What it's about
In this blog article, you will learn how you can also implement variant configurations at the operational process level and thus not only reduce effort, but also contribute to sustainably securing the company’s competitiveness.
What does variant configuration mean and what is it needed for?
Variant configurators are used in industry and software sectors to efficiently and scalably facilitate an increasing variety of products and processes. However, it is important here that companies do not limit themselves to using a configurator for product variants, but also keep an eye on implications for downstream process variants for assembly or testing processes and map these in an integrated manner.
Variant configuration initially refers to the selection of different variants within certain characteristics. We are all familiar with the online configurator of automobile manufacturers as a prominent example. Here, a large number of product variants can be generated on the basis of a template such as the basic Golf by selecting certain features. For features such as the audio system, seat covers and interior trim, manufacturers offer a range of potential variants.
However, variants are playing a strongly increasing role beyond the automotive industry. The number of product variants offered by many manufacturers has long been increasing in order to meet specific customer requirements. The management consultancy Oliver Wyman refers to this as the “redefinition of customer relationships” in the business customer sector, which does not stop at manufacturers of industrial products, machines or electronics.
Increasing product variants require the corresponding documentation
While many manufacturers are already using product configuration today, the use of variant configuration in the accompanying documentation is only just beginning. Typically, manufacturers also need variant-specific documents for the production of their variants, for example, to check quality characteristics. If the document is not variant-specific, maximum lists are created for checking characteristics, whose fields then have to be omitted or crossed out in large areas. In addition to wasting paper and increasing the effort required for documentation, this procedure also poses a particular risk for correct inspection.
If the number of variants increases, the documentation must follow:
Variant-specific assembly instructions
Product-specific inspection instructions
Variant-specific commissioning instruction
Variant-specific checklists
Variant-specific workflows
The alternative to using maximum lists would be to create individual variants. Since the creation of assembly instructions, test protocols, etc. is often still done in word processing programs, however, the effort here would increase immeasurably. In a customer survey, we found that the creation of a work instruction requires about 14 hours of work by a qualified specialist. The adaptation of a work instruction typically amounts to 1.5 hours. With 64 variants alone, the adaptation of a work step across all variants would take almost 100 hours and keep an employee busy for two and a half weeks. There are already 64 variants for 4 characteristics with 3 values each.
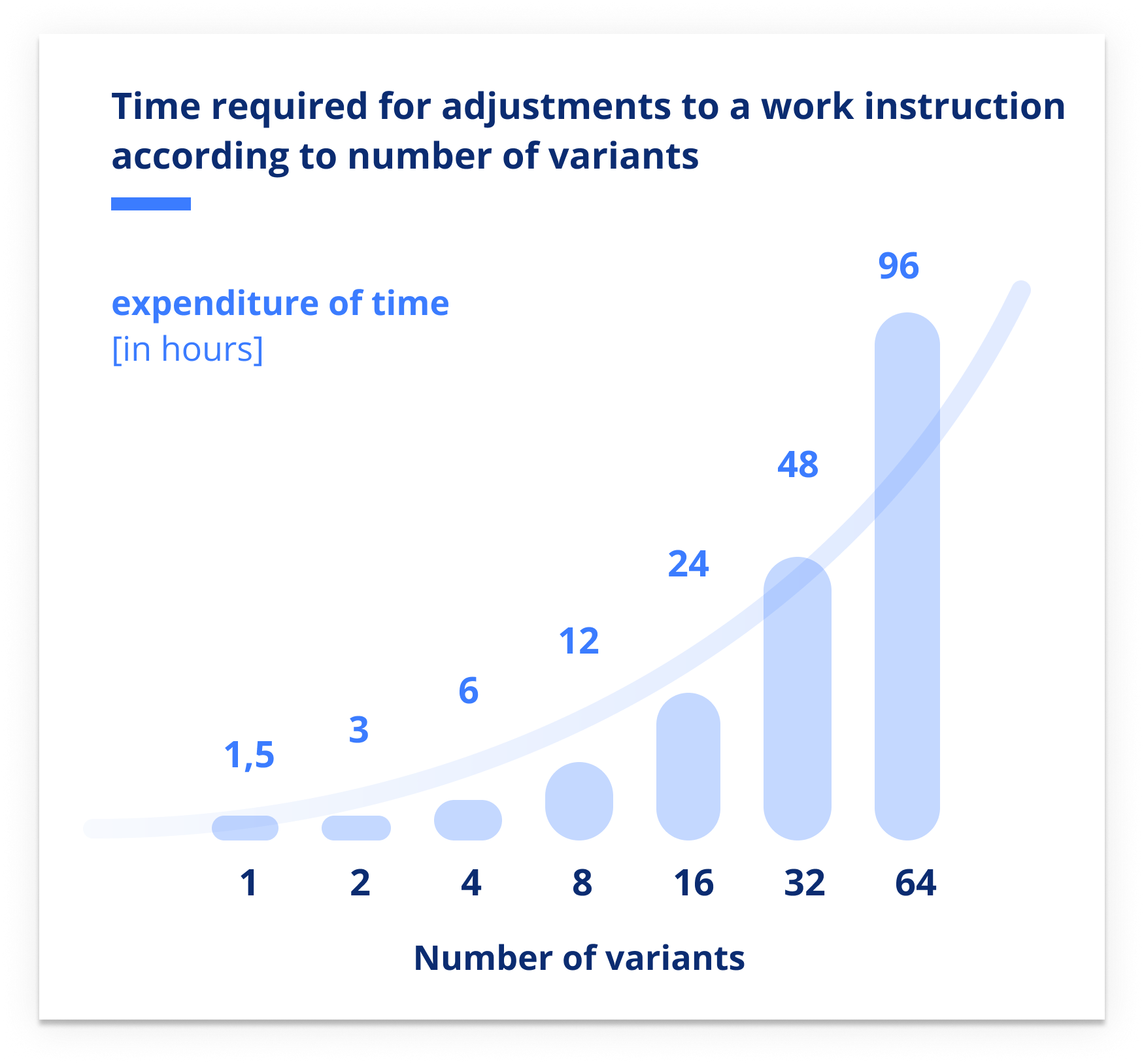
This also entails the risk that companies will not even undertake process adjustments due to the effort and complexity involved. In times of global competition, this is an enormous business risk. Especially in times of a shortage of skilled workers, it is obviously not a scalable approach to create and maintain work instructions and checklists in word processing programs. It requires a systematic and integrated approach.
Goals of variant configuration in documentation
Variant configuration in documentation thus pursues a number of goals:
Reduced effort in creation through automated configuration
Less effort in updating documents
Easy handling for employees by means of adaptive documents
Avoidance of duplicates and information redundancies
These direct operational goals ultimately result in higher productivity, because employees are involved in fewer non-value-added activities, increased process reliability, because employees receive precisely tailored documents instead of maximum lists, and ultimately increased competitiveness, because new product variants can not only be designed, but also easily assembled, tested or shipped.
The basis of variant configuration: modular structure for documents
Variants are characterized by the fact that they have a certain common denominator. Finally, the variant configuration is based on the variation in certain characteristics. A variant configurator thus requires a modular structure that maps these characteristics. If certain configuration settings are made, the corresponding modules are selected and a document is automatically created. In the case of a variant-based test of an industrial furnace, different test points are completed depending on the electrical power the furnace is to provide.
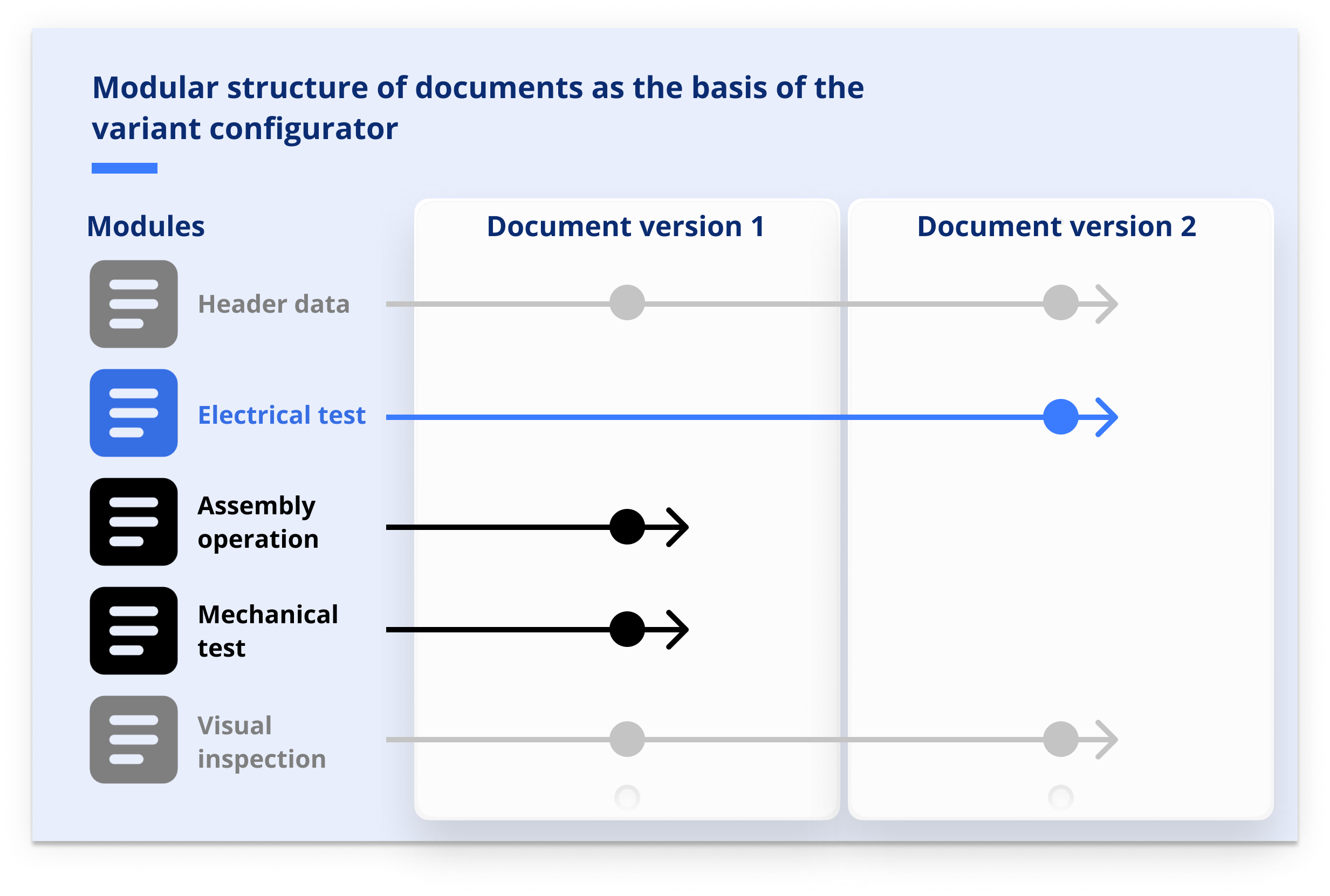
The modular structure ensures that adjustments can always be made centrally on the module and not in decentralized documents. Duplication of work, as in the example above, as well as information redundancies are solved in the long term.
The key to variant configuration is integration with ERP
When it comes to variant configuration, the Enterprise Resource Planning (ERP) system is of particular importance. Typically, the product variants are already stored in the ERP. In order to enable variant-specific testing or assembly, there should ideally be a direct link between the modules of the document and the variants in the ERP. Technically, such a connection can be realized in a few days via the API interface or middleware. The key here lies in the continued use of the existing characteristic identifiers from the ERP to enable addressing, assignment and sequencing of the modules. For this purpose, in the first step, the information of the desired configuration together with the metadata for the order is transferred from the ERP via the interface. In the second step, the modular content is selected and the variant-specific assembly or inspection instructions are created. These are then made available to the worker separately or in the context of an order.
In addition to the connection via the ERP system, there is a second possibility. This comes into play when full integration is not desired or the data is not available in any other system. In this case, you can simply use your own database and manually import the configuration characteristics and metadata. Any structured data format from CSV to XML or JSON is suitable for this purpose. The automated creation of the modular instruction and order then runs identically to the previous case using the defined characteristics and the implemented logic.
Adaptive information provision for operational staff
In order to carry out variant-oriented assembly or inspection processes, it is important to keep the complexity for the operative employees low in order to guarantee short cycle times and a high level of process reliability. Here, the automatic compilation of modules in the configurator initially ensures that employees receive all relevant information in one interface and are not irritated by excess or inapplicable information.
At the same time, however, it has been found that enriching instructions and checklists with media content such as images and videos is enormously beneficial to safe and reliable process management. In a customer study, the use of interactive work instructions and checklists led to a reduction in error rates of over 50%. Thus, a variant configurator ideally also dynamically accesses this media content.
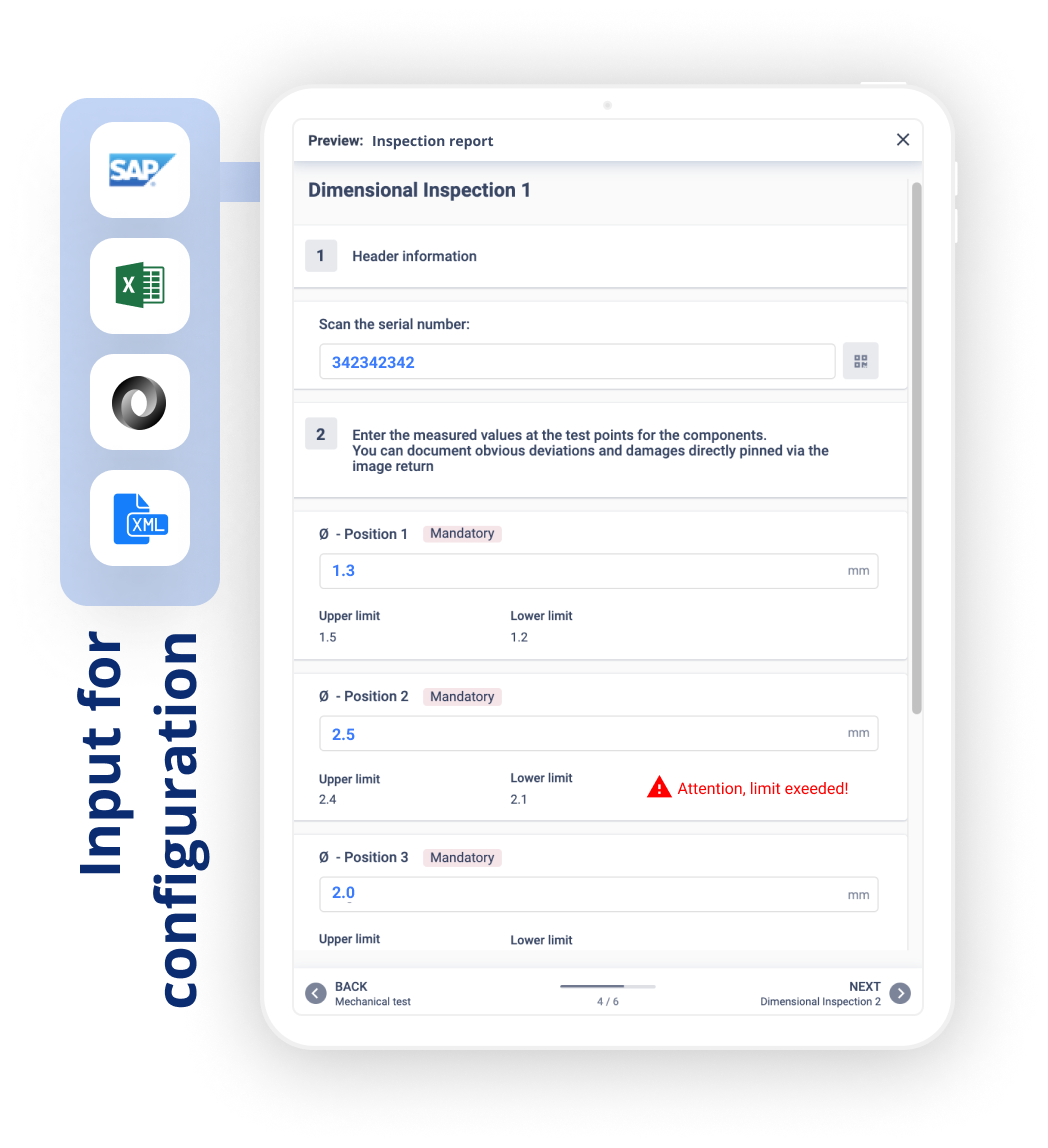
Advantage of integrated analysis capabilities
In order to be sustainably competitive, the use of the company’s own data for continuous process improvement is also decisive in the long term, as also stated in the above study by Oliver Wyman. For this purpose, too, it is essential to use a system that can recognize and assign variants in the case of variants in production. After all, otherwise data volumes would be generated that are difficult or impossible to compare and would not be able to contribute to continuous process optimization. In the case of the industrial furnace, it is relevant for quality inspection to what extent individual variants are affected, but also how inspection points across variants behave. This is only possible with a suitable data structure, which cannot be mapped in word processing programs or form builders.
You would like to get to know Operations1 or have specific questions?
Simply fill out the contact form with your thoughts and goals. We will get back to you immediately.
Benjamin Brockmann
Benjamin Brockmann (M. Sc., Management & Technology) founded Operations1 in 2017 together with Daniel Grobe (also M. Sc., Management & Technology). The founders developed the software solution based on various practical projects, including at the Fraunhofer Institute, and on their experience in industry, auditing and management consulting. Benjamin Brockmann has already worked for companies such as KPMG and Arthur D. Little.