What it is about
In this article, we answer the key questions around Connected Work and Connected Worker platforms. Keep reading to find answers to the following questions:
- What is a Connected Worker platform?
- Why is a Connected Worker platform important?
- What is the difference between a Connected Worker platform and a worker assistance system?
- Connected Worker Platform: Typical use cases
- What are the differences between Connected Worker Platforms?
- How do you choose the right Connected Worker Platform for you?
- Connected Worker Platform case study: How does the industry benefit?
What is a Connected Worker Platform?
The term "Connected Work" is primarily used to describe the organizational, process-related and technological connection of operational, so-called "deskless" employees: Typically employees in production, logistics or other production-related support processes. Read our blog post from the Connected Manufacturing Worker Event 2022 in London on current trends in Connected Work.
A Connected Worker platform represents the technological solution for realizing this connectivity. The difference to typical software applications is that workers are embedded in a comprehensive digital system. Information is provided contextualized, employees interact with IoT equipment and are connected in real time with each other and with management and work planning levels.
Why is a connected worker platform important?
Digitalization is changing our lives in all areas. But while mobile apps, wearables, and the like are greatly simplifying our everyday lives, this simplification has not been embraced by manufacturing companies yet. Digitization efforts have focused strongly on connecting machines, the establishment of shop floor dashboards, the introduction of digital production planning, and diverse, often unwieldy stand-alone solutions. Operational employees are thus faced with the challenge of combining their information from fragmented solutions with complex interfaces, often also from printed instructions and checklists. Problems are solved with little traceability, data is transferred manually from paper to Excel files, or is not even taken into account at all. Ultimately, the operational employee finds himself in a digital no man's land.
Key challenges of manufacturing companies conflict with this way of working. The work environment and the role of employees are changing: The shortage of skilled workers continues to increase, production processes are becoming more complex due to a growing number of product variants, rampant inflation will increase labor costs, and Covid-19 has shown the importance of operational resilience in the face of external shocks. While operational employees are undoubtedly central to a disruption-free and effective operation, a dwindling workforce spends too much time on repetitive, non-value-added, and less meaningful activities. This is exactly where connected workers come in and can provide a remedy.
What are the advantages of such a platform? 11 major advantages of a Connected Worker platform are:
Sustainable capture of process knowledge Digital capture and supply of knowledge in real time represent protection against demographic change and shortages of skilled workers. Less qualified employees can also perform more complex activities.
Reduction of errors Intuitive process guidance reduces rework, scrap and complaints.
Shorter response times Real-time connectivity and context-based information supply speed up problem solving.
Increased productivity By eliminating activities that don't add value such as search efforts, data transfers, archiving efforts, etc., operational employees have more time for important tasks.
Increased transparency Process data and on-site findings can be easily collected and made available in real time.
Elimination of paper costs Saving thousands of sheets of paper per year also makes sense from a sustainability perspective.
Reduction of documentation effort Particularly in work preparation, there is often an enormous amount of work involved in creating and updating work instructions and process descriptions.
Reduction of training effort New employees are often trained by running along with experienced employees. By providing intuitively understandable knowledge, new employees are productive faster and experienced employees are relieved.
Increasing audit safety By making it easy to provide evidence of activities performed and qualifications held, audit safety increases. For some industries, these certifications represent core requirements for collaboration.
Increasing the attractiveness of the working environment New generations expect a working environment that can be compared to the digital experience of their private life.
A safer work environment Last but not least: By digitally capturing risks, live communication and continuous analysis of safety findings, you create a permanently safe working environment.
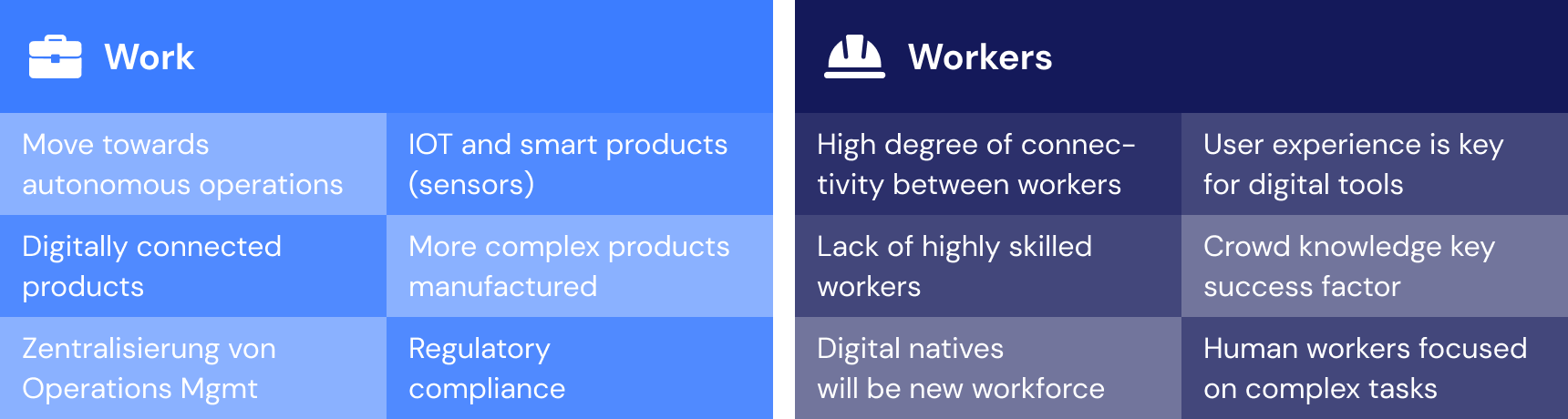
What is the difference between a Connected Worker platform and a worker assistance system?
The Center of Excellence for SMEs 4.0 Saarbrücken defines worker assistance systems as follows: "Worker assistance systems help your employees in manual assembly to carry out processes quickly and correctly. They display information and check processes for correct execution. In this way, they contribute to reduced error rates, ensure product quality and save costs." Worker assistance or worker information systems are thus commonly understood to provide cognitive or physical support for assembly activities. The platform term in the Connected Worker Platform, on the other hand, describes the broad area of application of the solution, which is often modular in design and aimed at holistic technological networking of employees.
The advantages of a Connected Worker solution over a worker assistance system are thus manifold: First, it increases the flexibility for companies to deploy operational employees because they only need training for one software for different use cases. At the same time, this reduces complexity for internal IT. Due to the novelty of this category, most software providers build on a software-as-a-service model. User companies thus benefit from continuous further development of the solution. In the case of stationary assembly with a high division of labor, however, classic worker assistance systems will continue to be used but supplemented by augmented reality tools and artificial intelligence. Assembly errors can thus be detected by image recognition, for example, and a transfer of the defective part can be blocked.
In our related blog post "Worker assistance system: 4 key factors for success" you will find more valuable information on worker assistance systems and the appropriate selection for your company.
Connected Worker Platform: Typical Use Cases as seen by Gartner
The use cases of Connected Worker Platforms are very diverse and can be categorized in different ways. Leading market research firm Gartner chooses five key use cases for Connected Work, as shown in the following graphic.
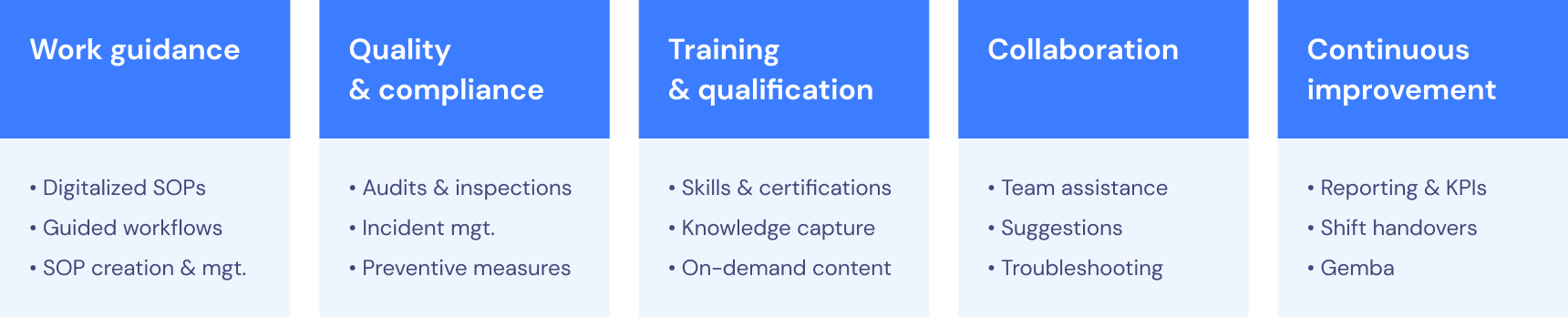
In Operations1, we distinguish between application areas that are oriented to the production areas: Maintenance, Quality, Assembly, Audits, HSSE/Safety, Continuous Improvement/OPEX, Service and Logistics. In addition to these use cases, there are numerous use cases such as SOPs, inspection procedures, TPM, preventive maintenance, commissioning, gemba walks, shift handovers, learning, incident management and many more.
How do you choose the right Connected Worker Platform for you?
The diversity of technological solutions has its origin in the diversity of operational activities. In our experience, the following steps help to find a suitable solution for one's own company:
Formulate goals Which process-related or economic goals are being pursued? A clear formulation of goals helps to have a guiding star in complex technical issues.
Define clear responsibilities Who plays which role in finding a solution? Which departments need to be involved, what are the reservations and interests of internal IT, the works council and the legal department? Who is authorized to make decisions up to what budget?
Research solutions Online research, industry events, and the company's own network are good starting points for research.
Establish evaluation criteria To make an objective selection, evaluation criteria such as ROI, user-friendliness, flexibility and scalability should be established in advance.
Contact solution providers Online, most solution providers offer the option to contact them via a form. Web demos are a good way to get deeper insights into a solution and ask questions.
Compare solutions Using evaluation criteria, solutions can be compared and a favored solution can be extracted.
Clarify purchasing process In the procurement of new technology, other parties are often involved in addition to purchasing, depending on the order volume. In order to quickly create operational added value, it is advisable to inquire about and record one's own purchasing process.
Why usability and scalability are so important
Of course, covering the objectives on the functionality side is a key success factor. In our experience, however, the factors of user-friendliness and scalability play an enormous role in the success of digitization projects. As discussed at the Connected Manufacturing Worker Event in London 2022, high adoption of the solution is central to a significant effect, ergo savings, quality improvements, safety improvements. Here, many user companies complained of low adoption of bulky solutions, so that the desired benefits of digitization measures did not materialize.
To achieve these benefits across the board, the solution must be highly scalable. Here, it is worthwhile to understand the technical infrastructure of the solutions examined. Keywords such as connectivity, comprehensive rights and role management, SSO, and a scalable data model are important for transferring solutions from a pilot phase to a company-wide rollout.
Connected Worker Platform Case Study: How Does Industry Benefit?
Connected Worker Platform Case Study: How Does Industry Benefit?
The versatility of a Connected Worker platform results in different benefits for user companies. In our compact case study of automotive supplier Hirschvogel, we describe how Hirschvogel benefits by providing real-time process knowledge, digital planning of activities, and collaborative troubleshooting. Results include:
60% reduction in downtime in international plants
50% reduction in process deviations
Savings of €250,000 per site by eliminating the need for external service providers
These results impressively demonstrate the added value a Connected Worker platform creates. In addition to measurable benefits, such a platform can also help to increase flexibility in the organization, sustainably secure knowledge, and provide a lever for attracting new employees, as incentives are created through a modern working environment.
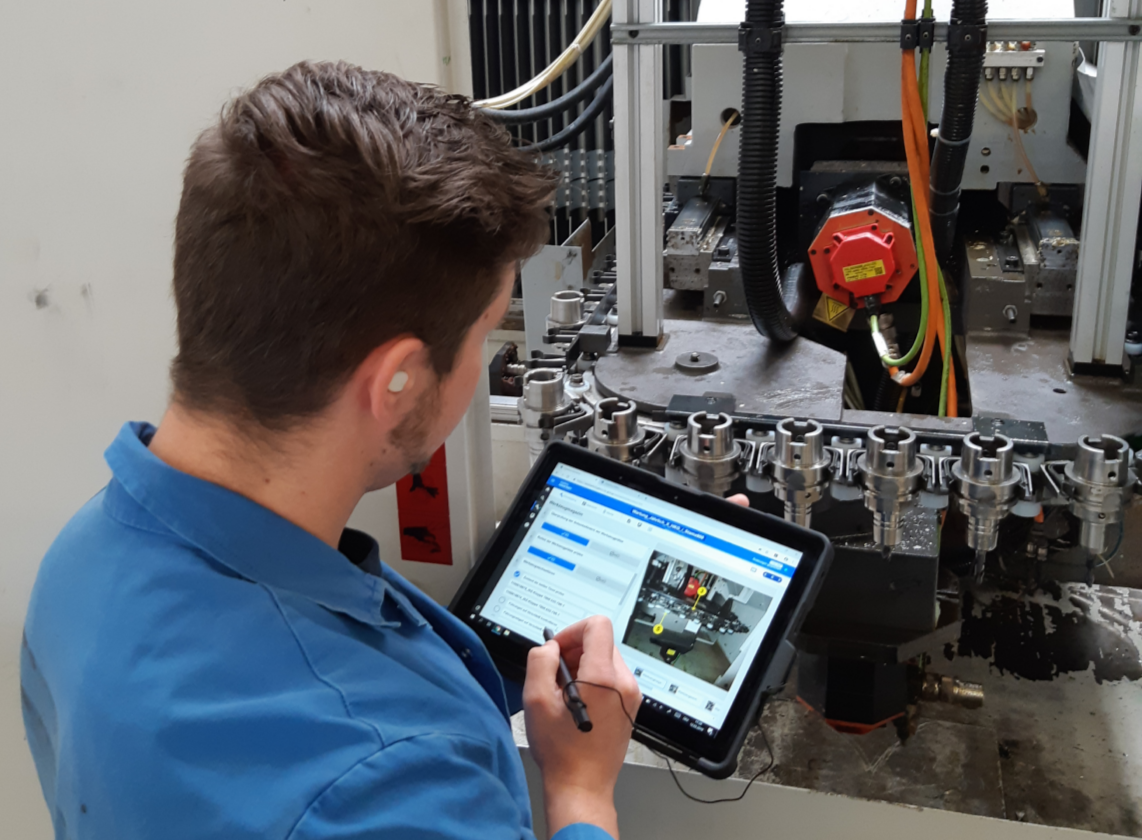
Conclusion: Operational employees have mostly been neglected in digitization initiatives. With Connected Worker Platforms, this is now changing.
Want to learn more or even test Operations1's Connected Worker Platform?
Please fill out the contact form with your thoughts and goals. We will get back to you immediately.
Who is using a Connected Worker Platform already?
Leading industrial companies already rely on the Operations1 platform. Learn more in the video.
Markus Glotzbach
During his professional career, Markus gained deep insights at companies and large groups in different industries and knows the digitalization hurdles and problems on the shopfloor. Before joining Operations1, he studied International Management (MA) and worked in the Cloud Computing as well as SaaS telematics sector.