What it's about
In this blog post, we will give you a comprehensive overview of the complex topic of Operational Excellence. What does the approach mean and why is it so important? We'll show you which concepts and methods are involved and why manufacturing companies are struggling to achieve Operational Excellence - even though the approach has actually grown out of manufacturing. Finally, we would like to give you tips on how to achieve operational excellence - and how digitization can help you with it.
What is Operational Excellence?
Operational Excellence (OpEx) means the holistic alignment of the company to the overall strategy. All processes and systems along the entire value chain are continuously optimized with regard to customer needs, quality and efficiency. Operational excellence can increase productivity, reduce costs and thus contribute to the long-term success of the company. At the same time, in addition to optimizing value-adding core processes, OpEx also has a cultural and an organizational dimension: continuous and sustainable optimization only works with the help of all employees. Therefore, OpEx is also always part of the corporate culture. The question of what exactly OpEx is can therefore be answered with: OpEx is a strategic management approach.
What are some examples of operational excellence?
To understand even better what OpEx is all about, it helps to understand what it is not. If line stoppages are imminent because components are not delivered on time, if a construction project cannot be continued because certain building materials do not meet the required quality standards, or if Customer Service does not conduct careful, results-oriented claim management in the event of a complaint, OpEx does not exist. The above examples show "faults in the system" - across the entire value chain: in logistics, product quality and service. Whether a company is operationally "excellent" is ultimately decided by the customer.
Operational Excellence vs. CIP
In the further course, we will present some methods for achieving operational excellence, but in this section we would first like to highlight the difference between OpEx and the continuous improvement process (CIP). While both approaches are similar at first glance - CIP also pursues measures to increase efficiency by increasing productivity and uncovering potential savings - OpEx goes further. CIP looks at the cyclical optimization of small-scale processes (Plan - Do - Check - Act) and is often integrated into quality management in companies. A dedicated group of employees takes care of the implementation of CIP measures. OpEx, on the other hand, is a holistic, strategic approach that should be lived and implemented by all company employees, not just by one department. The Institute for Operational Excellence puts it this way: "Each and every employee can see the flow of value to the customer, and fix that flow before it breaks down." CIP can be used as a single method to achieve operational excellence.
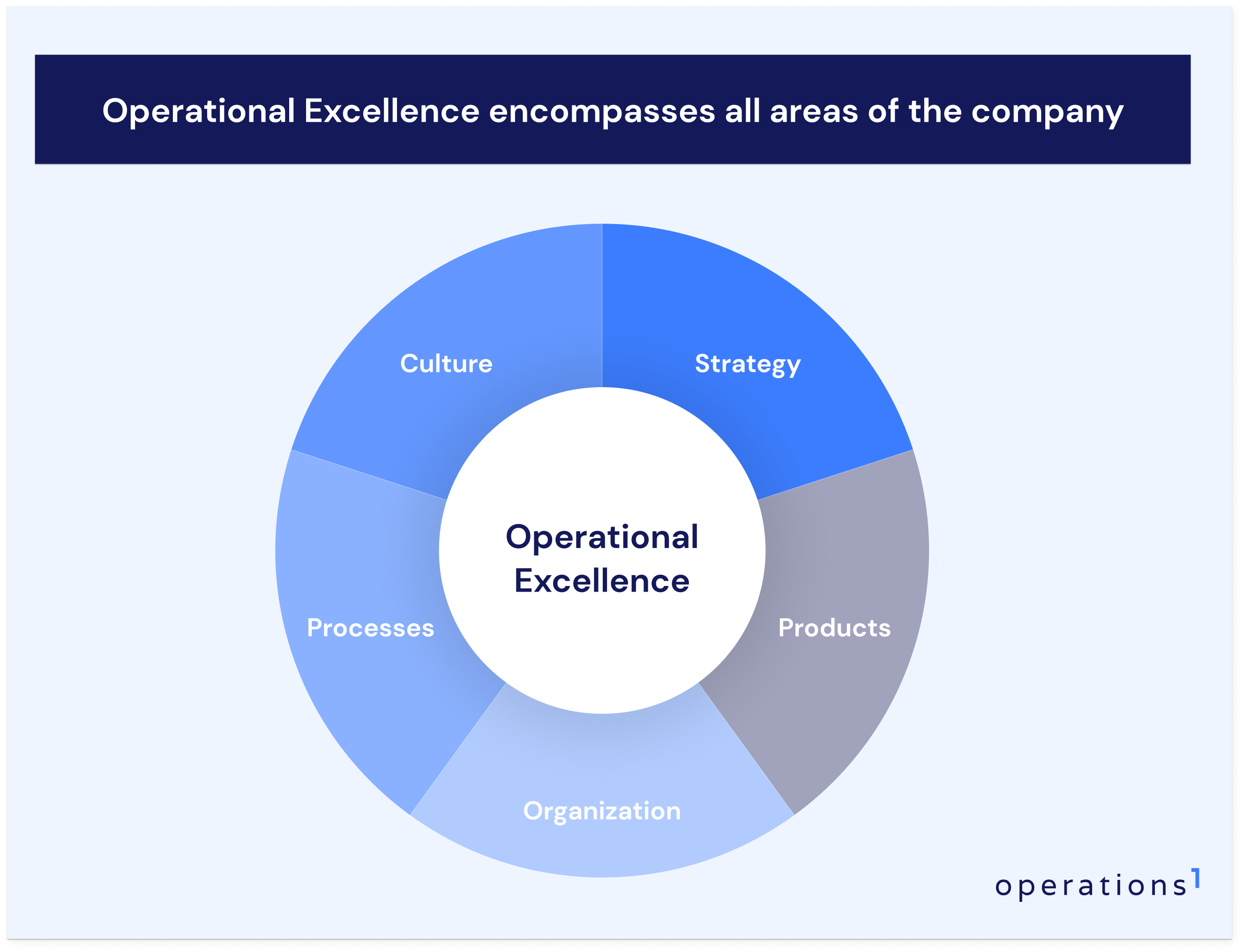
The toolbox of methods for achieving Operational Excellence is inexhaustible
In addition to CIP, there are many other methods and tools that can contribute to achieving Operational Excellence. Other typical buzzwords are, for example, Lean Management, Six Sigma, Kaizen, Target Costing, Supply Chain Management, Gemba Walks, MUDA or the seven types of waste, Total Productive Maintenance and many more. Thus, there exists an enormously large toolbox of methods to draw from when implementing Operational Excellence programs. The most important ones at a glance:
Kaizen
= step-by-step optimization, process knowledge.
Kaizen (Kai = change, transformation; Zen = for the better) comes from the Japanese and is often equated with CIP. The term is both a philosophy and a practical guideline for action, according to which every employee looks for ways to improve their workplace, the quality of workflows and processes, and products. Similar to OpEx, Kaizen is not a tool, but an attitude. The core ideas of the attitude include: good processes and teamwork lead to success, every process can be optimized, but not in leaps and bounds innovations, but through gradual perfection.
Lean Management
= avoidance of waste, process efficiency.
Lean Management can also be translated into "slim processes". Processes should be kept as lean as possible and waste should be minimized. This reduces costs as a result. The best-known implementation of the principle comes, like Kaizen, from Japan: the Toyota Production System (TPS) is today considered the most efficient production system in the world. Always keeping waste in mind, it is built on 5 principles: Process Synchronization, Process Standardization, Error Prevention, Production Equipment Improvement, Employee Involvement.
Six Sigma
= measurability of optimization, process effectiveness.
While Lean Management and Kaizen are still quite abstract, Six Sigma works with structured, statistical value analyses. In contrast to Lean Management, which focuses on avoiding waste, Six Sigma focuses on stable processes. This is to be achieved through a structured, scientifically based approach that has been tested in practice. Statistical means are used to describe, measure, analyze, improve and continuously monitor business processes.
The approaches are very similar and are often not clearly defined in practice. What does "optimize processes" mean in practical terms? Abstract concepts such as Lean Management or Kaizen can be broken down into clear, unambiguous measures and work processes. It only becomes more tangible when you go down one level further and look at individual instruments such as 5S checklists, TPM, or Gemba Walks. In these measures, concrete action steps for process optimization are defined and often prepared in the form of simple checklists.
From supplier to demand market - why Operational Excellence is so important
Why is there a need for a new management approach when companies always aim to generate sales and can only do so with good products and services? As mentioned in the beginning, customers today determine the success or failure of companies. The market has evolved from a supplier market to a demand market. One of the most important drivers of this development is globalization. Companies are faced with a much larger number of competitors. In particular, the comparatively high wage costs in Europe have increasingly forced companies to reach customers through differentiating features other than price. Product quality, service and innovation are taking the place of price wars. OpEx helps companies to leverage hidden potential.
5 Benefits of Operational Excellence Programs
Countering external shocks & increasing resilience with OpEx Globalization, currency crises, force majore events such as the current Covid-19 pandemic, international conflicts, raw material shortages. In an connected world, companies must remain flexible and able to act. A sustainable OpEx program helps to react quickly when, for example, production shutdowns or resource shortages threaten.
Achieve process efficiency & effectiveness Long travel and setup times, material waste or inefficient shift handover processes can be uncovered and eliminated with the OpEx programs. Each process is closely scrutinized and examined for inefficiency. If optimization is carried out systematically, efficiency potentials can be raised and productivity increased.
Strengthen and motivate employees All tools from the OpEx method case have one thing in common: they put people in the foreground. Expert opinions from experienced employees are valued, and lean and precise process instructions make work easier. This enables all employees to work actively toward the company's goals and to pull together. This increases identification with the company and general employee satisfaction. Another advantage lies in the training of new employees. If lean learning processes are installed, challenges such as the shortage of skilled workers can be overcome more easily.
Maintaining consistently high quality standards Lean, efficient processes automatically have a positive impact on product quality. If OpEx is used and practiced as a company-wide management tool, companies can ensure high work and product quality regardless of location. Customers can rely on consistent quality standards.
Reducing costs by cutting waste Companies can realize savings potential not only through more favorable purchasing and flexible pricing strategies, but also by achieving savings in the production of services. Processes are screened for inefficiency. Slow, inefficient and wasteful processes are identified and improved using various tools from the OpEx method box.
So there are many small adjusting screws that companies can additionally turn to make their products even better. In addition to the obvious savings for the company, customers also benefit in the end.
Production: The Cradle of Operational Excellence
Most Operational Excellence initiatives such as Six Sigma (Motorola) or Lean Manufacturing (Toyota) originated in manufacturing companies. Although the principles can also be applied in the service sector, they can really unfold best in the manufacturing industry, where many operational activities and work steps are required to create value.
The role of operational processes for Operational Excellence
Operational processes and their proper execution are of particular importance in the context of Operational Excellence. In their daily execution lies the truth to the effectiveness of OpEx efforts. In manufacturing operations, inspection, maintenance, assembly and audit processes (among many others) determine how efficiently and effectively a company produces its outputs. Although the manufacturing industry is the cradle of OpEx, many manufacturing companies today fail to get the maximum efficiency out of their processes. This is often due to the design of operational processes:
Characteristics of operational processes that conflict with Operational Excellence
Frequently, operational processes are not designed in such a way that they can directly contribute to the corporate strategy. Instead, they may even be in direct conflict with OpEx:
Operational processes do not reflect the knowledge of the employees If the process description is decoupled from the knowledge of the operational employees, there is a risk of shadow processes, low standardization, quality fluctuations and sustained loss of knowledge.
Actual processes show systematic deviations from documented target processes The decoupling of knowledge represents a direct quality risk. Such deviations are often due to misleading or outdated process instructions.
Process data is not collected and analyzed Companies often only measure results, rarely the process that underlies the results. The "we've always done it this way" principle takes hold. The collection of process data therefore seems like a non-value-adding effort driver. This leads to inefficiencies within the process not being recognized.
Processes are fragmented across different systems ERP, MES, CRM. Over time, companies grow a diverse IT system landscape that fragments business information into silos. Lean methods are difficult to apply because there is little transparency about processes. Manual data transfers generate additional effort that contradicts lean working.
Processes are not developed further and remain static The systems used prevent flexible further development of processes, which can lead to increased effort and quality risks. Often, the mindset of constantly questioning oneself, obtaining feedback, and evaluating processes is also lacking.
How to achieve operational excellence in your company
How can you overcome the contradiction between the pursuit of OpEx and error-prone operational processes?
"Operational excellence is a mindset, not a methodology."
Bryan Brulotte
Before you pick on the OpEx methodology toolbox in individual business or manufacturing areas, we'd like to remind you of the definition at the beginning of this blog post. OpEx is not an ultimate step-by-step guide to guaranteed success. Instead, the pursuit of OpEx must become a part of the company culture. Companies looking to implement an OpEx program should first ask themselves why. The goal of the program should always be to align all processes with the company's strategy. And that strategy should focus on customer satisfaction.
Where to start? 4 steps to a successful Operational Excellence program
The larger your company, the more challenging it is to roll out and communicate an OpEx program to all departments simultaneously. Therefore, start in phases with a pilot project:
Planning & goal setting: First define your goal. Do you want to increase customer satisfaction, improve product quality or increase process efficiency? Assemble an interdisciplinary team from different departments, organize training and education for the team.
Preparation: Build program structures and, if necessary, a project plan with milestones to be achieved. Analyze the current status quo versus the desired goal achievement. Select the appropriate tools for you from the OpEx methodology toolbox.
Piloting: Before you initiate a company-wide change process, first implement pilot projects. Especially important in this phase: communicate and communicate again! An OpEx program can only succeed with open communication.
Company-wide roll-out: Evaluate the pilot project to date. If it has been successful, you can gradually roll out the program company-wide. If you still see a need for optimization (e.g., in the selection of instruments), you can make incremental adjustments.
Operational Excellence in times of digitalization
For years, digitization has offered manufacturing companies the opportunity to eliminate redundancies, inefficiencies and waste. The aforementioned features of operational processes that represent hurdles for OpEx efforts can be eliminated by means of various tools. The methods from the OpEx case can be more easily carried out with software, while at the same time their success becomes measurable.
How digitization can help you achieve Operational Excellence
Software can make a big contribution to operational excellence by standardizing processes, increasing productivity and improving quality towards your customers.
Eliminate processes that do not add value: Work and process instructions can be created quickly and easily adapted when changes are made. This eliminates non-value-added, wasteful creation processes in the spirit of lean management. Software can use end-to-end integration to overcome data silos and save up to 100% of manual data effort.
Connect and support employees: OpEx focuses not only on processes, but more importantly on people. Digital tools can assist in the implementation of an OpEx program: Intuitive software reliably guides employees through processes. Long-standing employees can easily incorporate their process knowledge into the creation of new process instructions. Employee satisfaction increases and, at the same time, acceptance of new, digital tools increases. This leads to 21% more productivity.
Reduce error rates: All process knowledge is stored at a point of truth. Digital tools offer live monitoring, dashboards and task management. Errors are thus detected early and can be corrected immediately, increasing quality by 55%. Process data is stored and can be used for continuous improvement.
Digital tools not only offer companies an additional instrument for streamlining processes. They open up the possibility of making informed decisions based on data and in real time. The increased responsiveness helps companies to react adaptively to external influences and customer needs in a volatile, uncertain world.
Conclusion
Today, companies have to set all optimization levers in motion in order to remain competitive, to meet customer needs and, above all, to be able to react flexibly to external shocks. To do this, all processes and all links in the value chain must be optimized and brought into line with the corporate strategy. If this can be achieved, companies will reach the desirable state of "operational excellence". Manufacturing companies in particular can leverage considerable optimization potential using various methods such as Lean Management or Kaizen. The easiest way to apply these methods is with the help of digitization.
Operational excellence with Operations1
With Operations1 you increase your quality, productivity and optimize your processes continuously.
Focus on the essential: Your corporate strategy
You want to start an Operational Excellence program and you are looking for a software solution to help you implement and comply with lean, agile processes? With Operations1, you can eliminate non-value-added activities and leverage efficiencies. Provide digital work instructions and checklists and help your employees perform operational processes such as assembly, quality inspection and maintenance activities. Respond flexibly to unforeseen events and solve them collaboratively as a team.
Get in touch with us.
Daniel Grobe
Daniel Grobe (M. Sc., Management & Technology) founds cioplenu GmbH in 2017 together with Benjamin Brockmann (also M. Sc., Management & Technology). The founders develop the software solution on the basis of various practical projects, including at the Fraunhofer Institute, and their experience in industry, auditing and management consulting. Daniel Grobe is a Junior Board Member of bayme vbm and has already worked for companies such as KPMG and Continental.