What it is about
In this blog article, we explain how a Connected Worker Platform (CWP) is an effective lever against the skills shortage.
The following topics are covered in the blog post:
- Status quo: the skills shortage threatens the shopfloor.
- How a Connected Worker Platform helps against it & what it is
- The 3 key levers of a Connected Worker Platform: securing knowledge, increasing productivity, and retaining employees.
Status quo: the shortage of skilled workers threatens the shopfloor
The manufacturing industry is one of those sectors that will suffer seriously from one issue in the coming years: Skilled labor shortages. While the trend toward plant bottlenecks was already creeping in over the past few years, the shortage of skilled workers is now a bitter reality. A recent VDMA flash survey shows that 78 percent of companies see themselves threatened by a serious shortage of personnel. The shortage is expected to worsen over the next three months.
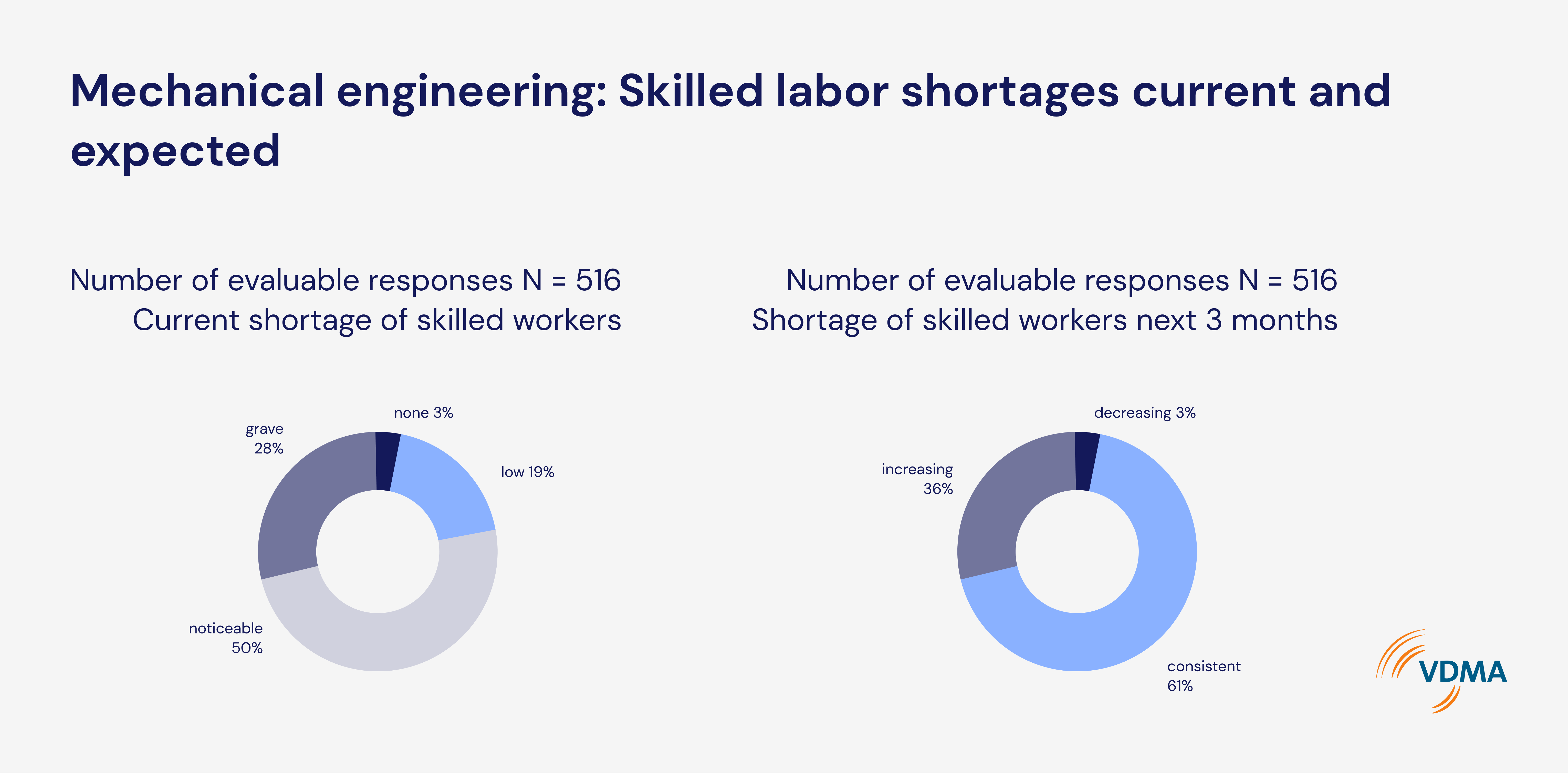
The main cause of this aggravation is the increasing aging of society. According to the German Federal Ministry for Economic Affairs and Energy, the number of people in Germany who are capable of working is expected to fall by 3.9 million over the next ten years. In manufacturing companies, areas such as assembly, maintenance and quality inspection will be particularly hard hit. In view of this alarming development, clear action is therefore necessary.
How can the shopfloor address the issue of a shortage of skilled workers? In our experience, this requires two things: a consistent digitization strategy and the right technology in the form of a Connected Worker Platform (CWP).
What is a Connected Worker Platform?
"Connected Work" generally refers to a modern form of working that focuses on connection, agility, efficiency and personal responsibility. Technologically, this can be realized with a so-called "Connected Worker Platform". In contrast to a Worker Assistance or Worker Information System, a Connected Worker Platform is based on the connectivity of the worker with his or her working environment. This interlinking concerns all organizational, process-related and technological procedures. The organizational component involves the horizontal connection of employees in the production environment as well as vertical connection to the management level through simplified communication and information provision. The process level involves bridging system gaps in the execution of processes - in other words, generally eliminating manual data transfers and time-consuming information procurement. Finally, technological connection aims to embed the worker in a comprehensive digital system.
A Connected Worker Platform thus goes far beyond the purely cognitive and physical support of Worker Assistance Systems, such as by providing assistance to prevent a physical stress disorder. It can also be described as a kind of "ecosystem" of connectivity between machines, workers and production supply chains.
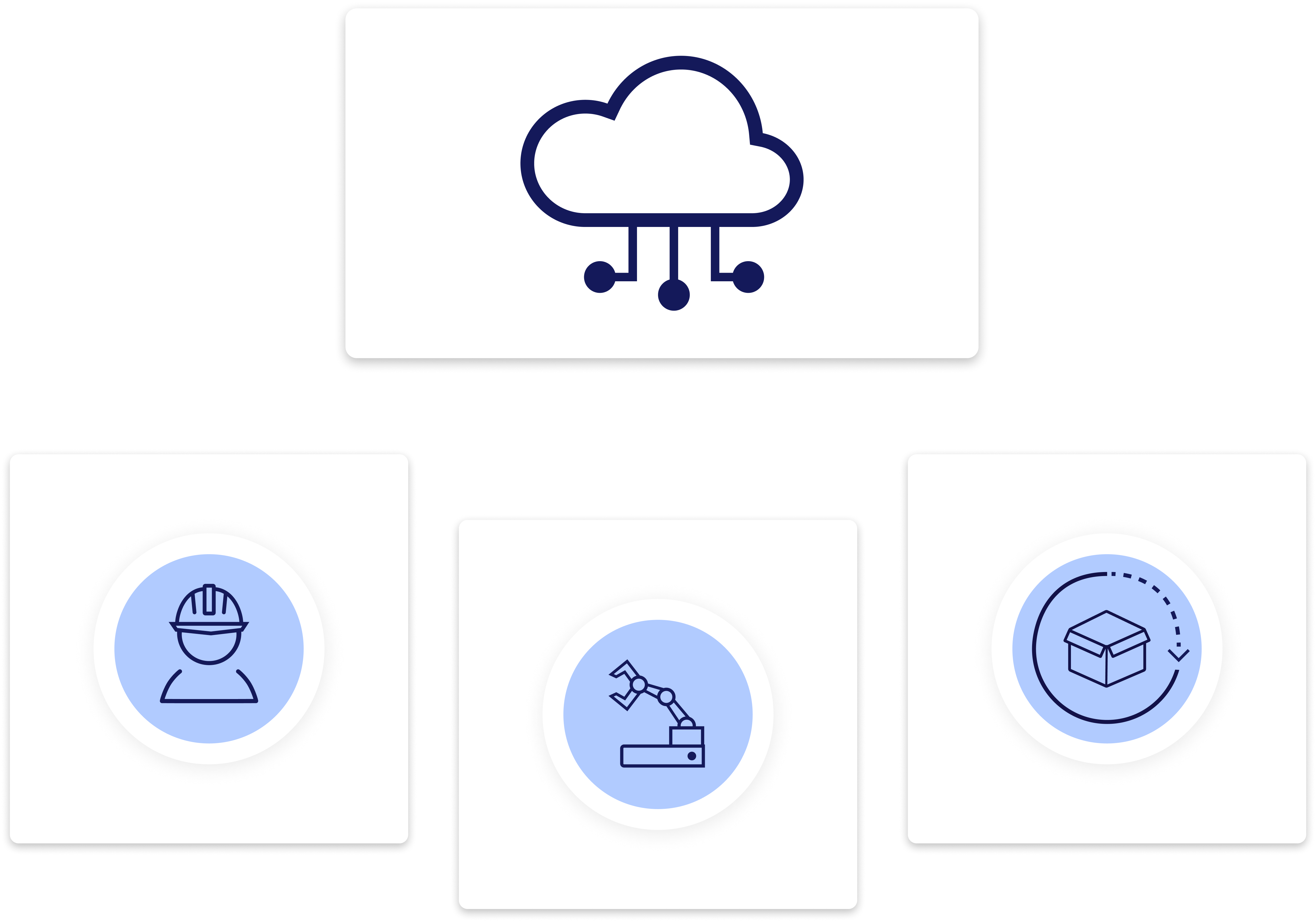
How a Connected Worker Platform protects against skills shortages
A Connected Worker Platform offers three key levers to sustainably protect the manufacturing and production industry against skill shortages: knowledge retention, productivity improvement, and employee retention.
Securing knowledge as protection against a shortage of skilled workers
The baby boomer generation is leaving the factory floor - and there is a danger that the accumulated knowledge of an entire working life will disappear with it. This is all the more alarming because the knowledge built up over the years is an important production factor and the basis for quality assurance. If expertise is not available, industrial production processes automatically grind to a halt. The consequences are obvious: Competitive advantages for the competition, it is not possible to react quickly enough to increasing customer requirements, orders are lost and the expertise disappears with the retiring workforce. In the long term, the innovation and competitiveness of a company are at stake and its future viability is threatened.
To prevent such a scenario from becoming reality in the first place, it is crucial to store a company's existing wealth of knowledge centrally in the cloud and thus make it accessible to every employee at any time from any location. A Connected Worker Platform makes this easy because it adds value in three ways:
It can make implicitly existing knowledge explicit.
It enables a central and structured organization of knowledge.
It ensures flexible employee deployment thanks to the intuitive provision of knowledge.
1. Making implicit knowledge explicit
The transfer of employee-dependent knowledge into knowledge made available to the entire workforce is achieved on the one hand through the simple creation of image- and video-based work instructions, checklists, test protocols, and much more. Central to this is that the operation is intuitive, based on transparent review processes and links the production resources "machine", "employee" and "information". Detailed information about the advantages of digital work instructions can be found in our blog post .
On the other hand, knowledge transfer is achieved by establishing living process knowledge with the help of continuous worker feedback on product, process and service quality. This ensures that knowledge does not become obsolete and is validated regularly. Supporting such a continuous improvement process (CIP) through a Connected Worker Platform ensures that employees receive the right information in a simple presentation manner and leads to higher process fidelity. Our blog post on this topic explains how this works in concrete terms in everyday work.
2. Structured organization of knowledge
A Connected Worker Platform offers the great added value of standardizing and organizing comprehensive process knowledge. Modular structuring of content creates a central point of process truth, which also sustainably and drastically reduces adaptation efforts in test documentation. In this way, standardized documents can be rolled out quickly, even at a company's international production sites, and similar work steps can be easily applied to variants - an enormous gain in time and efficiency.
In addition, documents and entire processes can be classified and structured in a Connected Worker Platform using filter logic. With the help of such structure classes, it is possible to assign specific access rights and to make knowledge available on an individualized basis for specific locations, teams, individual employees and products.
3. Flexible employee deployment
In a Platform for Connected Work, process knowledge is dynamically made available to each worker in real time and can be intuitively understood thanks to image- and video-based communication. For the company, this has the advantage that production workers can be deployed much more flexibly. One way this is achieved is through the multilingualism of the software solution. Employees from different production sites can thus work together efficiently and simultaneously on the same document. Time-consuming and incorrect translations by specially assigned employees are no longer necessary, and production processes can be implemented much more quickly.
The provision of information for specific variants on a Connected Worker Platform also means that employees can be deployed more flexibly, because they are only provided with the relevant information they need for the order or product in question. Creating a centralized yet flexible point of process truth for assembly and inspection processes as product diversity increases thus significantly reduces complexity for workers, avoids duplication and information redundancy, and reduces the effort required to create them through automated configuration. Our blog post sheds light on this in detail.
Finally, if knowledge is made available in a Connected Worker Platform in the way described, a company can also deal with the high fluctuation of temporary workers in a stable manner and hire manufacturing workers who have a lower skill level without hesitation.
In a nutshell, a Connected Worker Platform paves the way for a maximum of quality - regardless of location, language and employee qualification.
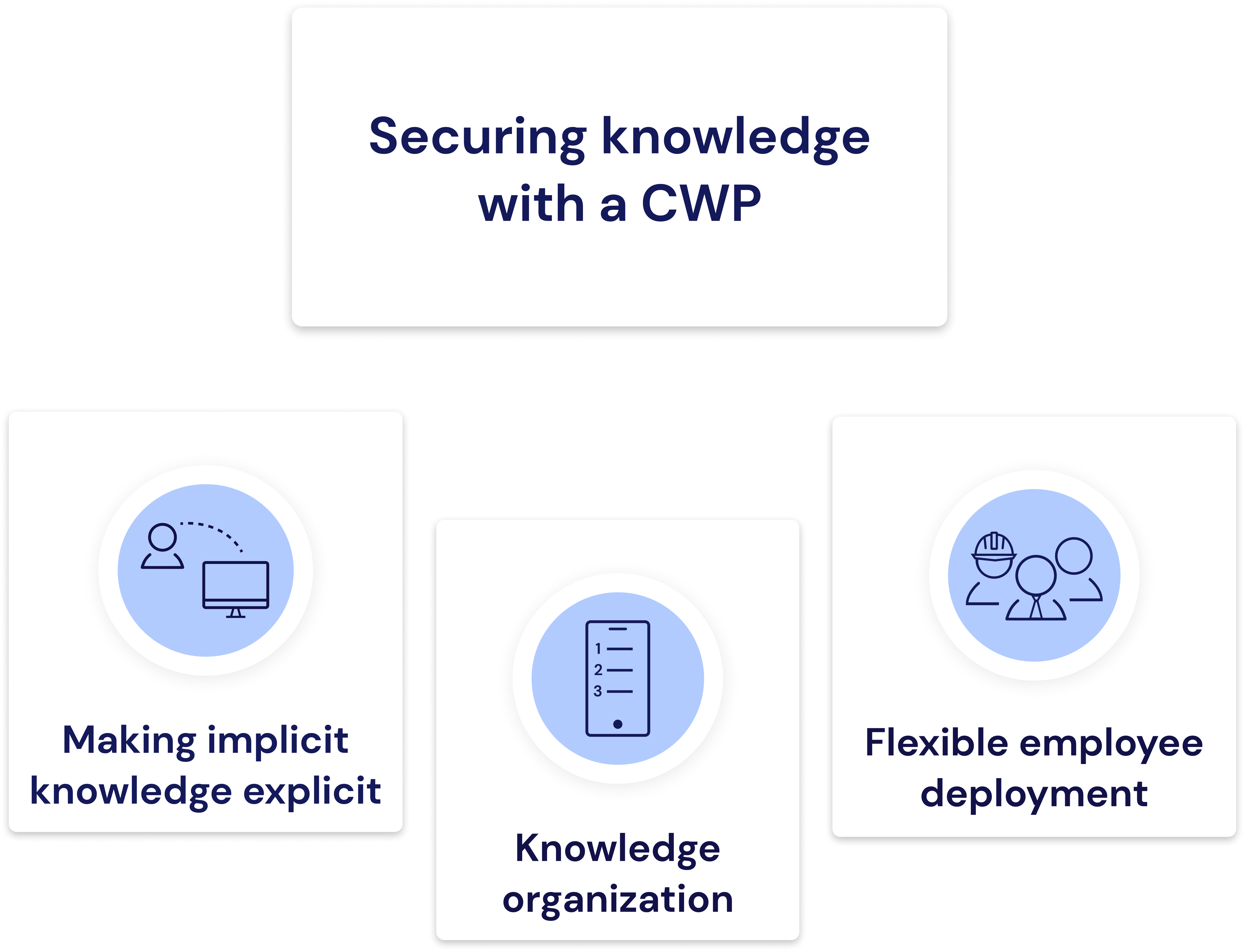
Increasing productivity with a Connected Worker Platform
The second lever that a Connected Worker Platform can use to protect the manufacturing industry from skills shortages relates to productivity.
If the introduction of a digital solution for Connected Work reduces complexity and eliminates non-value-added paper-based activities, this also has consequences for efficiency: The last mile to the worker can be digitally mapped in an integrated manner and a central point of process truth for assembly and inspection processes is created. Moreover, comprehensibly prepared checklists with detailed information provision enable workers to work more quickly on their own and achieve a much higher level of information-based security in the digital checklists, such as inspection steps. This eliminates the need for a long training period and supervision by experienced colleagues.
In customer studies, we were able to measure increase rates of up to 21 percent. Increases in efficiency naturally also have a positive impact on productivity. For example, our customer POLIPOL, a manufacturer of high-quality upholstered furniture, can report a 67 percent faster achievement of target productivity thanks to a Connected Worker Platform.
Consequently, with a Connected Worker Software Solution, a company can accomplish more with its existing workforce than without such a solution. As a result of efficient working, labor resources can be deployed more flexibly in other areas - for example, by saving time in activities. This then leads to an employee being able to take on other activities as well. Against this background, the shortage of skilled workers and a shrinking workforce no longer pose a threat to a company, but are merely variables in an equation for which the solution has already been found.
The graphic clearly illustrates the added value of increased productivity with a Connected Worker Solution.
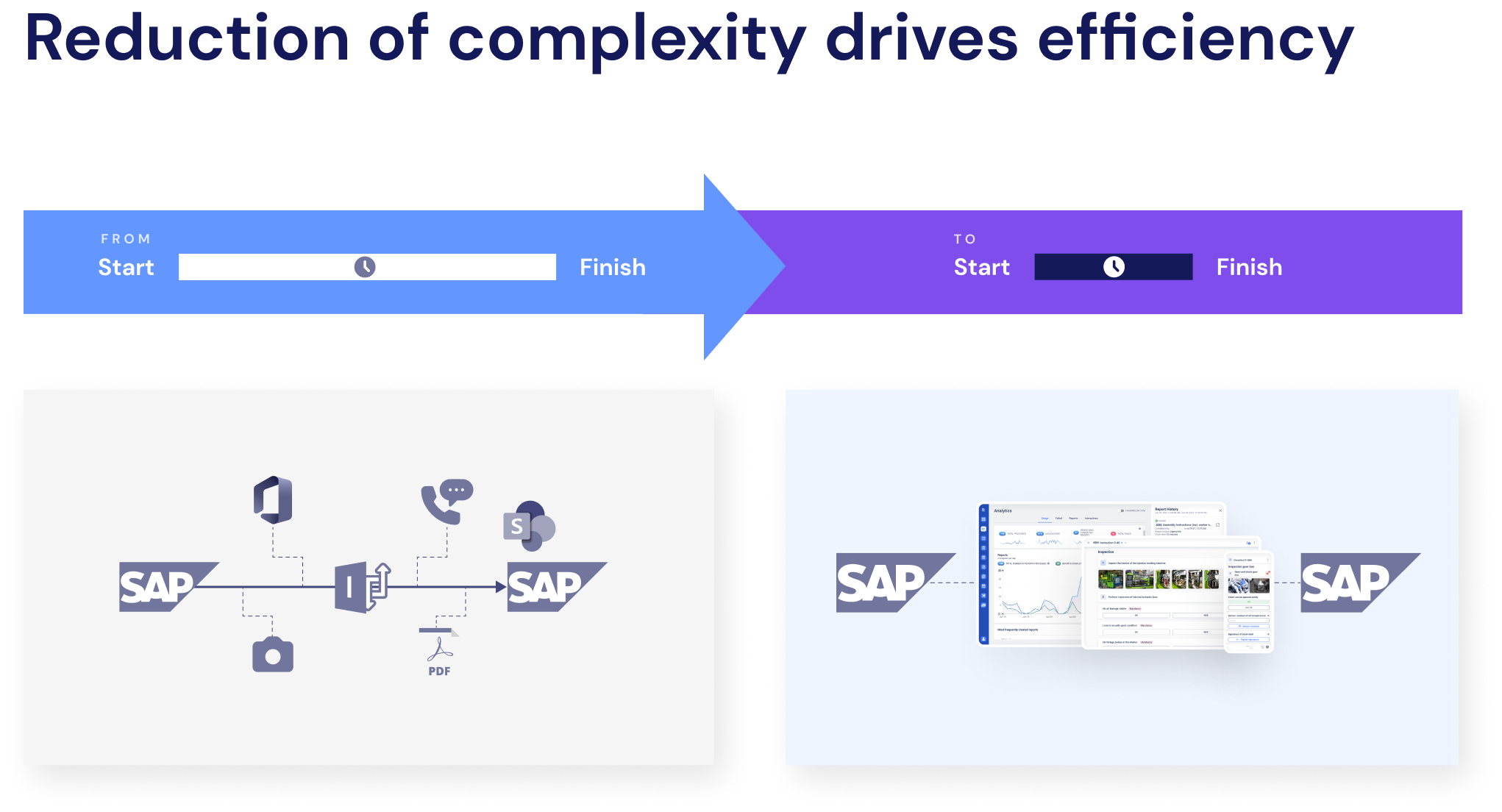
Retaining employees with the help of a Connected Worker Platform
In times of growing labor shortages, companies face the challenge of retaining their employees over the long term. According to the study "Kompetenzzentrum Fachkräftesicherung" (KOFA), sponsored by the German Federal Ministry for Economic Affairs and Climate Protection, this trend will continue to grow in the future, as the graphic shows.
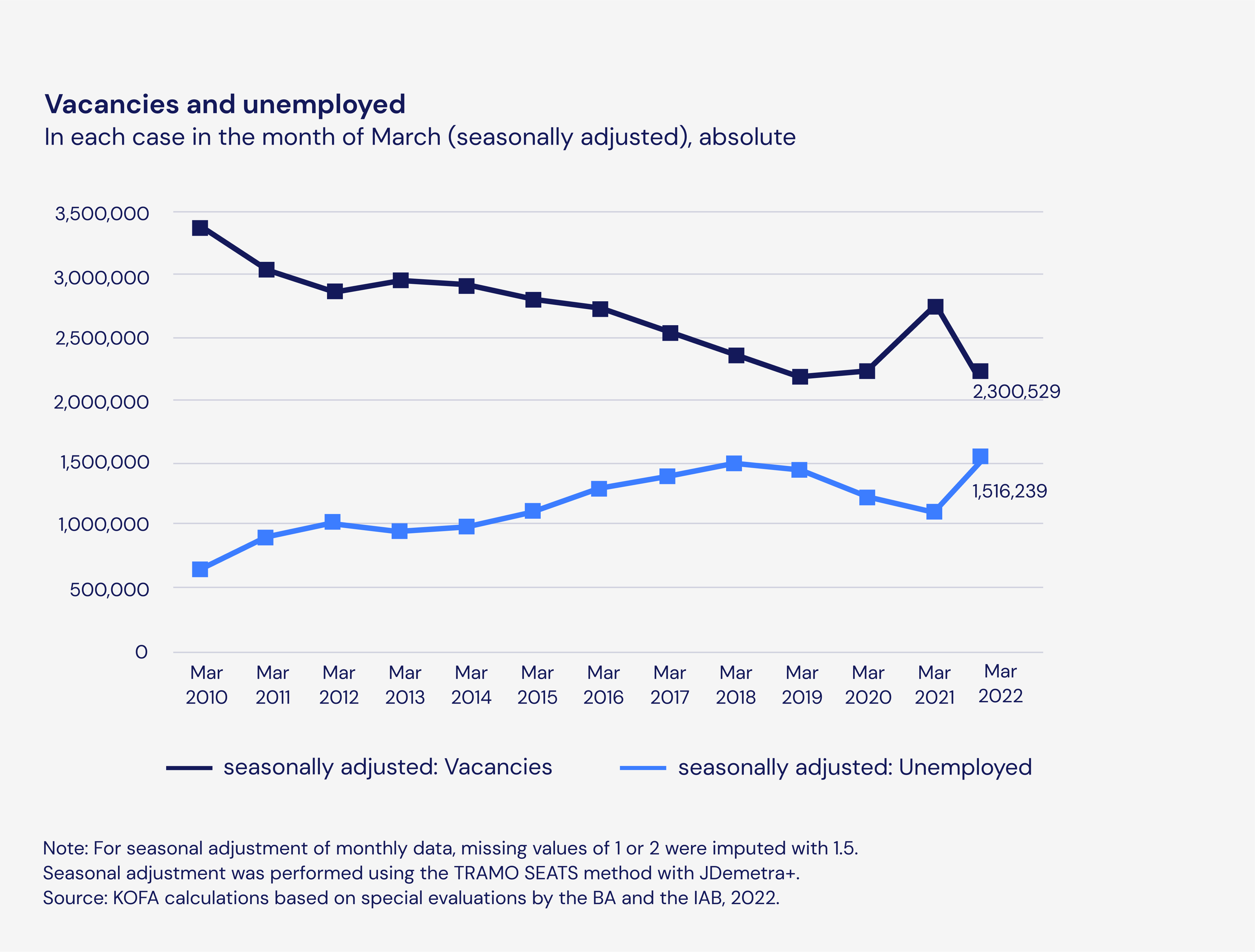
The chart visualizes the disturbing trend toward more and more vacancies on the labor market, which remain unfilled and reached a new record level of over 1.5 million in March of this year. In the first quarter of 2022, the number of vacancies increased by 5.3 percent across all requirement levels, while at the same time the number of unemployed fell by minus 16.7 percent year-on-year. The skilled labor situation for companies is thus tighter than ever, as the maximum number of vacancies is offset by a significantly shrinking number of unemployed. Retaining employees is therefore the top priority if companies want to secure their future and protect themselves against a shortage of skilled workers.
In parallel with this development, a Deloitte study from 2018, which is probably more topical today than ever before, shows that the majority of workers would like to see their activities digitized. Four years ago, 48% of the 640 respondents said that digital tools would make their work easier, 47% were convinced that they would work faster, and 63% said they would be open to technology if they knew specifically how it could support their work.
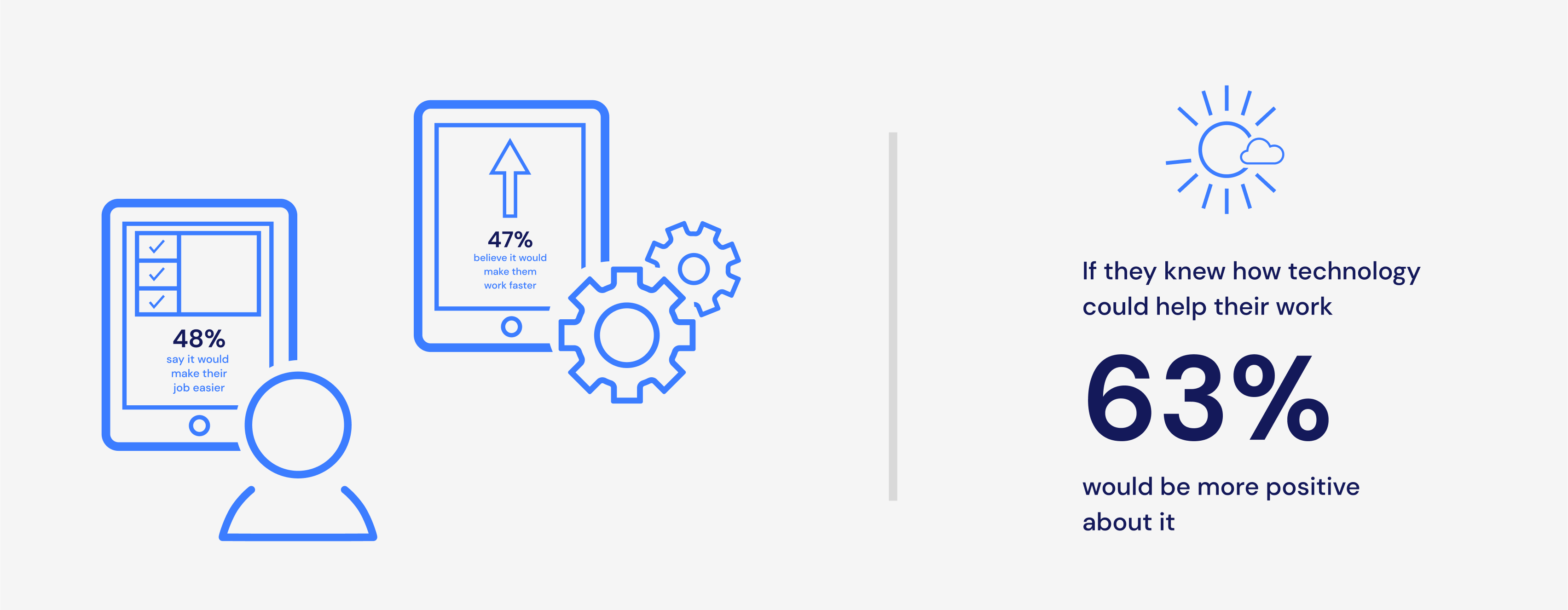
Therefore, the study sums up well the desire of employees to simplify and increase the efficiency of their work processes through consistent digitization. This is where a Connected Worker Platform comes in, because it offers workers full support and embeds them in a comprehensive digital system in which information is provided contextually and employees interact with IoT equipment and are connected in real time with each other as well as with management and work planning levels. As a result, it motivates shopfloor employees to remain loyal to a business for the long term.
In our experience, the winners when it comes to the shortage of skilled workers are those companies that already consistently rely on a Connected Worker Platform Solution. They position themselves as attractive employers, especially for the younger, upcoming generation, by creating additional incentives through a modern, sustainable working environment that employees are familiar with from their private lives. Digitization in production is therefore an essential component of a future-oriented employer branding strategy. Our customer Soudronic, a leading global manufacturer of production equipment for metal packaging headquartered in Switzerland, is a prime example of this.
Why a Connected Worker Platform is the future
The comments have shown that a Connected Worker Platform can be extremely effective in protecting the manufacturing industry from skills shortages. For more in-depth information about the software solution, its relevance to the industry, and how it differs from a Worker Assistance System, read our in-depth blog article on this topic. There you will also learn about the differentiating features between Connected Worker Platforms and get to know different use cases as well as a concrete use case from the industry.
The diagram summarizes the 3 central levers with which a Connected Worker Platform protects against a shortage of skilled workers. It becomes clear that with such a software solution, production companies are optimally equipped for the future.
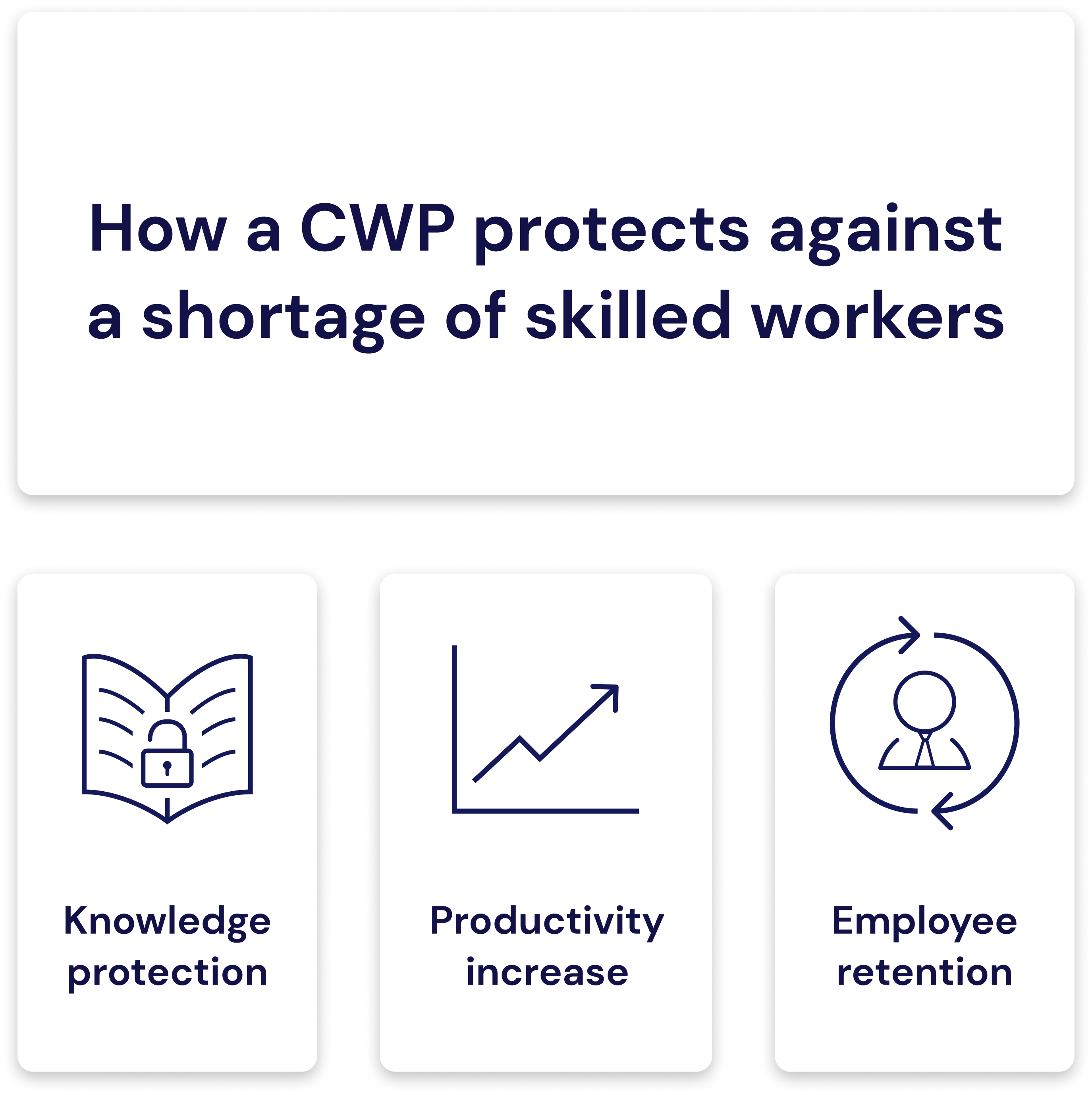
Conclusion: A Connected Worker Platform offers sustainable protection against the shortage of skilled workers.
Would you like to test Operations1?
Our Connected Worker Platform has many useful features in store for you.
Fill out the contact form with your thoughts and goals. We'll get back to you right away.
Editha Bertsch
Editha is an experienced project management expert for manufacturing companies. With a clear understanding of the specific challenges of the industry, she is passionate about developing innovative solutions.