What it is about
In this blog post, I describe my findings and impressions from the Factory of the Year (FoY) 2022 event.
Factory of the Year (FdJ) 2022 in Ludwigsburg
The Factory of the Year event is one of the most renowned industry competitions in Europe. At the final congress in Ludwigsburg in May 2022, the winners of the 2021 competition presented their successful strategies and were honoured at the festival's awards ceremony. The winners: ABB, Brose Group, Kurtz Ersa, Beiersdorf and Siemens. But why were these factories awarded and what moves the managers of these companies?
How do you win the Factory of the Year?
The title of Factory of the Year is up for grabs. The event is organised by the management consultancy Kearney and SV Veranstaltungen. All applicant companies will receive a detailed, confidential assessment that will give them an indication of their position in comparison to companies with a similar starting position. Shortlisted candidates are visited on-site by an experienced audit team from Kearney, followed by initial expert feedback. Finally, the Factory of the Year competition jury selects the winner. Steps in specific categories are awarded to entrants who demonstrate outstanding performance or exceptional creativity in each category of the assessment model.
Focus on the topics of sustainability, value orientation and digitalisation
Speakers at the event included the winners of the various categories as well as other leading voices from research and trade media. Not surprisingly, supply chain issues, digitalisation and automation were a focus topic. What was surprising to me, however, was how strong the call for more sustainability was. Dr. Marc Lakner presented the sustainability study by the consultancy Kearney with the urgent call to act decisively now. There would be emotional talks about defossilisation of factory systems (Robert Bosch GmbH, Fraunhofer) and Co2-neutral production as well as circular economy (Prof. Schuh, RWTH Aachen).
All the winning teams also share one characteristic: an enormous team spirit. Siemens Karlsruhe has specially launched a programme "Factory2be - Focus on People" and the keynote was started with mindfulness training. The motto: "It is only through people that our digitalised factory becomes intelligent". Beiersdorf, Kurtz Ersa and Co also impressed with a cohesive performance and exceptionally good atmosphere. The shortage of skilled workers makes it clear how important it is to invest in further training and the work experience. At the same time, however, it is important to create a sense of belonging in order to retain and motivate employees. Shared success seems to be a key element here.
In addition to these core aspects, I took away three other exciting aspects:
CIP is preferred compared to major disruptions (Brose).
Despite strong efforts such as advertising the professions in the school context, the perceived attractiveness of "classic professions" such as mechatronics or machining mechanics is declining, while demand has increased by double-digit percentages over the last 4 years (Brose)
Matrix production is a promising approach for high productivity despite small batch sizes and is already in productive use (Siemens Karlsruhe)
Much approval for more connection and support for the operational workforce
As Operations1, we had the honour of presenting our platform as a top 5 nominated start-up in Germany in the field of production. Very briefly, I was able to address three core aspects:
Where the disconnect is between connecting machines and connecting employees
How strategically important employee connection is in relation to skills shortages, demographic change, supply chain issues and continuous improvement
The immediate business benefits of engaging employees in a digital organisation and providing them with context-based information
The discrepancy between the connecting of machines and people is obvious. Even 10 years after the term Industry 4.0 was coined, many operational employees still work with a multitude of analogue and complex systems. Instead of unifying information flows and simplifying employees' daily work, the standard is that employees have to find their way around 10 tools at the same time: pen and paper, manuals, tacit knowledge, printers, reference documents, complex ERP interfaces, manual sensor data transmissions, separate digital cameras, manual database entries, decoupled task management, physical archives and much more. Here, in my opinion, it is essential to unify information flows.
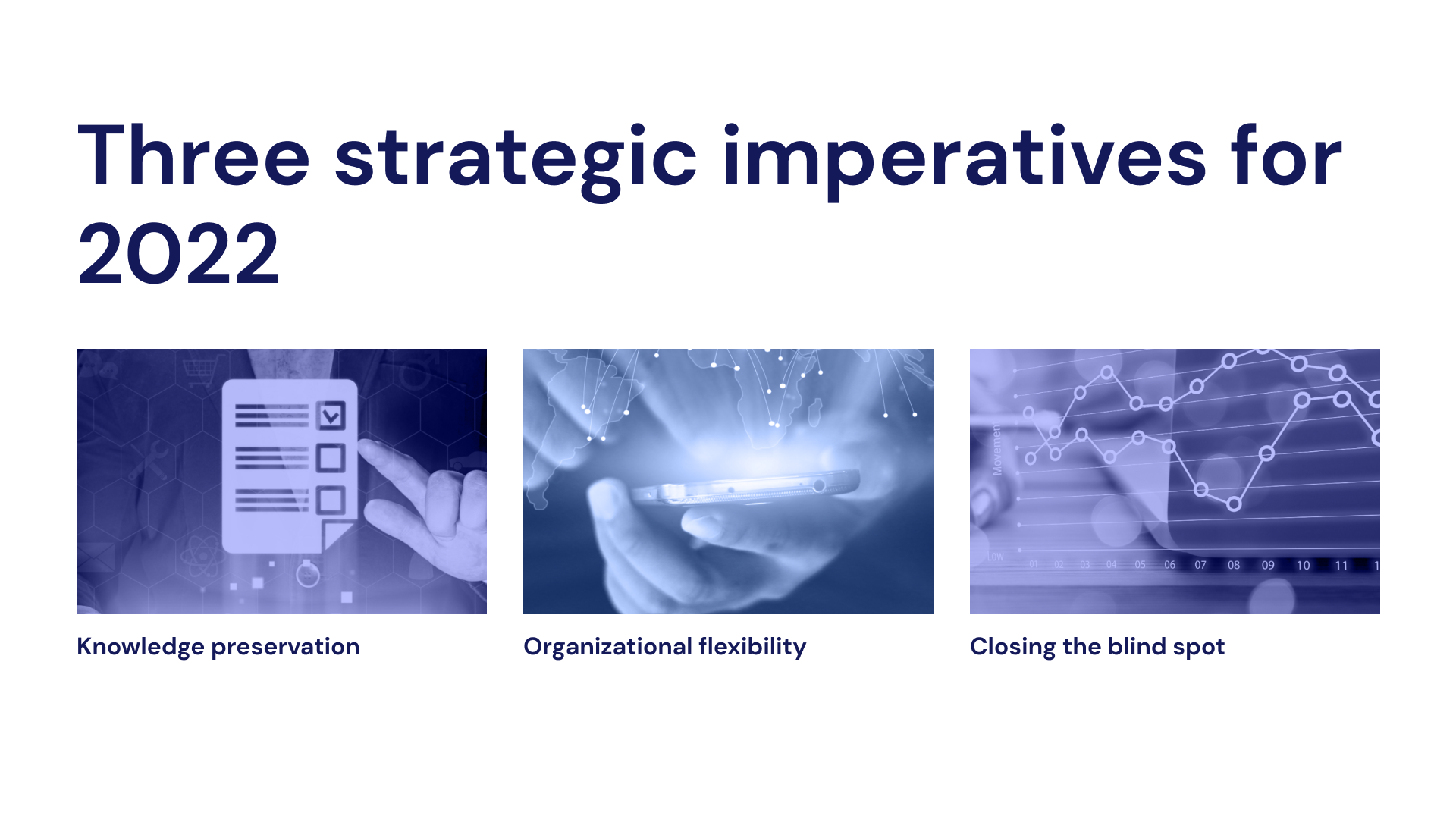
According to a McKinsey study collaborative processes still have 30% efficiency losses. Efficiency losses that can be painful, especially against the background of the shortage of skilled workers.
What role does this currently play in the major challenges facing manufacturing companies? The context-based provision of information and connecting of employees increases the flexibility of companies enormously. What our customers show is that new employees are productive much faster, employees can be deployed more flexibly for different activities and process knowledge is sustainably secured. The supposed elimination of "typical paper documentation" thus goes far beyond the efficiency gains that come from less document processing, avoidance of manual data transfers and travel times. The connecting of operational staff increases the resilience of the entire production operation.
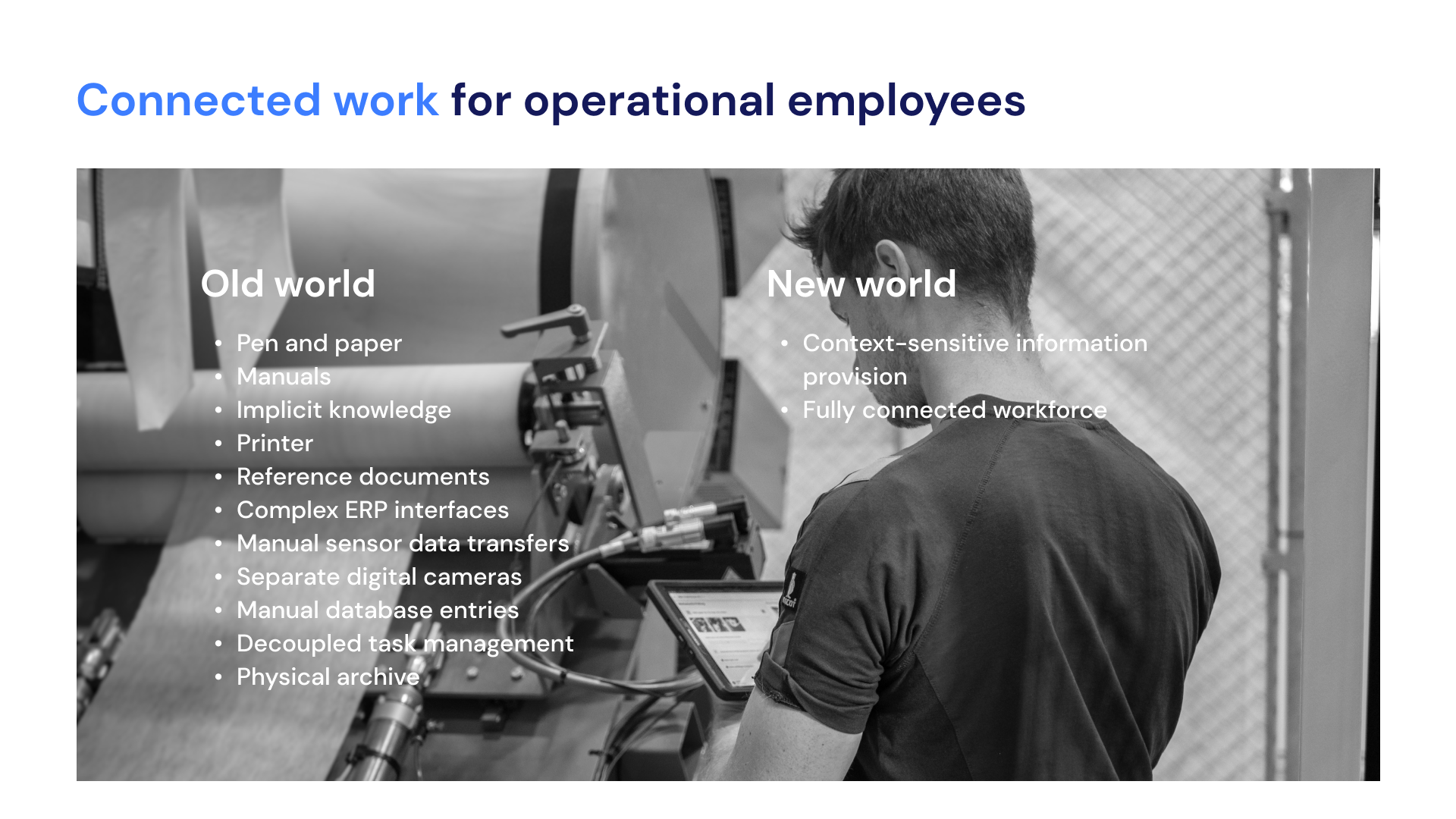
However, the directly measurable, business benefits also provide strong arguments to deal intensively with the topic of connected work. With our customers, for example, we measure reductions of 60% in the area of machine downtimes, seven-figure savings through insourcing of maintenance services, a decrease in error rates by 55% and cost savings in the six-figure range alone (see Soudronic case study) through the elimination of paper documentation. So it's worth it.
What I find particularly exciting is that despite major innovation offensives by Germany's leading factories, there is often still a discrepancy in how dynamic and "employee-friendly" the systems on site really are. It is true that the level of digitalisation is often already very high. However, there is a massive difference between displaying PDFs on a vertical touchscreen and the employee scrolling through them. Or whether an interactive, dynamic solution is in use via which the employee can communicate, feedback information and receive rich information through media content such as videos.
So not all digitalisation is the same. In my opinion, it is essential to constantly reinvent oneself and not to stop as soon as the paper disappears.
Conclusion
At the Factory of the Year 2022 event, the focus was on sustainability, value orientation and digitalisation and absolutely impressive companies were awarded. At the same time, it became clear that connecting and supporting operational employees will continue to be a major field of activity. Important here: proceed in an employee-centred and pragmatic way.
Do you have questions about the connecting your operational staff?
Feel free to send us your thoughts, comments and questions via the contact form. We will be happy to get back to you.
Benjamin Brockmann
Benjamin Brockmann (M. Sc., Management & Technology) founded Operations1 in 2017 together with Daniel Grobe (also M. Sc., Management & Technology). The founders developed the software solution based on various practical projects, including at the Fraunhofer Institute, and on their experience in industry, auditing and management consulting. Benjamin Brockmann has already worked for companies such as KPMG and Arthur D. Little.