Worum es geht
In diesem Blogbeitrag lernen Sie die gängigen Verschwendungsarten kennen und erfahren, wie der Einsatz einer Software Ihre Ressourcen optimal schont.
Was sind die 7+1 Verschwendungsarten / Muda?
Muda (japanisch „Verschwendung“), kommt aus der Operational Excellence- und Lean Management-Begriffswelt und beschreibt Aktivitäten, die Ressourcen verbrauchen und Kosten verursachen, aber keinen Mehrwert erzeugen. Beschrieben wurden diese Verschwendungsarten erstmals von Taiichi Ohno, dem Entwickler des Toyota Produktionssystems. In einer nachhaltigen, effizienten Produktion müssen alle nicht wertschöpfenden, verschwenderischen Tätigkeiten eliminiert oder weitestgehend reduziert werden. Ohno nennt 7 Bereiche, in denen Verschwendung auftreten kann:
#1 Transport
Lange, überflüssige Transportwege innerhalb einer Produktionshalle können Aufwand erzeugen. Ineffiziente Materialflüsse können auch beim Ein-, Aus- und Umlagern anfallen.
#2 Inventar
Zu hohe Material- und Lagerbestände binden Platz und damit Kapital. Damit können sowohl Fertigungserzeugnisse als auch Roh- und Betriebsstoffe gemeint sein.
#3 Bewegung
Lange Laufwege, Suchzeiten und ineffizient aufgebaute Arbeitsstationen, bei denen Mitarbeiter umständlich umgreifen oder um Maschinen herumlaufen müssen fallen unter die Verschwendung durch Bewegung.
#4 Wartezeiten
Wartezeiten bedeuten Stillstand in der Produktion. Maschinenstillstände, lange Rüstzeiten sowie die vorher genannten Verschwendungsarten können zu langen, nicht wertschöpfenden Wartepausen führen.
#5 Überproduktion
Überproduktion entsteht vor allem aufgrund schlechter Planung. Aber auch Qualitätsmängel können zu Überschuss führen. In diesem Fall wird „vorsorglich“ mehr produziert.
#6 Überbearbeitung
In diesem Fall spricht man auch von „Over Engineering“. Prozesse sind künstlich aufgebläht oder zu komplex und führen dadurch zu unnötiger Ressourcenbindung.
#7 Defekte
Produktionsfehler führen zu Ausschussproduktion. Diese Verschwendungsart ist die offensichtlichste und natürlich zu vermeiden. Aber häufig ist auf den ersten Blick nicht sofort ersichtlich, wo der Fehler liegt.
Im Englischen ergeben die sieben Verschwendungsarten das Akronym TIMWOOD (Transport, Inventary, Motion, Waiting, Overproduction, Overprocessing, Defects), welches man noch in älteren Ratgebern findet.
Seit einigen Jahren wird Ohno’s Konzept um eine weitere, oft unterschätzte Verschwendungsart ergänzt:
#8 Ungenutzte Mitarbeiterpotentiale
Mitarbeiterwissen und -qualifikation werden falsch eingesetzt. Mitarbeiter, die nicht entsprechend ihrer Qualifikation eingesetzt werden und auf deren wertvolle Erfahrung man nicht zurückgreift, sind verschwendetes Potential. Das haben Lean Methoden, die beim Streben nach operativer Exzellenz helfen, in den vergangenen Jahren zum Glück auch erkannt. Hier geht es nicht nur darum, die „Ressource Mensch“ möglichst gewinnbringend einzusetzen. Es geht um Wertschätzung und das gemeinsame Erreichen von Unternehmenszielen.
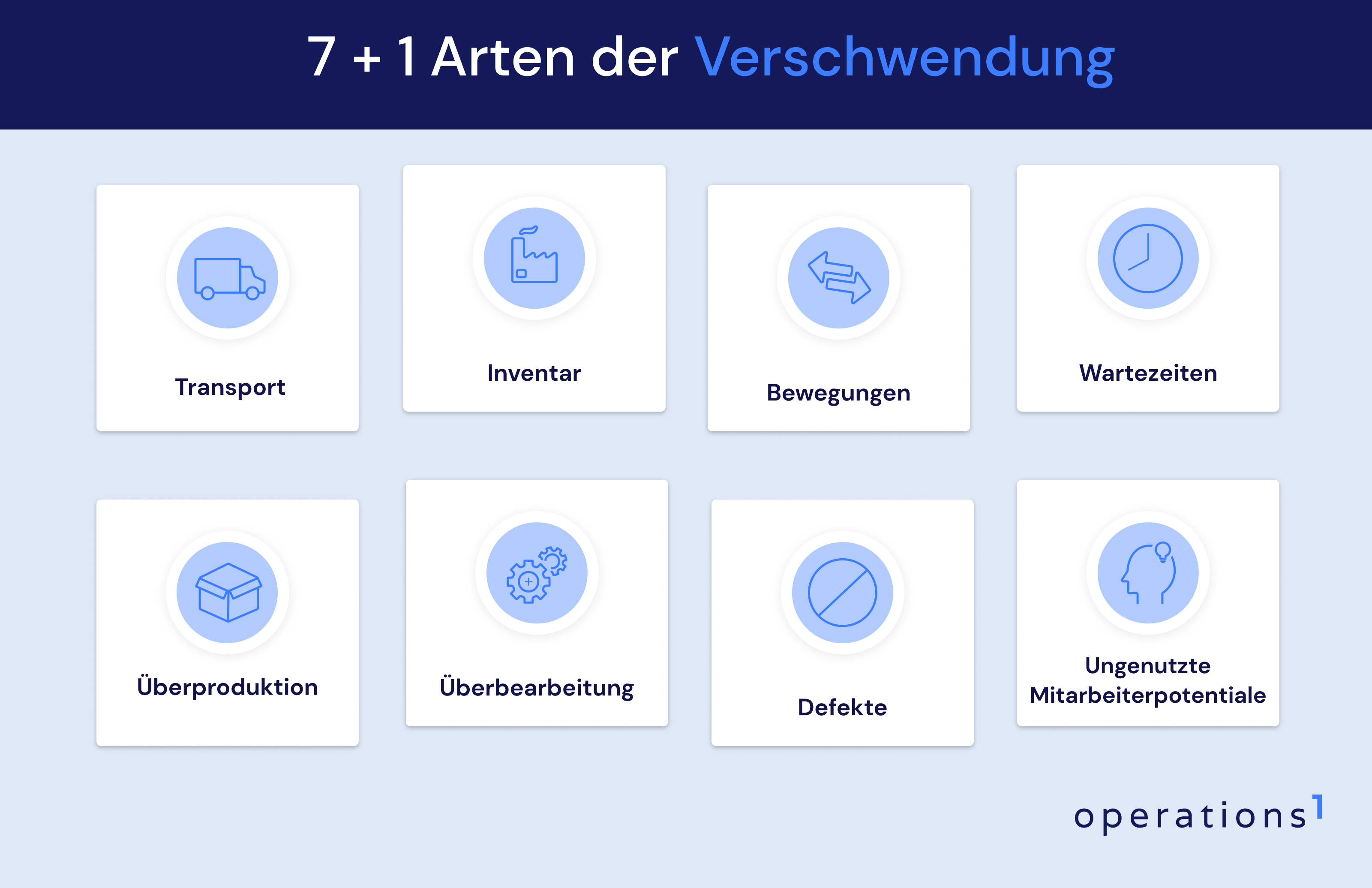
Papierbasiertes Arbeiten: Brandbeschleuniger für ineffiziente Prozesse
Kein Unternehmen verursacht mehrere oder gar alle acht Verschwendungsarten. Das würden Betriebe langfristig nicht überleben. Aber, im Zuge von Operational Excellence-Programmen, lassen sich in jedem Bereich der Wertschöpfungskette noch kleine Stellschrauben identifizieren, die optimiert und verschlankt werden können. Im produzierenden Gewerbe ist es oftmals papierbasiertes Arbeiten, was Prozesse behäbig werden lässt und somit Verschwendung verursacht. Prüfprozesse, Montage- und Instandhaltungsarbeiten, Wareneingangskontrollen oder Schichtübergaben: viele dieser Prozesse und Arbeitsgänge finden mithilfe papierbasierter Arbeitsanweisungen und Checklisten statt. Die Folge: Fehler, Qualitätsprobleme und vermeidbare Aufwände. Digitale Tools können diese Aufwände reduzieren und damit verschwenderischen Tätigkeiten entgegenwirken.
Software für Arbeitsanweisungen und Checklisten: Digitaler Feuerlöscher gegen Verschwendung
Gerade im Mittelstand kann Software einen großen Beitrag zur Reduzierung komplexer, aufwändiger Prozesse leisten. Track & Trace-Lösungen wirken ineffizienten Transportwegen und Materialbewegungen entgegen, während ERP- und MES-Systeme Produktionsplanung steuern. Mitarbeitergeführte Prozesse bleiben aber häufig analog, was nicht zuletzt daran liegt, dass operative Mitarbeiter „deskless“ sind. Informationen erreichen sie nur zeitverzögert oder sind veraltet. Die Verschwendungen, die so entstehen, lassen sich aber zum Glück mit digitalen Tools ebenfalls einfach verhindern.
Adaptive Process Ecexution (APE) Software setzt bei den operativen Mitarbeitern auf dem Shopfloor an und unterstützt sie bei der täglichen Ausführung ihrer Tätigkeiten. Mit end-to-end-integrierten Softwarelösungen werden Mitarbeiter intuitiv durch Arbeitsvorgänge geführt. Papierlisten weichen mobilen Endgeräten wie Tablets oder Smartphones. Die Vorteile:
Fehler & Defekte reduzieren: Medienbasierte Arbeitsanweisungen und Checklisten steigern sprach- und qualifikationsunabhängig das Prozessverständnis. Arbeiten werden schneller zuverlässig durchgeführt.
Wegezeiten minimieren: Wege- und Wartezeiten entfallen, da Live-Kollaboration und direkte Aufgabenzuweisung möglich sind. Bei aufgetretenen Problemen müssen Mitarbeiter nicht erst Ihre Vorarbeiter suchen und das Problem erklären, da die Einbindung von Fehlerbildern möglich ist.
Komplexität rausnehmen: Bei komplexen, variantenreichen Produkten kann die richtige Software bis zu 100% des ursprünglichen Erstellaufwands für Arbeitsanweisung einsparen. Mit Drag & Drop Funktionalitäten können z.B. variantengerechte Informationen direkt aus dem ERP gezogen werden. Überproduktion und Over Engineering werden damit verhindert, da Mitarbeiter die richtigen und für sie relevanten Informationen kontextbasiert am richtigen Ort und zu richtigen Zeit erhalten. Auch auf Rüstzeiten in komplexen Produktionen wirkt sich das positiv aus. Anlagenumrüstung gelingt mit digitalen Anleitungen schneller.
Bestände optimieren: Auch Prüfchecklisten für Wareneingangs- oder Warenausgangskontrollen können digital bereitgestellt werden. Das minimiert Verschwendung beim Inventar und Materialflüssen.
Transparenz steigern: Integrierte Software bildet die „letzte Meile“ zum Werker ab. APE-Software ermöglicht Transparenz und eine einfache, intelligente Auswertung operativer Arbeitsprozesse. Die vollständige Integration in die firmeneigene Systemlandschaft hilft dabei, Probleme in Echtzeit zu beheben und Zeitverschwendung vorzubeugen.
Fazit
Unternehmen, die schlanker und effizienter werden möchten, müssen verschwenderische Prozesse eliminieren. Die 7 + 1 Arten der Verschwendung nach Ohno helfen dabei, potenziell betroffene Bereiche zu identifizieren. In allen acht Bereichen trägt oftmals papierbasiertes Arbeiten in operativen Bereichen zur Verschwendung bei. Digitale Arbeitsanweisungen und Checklisten können dem entgegenwirken. Mit einer Softwarelösung können alle nicht wertschöpfenden Prozesse auf dem Shopfloor eingedämmt werden.
Sie möchten erfahren, wie Sie Verschwendungen mit Software entgegenwirken können?
Operations1 kann nicht wertschöpfenden Prozessen und Verschwendungen im Produktionsumfeld entgegenwirken. Die einfache, intuitive End-to-End-Software unterstützt Ihre Mitarbeiter bei dem täglichen Ausführen ihrer Aufgaben. Ohne Produktivitäts- und Papierverschwendung. Lesen Sie, wie Ihre Produktion mithilfe digitaler Arbeitsanweisungen schlanker und effizienter wird:
Editha Bertsch
Editha ist eine erfahrene Expertin im Bereich Projektmanagement für produzierende Unternehmen. Mit einem klaren Verständnis für die spezifischen Herausforderungen der Branche arbeitet sie leidenschaftlich daran, innovative Lösungen zu entwickeln.