What it's about
In this blog article, you learn what CIP means, how the typical challenges look like and how to automate the CIP with the help of software.
What is the Continuous Improvement Process (CIP)?
The Continuous Improvement Process (CIP) basically describes the endeavor to optimize processes in short time intervals by means of incremental steps. Process optimization can, for example, relate to increasing quality, reducing cycle times or lowering costs. CIP is integrated as a central element of quality management in the DIN ISO 90001 quality standard. In the certification process, companies must therefore prove that they have established processes and responsibilities that lead to continuous improvements in the provision of services. The model of the CIP is the Japanese Kaizen, which strives for the continuous improvement of all areas of the company. The term Kaizen is composed of “kai” = change and “zen” = change for the better.
Here’s how it works – typical procedure with CIP
1. Basis is the documentation: First of all, processes are captured.
2. At regular intervals, so-called “actual processes”, i.e. standard processes, are then compared to previously defined “target processes”.
3. This is followed by the evaluation and assessment of existing problems.
4. Finally, appropriate solution approaches and measures are derived.
The constant focus should be on customer requirements as well as hypothesis and data based approaches. The best known methodology is the PDCA cycle, which controls all improvement measures from planning to corrective actions.
Challenges in practice: Process adherence
In practice, it often happens that processes are defined in certain tools or documents, but are not executed in a compliant manner. This can lead to scrap metal refinement, for example, because workpieces are not checked correctly and are then processed further. Alternatively, low process adherence can also lead to unnecessary scrap because products are falsely considered defective. This example from quality management can be transferred to all other production-related areas, such as assembly processes or maintenance measures. The lower the process adherence, the higher the costs for poor quality, which are often hidden in general costs. Before an effective CIP can be established, it is essential to document operational processes and ensure that they are followed.
CIP Automation: Optimization of process instructions
If operational processes are supported by digital tools and employees receive the right and understandable information, process adherence increases. Thus, the foundations for CIP are established. But how can the continuous improvement process be established and lived in an agile way? At the first stage, it is very effective to include incremental improvements in the process instruction and to incorporate them in a digital release procedure. In case of digital work instructions and checklists, employee feedback can be retrieved digitally and evaluated at the end of the “Sprint” week. Process adherence can be continuously improved, for example, by requesting more suitable images or videos that describe the process step and by that improve the execution. In addition, images can be edited with arrows and other elements. Adjustments in process instructions, which increase the comprehensibility and the content, represent an absolute quick-win with regard to the continuous improvement process in industrial companies.
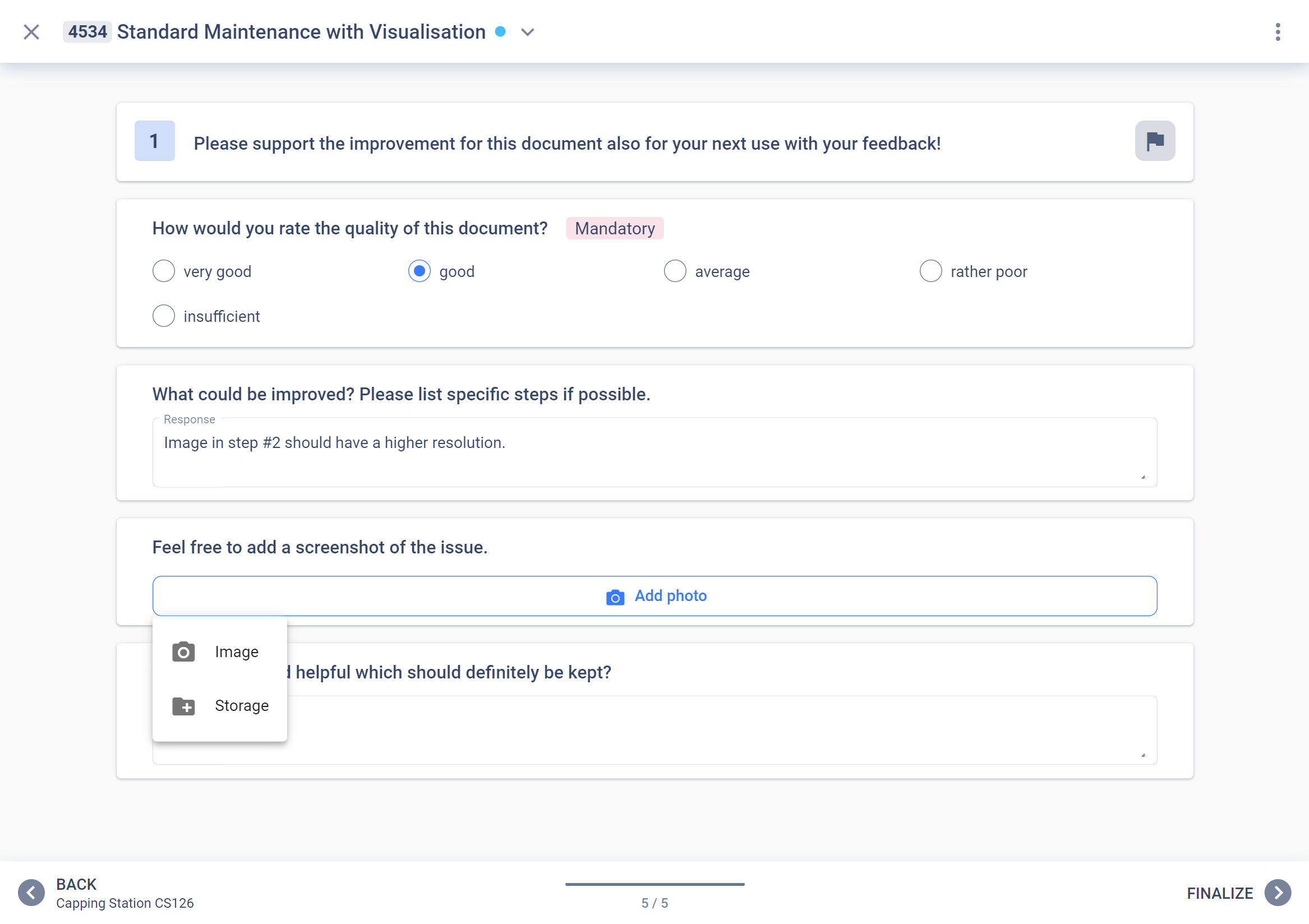
CIP Automation: Optimization of input processes
However, digital checklists can also be easily statistically evaluated to identify the sources of errors and take countermeasures. The input values in the software can be analyzed centrally without extensive statistical knowledge and without manual effort. These findings provide the starting point for more profound improvement projects. Here, the well-known PDCA cycle can be used.
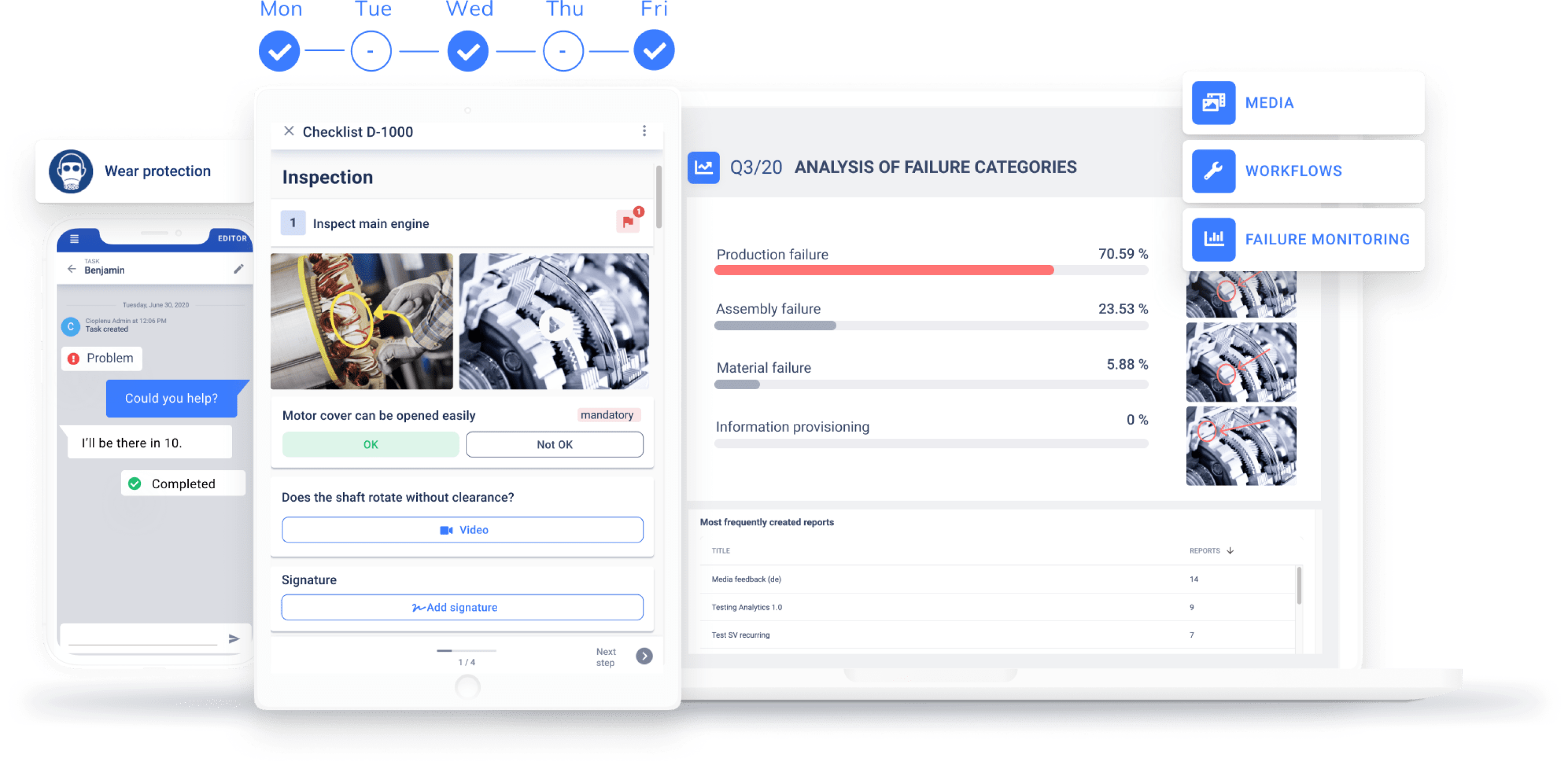
The simplified illustration above shows how return values of the worker generate automatic statistics. With the help of this information, countermeasures can be taken quickly.
The effect: Reduction of error rates
Statistical evaluations, such as those carried out in a globally active mechanical engineering company with over 5000 employees, have shown that the error rate is reduced by 50% within about four months by using a software solution. The blue solid line shows the approximate error rate of weekly maintenance instructions.
Integrating regular feedback into the instructions and evaluating process statistics thus serve the continuous improvement process in a lean and simple way. If the effects of this error reduction are taken into account, enormous cost savings can be derived. Those result from a reduction of rework and and increasement of customer-effective delivery reliability, since maintenance measures are carried out precisely and machine availability is increased.
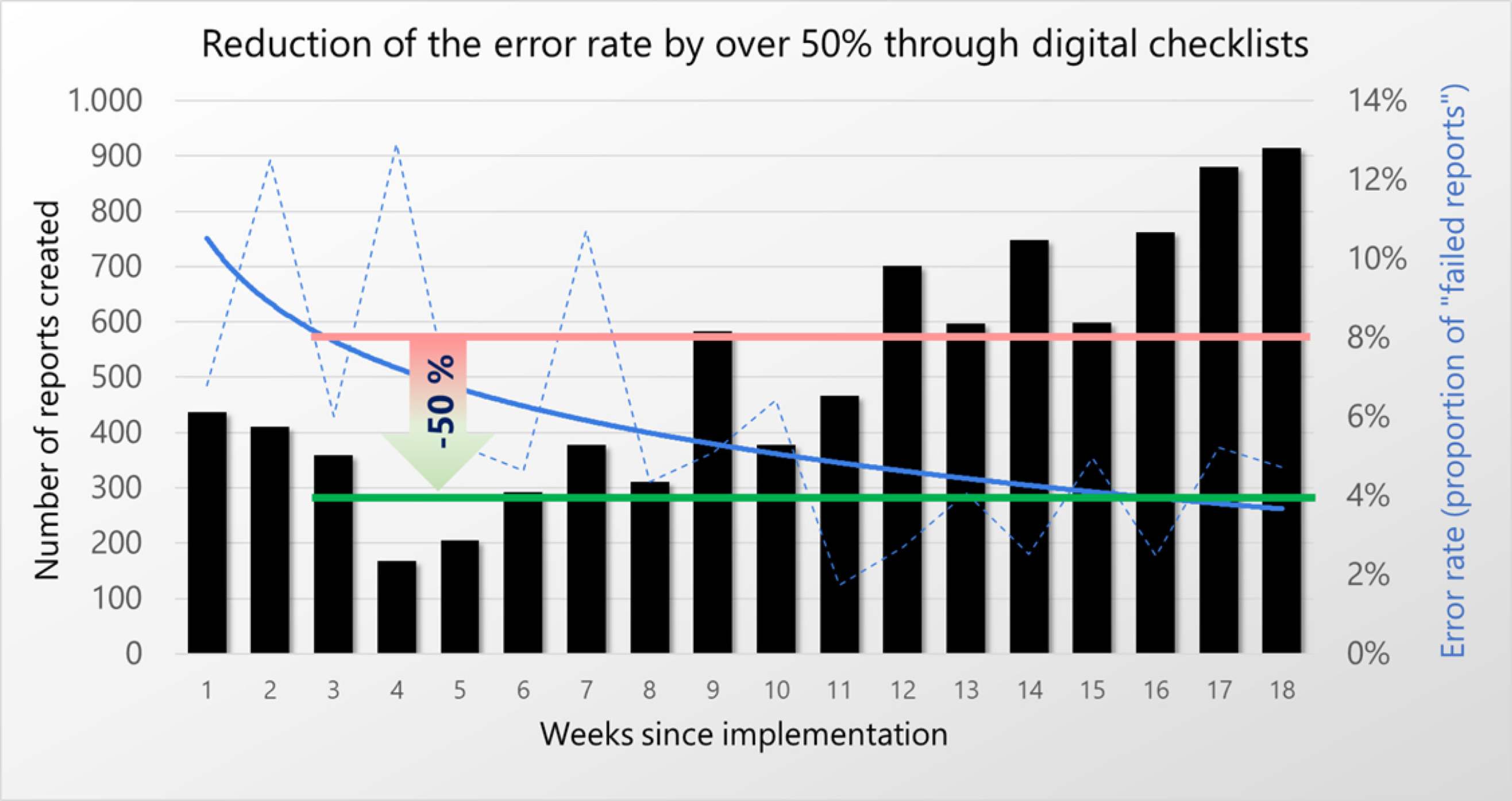
Work Instruction 4.0
With digital work instructions and checklists, you increase efficiency and make better decisions. Read in our whitepaper how our software solution can help you!
Markus Glotzbach
During his professional career, Markus gained deep insights at companies and large groups in different industries and knows the digitalization hurdles and problems on the shopfloor. Before joining Operations1, he studied International Management (MA) and worked in the Cloud Computing as well as SaaS telematics sector.