What it's about
Learn in this blog article how the maintenance plan guides your employees safely and reliably through any tasks on a daily basis and thus takes on an important function in manufacturing companies.
Clear maintenance plan as an important factor for successful maintenance
All recurring work and safety measures are scheduled in the maintenance plan: Maintenance plans determine when specific measures need to be conducted. This is a complex and challenging procedure for maintenance staff, as it is essential to ensure the optimum balance between efficient staff deployment and maximum plant availability.
What criteria must a maintenance plan fulfill?
1. Clear: Employees can quickly and intuitively understand which tasks need to be performed at what time.
2. Secure: The structure of the plan minimizes sources of failure, such as performing unnecessary maintenance work or omitting necessary maintenance work.
3. Dynamic: Maintenance intervals can be easily adjusted by feedback of findings, e.g. shortening the maintenance interval due to recurring findings in a specific component.
4. Integrated: An adjustment in the plan is directly reflected in the documents used for execution (similar to a smart workflow), i.e. maintenance instructions and checklists.
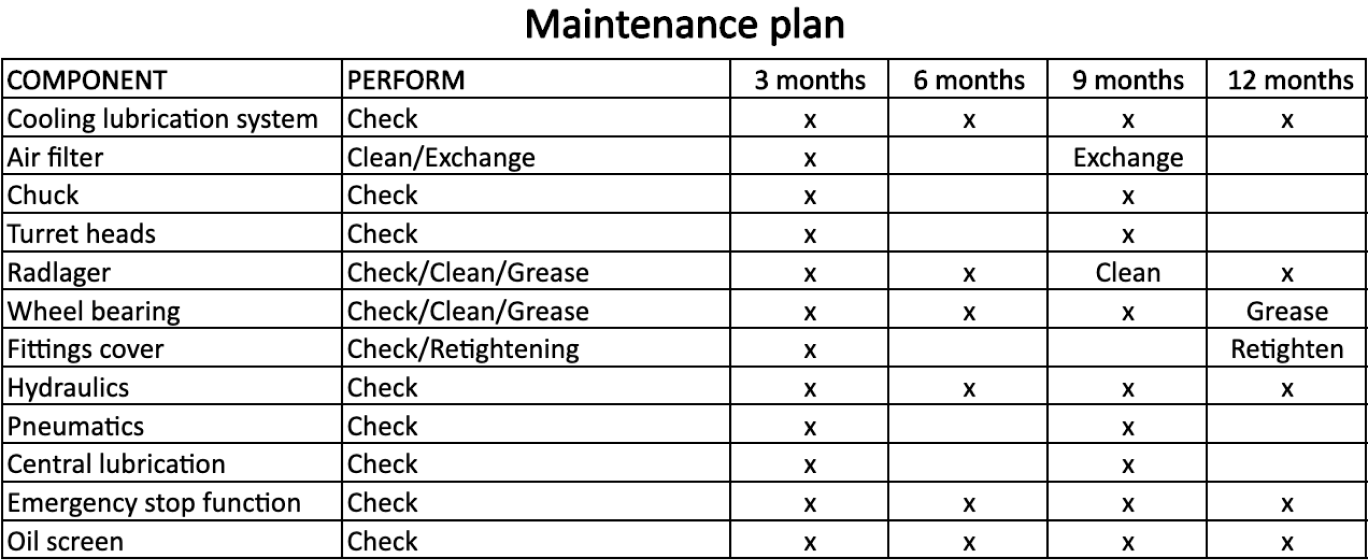
Maintenance plan 2023: With software to reliable maintenance processes
Maintenance plans often depict highly complex plant and machine structures. They therefore represent a basis for the overall maintenance performance that should not be underestimated. In fact, even in times of digitization, maintenance processes are still mostly planned in complex Excel sheets. Maintenance checklists and instructions, however, are available separately in paper form. As a result, the decisive link is often missing, which has a considerable effect on process adherence.
In 2023, companies need digital tools for optimal maintenance planning and control. These tools must be reliable, detailed and transparent in order to map the varied and complex processes and support maintenance workers in the execution of measures. Global players, such as the automotive supplier Hirschvogel Automotive Group, use software to map machines and systems digitally throughout the company. Defined intervals determine the scope of maintenance work. The maintenance planning is also directly linked to the corresponding maintenance checklists, which provide an appropriate information basis during process execution.
The solution used meets the following criteria:
Seamless integration into the existing IT landscape
Maintenance planning based on so-called ‘scheduled rows’
Mobile usability on the shop floor (worker assistance) and direct returns from the shop floor during execution
Live monitoring of the progress
Deep process transparency and intelligent analyses for continuous improvement
Interval planning in maintenance based on scheduled rows
The execution of inspections at certain intervals is necessary in order to maintain warranty claims of the manufacturer and to ensure high plant availability. The intervals at which the machines are serviced as standard depend primarily on the manufacturer, but also on the intensity of use. The manufacturer’s maintenance plan provides various inspection points, which are based on weak spots that have arisen in the past on similar machines.
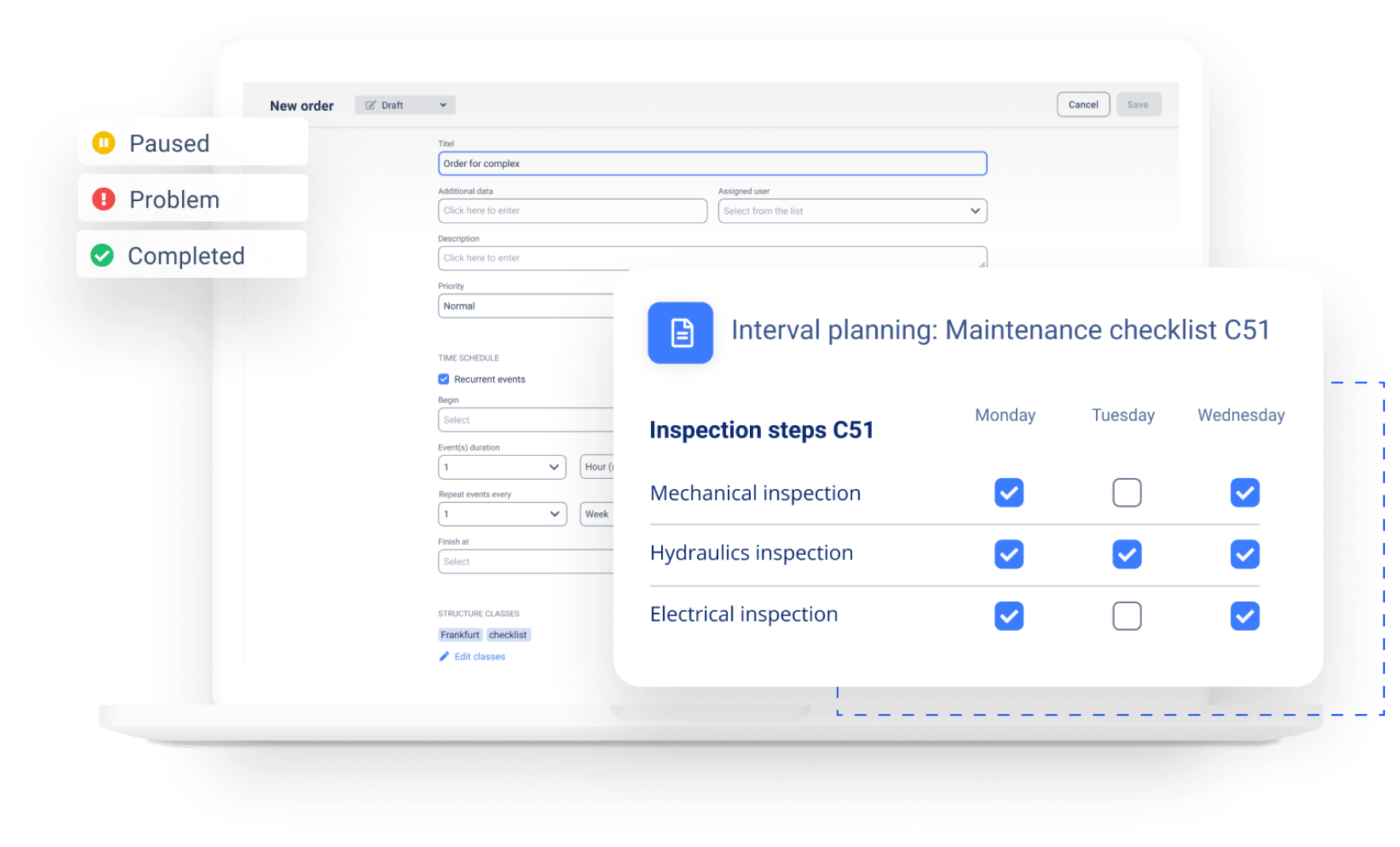
By planning in a software solution, capacities can be saved by precisely scheduling and managing recurring tasks and measures. Recurring activities can be defined by means of serial elements, so-called ‘scheduled rows’, and delegated to employees. The appropriate sub-steps for maintenance intervals are compiled from a clearly laid out test matrix, the relevant process instructions are digitally linked and the task is assigned to the employees, who are automatically and just in time reminded of the “To Dos”.
Automatically link the maintenance plan with maintenance instructions
So if the right software solution is used to digitally define maintenance planning based on ‘scheduled rows’, the link to maintenance instructions and checklists that guide maintenance staff through the process is also ensured. This allows step-by-step navigation through the process. Images, videos, pictograms, OK/NOK checkpoints, value returns and much more ultimately ensure that all sub-steps are processed with highest precision. Software such as Operations1 also offers the possibility of permanent insight into the progress with a live dashboard. In case of any incident, it is possible to react immediately via image and video return or chat function. Hectic telephone calls and coordination activities are no longer necessary when things have to move quickly.
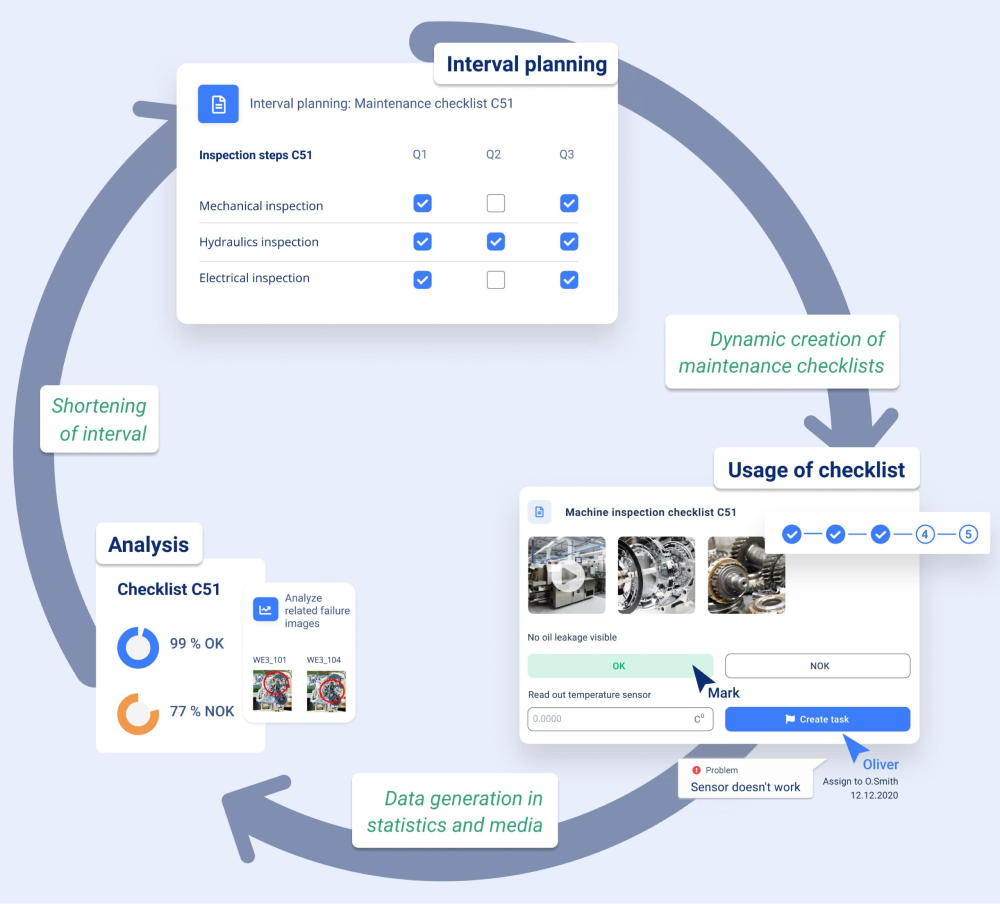
Practical example: Digital maintenance processes
By working with Operations1, Oetiker's entire maintenance system was digitized.
Within the first 6 months, the overall equipment effectiveness (OEE) was increased and the average repair time (MTTR) was reduced.
Conclusion
In summary: The maintenance plan should not be a stand-alone system. Rather, it should provide the clear and transparent basis for the dynamic creation of maintenance checklists in maintenance. By that, employees are guided safely and reliably through all tasks. A wide variety of returns directly from the process generate extensive data that can be intelligently evaluated using statistical and image-based analyses and thus contribute to adjustments of intervals – with an optimal balance of efficient employee deployment and maximum system availability in maintenance.
You would like to digitise your maintenance plans?
Learn how to digitise your machine maintenance plan and link it to interactive checklists. Get complete transparency on your activities performed.
Editha Bertsch
Editha is an experienced project management expert for manufacturing companies. With a clear understanding of the specific challenges of the industry, she is passionate about developing innovative solutions.