What it's about
In the following blog post, we explain how good work instructions become a great lever for efficient process management. You will not only learn how to write work instructions, but also which steps are important before and after. After all, instructions should not serve an end in themselves - but can even be used as a means for process optimization. Learn what 11 questions you should ask yourself before creating and what stylistic techniques are available to optimize work instructions. Finally, download a simple Word template for creating your work instruction.
Why well-written work instructions are so important
Work instructions describe in detail how activities must be carried out. So far, so good. There are numerous instructions on how to create them on the Internet. However, the structure of a work instruction - detached from its actual purpose - is often considered only. With well-formulated instructions, you can not only structure work processes. They can also influence how efficiently processes are run through: Scrap production and errors can be avoided before they occur due to ambiguous instructions. New employees can be trained more quickly. Processes can be managed and and lived adeptively.
Increase productivity and efficiency
Writing good, clear and easy-to-understand work instructions takes a lot of time. It is therefore understandable that it is initially seen as an expense driver. However, each work instruction gives you a new opportunity to examine processes in detail and to further optimize individual process steps. For the writing of the work instruction, this means simply speaking: Consciously questioning the status quo during the process. Does it really make sense for a certain operation to take place at this particular workstation? Is the sequence of the individual sub-steps really efficient or can the process be optimized at this point? Therefore, use the writing of work instructions to examine your production. Even highly professionalized and thoroughly optimized production processes can still be improved.
Optimal support for operational employees
There are countless types of operations in manufacturing companies, which are recorded in assembly instructions, packaging instructions, test instructions or in maintenance procedures. In times of lot size 1 and increasing quality requirements, production is becoming many times more complex. Many of these operations are still performed manually by employees. This will continue to be the case as digitization advances. People will continue to be at the center of complex production processes. This is confirmed, among other things, by a study by the World Economic Forum in collaboration with the University of Cambridge. That's why you should provide your employees with the best possible support, e.g. through intuitive tools and worker assistance systems. However, if you are working with paper-based instructions and do not yet have a digital tool in place, you should design your work instructions to add maximum value. Below we show how:
How To: 3 phases of creating a work instruction
Every work instruction can be divided into 3 phases: the planning, the actual creation and the deployment "in the field". All three phases are equally important.
Phase 1: Planning
Prioritize clearly:
Not every process needs a work instruction. It has no added value if it just sits around unused. Work instructions are especially important when A) processes are complex, B) legally required, or C) new employees need to be trained frequently. Case B) is actually very rare. According to ISO 9001, you do not need documented instructions at all. Therefore, consider whether it really makes sense to create them - or whether they are just an avoidable effort driver. But even if you don't "have to" - the documentation of your most important production processes is an integral component of your value creation.
Before you start writing, take a look at the status quo:
Does an instruction already exist that needs to be renewed? Does one need to be written for the first time? How is the process currently executed in reality? We also recommend that processes be reviewed when updating existing instructions. The quality management representative, work preparation or industrial engineering (or the respective responsible employees who create work instructions in your company) should sit down with the direct, operational process owners. Use collaborative tools such as MIRO or the classic flipchart and visualize the current processes . Is there potential for optimization? Let previous experience flow directly into the creation in a way that adds value.
Define operations and steps of the process:
Are you planning a new production line? When you create a new instruction for it, you record operations and working steps in detail. Operations are "larger topics" (e.g. "Assemble component X"), working steps are the activities within an operation (e.g. "Assemble component X in the following Y steps"). First define operations and determine the sequence of operations. Then formulate the working steps.
Phase 2: Creation
Formulate the introduction & purpose of the work instruction:
What may sound trivial has a great advantage: you place the individual working step in a larger context. People like to think and act in meaningful contexts. The purpose reminds your employees "what" you're actually doing it for. But keep it short.
Fleshing out:
Here's where it gets down to the nitty gritty. Formulate text, visual support, safety notes, add materials and tools... as the blog progresses, you'll learn exactly how to go about writing and what to consider.
Finetuning:
Read over it again - shorten where possible. Do a test: ask employees who are familiar with the process as well as people outside the field if the instruction is understandable.
Pro tip: When creating multilingual work instructions, always finalize one version first before translating.
Phase 3: Deployment
Test & validate:
Get started. Only when the instruction is in use you can further optimize it. Inform operational staff who are following the instruction for the first time that you are open to feedback.
Enable living processes:
Designate clear people responsible for feedback. After a while, check whether target processes are still being carried out as intended. If not: ask why and take the feedback into account in the next process optimization. The open feedback culture empowers your employees, shows appreciation and thus ultimately increases productivity. If you use digital work instructions, also use the data from the process execution to further develop the process.
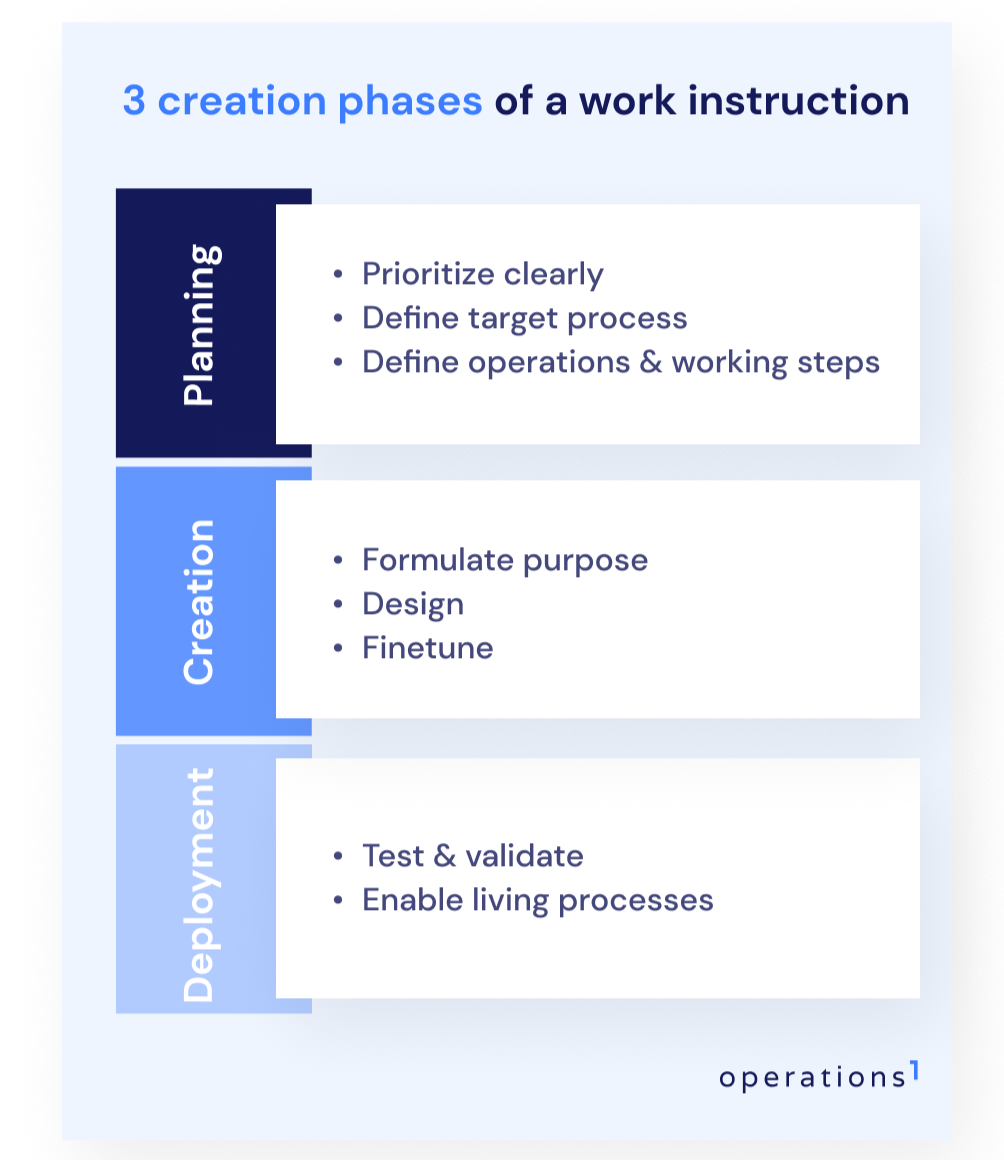
Do you want to simplify the writing of your work instructions?
Learn about the benefits of digital work instructions and focus on essential production processes. Download our e-paper "Work Instruction 4.0" and learn how software can support you in creating work instructions.
Writing work instructions correctly
We do not want to declare the creation of a work instruction an art form! If you work with word processing programs like Word or Excel instead of software you know how tedious writing, formatting and updating can be. However, the more often you write work instructions or SOPs, the easier it will be to create them. Even in the first phase - before you start writing - use eleven guiding questions to help you structure.
11 Guiding questions for the creation of a work instruction
For what: What is the purpose of this step?
Who: Who is to do the work?
What: What must be done in the work step?
How: Which individual sub-steps (work steps) belong to the work process (operation)?
With what: What aids (e.g. certain instruments or machines) are required?
Where: Where (on which belt section, in which hall, on which machine, etc.) is the work step to be performed?
How much: What is the required production quantity or, for example, the number of test operations?
How long: How long should the work step take?
What grade (quality): What is the desired target value that should be at the end of the assembly or testing operation?
What safety precautions: Are there work safety measures that must be observed?
What data: What data do I actually want to extract again from the process, e.g. for the CIP?
ATTENTION: If you are looking for guidance on work instructions, you will most likely find only 10 points in most guidebooks. Point 11 (data) is usually not considered. It is extremely important to consider what will happen with the instruction before it is written. Do employees just need to follow the manufacturing process, or even document data themselves? Many companies use the concept of worker self inspection, where employees take responsibility for checking the quality of their operations.
Note also: not every one of the 11 questions will be found in the form of an answer on your work instruction. So do not regard these guiding questions as a 1-to-1 template for your production operation - but as a supporting guide for your individual application.
4 success factors for good work instructions:
Once you have answered all the guiding questions for your company or use case, you can start with the actual writing. There are no rules, no set pattern, after which you must proceed. As already mentioned, work instructions are rarely mandatory. The form does not matter. However, there are some helpful tips that make both creating and following work instructions easier. Good work instructions are:
Short and to the point
Keep it short. Like this section. Period.
Clearly and concisely formulated
Each industry has its own technical language. Nevertheless, try to use clear and simple wording and as few foreign words as possible. Keep in mind that you are working with people from different backgrounds. Maybe there are language barriers or you want to train new employees faster because your company is growing. Therefore, try to avoid passive constructions and nouns. Example: Instead of "Molded parts are replaced and checked for ease of movement", you should rather write: "Replace and check molded parts. Do they move easily?". This procedure does require some rethinking, especially if a certain "operating language" has already become established. However, it simplifies the work of those carrying it out enormously.
Visually supported
Instead of pure continuous text, you should also use images and graphics. Photos of the working step, a simple image montage with a red arrow pointing to a specific area or a comparison between an incorrectly and correctly assembled product provide great support. Even simple document formatting such as broken-up text sections already help to understand and implement instructions more quickly. Work instructions are therefore often created today in the form of checklists. The bullet point-like formatting additionally supports the faster comprehension and processing of information.
Credible and consistent
Even the most visually appealing work instruction does not automatically lead to processes being lived properly. Employees must understand the meaning and purpose of the instruction - and above all understand it as a helpful tool, not as a complexity driver. It is therefore important that experienced employees who know the processes inside out at least provide advice during their creation. Often, work instructions only work in theory because they are created by employees who are not involved in production. Production employees who perform the processes on a day-to-day basis are in the best position to judge what works and what doesn't for your operation. Consult these employees early on. The authenticity of your work instruction increases - and with it the acceptance for the respective process.
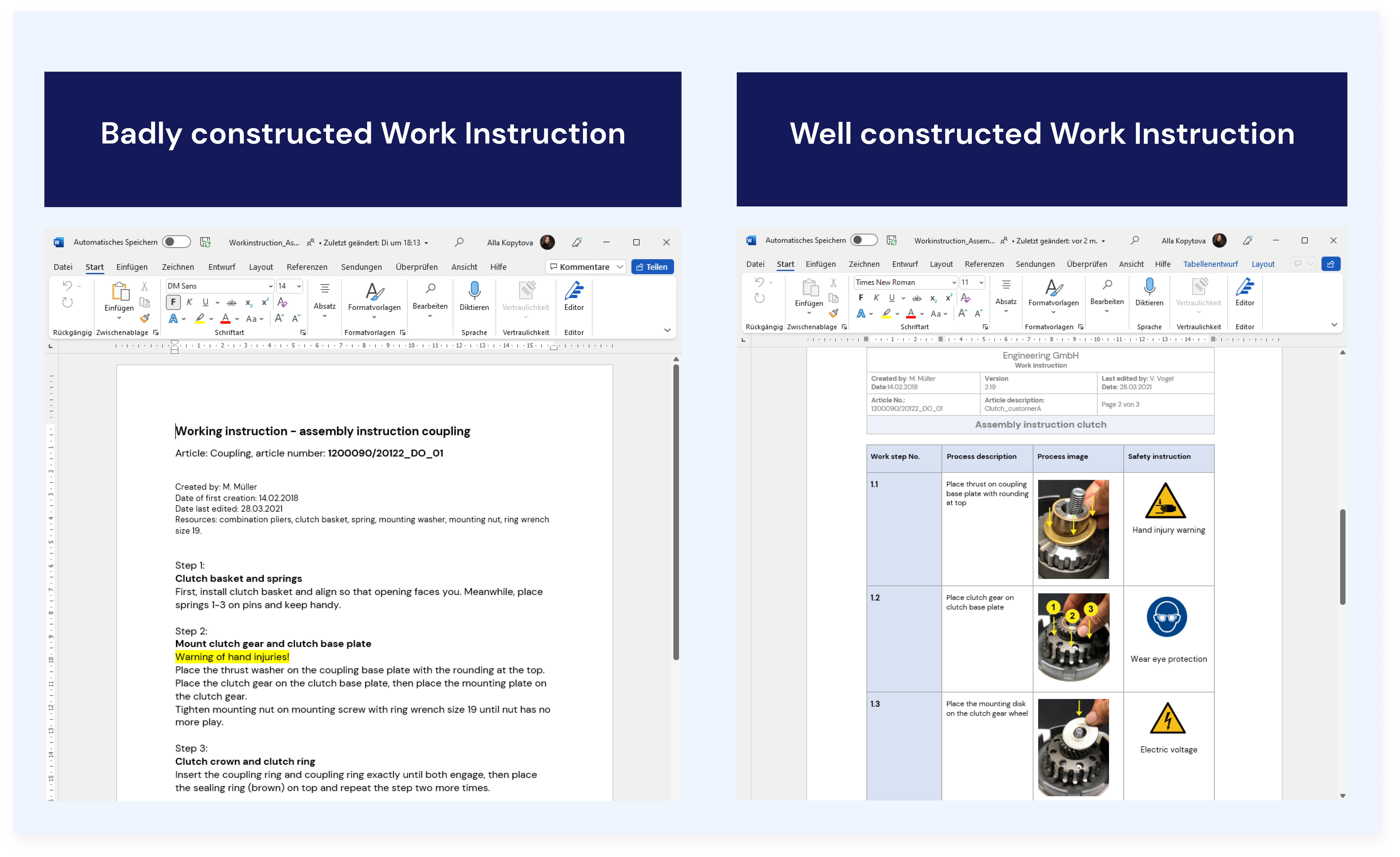
After the work instruction is before the process optimization
After you have created and distributed the instruction, you can now measure on the fly whether the document is really good based on productivity, scrap production, process duration and other metrics. If you have a feedback process in place, you will get valuable information mirrored. Use this knowledge to continuously optimize your processes and also the work instructions.
Of course, this is time-consuming - especially when you need to create work instructions across locations and languages. Even if you gain valuable insights from employee feedback. With paper-based work instructions, you have less flexibility to provide adaptive process guidance. You might also consider implementing a digital tool that helps you with all phases of creation and evaluation. With digital work instructions you save tremendous effort in creation, can track real-time progress on each operation, and receive structured feedback.
Conclusion
Work instructions should never serve an end in themselves and should only be created because "it has always been done that way". Much more, it requires planned preparation and follow-up work. To write good work instructions, you must first ask yourself what purpose they serve. The bottom line is always a target process. The work instruction is therefore a very effective tool for process optimization.
Keep in mind that processes are not static - and work instructions are therefore also living documents. However, creating and updating them is relatively time-consuming, especially if you want to capture complex processes, include media support, or create multiple language versions. That's why you should think about simplifying the creation process with the help of software. This way, you can concentrate even better on the proper implementation and further development of the target processes.
Editha Bertsch
Editha is an experienced project management expert for manufacturing companies. With a clear understanding of the specific challenges of the industry, she is passionate about developing innovative solutions.