short. What is behind this concept, which is already over fifty years old and originated in Japan?
Total Productive Maintenance Definition
Total Productive Maintenance is a term with a long history dating back to the 1950s. It refers to a concept in maintenance that aims to increase equipment effectiveness and the service life of equipment, thus realizing a production system that is as trouble-free as possible. Effective, cost-optimized maintenance is intended to eliminate losses and waste so that "zero defects", "zero failures", "zero accidents" and "100 percent quality" are ensured.
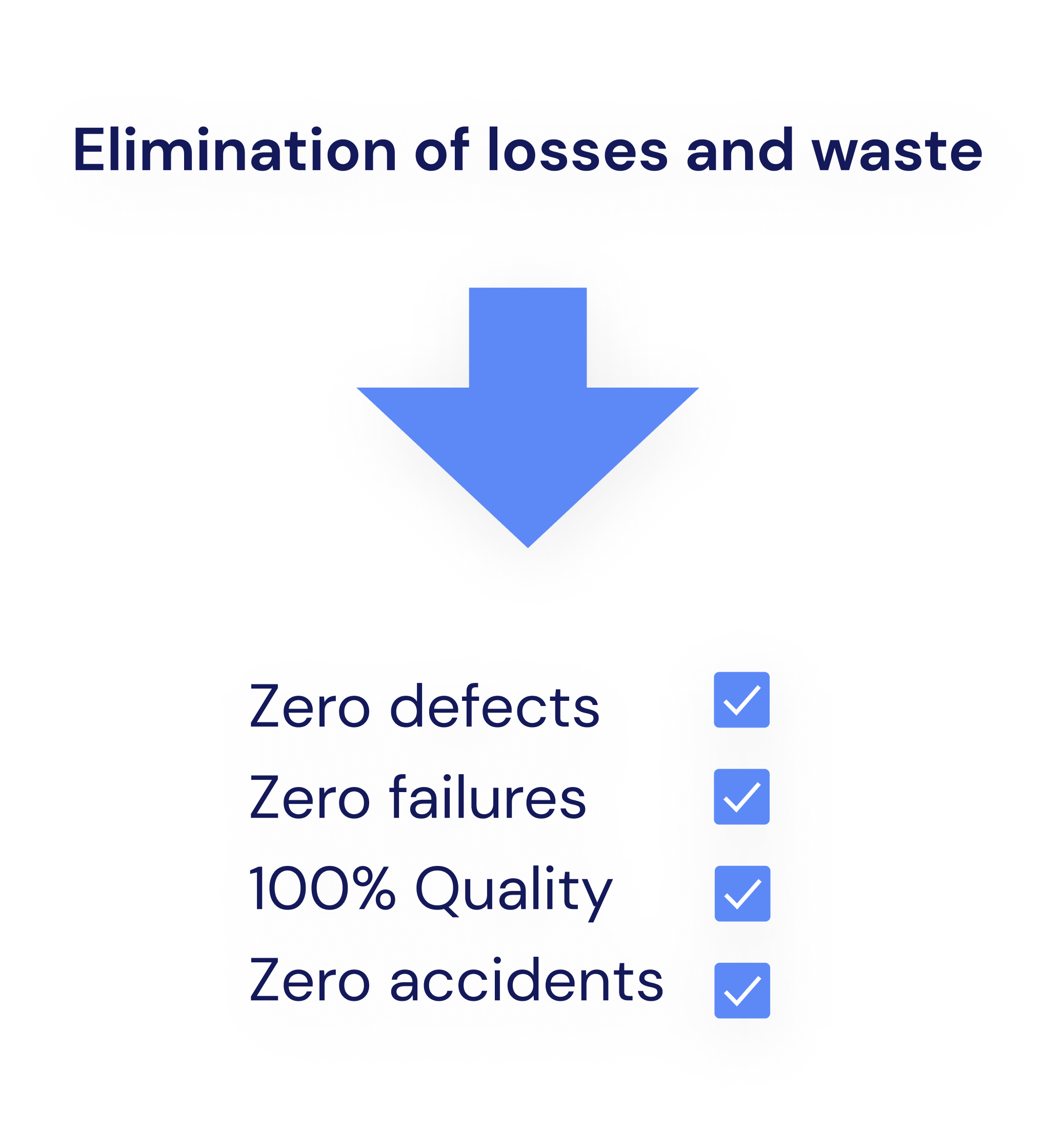
The key idea behind the TPM concept is to give manufacturing employees more responsibility by actively involving them in improvement activities and not just leaving them to the maintenance team. In this way, improvement measures can be implemented at the point of action and directly incorporated into the continuous improvement process.
Interdisciplinary plant maintenance can reduce downtime to an absolute minimum and thus improve the effectiveness and availability of the plants. The overall plant effectiveness as a whole is also increased as a result.
The origins of Total Productive Maintenance
The term "Total Productive Maintenance" goes back to the Japanese Seiichi Nakajima. The concept was first introduced in the late 1960s by the Japanese automotive supplier Nippon Denso (now Denso), the second largest member of the Toyota Group. Denso developed the TPM concept in four stages: Reactive Maintenance → Preventive Maintenance → Autonomous Maintenance → Total Productive Maintenance.
While "reactive maintenance" involves restoring the machine to a normal operating condition after failure, the concept of "preventive maintenance" places the responsibility for maintaining production equipment solely on the maintenance department. At Denso, this has resulted in a significant reduction in plant downtime.
With increasing automation and a high number of automated production lines, it became necessary to take a more sustainable approach to maintenance. Therefore, the Japanese automotive supplier decided to train machine operators to perform maintenance work autonomously - the concept of "autonomous maintenance" emerged.
The positive experience with autonomous maintenance eventually led to the development of Total Productive Maintenance, which focuses on the cooperation of all employees to maintain operating resources and high-quality production.
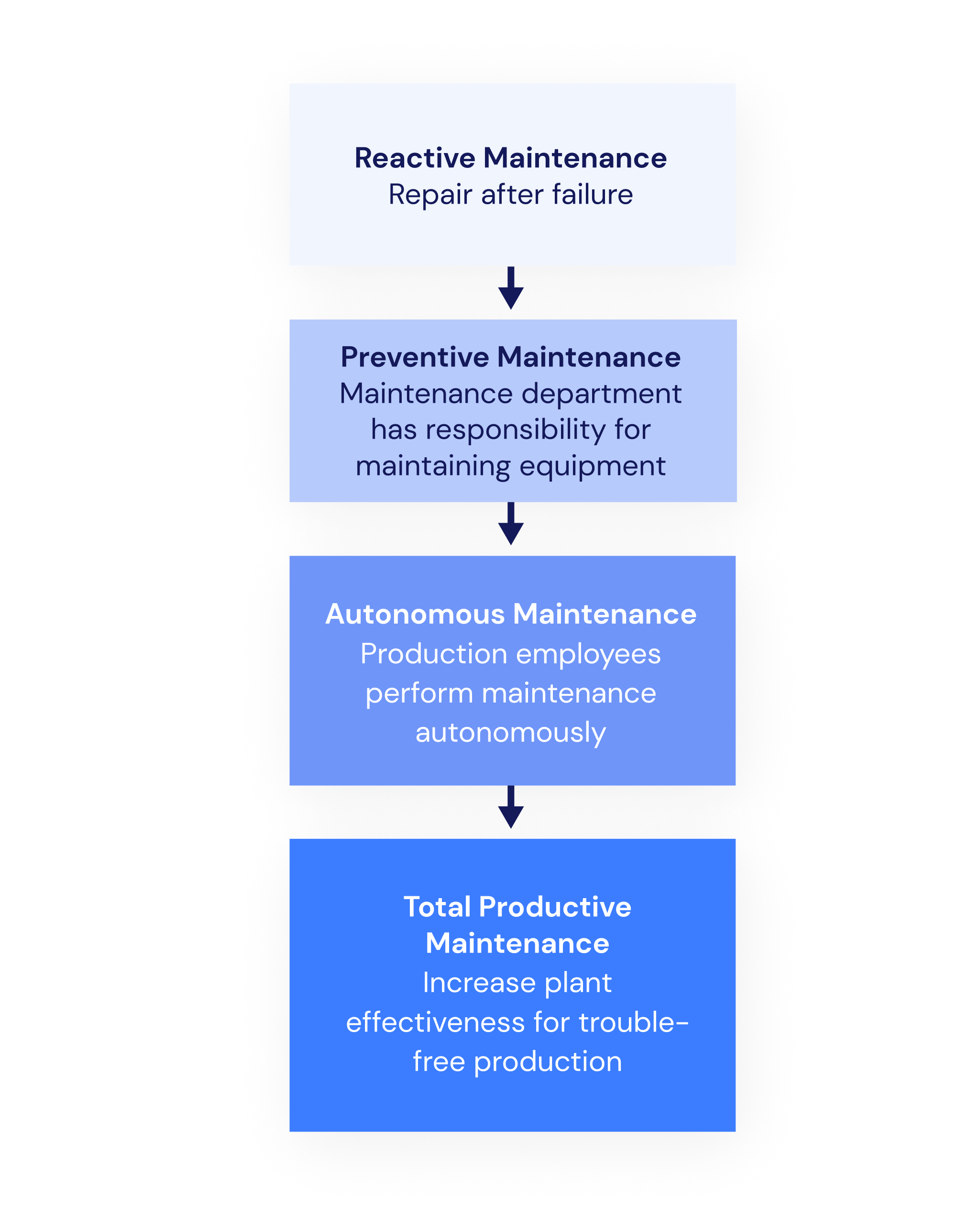
The 8 fields of action of TPM
Total Productive Maintenance follows the approach of holistic plant management. Based on this, 8 fields of action have developed in which TPM is realized:
Continuous Improvement
Autonomous Maintenance
Preventive Maintenance
Competence Management
Quality Maintenance
Ramp-up Management
TPM in Administrative Areas
Work Safety, Health and Environmental Protection
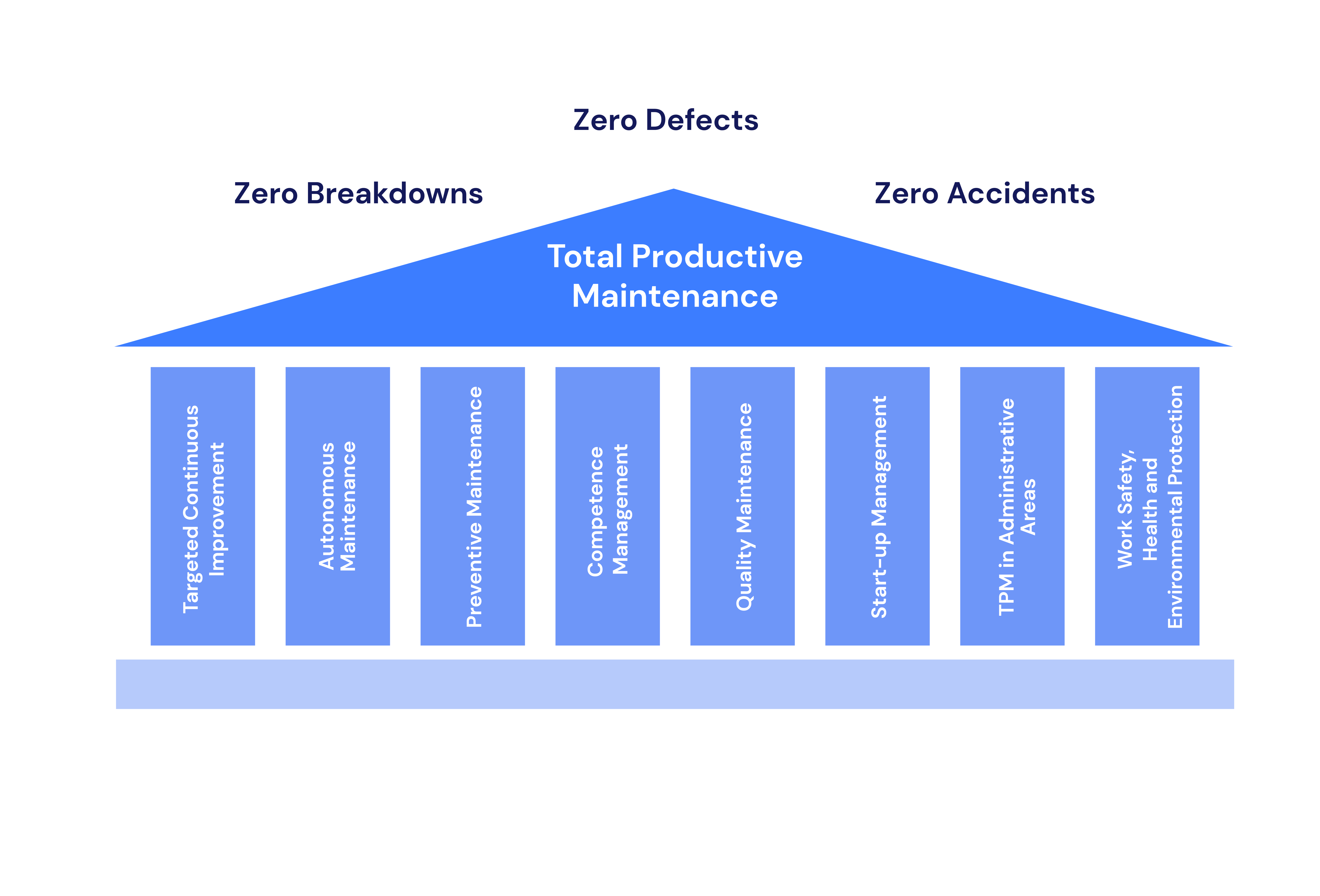
1. Continuous Improvement
Targeted Continuous Improvement is the first pillar of TPM. It is based on all regular activities to eliminate a total of 16 types of losses that affect the smooth interaction between machines and systems, employees and resources. The graphic illustrates this.
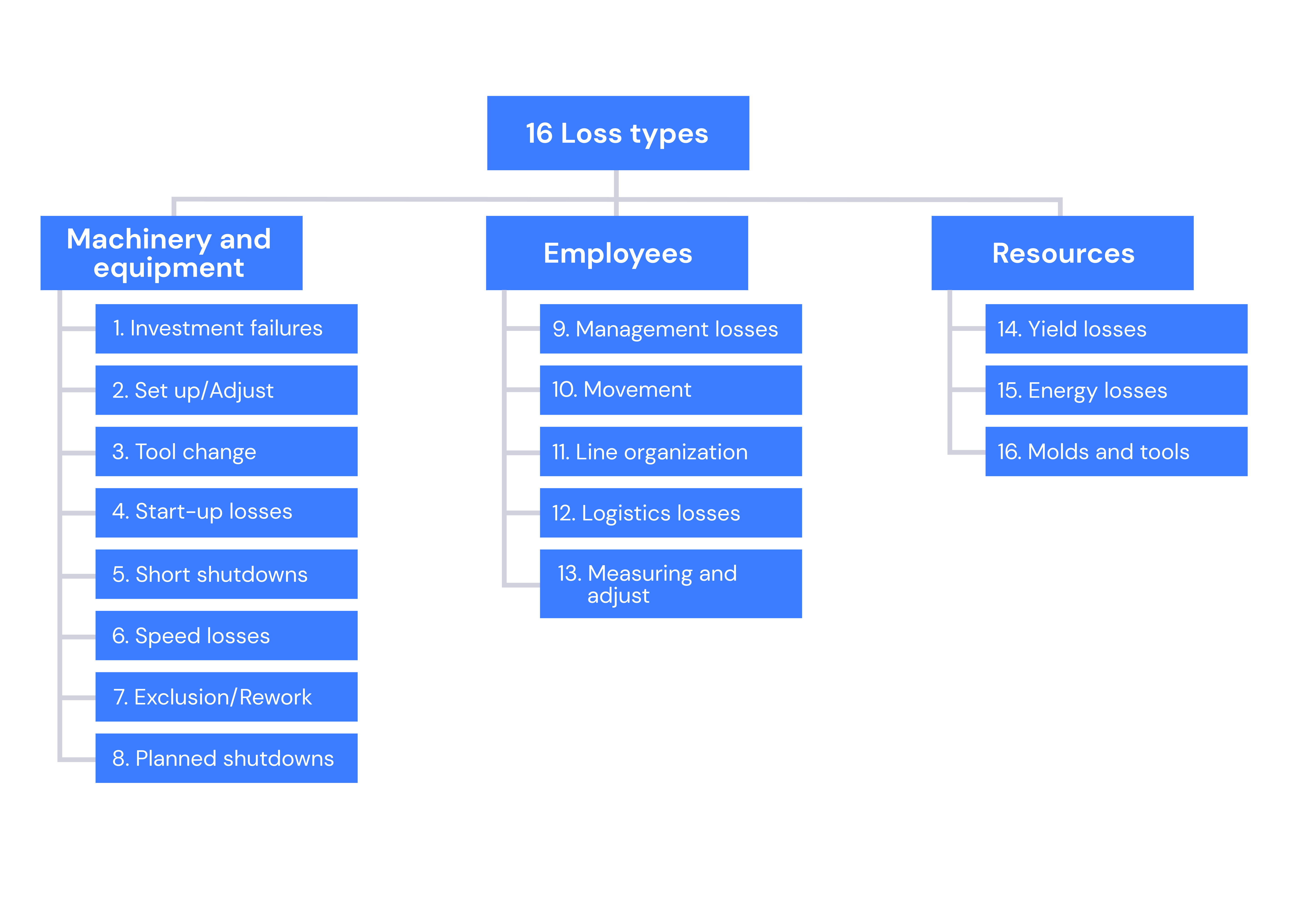
These include, for example, short stops and malfunctions at plants, safety aspects, consumer complaints and changeover times. Targeted continuous improvement is based on the conviction that constant optimization in small steps increases the competitiveness of companies. In this way, throughput times can be reduced, costs cut and quality optimized. This approach also makes it possible to identify trends at an early stage and respond to them appropriately. The model for continuous improvement is the Japanese Kaizen.
Our blog post "How to automate the CIP with software" will give you more valuable insights on how to successfully implement continuous improvement.
2. Autonomous Maintenance
Autonomous Maintenance is the second field of action of Total Productive Maintenance. It states that minor maintenance, inspection, cleaning and lubrication work is carried out by the machine operator himself rather than by highly specialized technicians. If employees on production lines have greater personal responsibility for their plant and are made aware of early fault detection, this will help maximize the efficiency of machines and plants in the long term. This also relieves the maintenance staff, who can direct their focus instead to complex maintenance measures and their optimization options.
3. Preventive Maintenance
The third field of action of TPM, Preventive Maintenance, focuses on the planning and implementation of maintenance measures even before a system shows signs of damage. This is intended to minimize failures and downtimes and increase the effectiveness and availability of the machines. The result is a paradigm shift in which the work process is no longer subject to a reactive approach but to a holistic preventive approach - with numerous long-term benefits for the company: Unpredictability is counteracted, interruption of production is avoided, and the overall service life of the equipment is increased. Preventive maintenance is thus an essential criterion for future-proof, resilient production.
The success of preventive maintenance can be measured by two key figures: MTTR (= mean time to repair) and MTBF (= mean time between failures). The goal is to minimize MTTR and maximize MTBF.
4. Competence Management
A key factor for Total Productive Maintenance is the fourth pillar of TPM, Competence Management. At its core, this involves well-trained employees and motivated managers. The aim is to train employees in such a way that they are able to carry out operating and maintenance measures in a qualified manner. Competence management thus forms the prerequisite for all other pillars of TPM.
5. Quality Maintenance
The fifth component of Total Productive Maintenance, Quality Maintenance, focuses on all measures that not only maintain but also increase product quality and process reliability. The areas of production, development and maintenance are closely interlinked here and are based on the principles of "zero losses," "zero machine failures," "zero rejects" and "zero defects. Quality maintenance is aimed at ensuring that the quality achieved is the result of ideal machine conditions. These should be set in such a way as to avoid defects and produce consistently high quality - the basis for customer satisfaction and loyalty. To prevent quality problems from occurring in the first place, quality maintenance includes the following tasks:
Setting quality standards
Implementation of systems for early identification of defects and errors
Trend analyses
Implementation of systems for defect and error prevention
Poka-yoke principle based on the avoidance of unintentional errors
Implementation of a quality management matrix
6. Ramp-up Management
The sixth component of Total Productive Maintenance is Ramp-up Management. It aims to ensure a lean start-up curve for new products and plants so that the market can be served quickly. The following parameters are required for this to succeed smoothly:
Early planning of new products, processes and plants
Early involvement of suppliers in planning
Shortening of development times for products, processes and plants
Shortening of start-up times for new products, processes and plants
Consideration of information to avoid maintenance
Plant planners, designers, maintenance and production staff are all involved in startup management. The closer these stakeholders are networked with each other, the better the implementation of the sixth pillar of Total Productive Maintenance will succeed.
7. Total Productive Maintenance in Administrative Areas of the Company
TPM is also being used in Administrative Areas of the Company. This affects departments such as purchasing, logistics and human resources. The proven "5S philosophy" of Lean is applied here in the sense of sorting, systematizing, cleaning, standardizing and self-discipline. TPM is also implemented in the office area. The processes there are made visible with suitable tools and aligned with value creation and efficiency. The aim is to ensure that important information reaches the right place at the right time, in the right form and at the lowest possible cost.
8. Work Safety, Health and Environmental Protection
The eighth field of action of TPM serves to achieve "zero accidents" as well as the emission and sustainability targets for the benefit of employees and the environment. To this end, employees are trained accordingly so that they can identify potential hazards in these three areas and take countermeasures in good time. This also includes raising awareness among individual employees. This means, for example, that employees are aware of environmental aspects that are important for the organization's operations and image. This includes factors such as water consumption, pollutant emissions, noise pollution, waste and energy consumption.
In this way, a corporate culture can be established in which productivity within manufacturing and all related functional areas is continuously optimized. Conversely, this means that a good implementation of Total Productive Maintenance always takes into account the employees in addition to the machines and wants to sensitize them to a productive interaction between man and machine.
TPM key figures
In order to be able to measure the success of the eight action areas of TPM with regard to the reduction of waste as well as sustainable efficiency, key figures are tracked in six target categories:
Productivity: labor productivity, value added per person, disruption reduction
Quality: process defects, number of defects, number of customer complaints
Costs: labor reduction, maintenance costs, energy costs
Logistics: inventory quantity, inventory turnover rate
Safety and Environment: number of accidents, sick leave, pollution indicators
Motivation: number of suggestions for improvement, number of small group meetings
The ultimate goal of Total Productive Maintenance is to increase overall equipment efficiency, also known as OEE (Overall Equipment Effectiveness). In order to maximize output (production, quality, deliveries, safety, health, environment and morale) while minimizing input (labor, machinery and materials), TPM aims to favorably influence the following three main factors:
Downtimes (due to set-up times, maintenance or malfunctions)
Cycle losses
Lack of quality
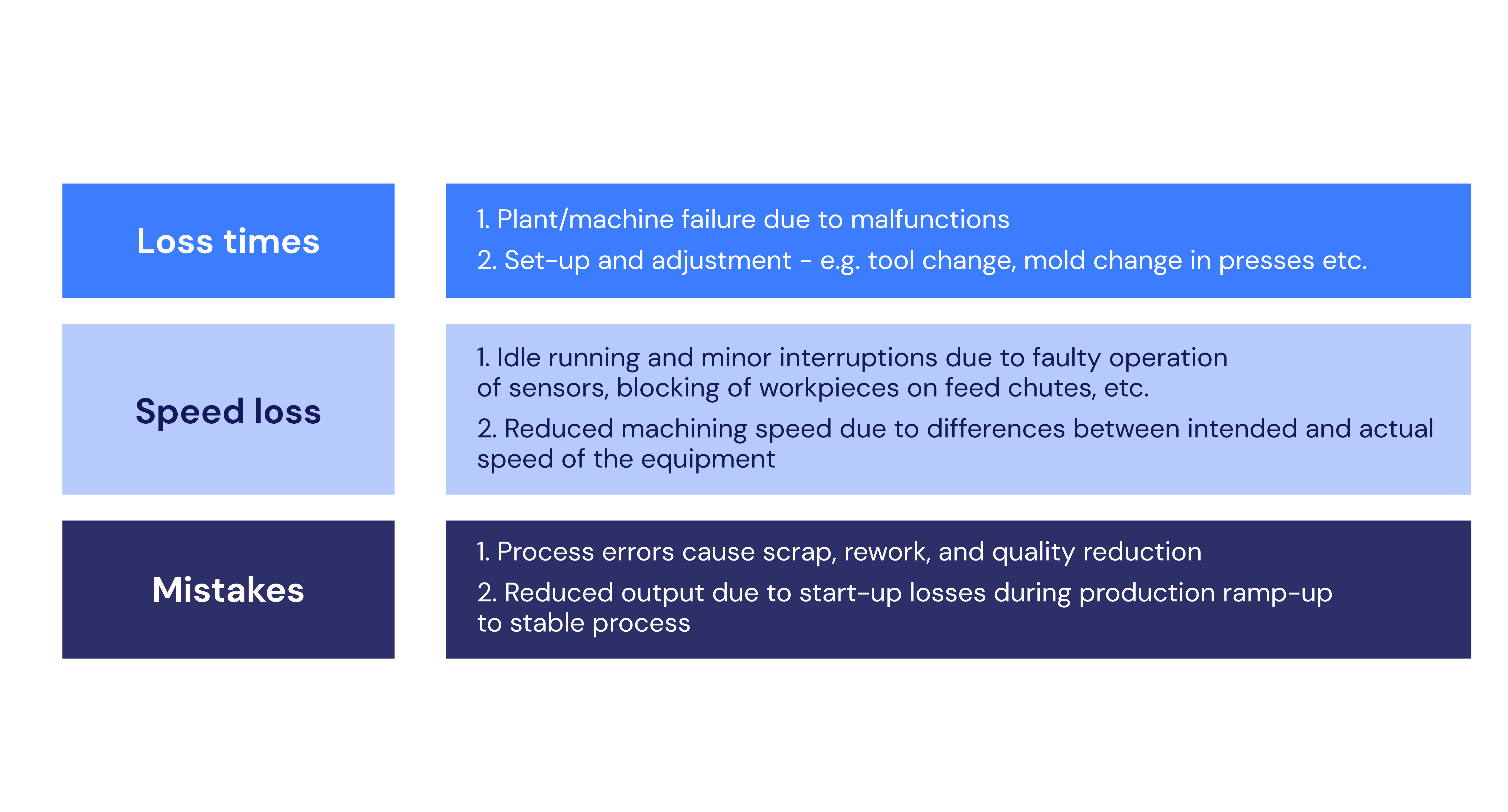
What are the benefits of TPM on the Shopfloor?
In view of the fact that companies today are confronted more than ever with continuously increasing market requirements, maximizing plant availability is a prerequisite for remaining competitive. The implementation of a holistic maintenance program such as the TPM concept is a decisive success factor for this.
The goal of ensuring maximum plant availability with minimum maintenance effort, which is pursued by means of Total Productive Maintenance, thus has numerous advantages on the shopfloor for companies of all sizes:
Reduction of malfunctions & significantly less machine downtime
Reduction of rejects
Reduced setup and set-up times
Increased productivity
Improved control of maintenance costs
Reduced workload of the maintenance department and less dependence on the knowledge of individuals
Improvement of safety standards
Increased employee motivation due to less stressful work and more individual responsibility of each employee
Future security & resilience
Based on the experience of the management consultancy TCW, the following diagram shows two key figures that impressively demonstrate the advantages of Total Productive Maintenance:
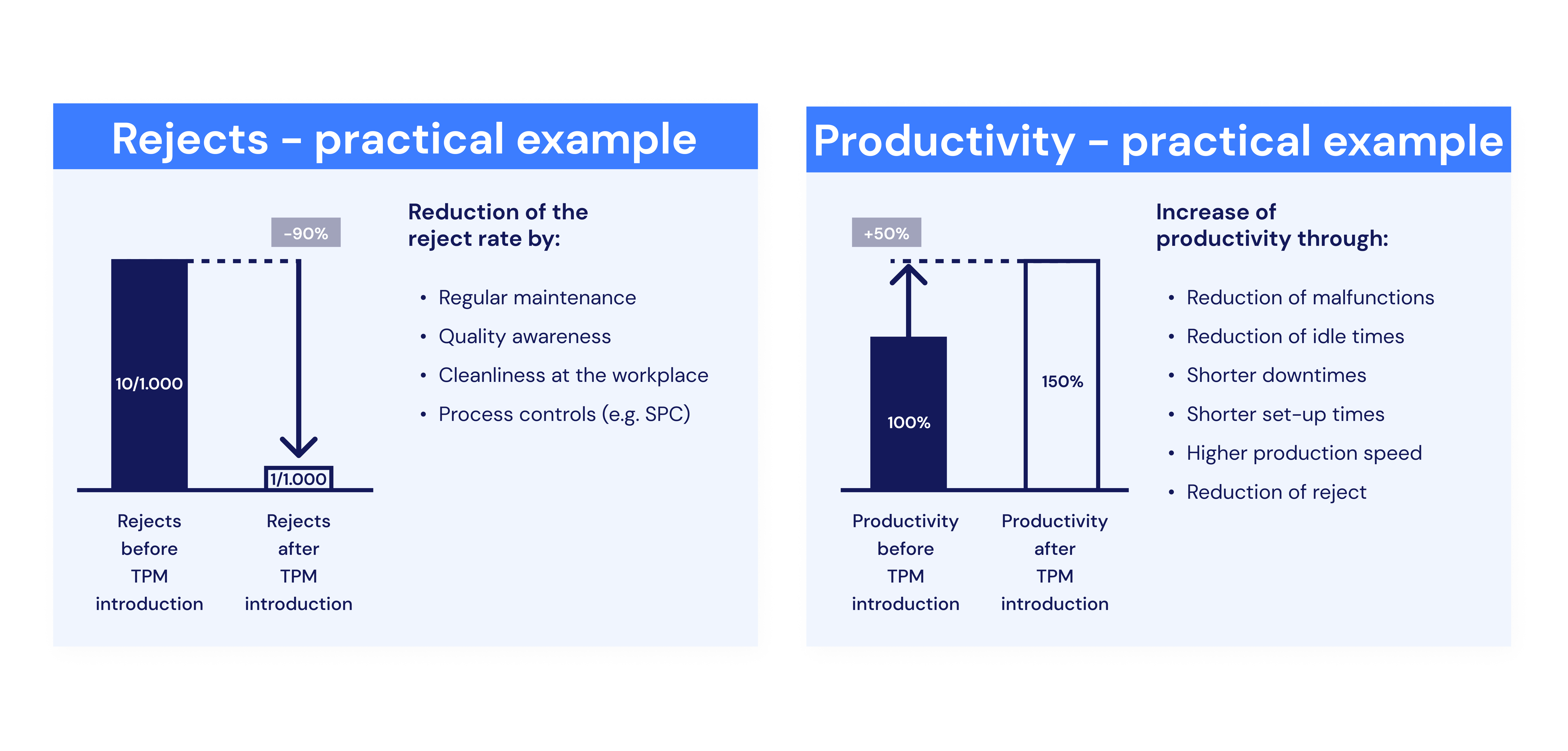
Our customer Hirschvogel, one of the largest global automotive suppliers in the field of solid forming of steel and aluminum, was also able to achieve remarkable results through the use of Total Productive Maintenance. In our Success Story you can read in detail how this was achieved with the help of the full digitalization of all maintenance processes with Operations1 software. We would like to share three key KPIs with you:
-60% reduction of downtime in the international Hirschvogel plants
-50% process deviations
250,000€ savings per site through reduction of external service providers
Disadvantages of TPM
Despite all the advantages, it is legitimate to ask whether Total Productive Maintenance also has disadvantages. The answer to this is clearly yes – provided that the implementation is accompanied by the following circumstances:
Management is not willing to initiate a continuous improvement process with a long ROI, in which all employees contribute their knowledge and skills to sustainably increase value creation.
Management is not willing to invest a lot of time in training and education of their employees. Especially in times of crises and external shocks such as supply chain disruptions, climate events and political grievances, manufacturing companies are faced with major challenges and time is considered a scarce resource.
The company is unwilling to have the patience required to implement Total Productive Maintenance. Since TPM often requires a noticeable change in culture, agile thinking, openness and the willingness to assume a high level of personal responsibility are required on the part of all employees involved.
The central disadvantage of TPM is therefore the effort required for implementation. If implementation is done half-heartedly, this will lead to frustration among all those involved. At the same time, however, TPM can also be introduced pragmatically.
How to implement Total Productive Maintenance?
When introducing Total Productive Maintenance, it is advisable to proceed in several successive steps:
Development of a TPM program with objectives, measures, milestones, deadlines, responsibilities, means
Structuring of the plants, recording of their responsibilities/defects with causes and consequences, derivation of measures
Definition of a pilot area, assignment of activities, training and instruction of plant operators, implementation of measures by stepwise transfer of tasks to the plant operators, recording of results, development of working documents
Evaluation of the pilot experiences, perfection of the work documents, extension of the employee competence up to autonomous maintenance
Implementation of the experiences, transfer to other areas
Processing of the experiences from the pilot areas into specifications, procurement concepts for new plants
It is important that the three different target groups - managers, production employees and maintenance staff - are met individually and that the reasons for introducing Total Productive Maintenance are explained in detail. While the advantages of TPM can be explained to managers in a presentation, production employees should be picked up in the form of on-the-job training. For example, it is a good idea to clean, maintain and start up a production plant according to TPM and have the employees draw a comparison with the current procedure in order to demonstrate the advantages. A special focus when introducing TPM is on the maintenance workers. They must mentally make the biggest cultural change from being a "fire department" to a driving and comprehensive service department with a high level of personal responsibility.
If the TPM method can be understood not as a time-limited project, but as a path that has a beginning but no fixed end, because optimization is never complete, good conditions are created for successful implementation.
Operations1 as the standard software solution for TPM
Today, maintenance employees are often faced with two challenges: Operationally, there are high efforts for planning and verification in maintenance. On the system side, they face extremely complex landscapes, as there is no system support for Total Productive Maintenance to date. Thus, activities such as maintenance planning, machine inspections, HSSE, qualification management & Co. take place in many separate technical solutions or on paper. In parallel, the shortage of skilled workers continues to grow, production processes are becoming more and more complex due to an increasing variety of products, rampant inflation will increase labor costs and Covid-19 has shown the importance of operational resilience in case of external shocks.
Digital Total Productive Maintenance addresses precisely these pain points: Operations1's software solution supports you thanks to its all-encompassing Connected Worker Platform approach, which aims at holistic technological connectivity of the workforce to ensure efficient and future-proof maintenance. Our software covers the four central TPM components of Preventive Maintenance, Autonomous Maintenance, Competence Management and Work Safety, Health and Environmental Protection.
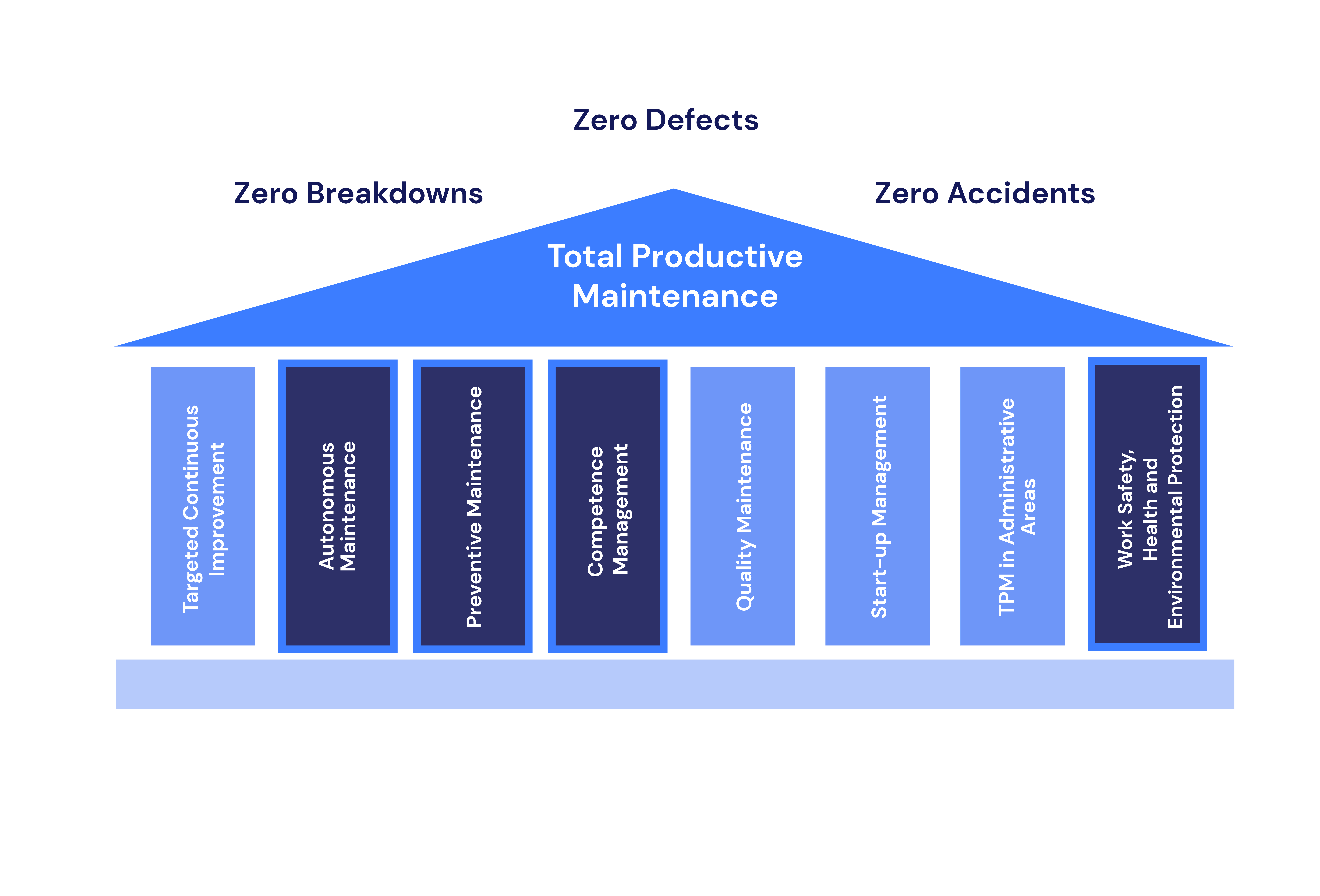
Digital TPM with Operations1 software offers you the following added value:
Maintenance plans can be created for preventive maintenance in Operations1 or you can connect the software solution to your inventory systems ERP, MES or CMMS, respectively
All TPM documents can be managed in all-in-one software
Intuitive checklists with image- or video-based maintenance instructions enable autonomous maintenance
Employee qualifications can be managed
Safety rounds, 6S and health and safety audits can be scheduled and documented
Maintenance reports are generated automatically
Employees can document CIP findings in real time via text, photo, or video
Unexpected incidents can be resolved via task management
Conclusion: TPM is one of the basic components of an effective production system.
Want to get to know Operations1?
Please fill out the contact form with your thoughts and goals. We will get back to you immediately.
Editha Bertsch
Editha is an experienced project management expert for manufacturing companies. With a clear understanding of the specific challenges of the industry, she is passionate about developing innovative solutions.