Worum es geht
In diesem Blogbeitrag möchten wir unsere zentralen Eindrücke vom Connected Manufacturing Worker Event in London teilen: Was bewegt die Führungskräfte von weltweit führenden Unternehmen bei der digitalen Unterstützung Ihrer operativen Mitarbeiter?
10 Jahre nach Prägung des Begriffs Industrie 4.0 stehen wir noch am Anfang
Bei den vielseitigen Gesprächen vor Ort wird klar – die Wertigkeit der Digitalisierung von kollaborativen, menschengeführten Prozessen ist sehr unterschiedlich. Während Daniel Grobe (CCO Operations1) in seiner Keynote davon spricht, dass der Status Quo in der Industrie aktuell digitale PDFs auf großen Screens, komplexe ERP und MES-Interfaces auf dem Shopfloor und gelegentlich wenig skalierbare Augmented Reality (AR)-Piloten umfasst, erntet er dafür viel grinsendes Kopfnicken aus dem Auditorium der Connected Manufacturing Worker Konferenz in London. Viele Leuchtturmprojekte beziehen sich schließlich auf Leitwerke und in der Breite sind Lösungen, die einen merklichen operativen und betriebswirtschaftlichen Mehrwert bringen, noch nicht angekommen.
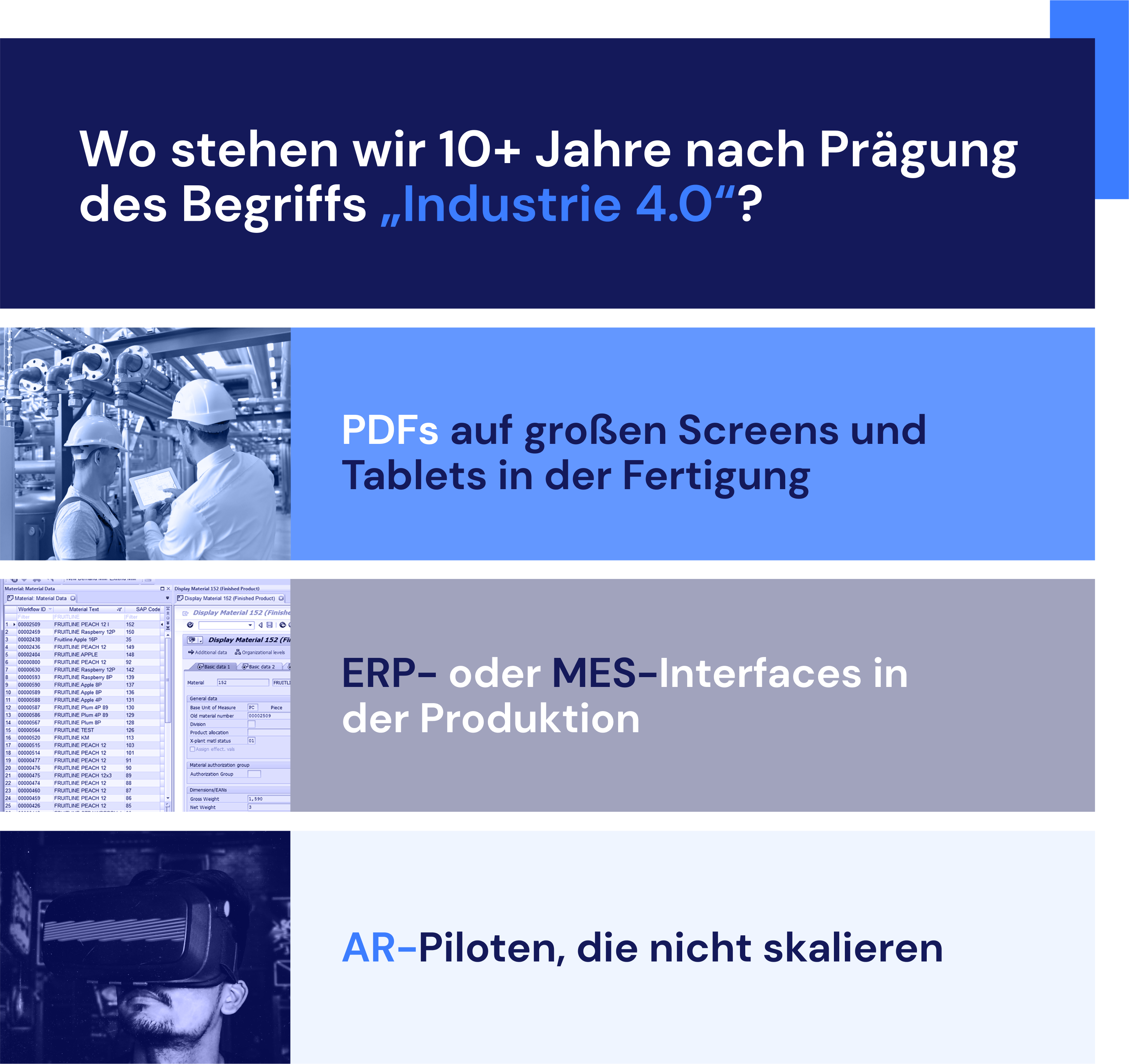
Das Event: Connected Manufacturing Worker (CMW) Konferenz in London
Die CMW Konferenz ist eine industrieübergreifende Veranstaltung für internationale Führungskräfte produzierender Unternehmen in London. Delegationen von Unternehmen wie Ford, GSK, BP, Philips, Lego und Carlsberg diskutieren in interaktiven Formaten über Herausforderungen und praxisnahe Lösungen zur Unterstützung der operativen Belegschaft, um Innovation, Produktivität und Qualität in ihren Fertigungsnetzwerken zu steigern. Dabei hatten wir von Operations1 die Gelegenheit, eine Keynote zum Thema „How connected work enables future-proof plant operations“ zu halten und in interaktiven Sessions mit den Teilnehmern zu diskutieren.
Was ist Connected Work?
Grundsätzlich lässt sich Connected Work als die Vernetzung von Arbeitskräften verstehen. Der Begriff wird vorrangig verwendet, um die organisatorische, prozessuale und technologische Vernetzung von operativen, sogenannten „schreibtischlosen“ Mitarbeitern zu beschreiben: Typischerweise Mitarbeitern in der Produktion, Logistik oder weiteren produktionsnahen Supportprozessen. Hierbei umfasst die organisatorische Vernetzung die horizontale Vernetzung der Mitarbeiter im Produktionsumfeld sowie die vertikale Vernetzung zur Management-Ebene durch eine vereinfachte Kommunikation und Informationsbereitstellung. Die prozessuale Komponente umfasst die Überbrückung von Systembrüchen bei der Durchführung von Prozessen – in der Regel also die Eliminierung von manuellen Datentransfers und aufwändiger Informationsbeschaffung. Die technologische Lösung ist dabei die Basis zur Realisierung dieser Vernetzung.
Das Marktforschungsunternehmen Gartner beschreibt Connected Work wie folgt: Connected Worker nutzen verschiedene digitale Tools und Datenverwaltungstechniken, um ihre Interaktionen mit der physischen und virtuellen Umgebung zu verbessern und zu integrieren und gleichzeitig die Entscheidungsgenauigkeit zu verbessern, das Wissen zu vermehren und Abweichungen zu verringern.
Connected Work in der Praxis: Unternehmen weisen messbare, signifikante Erfolge auf
Die vorgestellten Anwendungsfälle und technologischen Ansätze beim Connected Manufacturing Worker Event sind unterschiedlich. Das MedTech-Unternehmen Philips profitiert beispielsweise insbesondere von Applikationen, die in der Breite eine hohe Nutzerakzeptanz erzielen konnten. Im Anlernbereich konnte der Trainingsaufwand um 30-50% reduziert werden. Durch eine Andon-App konnten zudem in der Instandhaltung die Time-to-Fix, also die Zeit von einem Vorfall bis zur Behebung um 50% reduziert werden, was wiederum enormen Einfluss auf Liefertreue und Kundenzufriedenheit haben kann. In einer technisch vergleichsweise einfachen Lösung können Mitarbeiter Störfälle digital erfassen und zu entsprechenden Fachkräften routen und diese im gleichen Zuge klassifizieren. Die Kommunikation erfolgt somit strukturiert und nachvollziehbar.
Andere Unternehmen berichteten von Rückgängen der Instandhaltungskosten um 50%, einer Reduzierung des Aufwands für die Arbeitsvorbereitung um 65% und einem positiven Uptime-Effekt um drei Prozentpunkte, welcher finanziell jährlich siebenstelligen Einsparungen entspricht. Die Vorteile sind somit mannigfaltig und hängen stark vom Anwendungsfall und Kontext ab, weisen aber signifikantes Potential auf.
Aus eigener Projekterfahrung können wir solche Erfolge bestätigen. Neben der Steigerung der Prozesssicherheit und einer gesteigerten Reaktionsfähigkeit stehen häufig die Effizienzsteigerungen durch die Einführung einer Lösung für Connected Work zu Buche. In Kundenstudien konnten wir Steigerungsraten von bis zu 21% messen, welche insbesondere durch die Reduktion von Komplexität für den operativen Mitarbeiter im Prozess und die Eliminierung nicht-wertschöpfender Tätigkeiten einhergeht, wie in folgender Grafik dargestellt.
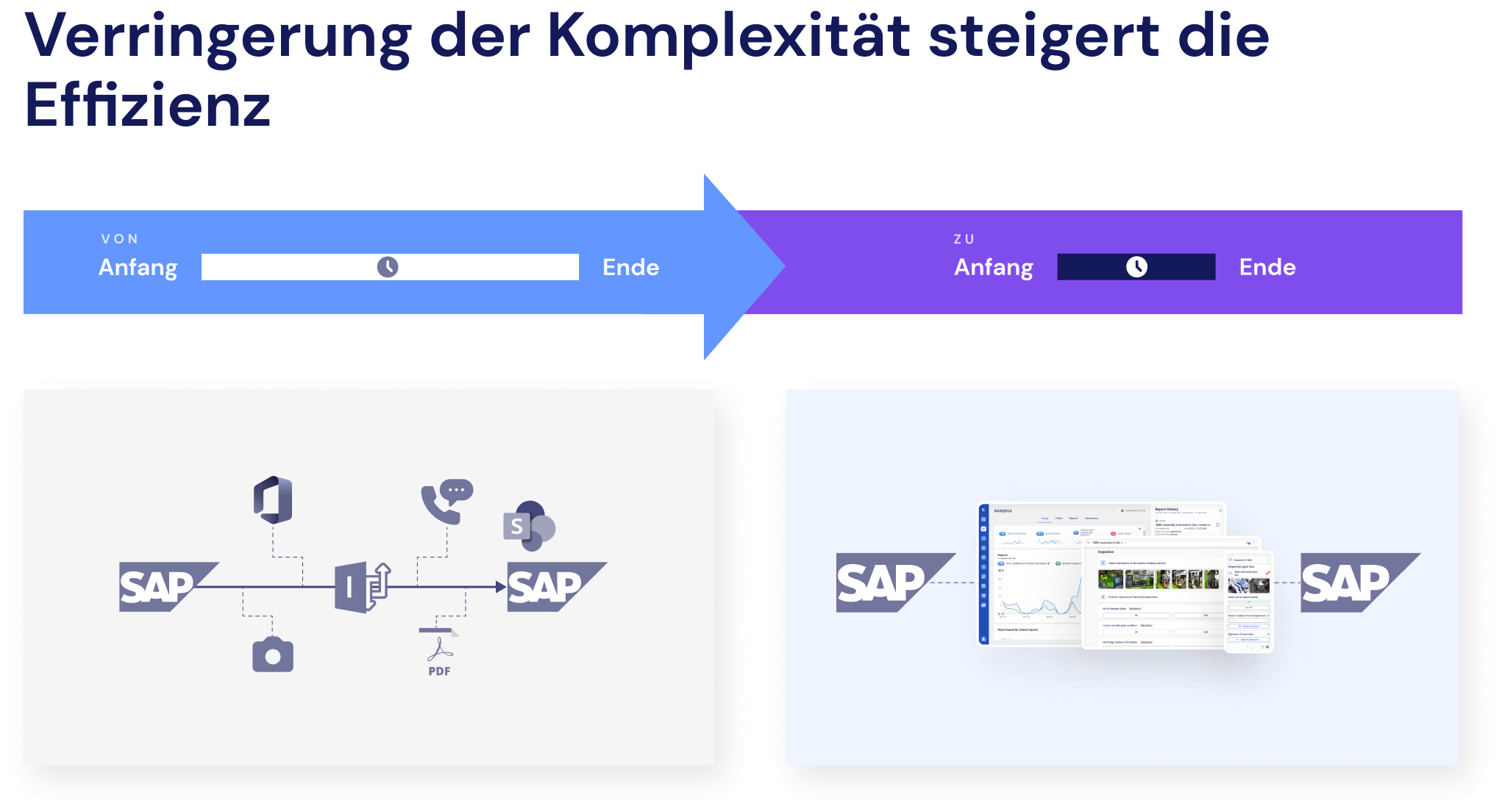
Einfachheit und Skalierbarkeit: Zwei Erfolgsfaktoren für die Auswahl der richtigen Technologie
Die beiden Faktoren Einfachheit und Skalierbarkeit von Lösungen wurden wiederkehrend von den Teilnehmern genannt. Einfachheit ist dabei zum einen der Schlüssel für kurze Anlernzeiten und somit auch einer hohen Adoption von neuen Lösungen. Das Risiko, dass Lösungen aufwändig identifiziert, konfiguriert, pilotiert und schlussendlich „liegen gelassen“ werden, sinkt somit stark. Skalierbarkeit ist offenkundig enorm wichtig, um flächendeckend die Vorteile zu heben, welche in Piloten bewiesen wurden. Somit kann wirklich signifikanter Mehrwert für das Unternehmen gebracht werden. Diese beiden Faktoren sollten bei der Technologiebewertung somit eine zentrale Rolle spielen.
Eigenentwicklung vs. Standardsoftware: Was ist der richtige Weg?
Da Technologie auf dem Connected Manufacturing Worker Event ein Schwerpunktthema war, so wurde auch ausführlich darüber diskutiert, inwieweit produzierende Unternehmen Softwarelösungen für Ihre Produktion intern entwickeln sollten. Ziel einer Eigenentwicklung ist typischerweise die hundertprozentige Erfüllung des Anforderungskatalogs. Aus den Gesprächen ging jedoch hervor, dass Eigenentwicklungen gerade bei einem internationalen Fertigungsnetzwerk zu enormen Herausforderungen führen. Trotz Standardisierungsbemühungen weisen Produktionsstätten vielfältige Unterschiede auf und es besteht die Gefahr, dass die interne IT durch eine hohe Anzahl, möglicherweise sogar konfliktionärer Feature-Requests überfrachtet und gelähmt wird. Zudem wurden das höhere Risiko zu scheitern genannt, sowie der mangelnde Zugriff auf Entwickler, welches Eigenentwicklungen stark erschwert. In unserem Blogbeitrag Individualsoftware vs. Standardsoftware lesen sie hierzu eine umfassende Bewertung.
Fazit: Connected Work ist ein Wachstumsfeld
Auf der Konferenz wurde klar, dass der Fokus auf die Unterstützung operativer Mitarbeiter weiter zunehmen wird. Vorreiterunternehmen können signifikante, messbare Erfolge vorweisen. Zuletzt merkt man diese zunehmende Relevanz darin, dass Unternehmen wie Henkel eigene Stellen wie den „Manager Connected Factory Worker“ schaffen, um sich mit Digitalisierungspotenzialen für operative Mitarbeiter auseinander zu setzen.
Sie möchten Kontakt aufnehmen?
Möchten Sie Ihre Meinung teilen oder haben Fragen zum Thema Connected Work? Dann füllen Sie das Kontaktformular aus. Wir melden uns umgehend mit einer entsprechenden Antwort bei Ihnen.
Markus Glotzbach
Während seiner beruflichen Laufbahn sammelte Markus tiefe Einblicke bei Unternehmen und Konzernen unterschiedlicher Industrien und kennt die Digitalisierungshürden und Probleme auf dem Shopfloor. Vor seinem Wechsel zu Operations1 studierte er International Management (MA) und war im Cloud Computing- sowie im SaaS-Telematik-Bereich tätig.