What it is about
In this blog article, we explain the added value of digital autonomous maintenance on the shopfloor.
The following questions are addressed in the blog post:
- What is autonomous maintenance?
- What are its benefits?
- How is it implemented?
- 9 advantages of digital autonomous maintenance with Operations1
What is autonomous maintenance?
Autonomous maintenance, which is also referred to as "self-sufficient maintenance", pursues the goal of ensuring that machine operators are able to operate the plant independently. To this end, they are trained in such a way that they can carry out cleaning, inspection and maintenance work independently of the maintenance supervisor. The resulting dissolution of the strict division of tasks between workers and maintenance leads to an increase in awareness on the production side in the early detection of faults and at the same time relieves the maintenance staff, who can direct their focus instead to complex maintenance measures and their optimization possibilities.
This creates a foundation based on 3 principles:
A positive relationship is created between the worker and his machine.
The production worker should be able to feel responsible for his own tool.
The employee's performance can only be as good as the condition of his machine.

The concept of autonomous maintenance originated in Japan and is part of Total Productive Maintenance (TPM). This refers to a concept in maintenance that aims to increase equipment effectiveness and the service life of equipment, thus realizing a production system that is as trouble-free as possible. Effectively optimized, cost-optimized maintenance is designed to eliminate losses and waste, thus ensuring "zero defects," "zero failures," "zero accidents," and "100 percent quality."
Autonomous maintenance forms the second of a total of eight pillars of TPM, as the graphic shows.
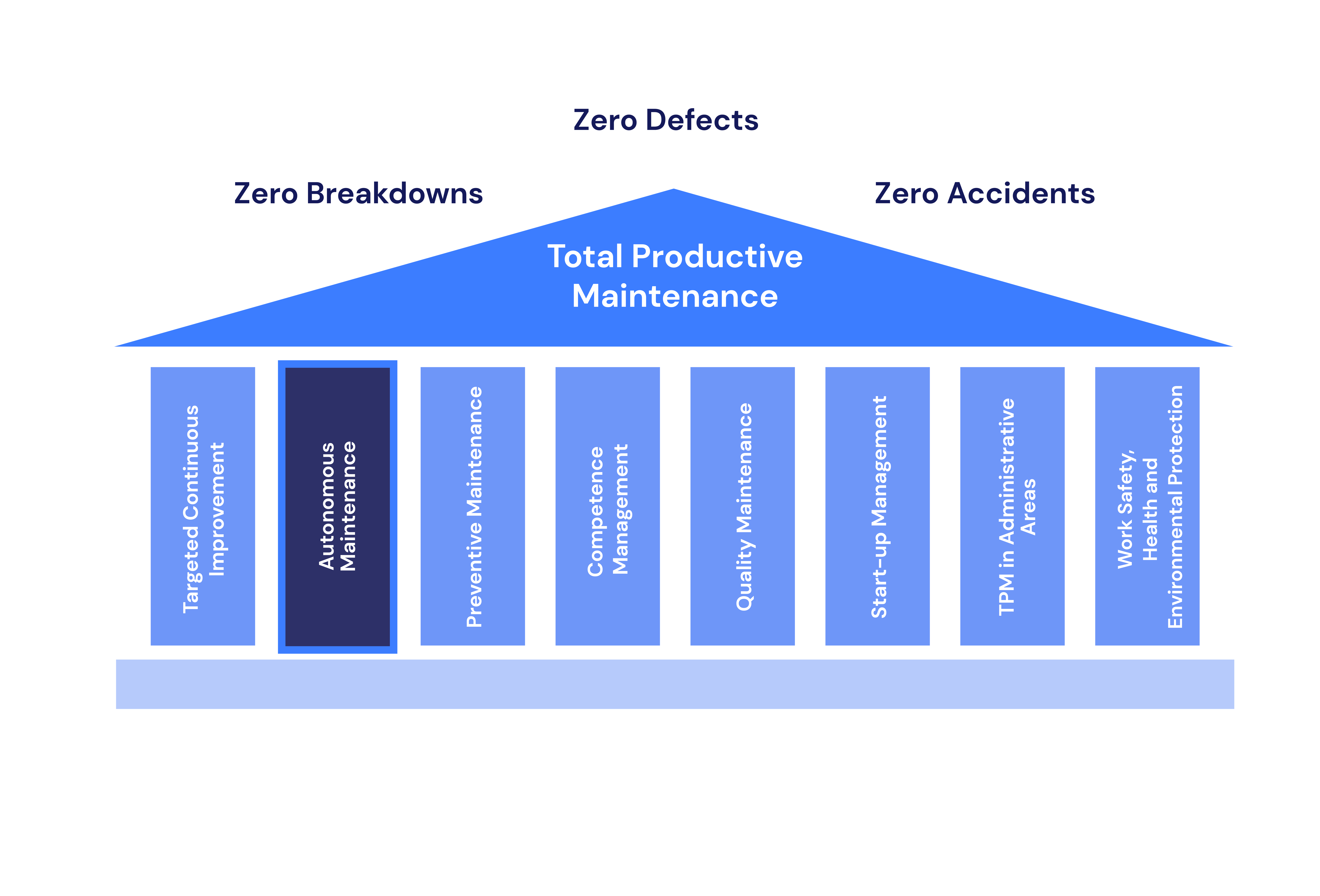
Detailed information about the concept of TPM, its origins, the advantages and disadvantages on the shopfloor, the implementation as well as the added value of digital TPM can be found in our blog article.
What are the advantages of autonomous maintenance?
When the attitude of "everyone takes care of his machine" is internalized by production employees and lived in everyday life, a paradigm shift with numerous benefits for all stakeholders involved is created. These 9 benefits are the result of autonomous maintenance:
Increasing productivity and quality The concept of "More care through personal responsibility" leads to fewer feedback loops and thus increases the performance of man and machine.
Reduction of costs While external maintenance technicians often have to travel from outside, operators are always close to their machine anyway.
Low downtime When long response times for maintenance and a high dependence on service providers are eliminated, machine downtime is also reduced. Our customer Hirschvogel was able to minimize downtime by 60%.
Higher resilience In times of shortage of skilled workers, the higher competence of workers proves to be particularly future-proof for the company – also and especially with regard to the factor competitiveness.
Higher employee retention If the workers are given more competence for their machine, they will stay with the company longer because they feel more valued and more connected to "their" machine.
Relief for maintenance staff Maintenance staff can be deployed where they are really needed or direct their focus to more complex work.
Early fault detection This can prevent permanent damage to the plant.
Increased occupational safety The risk of injury to employees decreases when machines are maintained more regularly and malfunctions or problems occur less frequently.
Increasing overall equipment effectiveness (OEE) The basic question is: How productive was a plant in real terms in relation to its operating time? Overall equipment effectiveness (OEE) describes the performance of a plant and relates the following 3 factors: 1) machine availability (= ratio of planned production time to real operating time), 2) machine performance (= output) and 3) quality level (= number of usable parts to total number of parts produced). The diagram illustrates this relationship.
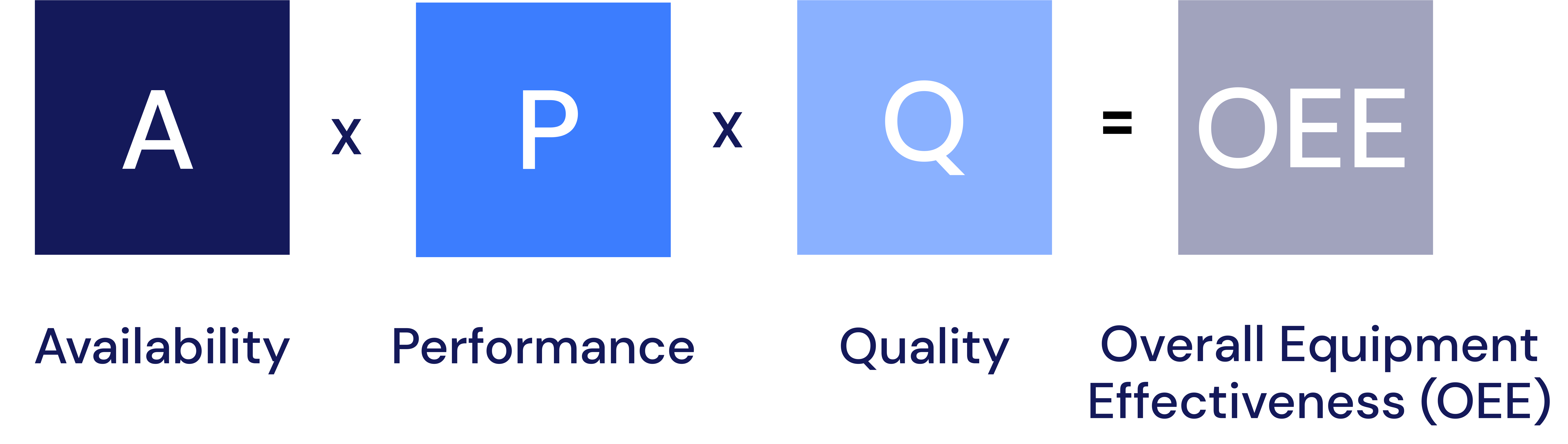
The many advantages make it clear: The use of autonomous maintenance significantly increases the efficiency and safety of a company.
How is autonomous maintenance introduced?
Autonomous maintenance can be introduced in a structured manner using a 7-step approach:
Stage 1: Joint basic cleaning & initial inspection
In stage 1, a joint basic inspection of the entire plant is carried out with the production staff to check the machine for defects. The latter are identified and subsequently rectified. In addition, new cleaning and maintenance plans are drawn up jointly and implementation is ensured.
Stage 2: Establishing optimal conditions for efficient cleaning operations
This is achieved by jointly identifying and eliminating sources of contamination. In addition, sources of defects and areas that are difficult to access are eliminated. In this way, cleaning, inspection and maintenance times can be reduced.
Stage 3: Defining standards for cleaning and lubrication
In this stage, improved standards for cleaning, inspection and maintenance are defined in the form of checklists. This is supported by the establishment of cross-functional improvement teams.
Stage 4: Development of training modules for autonomous maintenance
In stage 4, workers are taught the necessary knowledge to take over maintenance tasks independently in training modules.
Stage 5: First autonomous plant inspections
At this stage, the machine operators are sufficiently familiar with their new tasks and can independently perform cleaning, inspection and maintenance of the equipment according to adapted plans. In this phase, it is important to develop standardized checklists and maintenance plans that define maintenance intervals and responsibilities. The standards drawn up should also be constantly scrutinized and optimized.
Stage 6: Standardization in the process landscape
In this stage, workers can operate the plants independently and perform cleaning, inspection and maintenance tasks autonomously. Likewise, they can carry out simple repairs independently. The aim of this stage is also to optimize the entire workplace in terms of cleanliness, orderliness and the lowest possible losses.
Stage 7: Independent application of autonomous maintenance
In stage 7, autonomous maintenance is fully implemented. The aim is to continuously develop the existing processes. This is achieved by documenting and subsequently analyzing lost times.
It is important to check and ensure the achievement of each individual stage through internal audits. Only in this way can autonomous maintenance be implemented and lived in a sustainable way. The graphic summarizes the individual stages.
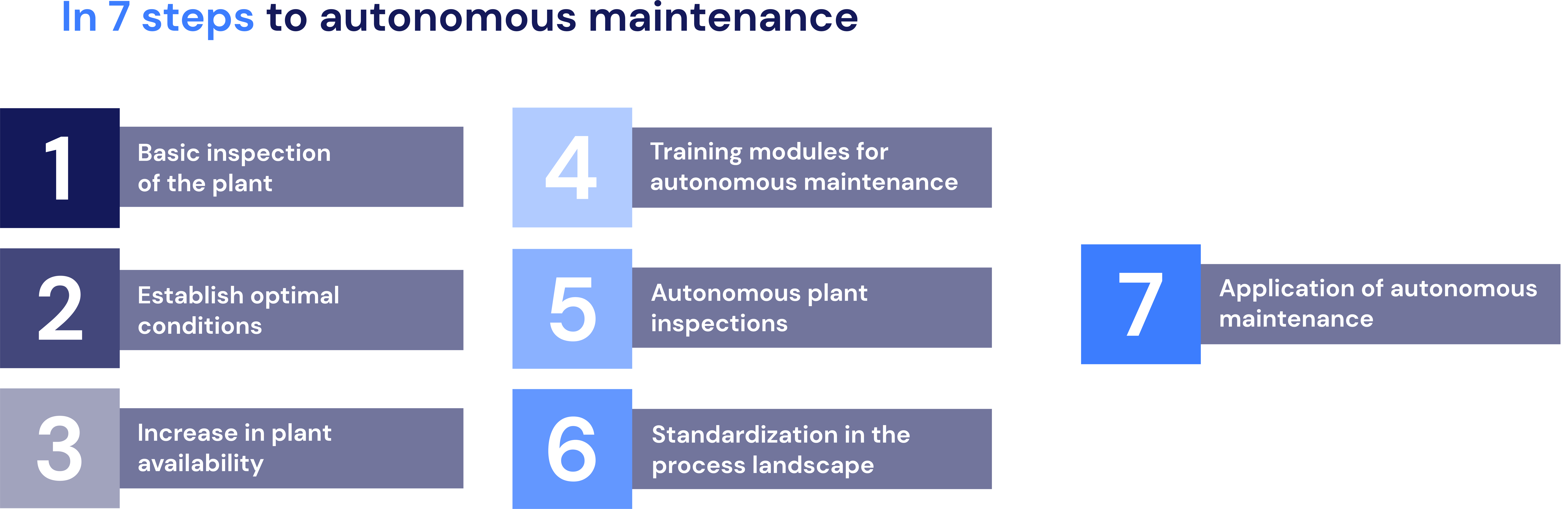
Autonomous maintenance – 9 advantages of a digital implementation with Operations1
We have seen how it is possible to increase the efficiency, safety and reliability of a company by means of autonomous maintenance. With a digital implementation of autonomous maintenance, you can take your operations to a new level of excellence.
These 9 advantages provide you with a digital implementation of autonomous maintenance with Operations1:
Simple and intuitive, text and video-based information delivery - paperless, real-time and multilingual
Simple and flexible user interface
If required, connection of Operations1 with your inventory systems such as CMMS, ERP and MES
Fast and collaborative problem resolution via task management and live chat
Uncomplicated documentation of non-rectifiable defects by means of video and image recordings for the maintenance engineer
Easy creation of maintenance plans and uncomplicated linking with digital work instructions and checklists
Mapping of maintenance intervals using detailed planning, in which activities are defined and assigned to employees
Flexible implementation of live monitoring through monitoring of activity progress in the dashboard
Automatic generation and transparency in the evaluation of digital maintenance reports
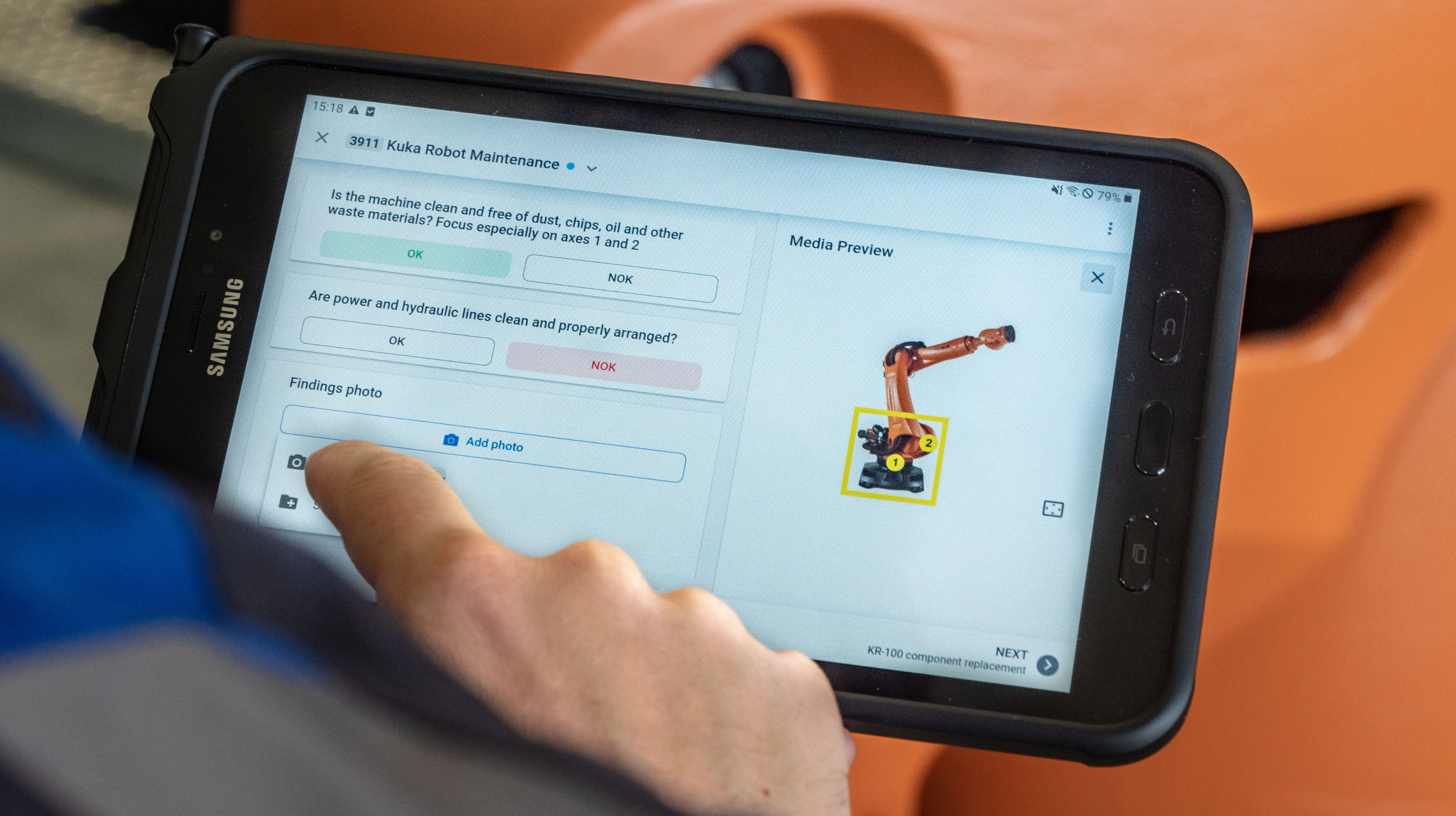
It becomes clear that autonomous maintenance is the key to increased productivity, cost reduction and greater resilience. With the help of a digital implementation, you provide process knowledge in real time and increase your competitiveness in the long term.
Conclusion: Autonomous maintenance is the basis for operational excellence on the shopfloor.
You want to work like Hirschvogel, Oetiker and many other market leaders?
Please fill out the contact form with your thoughts and goals. We will get back to you immediately and exchange ideas with you about your digital maintenance approach.
Markus Glotzbach
During his professional career, Markus gained deep insights at companies and large groups in different industries and knows the digitalization hurdles and problems on the shopfloor. Before joining Operations1, he studied International Management (MA) and worked in the Cloud Computing as well as SaaS telematics sector.