What it's about
In this blog post, you'll learn about common types of waste and how using software can best conserve your resources.
What are the 7+1 Types of Waste / Muda?
Muda (Japanese for "waste"), comes from the Operational Excellence and Lean Management terminology, and describes activities that consume resources and incur costs, but do not add value. These types of waste were first described by Taiichi Ohno, the developer of the Toyota Production System. In sustainable, efficient production, all non-value-added, wasteful activities must be eliminated or reduced as much as possible. Ohno describes 7 types/areas of waste:
#1 Transport
Long, unnecessary transport routes within a production hall can generate expenses. Inefficient material flows can also occur during storage, retrieval and transfer.
#2 Inventory
Excessive material and inventory levels tie up space and thus capital. This can mean manufacturing products as well as raw materials and supplies.
#3 Motion
Long walking distances, search times, and inefficiently set up work stations where employees have to awkwardly reach around or walk around machines fall under waste due to motion.
#4 Waiting
Waiting times mean downtime in production. Machine downtime, long setup times, and the previously mentioned types of waste can lead to long, non-value-added waiting periods.
#5 Overproduction
Overproduction occurs mainly due to poor planning. However, quality deficiencies can also lead to surplus. In this case, more is produced "as a precaution".
#6 Overprocessing
In this case, one also speaks of "over engineering". Processes are artificially inflated or too complex and thus lead to unnecessary resource commitment.
#7 Defects
Production errors lead to scrap production. This type of waste is the most obvious and, of course, to be avoided. But often it is not immediately obvious at first glance where the fault lies.
The seven types of waste result in the acronym TIMWOOD (Transport, Inventory, Motion, Waiting, Overproduction, Overprocessing, Defects), which can still be found in older guidebooks.
For some years now, Ohno's concept has been supplemented by another, often underestimated type of waste:
#8 Unused employee potential
Employee knowledge and qualifications are misused. Employees who are not deployed according to their qualifications and whose valuable experience is not drawn upon are wasted potential. Fortunately, lean methods, which help in the pursuit of operational excellence, have also recognized this in recent years. Here, it's not just about using the "human resource" as profitably as possible. It is about appreciation and the joint achievement of corporate goals.
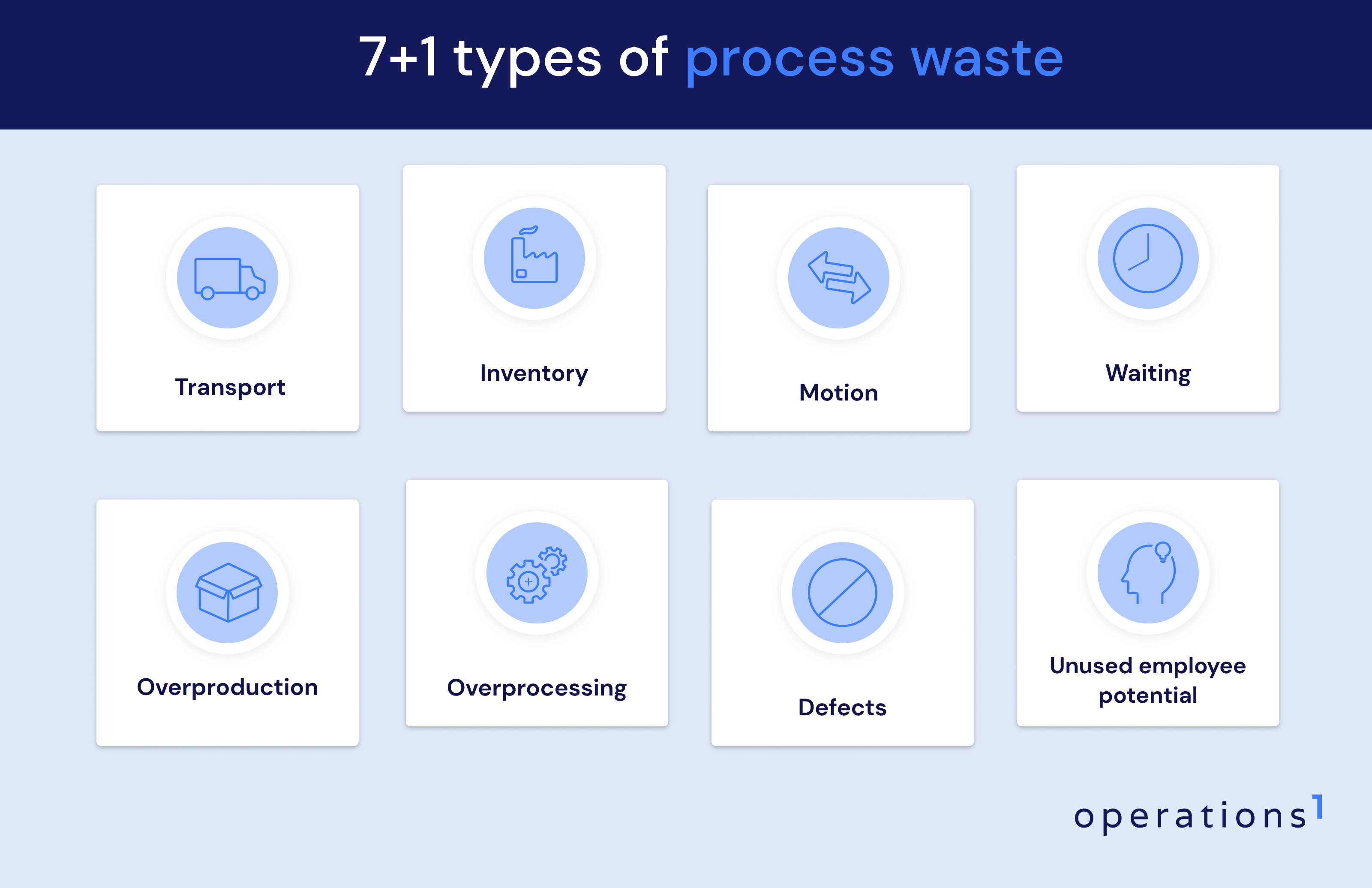
Paper-based work: Fire accelerator for inefficient processes
No company causes several or even all eight types of waste. Companies would not survive this in the long term. However, in the course of operational excellence programs, small levers can be identified in every area of the value chain that can be optimized and streamlined. In the manufacturing industry, it is often paper-based work that makes processes cumbersome and thus causes waste. Inspection processes, assembly and maintenance work, incoming goods inspections or shift handovers: many of these processes and operations take place with the help of paper-based work instructions and checklists. The result: errors, quality problems and avoidable effort. Digital tools can reduce these efforts and thus counteract wasteful activities.
Software for work instructions and checklists: Digital fire extinguishers against waste
Especially in medium-sized companies, software can make a major contribution to reducing complex, costly processes. Track & trace solutions counter inefficient transport routes and material movements, while ERP and MES systems control production planning. Employee-managed processes, however, often remain analog, not least because operational employees are "deskless." Information reaches them only with a time delay or is outdated. Fortunately, the waste that occurs in this way can also be easily prevented with digital tools.
Adaptive Process Ecexution (APE) Software starts with the operational employees on the shop floor and supports them in the daily execution of their activities. With end-to-end integrated software solutions, employees are guided intuitively through work processes. Paper lists give way to mobile devices such as tablets or smartphones. The advantages:
Reduce errors & defects: Media-based work instructions and checklists increase process understanding regardless of language and qualification. Work is performed more quickly and reliably.
Minimize travel times: Travel and waiting times are eliminated because live collaboration and direct task assignment are possible. When problems occur, employees do not have to search for their foremen and explain the problem first, as the integration of error images is possible.
Take complexity out of the equation: For complex, variant-rich products, the right software can save up to 100% of the original work instruction creation effort. With drag & drop functionality, for example, variant-specific information can be pulled directly from the ERP. Overproduction and over-engineering are thus prevented, as employees receive the right information, relevant to them, at the right place and at the right time, based on context. This also has a positive effect on setup times in complex production processes. Plant changeovers are faster with digital instructions.
Optimize inventories: Inspection checklists for goods receipt or goods issue inspections can also be provided digitally. This minimizes waste in inventory and material flows.
Increase transparency: Integrated software maps the "last mile" to the worker. APE software enables transparency and simple, intelligent evaluation of operational work processes. Full integration into the company's own system landscape helps to resolve problems in real time and prevent time wastage.
Conclusion
Companies that want to become leaner and more efficient need to eliminate wasteful processes. Ohno's 7 + 1 types of waste help identify potentially affected areas. In all eight areas, paper-based work in operational areas often contributes to waste. Digital work instructions and checklists can counteract this. With a software solution, all non-value-adding processes on the shopfloor can be contained.
Would you like to learn how you can counter waste with software?
Operations1 can counteract non-value-added processes and waste in the production environment. The simple, intuitive end-to-end software helps your employees perform their daily tasks. Without wasting productivity and paper. Read how digital work instructions can make your production leaner and more efficient:
Editha Bertsch
Editha is an experienced project management expert for manufacturing companies. With a clear understanding of the specific challenges of the industry, she is passionate about developing innovative solutions.