Worum es geht
In diesem Blogbeitrag geben wir Ihnen einen umfassenden Überblick über den komplexen Themenbereich Operational Excellence. Was bedeutet der Ansatz und warum ist er so wichtig? Wir zeigen, welche Begriffswelten und Methoden dazugehören und warum produzierende Unternehmen sich heute mit der Umsetzung des Ansatzes schwertun – obwohl der Ansatz eigentlich aus der Fertigung gewachsen ist. Schließlich möchten wir Ihnen Tipps geben, wie Sie Operational Excellence erreichen – und wie Ihnen Digitalisierung dabei helfen kann.
Was ist Operational Excellence?
Definition Operational Excellence
Operational Excellence (OpEx) bedeutet die ganzheitliche Ausrichtung des Unternehmens an der Gesamtstrategie. Sämtliche Prozesse und Systeme entlang der gesamten Wertschöpfungskette werden kontinuierlich im Hinblick auf Kundenbedürfnisse, Qualität und Effizienz optimiert. Exzellente Prozesse steigern die Produktivität, senken Kosten und tragen somit zum langfristigen Unternehmenserfolg bei. Gleichzeitig hat OpEx neben der Optimierung wertschöpfender Kernprozesse auch eine kulturelle und eine organisatorische Dimension: die kontinuierliche und nachhaltige Optimierung funktioniert nur mithilfe aller Mitarbeiter. Daher ist OpEx auch stets ein Teil der Unternehmenskultur. Die Frage, was OpEx nun genau ist, lässt sich somit beantworten mit: OpEx ist ein strategischer Management-Ansatz.
Beispiele Operational Excellence:
Um noch besser zu verstehen, was OpEx ausmacht, hilft es zu verstehen, was es nicht ist. Wenn Bandstillstand droht, weil Komponenten nicht rechtzeitig geliefert werden, wenn ein Bauvorhaben nicht fortgesetzt werden kann, weil gewisse Baustoffe nicht den geforderten Qualitätsstandards entsprechen oder wenn der Customer Service bei einer Reklamation kein sorgfältiges, ergebnisorientiertes Beanstandungsmanagement betreibt, ist keine OpEx gegeben. Die genannten Beispiele zeigen „Fehler im System“ – und zwar über die gesamte Wertschöpfungskette hinweg: in der Logistik, bei der Produktqualität und im Service. Ob ein Unternehmen operativ „exzellent“ ist, entscheidet am Ende der Kunde.
Operational Excellence vs. KVP
Im weiteren Verlauf stellen wir einige Methoden zum Erlangen operativer Exzellenz vor, aber in diesem Abschnitt möchten wir zuerst den Unterschied zwischen OpEx und dem kontinuierlichen Verbesserungsprozess (KVP) beleuchten. Während beide Ansätze sich auf den ersten Blick ähneln – auch KVP verfolgt Maßnahmen zur Effizienzsteigerung durch Erhöhung der Produktivität und dem Aufdecken von Einsparpotentialen – geht OpEx weiter. KVP betrachtet die zyklische Optimierung kleinteiliger Prozesse (Plan – Do – Check – Act) und ist in Unternehmen oftmals im Qualitätsmanagement aufgehangen. Eine dedizierte Gruppe von Mitarbeitern kümmert sich um die Umsetzung von KVP-Maßnahmen. OpEx hingegen ist ein ganzheitlicher, strategischer Ansatz, der von allen Betriebszugehörigen gelebt und umgesetzt werden soll, nicht nur von einer Abteilung. Das Institute for Operational Excellence formuliert es so: "Jeder einzelne Mitarbeiter kann den Wertschöpfungsfluss zum Kunden sehen und diesen reparieren, bevor er zusammenbricht." Der KVP kann als eine Einzelmethode zum Erreichen operativer Exzellenz genutzt werden.
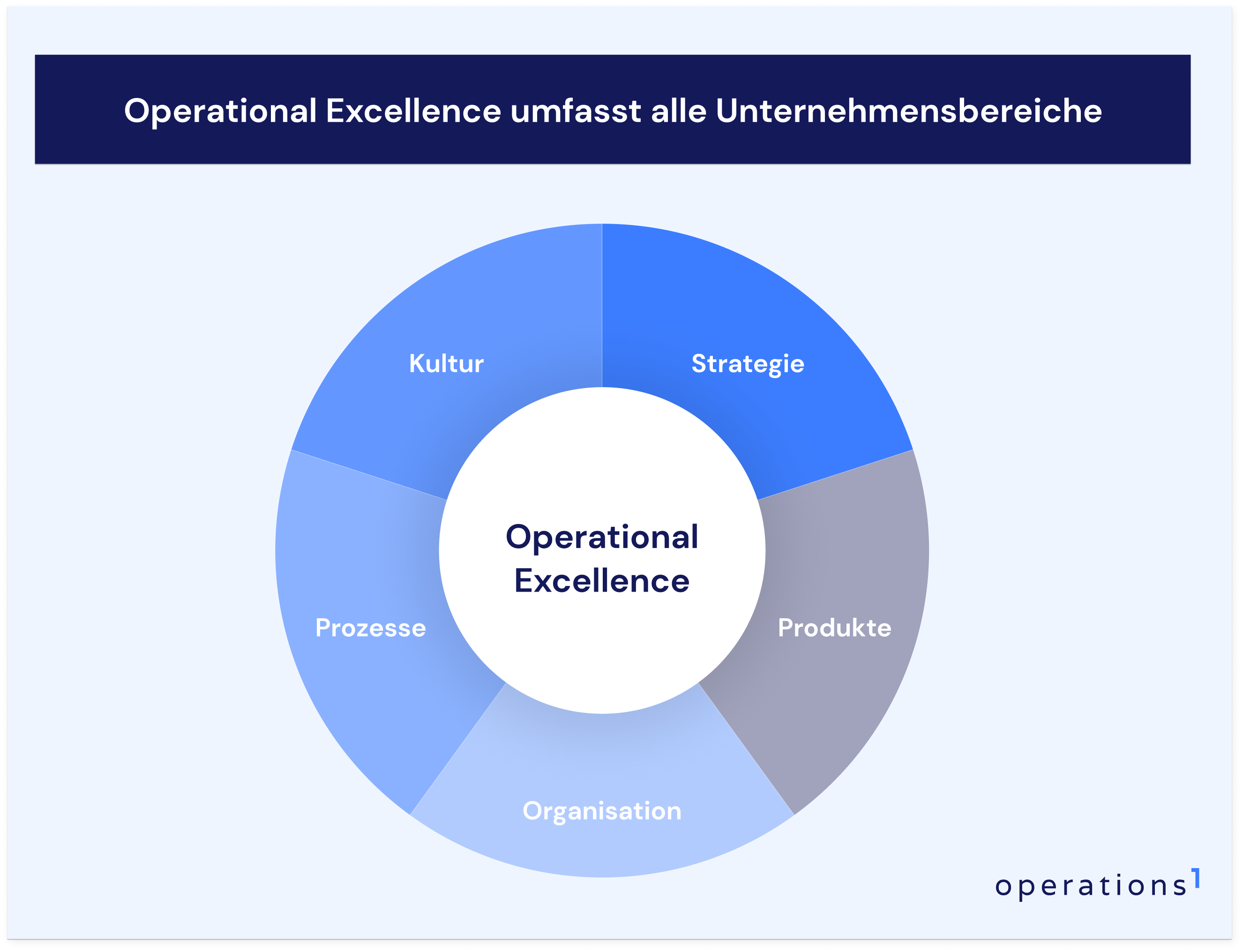
Der Methodenkoffer zu Operational Excellence ist unerschöpflich
Neben dem KVP gibt es noch viele weitere Methoden und Instrumente, die zum Erlangen operativer Exzellenz beitragen können. Typische weitere Schlagworte im Bereich Operational Excellence sind beispielsweise Lean Management, Six Sigma, Kaizen, Target Costing, Supply Chain Management, Gemba Walks, Rüstzeitoptimierung, die sieben Arten der Verschwendung, Total Productive Maintenance und viele mehr. Es existiert somit ein enorm großer Methodenkoffer, in dem man sich bei der Umsetzung von Operational Excellence-Programmen bedienen kann. Die wichtigsten auf einen Blick:
Kaizen
= schrittweise Optimierung, Prozess-Wissen.
Kaizen (Kai = Veränderung, Wandel; Zen = zum Besseren) kommt aus dem japanischen und wird oftmals mit KVP gleichgesetzt. Der Begriff ist zugleich eine Philosophie, als auch eine praktische Handlungsanweisung, nach der jeder Mitarbeiter nach Möglichkeiten sucht, seinen Arbeitsplatz, die Qualität von Arbeitsabläufen und -prozessen und Produkten zu verbessern. Ähnlich wie auch OpEx ist Kaizen kein Werkzeug, sondern eine Einstellung. Die Kernideen der Einstellung umfassen: gute Prozesse und Teamwork führen zum Erfolg, jeder Prozess kann optimiert werden, allerdings nicht in sprunghaften Innovationen, sondern durch schrittweise Perfektionierung.
Lean Management
= Vermeidung von Verschwendung, Prozess-Effizienz.
Lean Management kann auch in „schlankes Management“ übersetzt werden. Prozesse sollen möglichst schlank gehalten werden, Verschwendung minimiert und Kosten dadurch gesenkt werden. Die bekannteste Umsetzung des Prinzips stammt, wie auch Kaizen, aus Japan: Das Toyota-Produktions-System (TPS) gilt heute als das effizienteste Produktionssystem der Welt. Die Verschwendung stets im Blick behaltend, baut es auf 5 Grundsätzen auf: Prozess-Synchronisation, Prozess-Standardisierung, Vermeidung von Fehlern, Verbesserung der Produktionsanlagen, Einbeziehung der Mitarbeiter.
Six Sigma
= Messbarbarkeit der Optimierung, Prozess-Effektivität.
Während es sich bei Lean Management und Kaizen noch um recht abstrakte Management-Ansätze handelt, arbeitet Six Sigma mit strukturierten, statistischen Wertanalysen. Im Gegensatz zum Lean Management, das sich auf die Vermeidung von Verschwendung fokussiert, stehen bei Six Sigma stabile Prozesse im Vordergrund. Erreicht werden soll das durch eine strukturierte, wissenschaftlich fundierte und in der Praxis erprobte Vorgehensweise. Mit statistischen Mitteln werden dabei Geschäftsvorgänge beschrieben, gemessen, analysiert, verbessert und kontinuierlich überwacht.
Die Ansätze ähneln sich stark und werden auch in der Praxis oftmals nicht trennscharf gelebt. Was bedeutet „Prozesse optimieren“ praktisch übersetzt? Abstrakte Begriffswelten wie Lean Management oder Kaizen lassen sich in klare, eindeutige Maßnahmen und Arbeitsgänge runterbrechen. Greifbarer wird es erst dann, wenn man eine Ebene weiter runter geht und sich Einzelinstrumente wie 5S Checklisten, TPM oder Gemba-Walks anschaut. In diesen Maßnahmen werden konkrete Handlungsschritte zur Prozessoptimierung festgelegt und oftmals in Form einfacher Checklisten aufbereitet.
Vom Anbieter- zum Nachfragemarkt - Warum Operational Excellence so wichtig ist
Warum bedarf es eines neuen Management-Ansatzes, wenn Unternehmen immer zum Ziel haben, Umsatz zu erwirtschaften und das nur mit guten Produkten und Dienstleistungen gelingt? Wie eingangs erwähnt, entscheiden Kunden heute über Erfolg und Misserfolg von Unternehmen. Der Markt hat sich von einem Anbieter- zu einem Nachfragemarkt entwickelt. Einer der wichtigsten Treiber dieser Entwicklung ist die Globalisierung. Unternehmen sehen sich mit einer viel größeren Anzahl an Wettbewerbern konfrontiert. Insbesondere die vergleichsweise hohen Lohnkosten in Deutschland zwangen Unternehmen in den vergangenen Jahrzehnten immer mehr dazu, Kunden über andere Differenzierungsmerkmale als den Preis zu erreichen. Produktqualität, Service und Innovation rücken anstelle des Preiskampfs. OpEx hilft Unternehmen dabei, verborgene Potentiale heben.
5 Vorteile von Operational Excellence-Programmen
Mit OPEX externen Schocks begegnen & Resilienz steigern Globalisierung, Währungskrisen, Force Majore Ereignisse wie die aktuelle Covid-19 Pandemie, international schwelende Konflikte, Rohstoffmängel. In einer vernetzten Welt müssen Unternehmen flexibel und handlungsfähig bleiben. Ein nachhaltiges OpEx Programm hilft dabei, schnell zu reagieren, wenn z.B. Produktionsstillstand oder Ressourcenverknappung droht.
Prozess-Effizienz & Effektivität erlangen Lange Wege- und Rüstzeiten, Materialverschwendung oder ineffiziente Schichtübergabe-Prozesse können mit den OpEx-Programmen aufgedeckt und beseitigt werden. Jeder Prozess wird dabei genau unter die Lupe genommen und auf Unwirtschaftlichkeit untersucht. Erfolgt die Optimierung systematisch, können Effizienzpotentiale gehoben und die Produktivität gesteigert werden.
Mitarbeiter stärken und motivieren Alle Instrumente aus dem OpEx Methodenkoffer haben eins gemeinsam: sie stellen den Menschen in den Vordergrund. Expertenmeinungen erfahrener Mitarbeiter werden geschätzt, durch schlanke und präzise Prozessanweisungen wird die Arbeit erleichtert. So können alle Mitarbeiter aktiv auf die Unternehmensziele hinarbeiten und gemeinsam „an einem Strang“ ziehen. Das steigert die Identifikation mit dem Unternehmen und allgemeine Mitarbeiterzufriedenheit. Ein weiterer Vorteil liegt in der Anlernung neuer Mitarbeiter. Wenn schlanke Anlern-Prozesse installiert sind, können Herausforderungen wie der Fachkräftemangel einfacher überwunden werden.
Einhaltung gleichbleibend hoher Qualitätsstandards Schlanke, effiziente Prozesse wirken sich automatisch positiv auf die Produktqualität aus. Wenn OpEx als unternehmensweites Management-Tool eingesetzt und gelebt wird, können Unternehmen standortunabhängig hohe Arbeits- und Produktqualität sicherstellen. Kunden können sich auf gleichbleibende Qualitätsstandards verlassen.
Kosten reduzieren durch Eindämmung von Verschwendung Unternehmen können Einsparpotentiale nicht nur durch günstigeren Einkauf und flexible Pricing-Strategien realisieren, sondern auch Einsparungen bei der Leistungserstellung erzielen. Prozesse werden auf Unwirtschaftlichkeit durchleuchtet. Behäbige, ineffiziente und verschwenderische Prozesse werden mittels verschiedener Instrumente aus dem OpEx Methodenkoffer identifiziert und verbessert.
Es gibt also viele kleine Stellschrauben, an denen Unternehmen zusätzlich drehen und so ihre Produkte noch besser machen können. Neben den offensichtlichen Einsparungen für das Unternehmen profitieren am Ende auch die Kunden.
Produktion: Die Wiege der Operational Excellence
Die meisten Initiativen zur operativen Exzellenz wie Six Sigma (Motorola) oder Lean Manufacturing (Toyota) stammen aus produzierenden Unternehmen. Die Prinzipien können zwar auch im Dienstleistungssektor angewandt werden, aber richtig entfalten können sie sich am besten in der Fertigungsindustrie, in der viele operative Tätigkeiten und Arbeitsschritte zur Werterstellung benötigt werden.
Die Rolle von operativen Prozessen für Operational Excellence
Operativen Prozessen und Ihrer ordnungsgemäßen Durchführung kommt im Rahmen der Operational Excellence eine besondere Bedeutung zu. In ihrer täglichen Durchführung liegt die Wahrheit zur Wirksamkeit der OpEx-Bestrebungen. Im Produktionsbetrieb entscheiden (neben vielen anderen) Prüf-, Wartungs-, Montage- und Auditprozesse darüber, wie effizient und effektiv ein Unternehmen seine Leistungen erstellt. Obwohl die Fertigungsindustrie die Wiege von OpEx ist, schaffen es heute viele produzierende Unternehmen nicht, das Effizienz-Maximum aus ihren Prozessen rauszuholen. Das liegt oftmals an der Ausgestaltung operativer Prozesse:
5 Merkmale von operativen Prozessen, die im Konflikt mit Operational Excellence stehen
Häufig sind operative Prozesse nicht derart gestaltet, dass Sie direkt auf die Unternehmensstrategie einzahlen können. Stattdessen können sie sogar in direktem Konflikt zu OpEx stehen:
Operative Prozesse spiegeln nicht das Wissen der Mitarbeiter wider Ist die Prozessbeschreibung vom Wissen der operativen Mitarbeiter entkoppelt, besteht die Gefahr von Schattenprozessen, geringer Standardisierung, Qualitätsschwankungen und nachhaltigem Wissensverlust.
Ist-Prozesse weisen systematische Abweichungen von dokumentierten Soll-Prozessen auf Die Entkopplung des Wissens stellt ein unmittelbares Qualitätsrisiko dar. Zurückzuführen ist eine solche Abweichung häufig auf missverständliche oder veraltete Prozessanweisungen.
Prozessdaten werden nicht erhoben und analysiert Unternehmen messen häufig nur Resultate, selten den Prozess, der den Resultaten zugrunde liegt. Das „Wir haben das schon immer so gemacht“-Prinzip greift. Das Erfassen von Prozessdaten erscheint daher wie ein nicht wertschöpfender Aufwandstreiber. Das führt dazu, dass Ineffizienzen innerhalb des Prozesses nicht erkannt werden.
Prozesse sind über verschiedene Systeme fragmentiert ERP, MES, CRM. Über die Zeit wächst in Unternehmen eine vielfältige IT-Systemlandschaft, welche Geschäftsinformationen in Silos fragmentiert. Lean Methoden lassen sich nur schwerlich anwenden, da wenig Transparenz über Prozesse herrscht. Manuelle Datentransfers erzeugen Zusatzaufwand, der im Widerspruch zum schlanken Arbeiten steht.
Prozesse werden nicht weiterentwickelt und verbleiben statisch Die verwendeten Systeme verhindern eine flexible Weiterentwicklung von Prozessen, was zu erhöhtem Aufwand und Qualitätsrisiken führen kann. Häufig fehlt auch das Mindset, sich stetig zu hinterfragen, Feedback einzuholen, und Prozesse auszuwerten.
Wie Sie Operational Excellence in Ihrem Unternehmen erlangen
Wie können Sie den Widerspruch zwischen dem Streben nach OpEx und fehleranfälligen operativen Prozessen überwinden?
"Operational Excellence is a mindset, not a methodology."
Bryan Brulotte
Bevor Sie sich in einzelnen Unternehmens- oder Fertigungsbereichen auf dem OpEx-Methodenkoffer bedienen, würden wir gerne an die Definition am Anfang dieses Blogbeitrags erinnern. Bei OpEx handelt es sich nicht um eine ultimative Schritt-für-Schritt-Anleitung zum garantierten Erfolg. Stattdessen muss das Streben nach OpEx ein Teil der Unternehmenskultur werden. Firmen, die ein OpEx-Programm einführen möchten, sollten sich zunächst fragen, warum. Ziel des Programms sollte immer eine Ausrichtung aller Prozesse an die Unternehmensstrategie sein. Und diese Strategie sollte die Kundenzufriedenheit in den Mittelpunkt stellen.
Wo beginnen? 4 Schritte zu einem erfolgreichen Operational Excellence Programm
Je größer Ihr Unternehmen ist, desto anspruchsvoller ist es, ein OpEx-Programm gleichzeitig an alle Abteilungen auszurollen und zu kommunizieren. Starten Sie daher phasenweise mit einem Pilotprojekt:
Planung & Zielsetzung: Definieren Sie zunächst ihr Ziel. Möchten Sie die Kundenzufriedenheit steigern, die Produktqualität verbessern oder die Prozess-Effizienz erhöhen? Stellen Sie ein interdisziplinäres Team aus verschiedenen Fachabteilungen zusammen, organisieren Sie Schulungen und Trainings für das Team.
Vorbereitung: Bauen Sie Programm-Strukturen und gegebenenfalls einen Projektplan mit zu erzielenden Meilensteinen auf. Analysieren Sie den gegenwärtigen Status Quo gegenüber der gewünschten Zielerreichung. Wählen Sie die für Sie passenden Instrumente aus dem OpEx-Methodenkoffer.
Pilotierung: Bevor Sie einen unternehmensweiten Change-Prozess einläuten, setzen Sie zunächst Pilotprojekte um. Besonders wichtig in dieser Phase: kommunizieren und nochmals kommunizieren! Ein OpEx Programm kann nur erfolgreich mit einer offenen Kommunikation gelingen.
Unternehmensweiter Roll-Out: Evaluieren Sie das bisherige Pilotprojekt. Wenn es erfolgreich verlaufen ist, können Sie das Programm unternehmensweit nach und nach ausrollen. Wenn Sie noch Optimierungsbedarf sehen (z.B. bei der Auswahl der Instrumente), können Sie inkrementell nachjustieren.
Operational Excellence in Zeiten der Digitalisierung
Die Digitalisierung bietet produzierenden Unternehmen seit Jahren die Möglichkeit mit Redundanzen, Ineffizienzen und Verschwendungen aufzuräumen. Die bereits genannten Merkmale operativer Prozesse, die Hürden für OpEx-Bemühungen darstellen, können mittels verschiedener Tools ausgeräumt werden. Die Methoden aus dem OpEx-Koffer können einfacher mit Software durchgeführt werden, während ihr Erfolg zugleich messbar wird.
Wie Digitalisierung Sie bei Erreichung der operativen Exzellenz unterstützen kann
Eine Software kann einen großen Beitrag zu Operational Excellence leisten, indem sie Prozesse standardisiert, Produktivität steigert und die Qualität gegenüber Ihren Kunden verbessert.
Nicht wertschöpfende Prozesse eliminieren: Arbeits- und Prozessanweisungen können schnell erstellt und bei Änderungen einfach angepasst werden. Damit entfallen im Sinne des Lean Managements nicht wertschöpfende, verschwenderische Erstellprozesse. Eine Software kann mittels End-to-End-Integration Datensilos überwinden und bis zu 100% des manuellen Datenaufwands einsparen.
Mitarbeiter vernetzen und unterstützen: OpEx stellt nicht nur Prozesse, sondern vor allem Menschen in den Mittelpunkt. Digitale Tools können bei der Einführung eines OpEx-Programms unterstützen: Mit Hilfe einer intuitiven Software werden Mitarbeiter zuverlässig durch Prozesse geführt. Langjährige Mitarbeiter können Ihr Prozesswissen einfach in die Erstellung neuer Prozessanweisungen einfließen lassen. Die Mitarbeiterzufriedenheit steigt und zeitgleich die Akzeptanz für neue, digitale Tools. Das führt zu 21% mehr Produktivität.
Fehlerquote senken: Jegliches Prozesswissen wird an einem Punkt der Wahrheit gespeichert. Digitale Tools bieten Live-Monitoring, Dashboards und Task Management. Fehler werden dadurch früh erkannt und können umgehend behoben werden, wodurch die Qualität um 55% steigt. Prozessdaten werden gespeichert und können zur kontinuierlichen Verbesserung genutzt werden.
Damit bieten digitale Tools Unternehmen nicht nur ein zusätzliches Instrument, Prozesse schlanker zu gestalten. Sie eröffnen die Möglichkeit, fundierte Entscheidungen datenbasiert und in Echtzeit zu treffen. Die erhöhte Reaktionsfähigkeit hilft Unternehmen dabei, in einer volatilen, unsicheren Welt, adaptiv auf externe Einflüsse und Kundenbedürfnisse zu reagieren.
Operational Excellence mit Operations1
Mit Operations1 steigern Sie Ihre Qualität, Produktivität und optimieren Ihre Prozesse kontinuierlich.
Fazit
Unternehmen müssen heute alle Optimierungshebel in Bewegung setzen, um wettbewerbsfähig zu bleiben, Kundenbedürfnisse zu erfüllen und vor allem um flexibel auf externe Schocks reagieren zu können. Dazu müssen alle Prozesse und alle Glieder der Wertschöpfungskette optimiert und in Einklang mit der Unternehmensstrategie gebracht werden. Wenn das gelingt, erreichen Unternehmen den erstrebenswerten Zustand der „Operational Excellence“. Insbesondere Fertigungsunternehmen können mit verschiedenen Methoden wie Lean Management oder Kaizen erhebliche Optimierungspotentiale heben. Am einfachsten gelingt der Einsatz dieser Methoden mithilfe von Digitalisierung.
Auf das Wesentliche konzentrieren: Ihre Unternehmensstrategie
Sie möchten ein Operational Excellence-Programm starten und Sie suchen nach einer Software-Lösung, die Sie bei der Einführung und Einhaltung schlanker, agiler Prozesse unterstützt? Mit Operations1 können Sie nicht wertschöpfende Tätigkeiten eliminieren und Effizienzen heben. Stellen Sie digitale Arbeitsanweisungen und Checklisten bereit und unterstützen Sie Ihre Mitarbeiter bei der Durchführung operativer Prozesse wie Montage-, Qualitätsprüfungs- und Instandhaltungstätigkeiten. Reagieren Sie flexibel auf unvorhergesehene Ereignisse und lösen Sie diese kollaborativ im Team.
Nehmen Sie jetzt Kontakt auf.
Daniel Grobe
Daniel Grobe (M. Sc., Management & Technology) gründet 2017 gemeinsam mit Benjamin Brockmann (ebenfalls M. Sc., Management & Technology) die cioplenu GmbH. Die Software-Lösung entwickeln die Gründer auf Basis diverser Praxisprojekte, u. a. am Fraunhofer Institut, und aufgrund ihrer Erfahrungen in der Industrie, Wirtschaftsprüfung und Unternehmensberatung. Daniel Grobe ist Junior Board Member der bayme vbm und war bereits für Unternehmen wie KPMG und Continental tätig.