Digital Maintenance Logs
With digital maintenance checklists, you simplify any maintenance work through an intuitive interface for your employees, automatic log generation and comprehensive evaluability. This way, you know the progress of maintenance procedures at any time, solve incidents collaboratively and use your findings directly to improve processes.
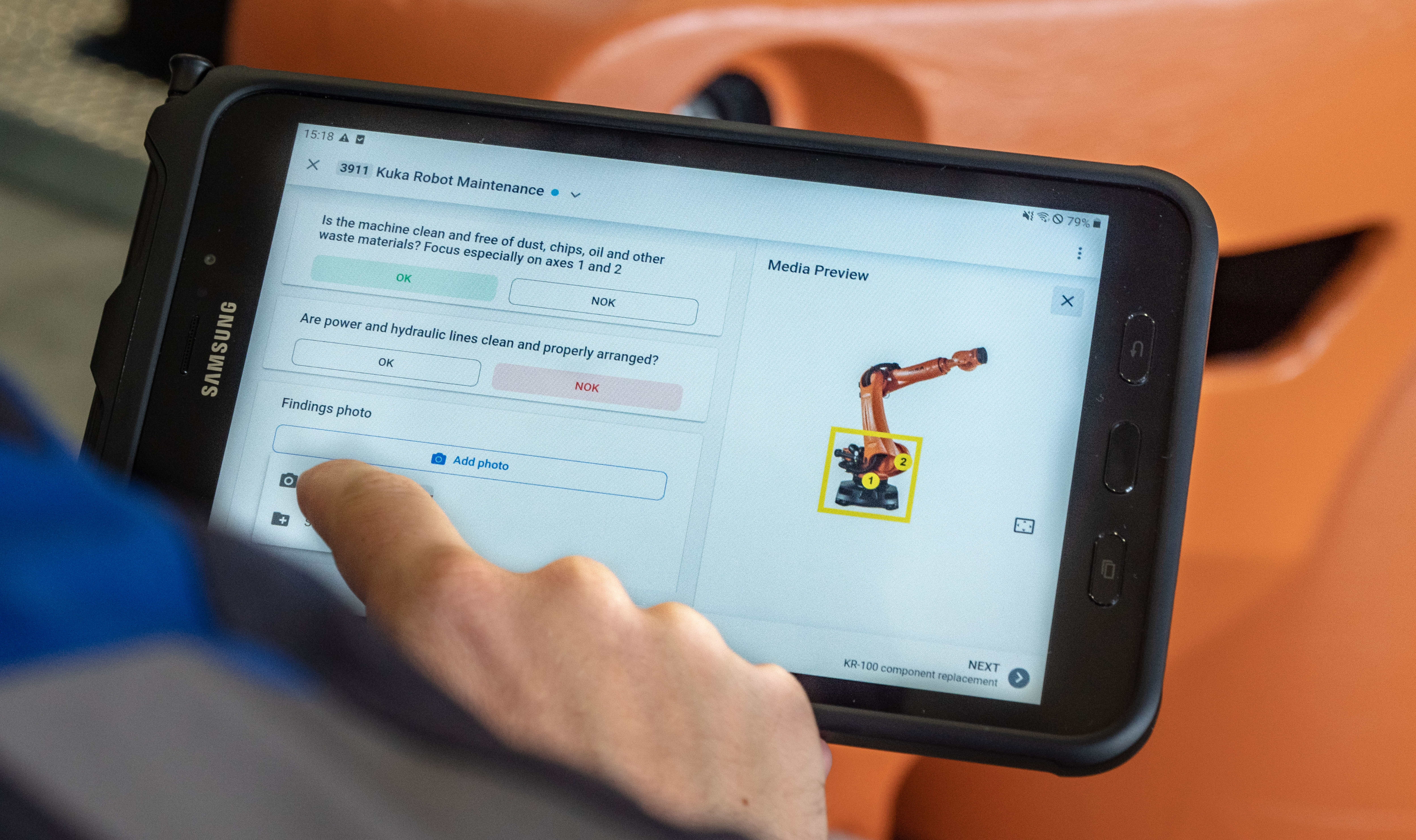
- -95% Effort for Docu
- +21% Higher productivity
- -85% Lower downtime
Central functionalities in maintenance
With Operations1, you eliminate all paper in your maintenance processes. Maintenance checklists can be created, updated and released digitally simply by dragging and dropping. Thanks to the cloud approach, your employees always receive the latest version of your digital maintenance checklists on the mobile device of their choice. To do this, they simply call up the checklist via an integrated search function, scan of a QR code or through an order link. All data points relevant for the maintenance log as well as information on the maintenance progress can be evaluated in a central overview. This ensures that all work is carried out, incidents are resolved and data is collected.
Connection of sensor data
Read sensor data on your machines and third-party systems in real time and play the data into the digital checklist. This way, you transfer information to your logs without errors.
Various interactions
Work predefined answers into checklists and allow Single- or Multiple-Choice. In your checklist you keep records for each individual work step.
Deposited units
Combine value- and target-performance-queries with all common units (mm, °C, Ω) to create meaningful evaluations for your digital checklists.
Further functionalities of the software
Change Notifications Employees receive change notifications in checklists before they start the process. Ask your employees for a personal signature.
Versioning Your documents keep their specific ID throughout versioning. This allows a consistent analysis.
Language Use your documents in all common languages. You can collaborate simultaneously in several languages on one checklist.
Images & videos Organize and edit images in a central place. This way you ensure a single point of truth.
Monitoring of the progress Keep an eye on the status of your tasks in a well-organized dashboard and react specifically and quickly to new incidents.
Offline capability You can also use the software offline. As soon as you are connected to the internet again, you can upload your work reports.
Scalable organisation Use structure classes for your teams, locations or machines. This allows you to easily organize your documents.
Modular checklists Create templates for checklists and use them as reusable modules. This way you save an enormous amount of time.
Orders & rules Schedule recurring tasks and rules on an employee-specific basis. Ensure that all assignments are completed.
Analytics Visualize your statistics easily and increase the significance with pictures and videos taken on site.
Variant configurator Automate the creation of variant-rich documentation. This saves you time and brings additional security.
Task management Create individual tasks, assign them to staff and track progress. React more quickly to incidents.
Maintenance log template: Use the Operations1 template
Operations1 offers you the possibility to import your existing maintenance documents and convert them into digital maintenance checklists. In addition, you can use the maintenance log template from the Operations1 library and adapt it for yourself. You create a new checklist simply by drag & drop. This way, you ensure an easy start and benefit from the digitization of your maintenance documents from day one.
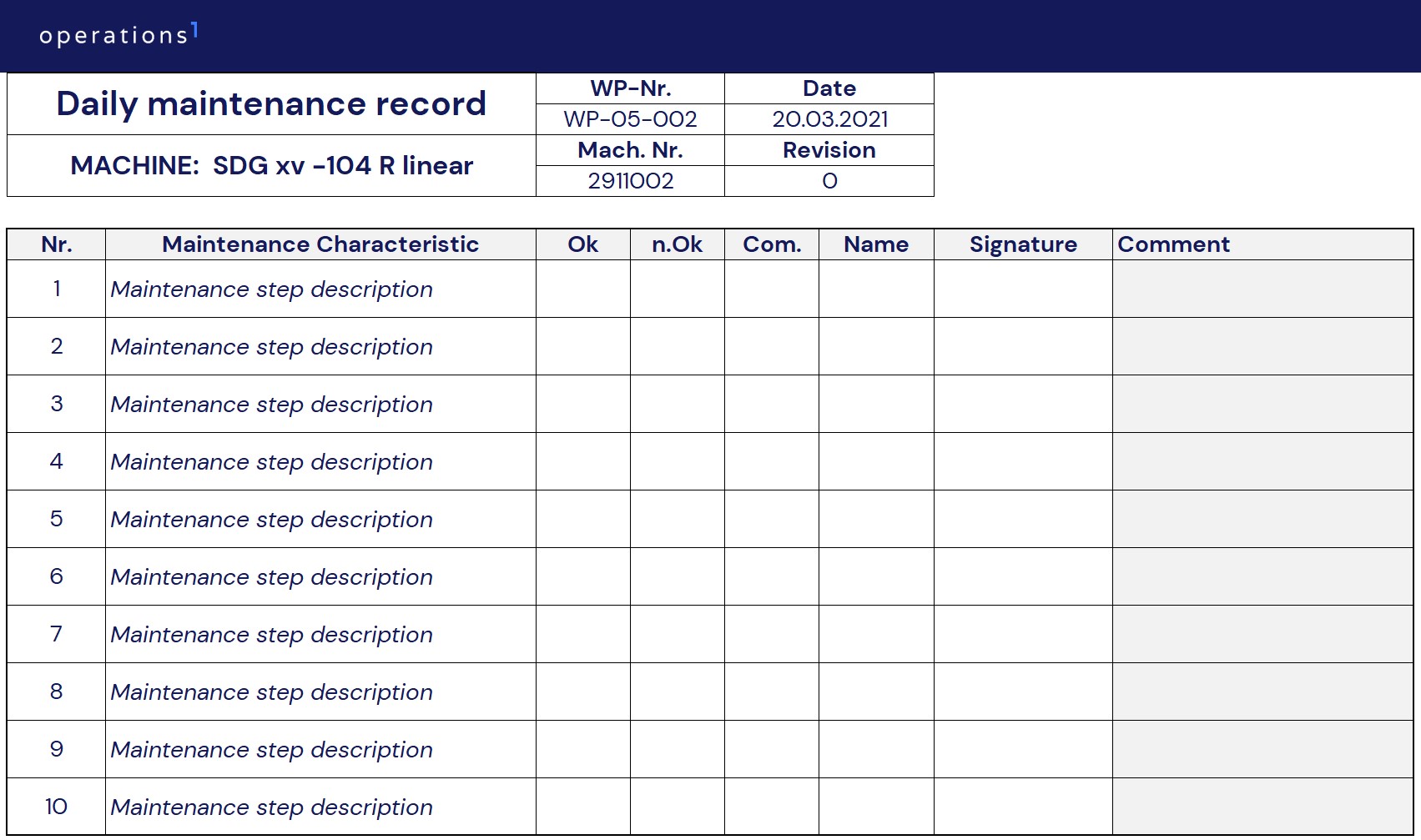
Interested? Get to know Operations1 in a live demo
We would be happy to show you the functions of Operations1 in an individual live demo and answer your questions.