Worum es geht
In diesem Blogartikel geben wir eine umfassende Erklärung zum Thema TPM (Total Productive Maintenance) und erläutern deren Mehrwert für Unternehmen – vor allem mit Bezug auf die Operations1-Softwarelösung. Folgende Fragen werden im Blogbeitrag behandelt:
- Was ist TPM (Total Productive Maintenance)?
- Die 8 Aktionsfelder von TPM
- Welche Vor- und Nachteile hat TPM auf dem Shopfloor?
- Wie lässt sich TPM umsetzen?
- Operations1 als Standard-Softwarelösung für TPM
Was ist TPM (Total Productive Maintenance)?
Wer in der Produktion, insbesondere in der Instandhaltung arbeitet, kommt an dem Begriff Total Productive Maintenance, kurz TPM, nicht vorbei. Was verbirgt sich hinter diesem Konzept, das schon über fünfzig Jahre alt ist und seinen Ursprung in Japan hat?
Begriffsdefinition
Total Productive Maintenance ist ein Begriff mit einer sehr langen Tradition, die in die 50-er Jahre des letzten Jahrhunderts zurückreicht. Bezeichnet wird damit ein Konzept in der Instandhaltung, das darauf abzielt, die Anlageneffektivität und die Lebensdauer der Anlagen zu steigern und so ein möglichst störungsfreies Produktionssystem zu realisieren. Durch eine wirkungsoptimierte, kostenoptimale Instandhaltung sollen Verluste und Verschwendung eliminiert werden, so dass „Null-Defekte“, „Null-Ausfälle“, „Null-Unfälle“ und „100 Prozent Qualität“ sichergestellt werden.
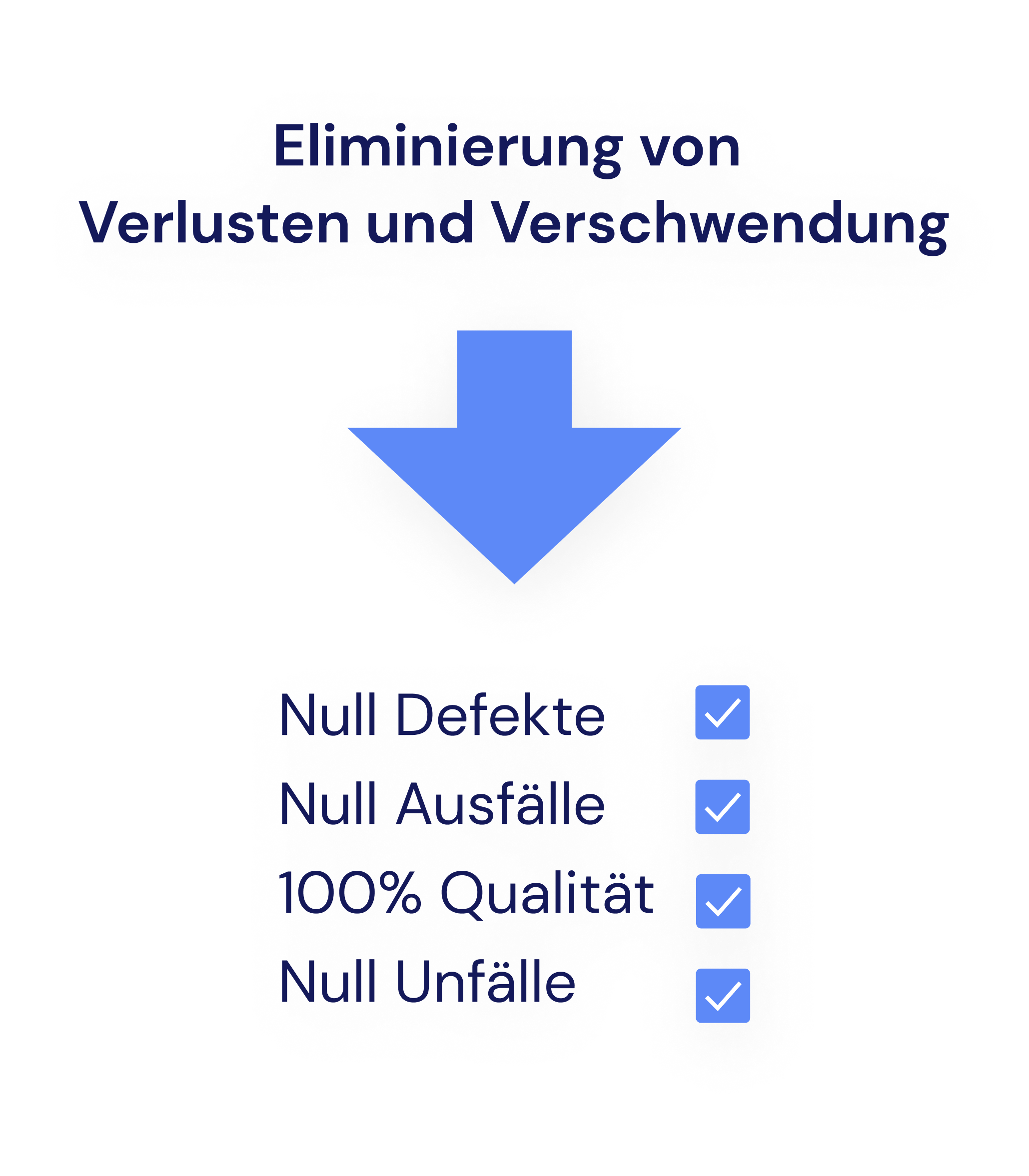
Ein tragender Gedanke hinter dem TPM-Konzept ist, dem Fertigungsmitarbeiter mehr Verantwortung zu übertragen, indem er aktiv mit in Verbesserungsaktivitäten einbezogen wird und diese nicht nur dem Instandhaltungsteam überlässt. Hierdurch können Verbesserungsmaßnahmen bereits am Ort des Geschehens umgesetzt werden und in den kontinuierlichen Verbesserungsprozess direkt mit einfließen.
Durch eine fachübergreifende Instandhaltung der Anlagen lassen sich Stillstände auf ein absolutes Minimum reduzieren und so die Effektivität und Verfügbarkeit der Anlagen verbessern. Auch die Gesamtanlageneffektivität als Ganzes wird dadurch gesteigert.
Die Ursprünge von TPM
Die Bezeichnung „Total Productive Maintenance“ geht auf den Japaner Seiichi Nakajima zurück. Das Konzept wurde erstmals Ende der 60-er Jahre von dem japanischen Automobilzulieferer Nippon Denso (heute Denso), dem zweitgrößten Mitglied der Toyota-Gruppe, eingeführt. Denso entwickelte das TPM-Konzept in vier Stufen: reaktive Instandhaltung → vorbeugende Instandhaltung → autonome Instandhaltung → Total Productive Maintenance.
Während bei der „reaktiven Instandhaltung“ die Maschine nach Ausfall wieder in einen normalen Betriebszustand versetzt wird, überträgt das Konzept der „vorbeugenden Instandhaltung“ die Verantwortung für das Instandhalten der Produktionsanlagen allein der Instandhaltungsabteilung. Dies hatte bei Denso eine wesentliche Reduktion der Anlagenstillstände zur Folge.
Mit zunehmender Automatisierung und einer hohen Anzahl an automatisierten Produktionsanlagen wurde es notwendig, die Wartung nachhaltiger anzugehen. Daher entschied der japanische Automobilzulieferer, die Maschinenbediener so zu schulen, dass sie Wartungsarbeiten autonom durchführen konnten – das Konzept der „autonomen Instandhaltung“ bildete sich heraus.
Aus den positiven Erfahrungen mit der autonomen Instandhaltung entwickelte sich schließlich die Total Productive Maintenance, in deren Mittelpunkt die Zusammenarbeit aller Mitarbeiter zur Aufrechterhaltung der Betriebsmittel und einer qualitativ hochwertigen Produktion steht.
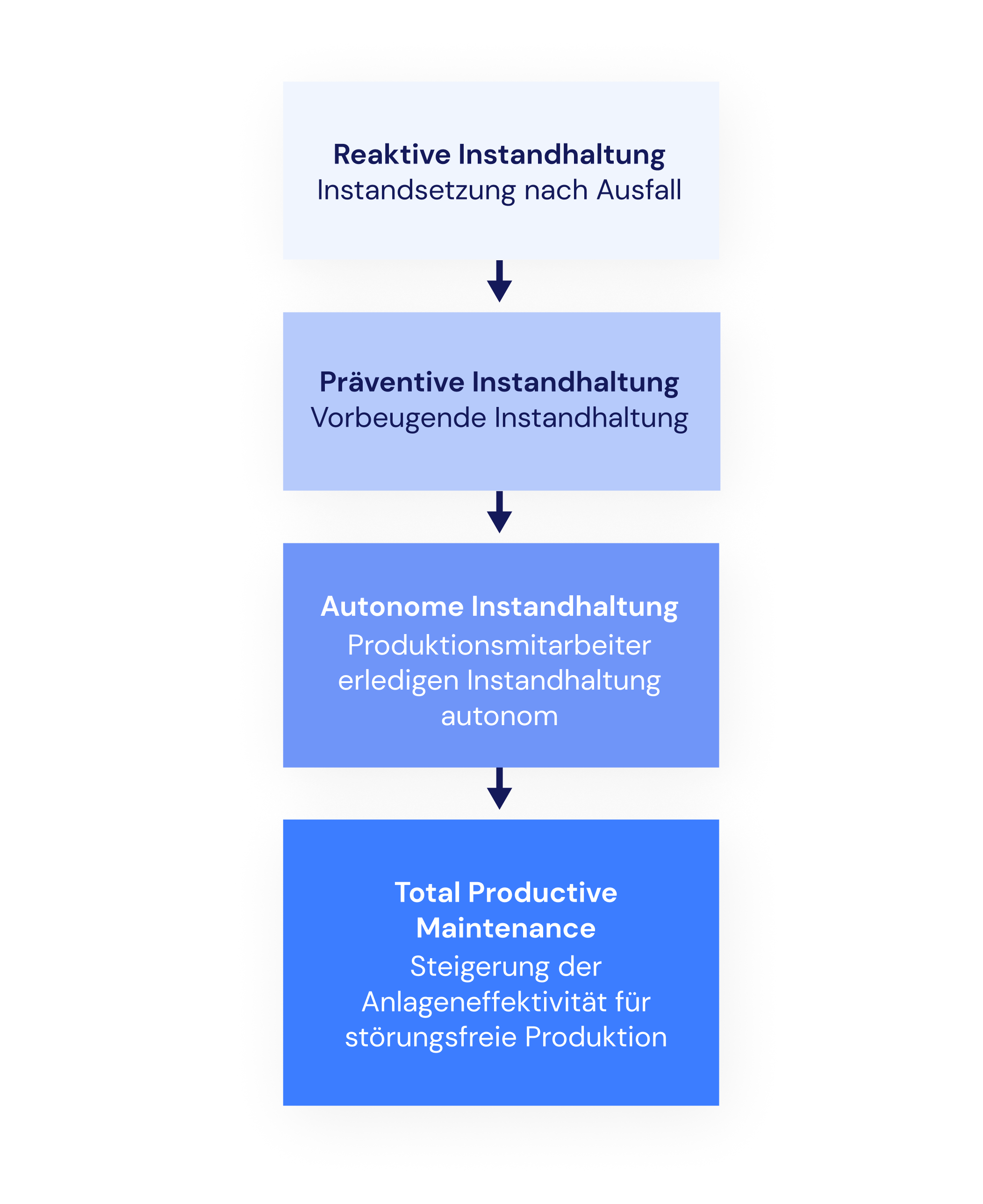
Die 8 Aktionsfelder von TPM
Total Productive Maintenance verfolgt den Ansatz eines ganzheitlichen Anlagenmanagements. Basierend darauf haben sich 8 Aktionsfelder entwickelt, in denen TPM realisiert wird:
Zielgerichtete kontinuierliche Verbesserung
Autonome Instandhaltung
Vorbeugende Instandhaltung
Kompetenzmanagement
Qualitätserhaltung
Anlaufmanagement
TPM in administrativen Bereichen
Arbeitssicherheit, Gesundheits- und Umweltschutz
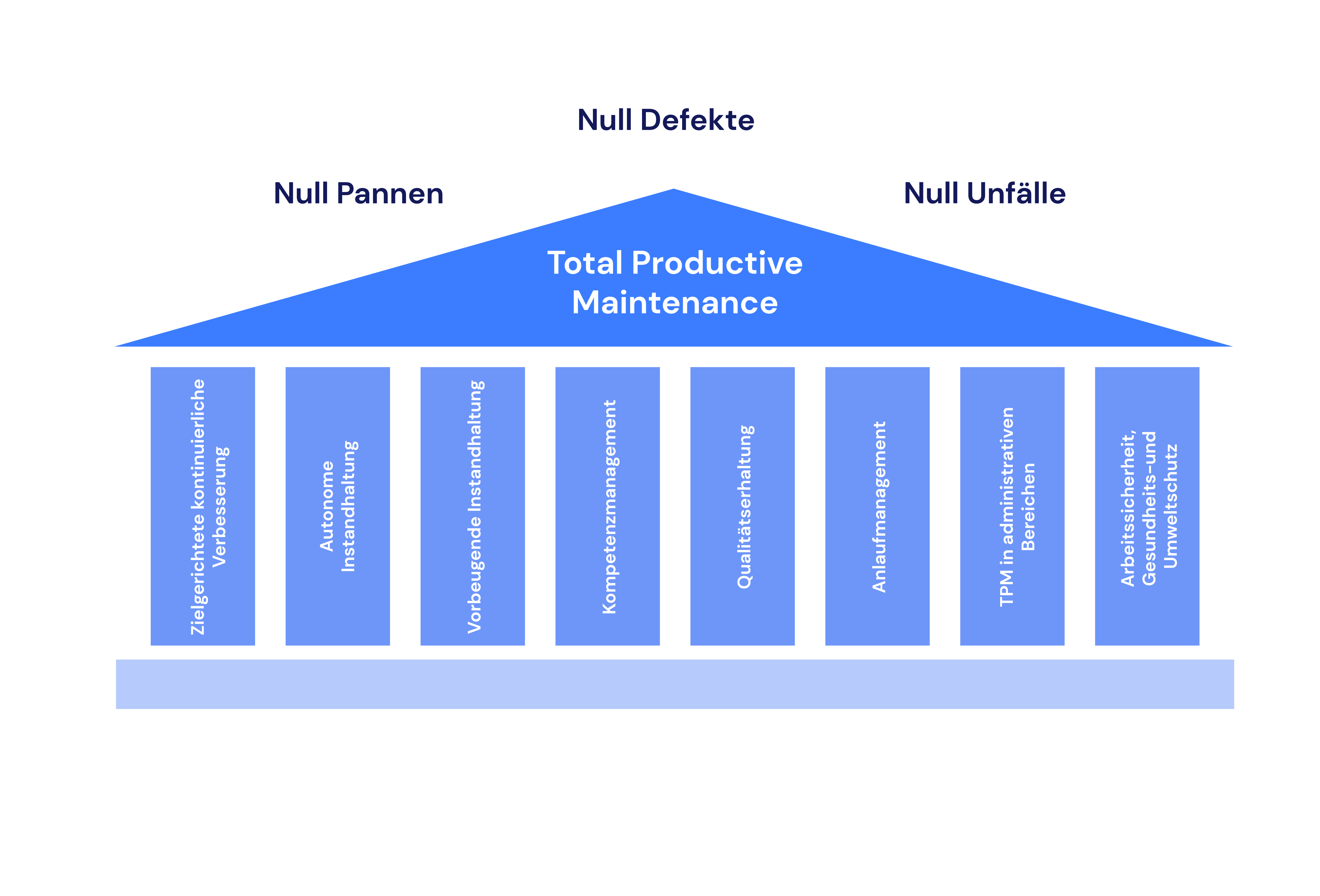
1. Zielgerichtete kontinuierliche Verbesserung
Die zielgerichtete kontinuierliche Verbesserung ist die erste Säule von TPM. Sie basiert auf sämtlichen regelmäßigen Aktivitäten zur Eliminierung von insgesamt 16 Verlustarten, die das reibungslose Zusammenspiel zwischen Maschinen und Anlagen, Mitarbeiter und Ressourcen betreffen. Die Grafik führt dies vor Augen.
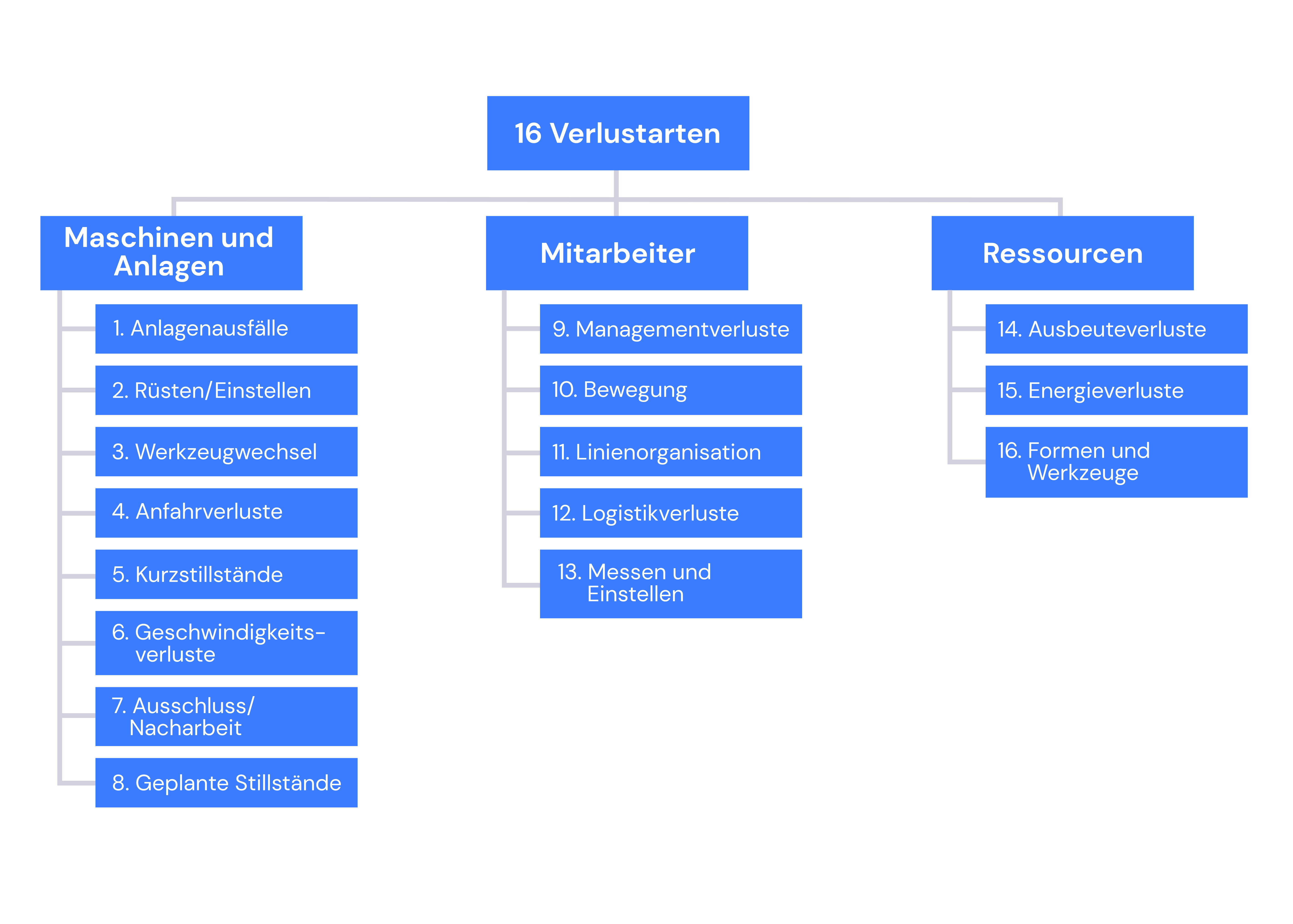
Hierzu gehören beispielsweise kurze Stopps und Störungen bei Anlagen, Sicherheitsaspekte und Umrüstzeiten. Die zielgerichtete kontinuierliche Verbesserung basiert auf der Überzeugung, dass eine stetige Optimierung in kleinen Schritten die Wettbewerbsfähigkeit von Unternehmen steigert. So können Durchlaufzeiten reduziert, Kosten gesenkt und die Qualität optimiert werden. Mit diesem Ansatz lassen sich auch Trends frühzeitig erkennen und angemessen bedienen. Vorbild der kontinuierlichen Verbesserung ist das japanische Kaizen.
Unser Blogbeitrag „KVP: automatisiert mit Software“ gibt Ihnen weitere wertvolle Insights zu einer gelungenen Umsetzung von kontinuierlicher Verbesserung.
2. Autonome Instandhaltung
Die autonome Instandhaltung ist das zweite Aktionsfeld von Total Productive Maintenance. Sie besagt, dass kleinere Wartungs-, Inspektions-, Reinigungs- und Schmierarbeiten vom Maschinenbediener selbst durchgeführt werden und nicht von hochspezialisierten Technikern. Wenn die Mitarbeiter an den Produktionsanlagen eine höhere Eigenverantwortung für ihre Anlage haben und für die Fehlerfrüherkennung sensibilisiert werden, trägt dies langfristig zu einer Maximierung der Effizienz von Maschinen und Anlagen bei. Dies entlastet auch die Instandhaltungsmitarbeiter, die ihren Fokus stattdessen auf komplexe Instandsetzungsmaßnahmen und deren Optimierungsmöglichkeiten lenken können.
3. Vorbeugende/Präventive Instandhaltung
Das dritte Aktionsfeld von TPM, die vorbeugende oder auch präventive Instandhaltung, setzt auf die Planung und Durchführung von Instandhaltungsmaßnahmen noch bevor eine Anlage Schäden aufweist. Dadurch sollen Ausfälle und Stillstände minimiert und die Effektivität und Verfügbarkeit der Maschinen gesteigert werden. So entsteht ein Paradigmenwechsel, bei dem der Arbeitsprozess nicht mehr einer reaktiven, sondern einer ganzheitlich vorbeugenden Betrachtungsweise unterzogen ist – mit zahlreichen langfristigen Vorteilen für das Unternehmen: Unvorhersehbarkeit wird entgegengewirkt, eine Unterbrechung der Produktion vermieden und die Gesamtlebensdauer der Anlagen erhöht sich. Die präventive Instandhaltung ist somit ein essenzielles Kriterium für eine zukunftssichere, resiliente Produktion.
Die Erfolge der vorbeugenden Instandhaltung lassen sich anhand von zwei Kennzahlen messen: der MTTR (= mean time to repair/mittlere Reparaturzeit) und der MTBF (= mean time between failures /mittlere Laufzeit zwischen zwei Stillständen). Ziel ist die Minimierung der MTTR und die Maximierung der MTBF.
4. Kompetenzmanagement
Ein Schlüsselfaktor für Total Productive Maintenance ist die vierte Säule von TPM, das Kompetenzmanagement. Im Kern geht es dabei um gut ausgebildete Mitarbeiter und motivierte Führungskräfte. Das Ziel ist, die Mitarbeiter derart auszubilden, dass sie in der Lage sind, Bedienungs- und Instandhaltungsmaßnahmen qualifiziert auszuführen. Das Kompetenzmanagement bildet somit die Voraussetzung für alle weiteren Säulen von TPM.
5. Qualitätserhaltung
Der fünfte Baustein von Total Productive Maintenance, die Qualitätserhaltung, fokussiert auf alle Maßnahmen, welche die Produktqualität und Prozesssicherheit nicht nur erhalten, sondern auch steigern. Die Bereiche Produktion, Entwicklung und Instandhaltung greifen hierbei eng ineinander und basieren auf den Prinzipien „Null-Verluste“, „Null-Maschinenausfall“, „Null-Ausschuss“ und „Null-Fehler“. Die Qualitätserhaltung ist darauf ausgerichtet, sicherzustellen, dass die erreichte Qualität das Ergebnis idealer Maschinenbedingungen ist. Diese sollen so eingestellt sein, dass Fehler vermieden werden und dauerhaft hohe Qualität produziert wird – die Basis für Kundenzufriedenheit und -bindung. Damit Qualitätsprobleme möglichst gar nicht erst aufkommen, umfasst die Qualitätserhaltung folgende Aufgaben:
Festsetzung von Qualitätsstandards
Implementierung von Systemen zur frühzeitigen Identifikation von Defekten und Fehlern
Trendanalysen
Implementierung von Systemen zur Defekt- und Fehlervermeidung
Poka-Yoke-Prinzip, das auf der Vermeidung unabsichtlicher Fehler basiert
Implementierung einer Qualitätsmanagement-Matrix
6. Anlaufmanagement
Den sechsten Baustein von Total Productive Maintenance bildet das Anlaufmanagement. Es zielt darauf, eine schlanke Anlaufkurve bei neuen Produkten und Anlagen zu gewährleisten, so dass der Markt zügig bedient werden kann. Folgender Parameter bedarf es, damit dies reibungslos gelingt:
frühzeitige Planung von neuen Produkten, Prozessen und Anlagen
frühzeitige Einbeziehung der Lieferanten in die Planung
Verkürzung der Entwicklungszeiten von Produkten, Prozessen und Anlagen
Verkürzung der Anlaufzeiten bei neuen Produkten, Prozessen und Anlagen
Berücksichtigung von Informationen zur Vermeidung von Instandhaltung
Involviert in das Anlaufmanagement sind Anlagenplaner, Konstrukteure, Instandhaltungs- und Produktionsmitarbeiter. Je enger diese Stakeholder miteinander vernetzt sind, je besser gelingt die Umsetzung der sechsten Säule von Total Productive Maintenance.
7. TPM in administrativen Bereichen
Um Verluste und Verschwendung in nicht unmittelbar produzierenden Unternehmensbereichen zu eliminieren, wird TPM auch in administrativen Unternehmensbereichen eingesetzt. Betroffen hiervon sind Abteilungen wie Einkauf, Logistik und Personalwesen. Anwendung findet hierbei die bewährte „5S-Philosophie“ von Lean im Sinne von Sortieren, Systematisieren, Säubern, Standardisieren und Selbstdisziplin. TPM wird außerdem im Bürobereich realisiert. Die dortigen Abläufe werden mit geeigneten Werkzeugen sichtbar gemacht und auf Wertschöpfung und Effizienz ausgerichtet. Dadurch soll sichergestellt werden, dass wichtige Informationen zur richtigen Zeit, in der richtigen Form und zu den geringstmöglichen Kosten an den richtigen Ort gelangen.
8. Arbeitssicherheit, Gesundheits- und Umweltschutz
Das achte Aktionsfeld von TPM dient zur Erreichung von „Null-Unfällen“ sowie der Emissions- und Nachhaltigkeitsziele zum Wohl von Mitarbeitern und Umwelt. Dazu werden die Mitarbeiter entsprechend geschult, so dass sie potenzielle Gefahren in diesen drei Bereichen identifizieren und rechtzeitig Gegenmaßnahmen ergreifen können. Hierzu zählt auch die Bewusstseinsbildung bei den einzelnen Mitarbeitern. Dies bedeutet beispielsweise, dass sich die Mitarbeiter der Umweltaspekte bewusst sind, die für die Betriebsführung und das Image der Organisation wichtig sind. Hierunter fallen Faktoren wie Wasserverbrauch, Schadstoffemissionen, Lärmbelästigung, Abfall und Energieverbrauch.
Auf diese Weise kann sich eine Unternehmenskultur etablieren, in der die Produktivität innerhalb der Fertigung und aller damit zusammenhängenden Funktionsbereiche kontinuierlich optimiert wird. Das bedeutet im Umkehrschluss, dass eine gute Umsetzung von Total Productive Maintenance neben den Maschinen stets die Mitarbeiter mitberücksichtigt und für eine produktive Wechselwirkung zwischen Mensch und Maschine sensibilisieren möchte.
TPM-Kennzahlen
Um den Erfolg der acht Aktionsfelder von TPM im Hinblick auf die Reduktion von Verschwendung sowie nachhaltige Effizienz messen zu können, werden Kennzahlen in sechs Zielkategorien verfolgt:
Produktivität: Arbeitsproduktivität, Wertschöpfung pro Person, Störungsreduzierung
Qualität: Prozessfehler, Anzahl der Defekte, Anzahl der Kundenreklamationen
Kosten: Arbeitskräftereduzierung, Instandhaltungskosten, Energiekosten
Logistik: Bestandsmenge, Lagerumschlagshäufigkeit
Sicherheit und Umwelt: Anzahl der Unfälle, Krankenstand, Kennzahlen bzgl. Verschmutzung
Motivation: Anzahl der Verbesserungsvorschläge, Anzahl Kleingruppentreffen
Oberstes Ziel von Total Productive Maintenance ist die Erhöhung der Gesamtanlageneffizienz, auch als OEE (Overall Equipment Effectiveness) bezeichnet. Um den Output (Produktion, Qualität, Lieferungen, Sicherheit, Gesundheit, Umwelt und Arbeitsmoral) zu maximieren und gleichzeitig den Input (Arbeitskraft, Maschinen und Material) zu minimieren, zielt TPM darauf ab, folgende drei Hauptfaktoren günstig zu beeinflussen:
Stillstandszeiten (durch Rüstzeiten, Instandhaltung oder Störungen)
Taktverluste
fehlende Qualität
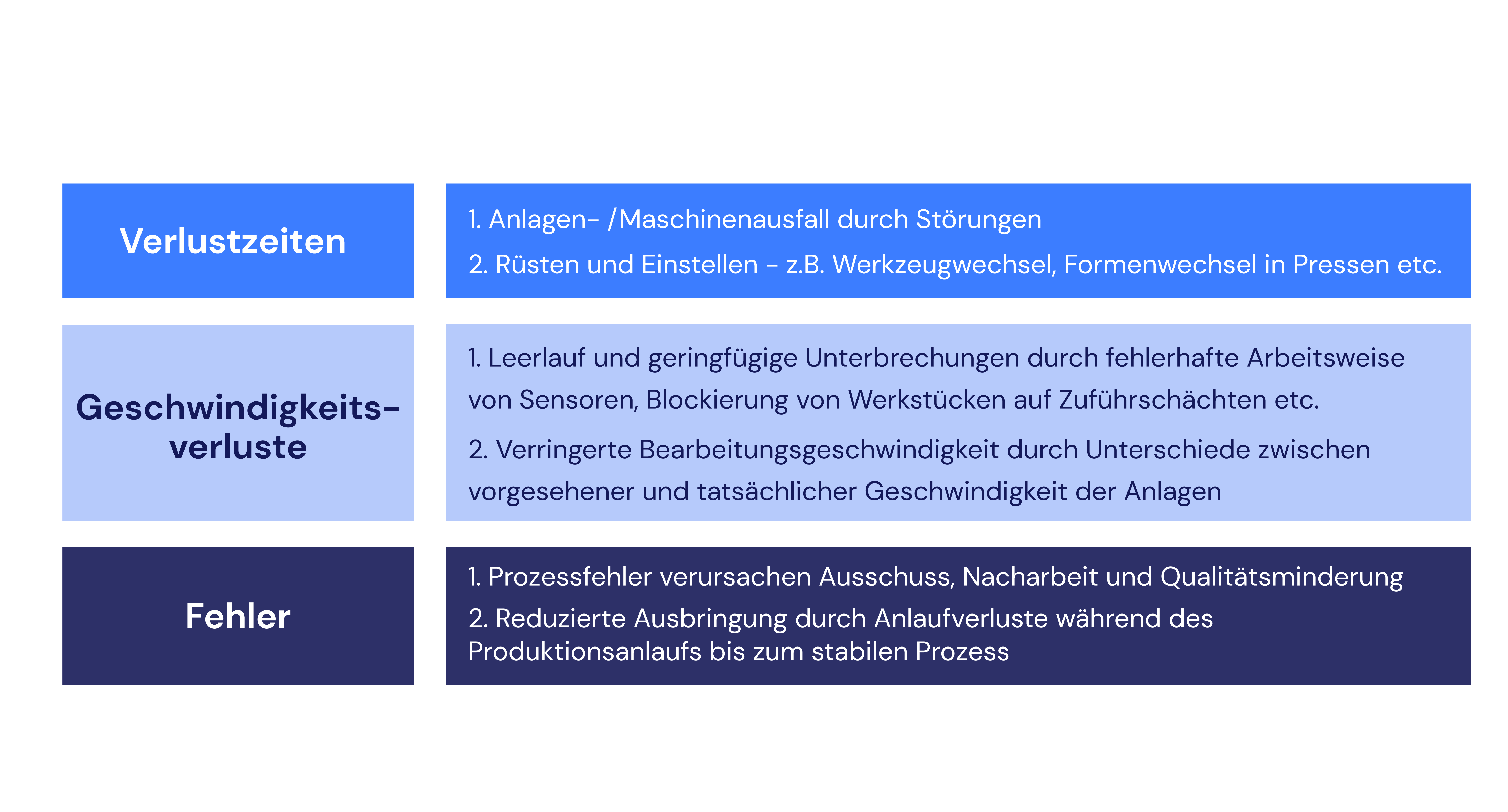
Welche Vorteile hat TPM auf dem Shopfloor?
Angesichts der Tatsache, dass sich Unternehmen heutzutage mehr denn je mit kontinuierlich steigenden Marktanforderungen konfrontiert sehen, ist eine Maximierung der Anlagenverfügbarkeit eine Voraussetzung, um wettbewerbsfähig bleiben zu können. Die Implementierung eines ganzheitlichen Instandhaltungsprogramms wie es das TPM-Konzept vorsieht, ist hierfür ein entscheidender Erfolgsfaktor.
Das mittels Total Productive Maintenance verfolgte Ziel der Sicherstellung einer maximalen Anlagenverfügbarkeit bei minimalem Instandhaltungsaufwand hat auf dem Shopfloor für Unternehmen unterschiedlichster Größe somit zahlreiche Vorteile:
Reduktion von Funktionsstörungen & erheblich weniger Maschinenstillstände
Reduktion von Ausschuss
geringere Rüst- und Einrichtzeiten
Steigerung der Produktivität
verbesserte Kontrolle der Instandhaltungskosten
Entlastung der Instandhaltungsabteilung und geringere Abhängigkeit vom Wissen Einzelner
Verbesserung von Sicherheitsstandards
Erhöhung der Mitarbeitermotivation durch stressfreieres Arbeiten und mehr Eigenverantwortung jedes einzelnen Mitarbeiters
Zukunftssicherheit & Resilienz
Basierend auf Erfahrungswerten der Unternehmensberatung TCW führen wir im folgenden Schaubild beispielhaft zwei wesentliche Kennzahlen an, welche die Vorteile von Total Productive Maintenance eindrücklich demonstrieren:
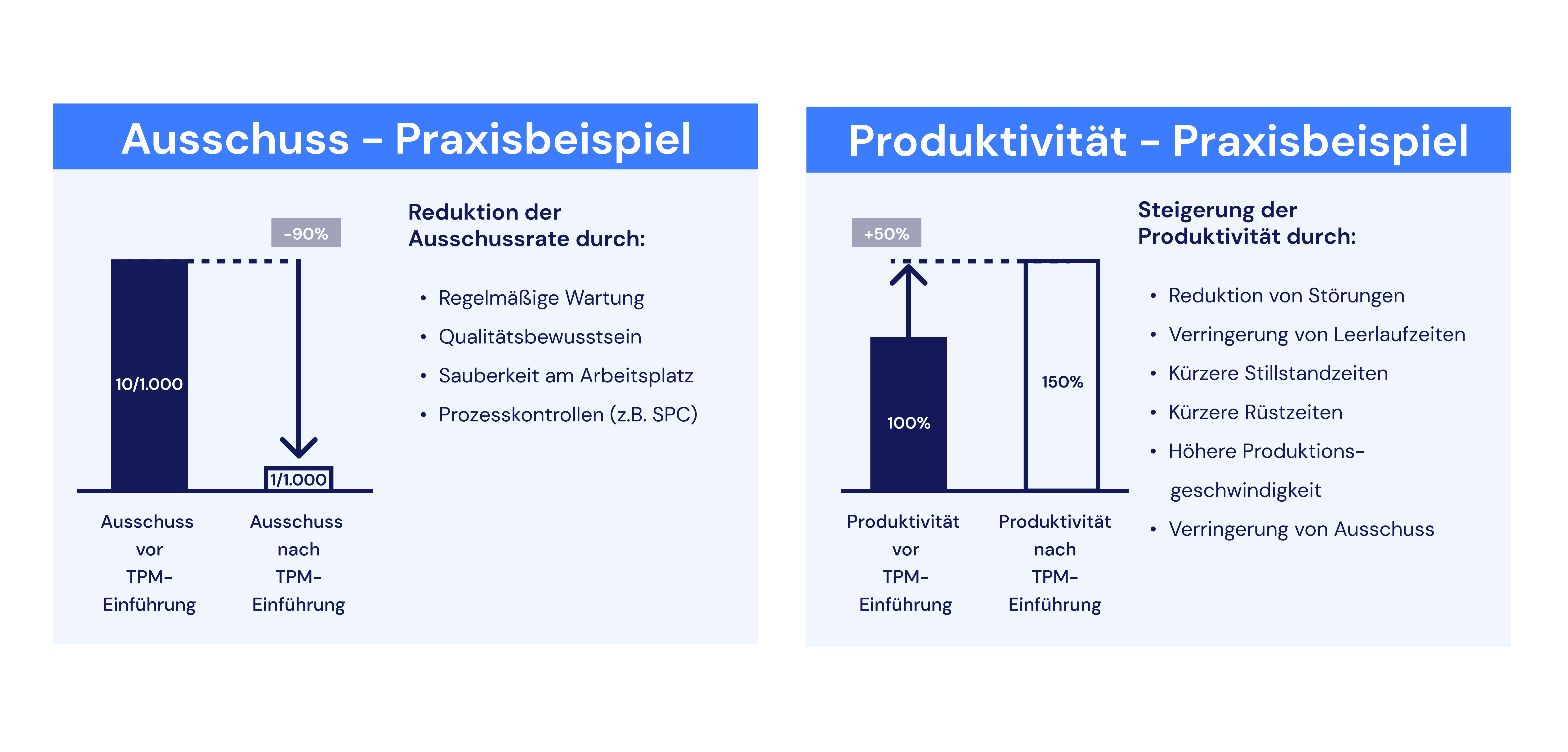
Auch unser Kunde Hirschvogel, einer der größten, weltweit operierenden Automobilzulieferer auf dem Gebiet der Massivumformung von Stahl und Aluminium, konnte durch den Einsatz von Total Productive Maintenance beachtliche Ergebnisse erzielen. In unserer Success Story können Sie im Detail nachlesen, wie dies mithilfe der vollumfänglichen Digitalisierung sämtlicher Instandhaltungsprozesse mit der Operations1-Software gelang. Drei wesentliche KPI’s möchten wir mit Ihnen teilen:
-60% Reduzierung der Downtime in den internationalen Hirschvogel-Werken
-50% Prozessabweichungen
250.000€ Einsparungen pro Standort durch Reduzierung der externen Dienstleister
Nachteile von TPM
Trotz all der Vorteile ist die Frage berechtigt, ob Total Productive Maintenance auch Nachteile mit sich bringt. Die Antwort hierauf lautet klar Ja: sofern die Implementierung nämlich von den folgenden Gegebenheiten begleitet wird:
Die Unternehmensleitung ist nicht bereit, einen kontinuierlichen Verbesserungsprozess mit langem ROI einzuleiten, bei dem alle Mitarbeiter ihr Wissen und Können einbringen, um nachhaltig die Wertschöpfung zu erhöhen.
Die Unternehmensleitung ist nicht bereit, viel Zeit in Schulung und Ausbildung ihrer Mitarbeiter zu investieren. Gerade in Zeiten von Krisen und externen Schocks wie Lieferkettendisruptionen, Klimaereignissen und politischen Missständen werden Produktionsunternehmen vor große Herausforderungen gestellt und der Faktor Zeit gilt als Mangelware.
Das Unternehmen ist nicht gewillt, die notwendige Geduld für die Einführung von Total Productive Maintenance aufzubringen. Da TPM häufig einen spürbaren Kulturwandel erfordert, sind seitens aller beteiligten Mitarbeiter agiles Denken, Offenheit und die Bereitschaft zu hoher Eigenverantwortung erforderlich.
Der zentrale Nachteil von TPM ist somit der Aufwand bei der Implementierung. Geschieht die Umsetzung halbherzig, wird dies bei allen Beteiligten zu Verdruss führen. Gleichzeitig lässt sich TPM aber auch pragmatisch einführen.
Wie lässt sich TPM umsetzen?
Bei der Einführung von Total Productive Maintenance empfiehlt es sich, in mehreren aufeinander aufbauenden Schritten vorzugehen:
Entwicklung eines TPM-Programms mit Zielsetzungen, Maßnahmen, Meilensteinen, Terminen, Verantwortlichkeiten, Mitteln
Strukturierung der Anlagen, Erfassung ihrer Zustände/Defekte mit Ursachen und Folgen, Ableitung von Maßnahmen
Festlegung eines Pilotbereiches, Zuordnung der Tätigkeiten, Schulung und Unterweisung der Anlagenführer, Umsetzung der Maßnahmen durch schrittweise Übertragung von Aufgaben an die Anlagenführer, Erfassung der Ergebnisse, Entwicklung von Arbeitsunterlagen
Auswertung der Piloterfahrungen, Vervollkommnung der Arbeitsunterlagen, Erweiterung der Mitarbeiterkompetenz bis zur autonomen Instandhaltung
Umsetzung der Erfahrungen, Übertragung auf andere Bereiche
Verarbeitung der Erfahrungen aus den Pilotbereichen in Lastenhefte, Beschaffungskonzepte für Neuanlagen
Wichtig ist, dass die drei unterschiedlichen Zielgruppen Führungskräfte, Produktionsmitarbeiter und Instandhalter individuell abgeholt und die Gründe für die Einführung von Total Productive Maintenance detailliert erläutert werden. Während den Führungskräften die Vorteile von TPM in einem Vortrag erläutert werden können, sollten die Produktionsmitarbeiter in Form von Trainings-on-the-job abgeholt werden. Es bietet sich beispielsweise an, eine Produktionsanlage nach TPM zu reinigen, zu warten und in Betrieb zu nehmen und von den Mitarbeitern einen Vergleich zum aktuellen Vorgehen ziehen zu lassen, um so die Vorteile aufzuzeigen. Ein besonderes Augenmerk bei der Einführung von TPM liegt auf den Instandhaltungsarbeitern. Sie müssen mental den größten Kulturwandel von der „Feuerwehr-Abteilung“ zur treibenden und umfänglichen Dienstleistungsabteilung mit hoher Eigenverantwortung vollziehen.
Gelingt es, die TPM-Methode nicht als ein zeitlich befristetes Projekt zu begreifen, sondern als einen Weg, der einen Anfang hat, aber kein festgesetztes Ende, weil Optimierung nie abgeschlossen ist, sind gute Bedingungen für eine erfolgreiche Umsetzung geschaffen.
Operations1 als Standard-Softwarelösung für TPM
Instandhaltungsmitarbeiter stehen heutzutage vielfach vor zweierlei Herausforderungen: Operativ bestehen hohe Aufwände für Planung und Nachweisführung in der Instandhaltung. Systemseitig sehen sie sich äußerst komplexen Landschaften ausgesetzt, da es für Total Productive Maintenance bisher keine systemseitige Unterstützung gibt. So finden Tätigkeiten wie Wartungsplanung, Maschineninspektionen, HSSE, Qualifikationsmanagement & Co. in vielen separaten technischen Lösungen oder auf Papier statt. Parallel dazu nimmt der Fachkräftemangel weiterhin zu, Produktionsprozesse werden aufgrund einer steigenden Produktvariantenvielfalt stetig komplexer, durch die grassierende Inflation werden die Lohnkosten steigen und Covid-19 hat gezeigt, wie wichtig eine operative Resilienz im Falle von externen Schocks ist.
Digitale Total Productive Maintenance setzt genau an diesen Pain Points an: Die Software-Lösung von Operations1 unterstützt Sie dank des allumfassenden Connected Worker Plattform-Ansatzes, welcher auf eine ganzheitliche technologische Vernetzung der Mitarbeiter abzielt und so eine effiziente und zukunftssichere Instandhaltung gewährleistet. Unsere Software deckt die vier zentralen TPM-Bausteine präventive Instandhaltung, autonome Instandhaltung, Kompetenzmanagement und Arbeitssicherheit, Gesundheits- und Umweltschutz ab.
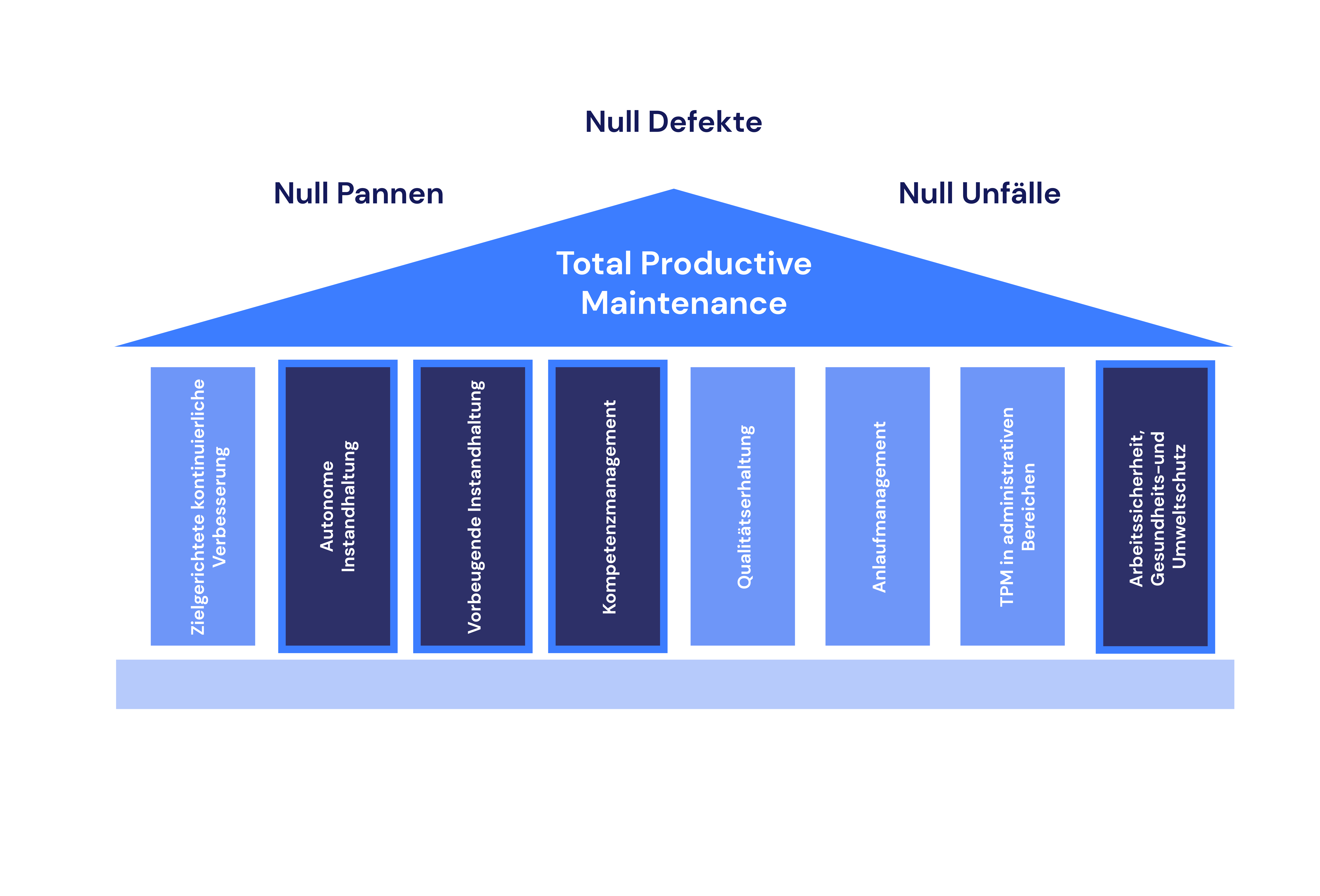
Folgenden Mehrwert bietet Ihnen digitale TPM mit der Operations1-Software:
Wartungspläne lassen sich für präventive Instandhaltung in Operations1 erstellen oder Sie verbinden die Software-Lösung mit Ihren Bestandssystemen ERP, MES bzw. CMMS
Alle TPM-Dokumente können in einer All-in-One-Software verwaltet werden
Intuitive Checklisten mit bild- oder videogestützten Wartungsanweisungen ermöglichen autonome Instandhaltung
Mitarbeiterqualifikationen lassen sich verwalten
Sicherheitsrundgänge, 6S und Arbeitsschutzaudits können geplant und dokumentiert werden
Wartungsberichte werden automatisch erstellt
Mitarbeiter können in Echtzeit via Text, Foto oder Video-Befunde im Sinne von KVP dokumentieren
Unerwartete Vorfälle lassen sich über das Task Management lösen
Fazit: Total Productive Maintenance ist einer der Grundbausteine eines wirksamen Produktionssystems.
Sie möchten Operations1 kennenlernen?
Füllen Sie hierzu bitte das Kontaktformular mit Ihren Gedanken und Zielen aus. Wir melden uns umgehend bei Ihnen zurück.
Editha Bertsch
Editha ist eine erfahrene Expertin im Bereich Projektmanagement für produzierende Unternehmen. Mit einem klaren Verständnis für die spezifischen Herausforderungen der Branche arbeitet sie leidenschaftlich daran, innovative Lösungen zu entwickeln.