What it is about
In this blog post, we'd like to share our key impressions from the Connected Manufacturing Worker event in London: What's driving executives from the world's leading companies to digitally support their operational workforce?
10 years after coining the term Industry 4.0, we are still at the beginning
During the multifaceted talks on site, it becomes clear - the value of the digitization of collaborative, human-led processes varies greatly. While Daniel Grobe (CCO Operations1) talks in his keynote about how the status quo in industry currently includes digital PDFs on large screens, complex ERP and MES interfaces on the shopfloor, and occasional low-scalability augmented reality (AR) pilots, he earns a lot of grinning head nods from the auditorium at the Connected Manufacturing Worker conference in London. After all, many lighthouse projects relate to lead plants, and solutions that bring noticeable operational and business added value have not yet arrived on a broad scale.
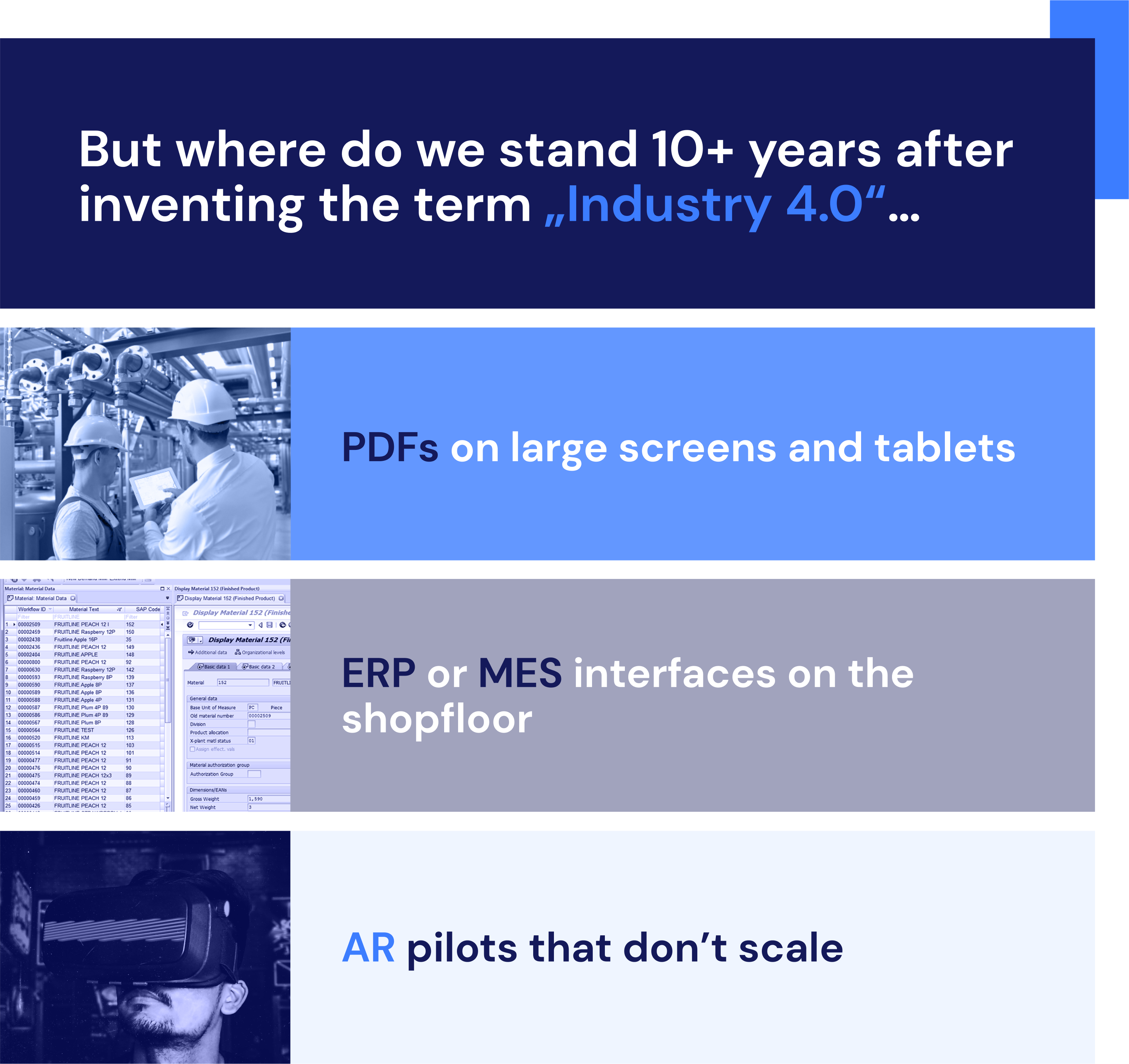
The Event: Connected Manufacturing Worker (CMW) Conference in London
The CMW Conference is a cross-industry event for international leaders of manufacturing companies in London. Delegations from companies such as Ford, GSK, BP, Philips, Lego and Carlsberg engage in interactive formats to discuss challenges and practical solutions to support the operational workforce to increase innovation, productivity and quality in their manufacturing networks. In this context, we from Operations1 had the opportunity to deliver a keynote on "How connected work enables future-proof plant operations" and discuss with the participants in interactive sessions.
What is Connected Work?
Basically, Connected Work can be understood as the connection of frontline workers. The term is primarily used to describe the organizational, process and technological networking of operational, so-called "deskless" employees: Typically employees in production, logistics or other production-related support processes. Here, the organizational connection comprises the horizontal connection of employees in the production environment as well as the vertical connection to the management level through simplified communication and information supply. The process-related component comprises the bridging of system breaks in the execution of processes - in other words, the elimination of manual data transfers and time-consuming information gathering. The technological solution is the basis for realizing this connection.
Market research firm Gartner describes Connected Work as follows: Connected Workers use various digital tools and data management techniques to enhance and integrate their interactions with the physical and virtual environment while improving decision accuracy, increasing knowledge and reducing variability.
Connected Work in practice: companies demonstrate measurable, significant successes
The use cases and technological approaches presented at the Connected Manufacturing Worker event vary. Medtech company Philips, for example, benefited in particular from applications that achieved high user adoption across the board. In the training and onboarding area, efforts could be reduced by 30-50%. An Andon app has also reduced the time-to-fix in maintenance by 50%, which in turn can have an enormous impact on delivery reliability and customer satisfaction. In a technically comparatively simple solution, employees can record incidents digitally, route them to the appropriate specialists and classify them at the same time. Communication is thus structured and traceable.
Other companies have reported a 50% reduction in maintenance costs, a 65% reduction in work preparation costs and a positive uptime effect of three percentage points, which corresponds to annual financial savings in the seven-digit range. The benefits are thus manifold and strongly depend on the use case and context, but show significant potential.
From our own project experience, we can confirm such successes. In addition to the increase in process reliability and increased responsiveness, the efficiency gains resulting from the introduction of a Connected Work solution often stand out. In customer studies, we have been able to measure increase rates of up to 21%, which are associated in particular with the reduction of complexity for the operational employee in the process and the elimination of non-value-added activities, as shown in the following graphic.
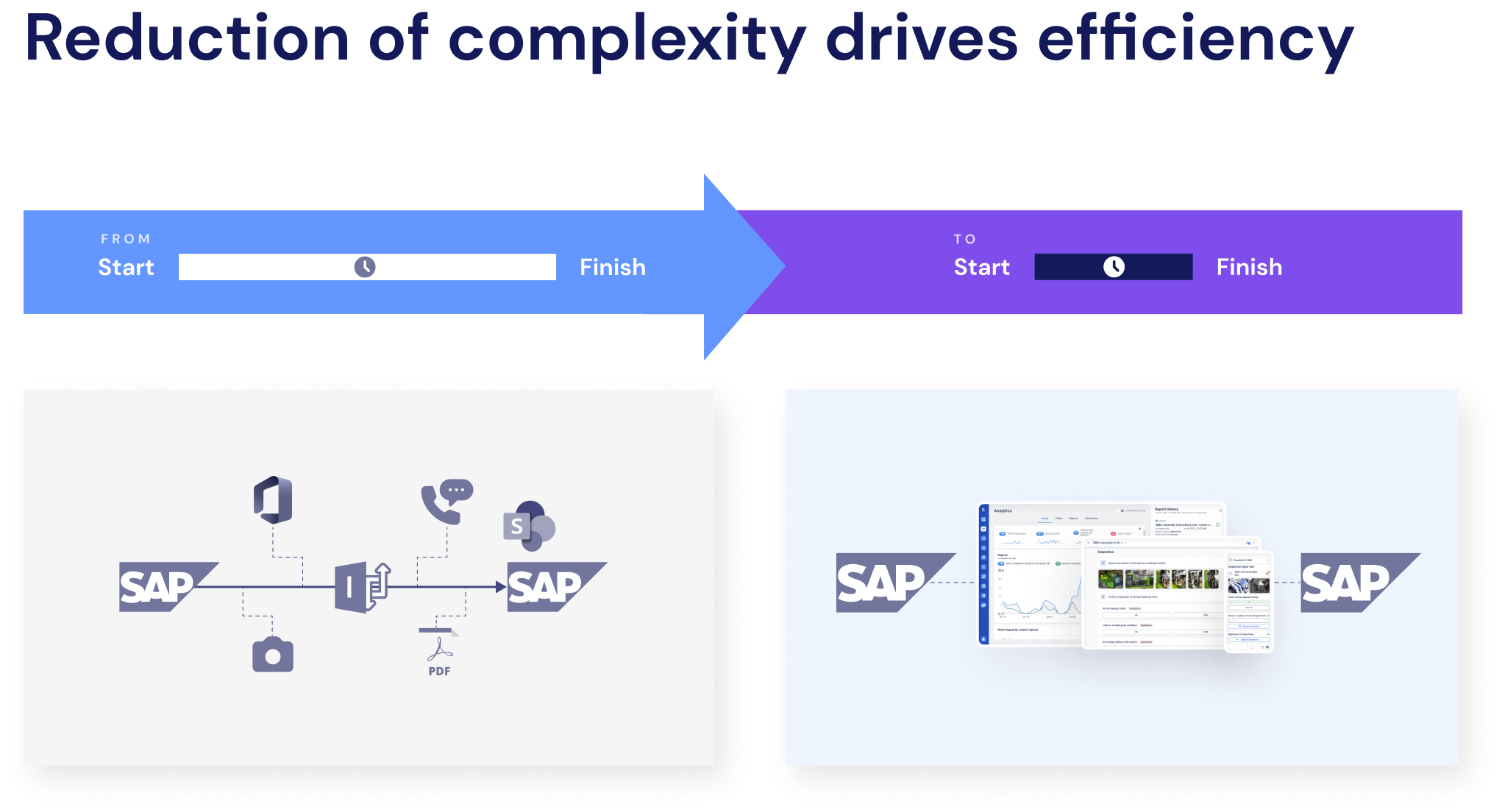
Simplicity and scalability: two success factors for selecting the right technology
The two factors of simplicity and scalability of solutions were mentioned repeatedly by the participants. On the one hand, simplicity is the key to short onboarding times and thus also to high adoption of new solutions. The risk that solutions are identified, configured, piloted and finally "left lying around" is thus greatly reduced. Scalability is obviously enormously important in order to leverage the benefits proven in pilots across the board and thus bring truly significant added value to the company. These two factors should therefore play a central role in the technology evaluation.
In-house development vs. off-the-shelf software: which is the right way to go?
As technology was a key topic at the Connected Manufacturing Worker event, the extent to which manufacturing companies should develop software solutions for their production in-house was also discussed at length. Typically, the goal of in-house development is to meet the catalog of requirements one hundred percent. However, it became clear from the discussions that in-house developments lead to enormous challenges, especially in the case of an international production network. Despite standardization efforts, production sites have multiple differences and there is a risk that internal IT will be overloaded and paralyzed by a high number of, possibly even conflicting, feature requests. In addition, the higher risk of failure was mentioned, as well as the lack of access to developers, which makes in-house developments very difficult. You can read a comprehensive evaluation of this in our blog post Individual software vs. standard software.
Conclusion: Connected Work is a growth area
At the conference, it became clear that the focus on supporting operational employees will continue to increase. Pioneering companies can demonstrate significant, measurable success. Most recently, this increasing relevance can be seen in the fact that companies such as Henkel are creating their own positions such as "Manager Connected Factory Worker" to address digitization potential for operational employees.
Would you like to get in touch?
Would you like to share your opinion or do you have questions about Connected Work? Then fill out the contact form. We will get back to you promptly with an appropriate response.
Markus Glotzbach
During his professional career, Markus gained deep insights at companies and large groups in different industries and knows the digitalization hurdles and problems on the shopfloor. Before joining Operations1, he studied International Management (MA) and worked in the Cloud Computing as well as SaaS telematics sector.