- -60% Downtime in overseas plants
- -50% Process deviations
- 250 000€ savings per site
Operations1 contributes to an improvement in costs and thus also to our competitiveness.
Maintenance Leader, Hirschvogel Holding
Status quo
Back in 2018, Hirschvogel faced two main challenges: Long reaction times in maintenance and a high dependency on service providers, resulting in high cost for the enterprise.
Furthermore, the high dependency on individual workers’ knowledge, which constituted an operational risk for the company, cumbersome handling of paper documents, and the complicated proof of performed processes required a fundamental change.
Learn how Hirschvogel saves 250.000 euros anually per site with Operations1
Implementation
Hirschvogel fully digitized all maintenance processes with Operations1. Maintenance activities can now be carried out by a broader group of people, resulting in shorter response times.
Hirschvogel is also able to track maintenance processes in great detail. This simplifies audits and allows the team to focus more on value-added activities.

Software rollout
Based on the success in maintenance, Hirschvogel decided to roll out the Operations1 software solution in many application areas such as quality control, logistics, shift handover, manufacturing, health and safety, and training.
Operations1 thus became the central platform for employee-driven processes worldwide. In total, over 1,500 Hirschvogel employees work with Operations1.
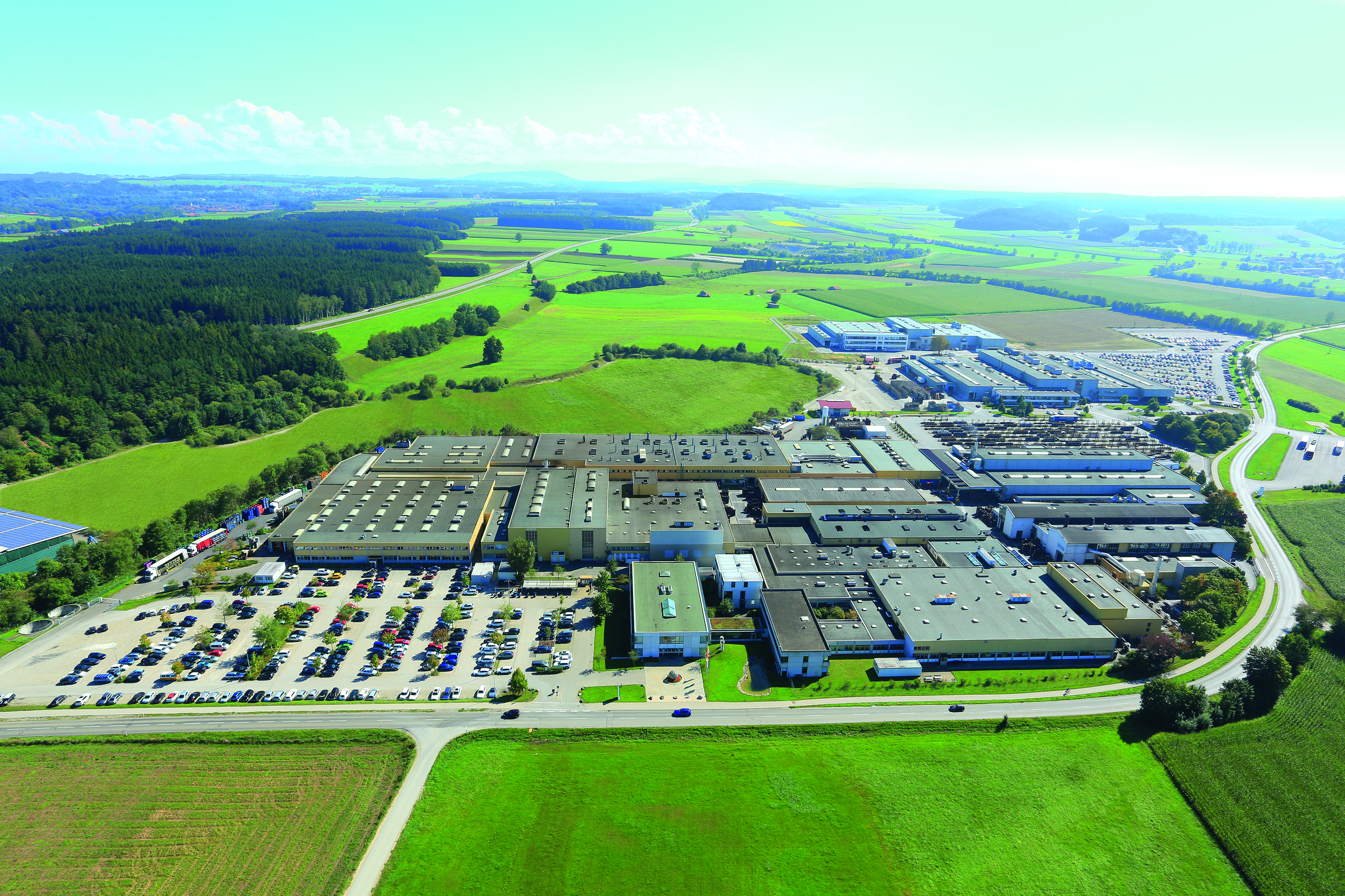
Results
Thanks to the global implementation of Operations1, leading automotive supplier Hirschvogel successfully transformed its formerly fragmented, paper-based process landscape.
Costs for external service providers were reduced by 250,000 € per site, while downtime in international plants dropped by -60%.
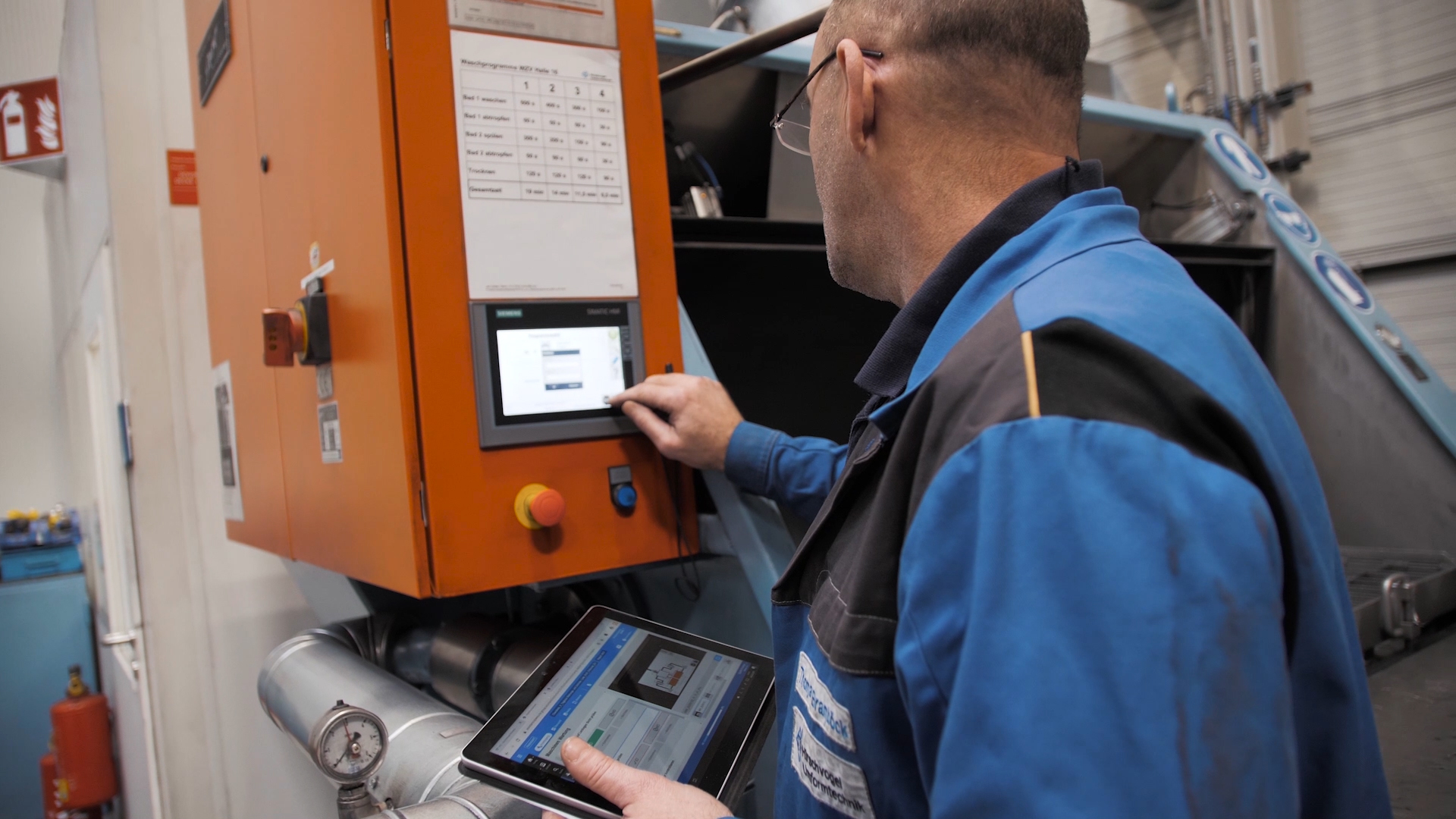
Digitize your maintenance processes with Operations1
Let’s start a conversation
Would you like to know how the digitalization of your maintenance processes can be implemented with Operations1?
Arrange a non-binding appointment with our team. Our experts will be happy to advise you based on your individual use case!