What it is about
In this article, we explain the added value of digital documentation for operational staff:
- What is a process description?
- What do you need process descriptions for?
- How is a good process description structured and how is it created?
- Difficulties of paper-based process descriptions
- What is the difference between a process description and a work instruction?
- 7 +1 Advantages of digital documentation with Operations1
What is a process description?
Whether repair and adjustment instructions, assembly, production, testing or maintenance instructions: process descriptions are an indispensable part of manufacturing operations. But what exactly is behind this term?
A process description is a sequence of events that forms the basis for the proper execution of activities on the store floor. It explains the sequence of activities performed by employees in manufacturing and service-oriented companies. The process steps and all relevant information are named in a very structured way according to the basic principle "Who does what, when and with what?" and "What information is required for this?

A process description is therefore a concatenation of individual process steps of an overarching workflow. The starting point of a process description is a systematic process analysis.
In addition, different superordinate aspects of a process description can be distinguished:
Control aspect: Employees should be able to see what is being done when and why. This both identifies and avoids sources of error, inconsistencies or duplication of work.
Organizational aspect: Tasks and activities can be assigned to departments or individual persons.
Information aspect: Here we look at what information is required for the correct execution of the individual activities and action steps.
Monitoring aspect: It is checked whether the process has achieved its goal in terms of process times and costs.
Safety aspect: Questions such as "Are all guidelines and legal requirements complied with?", "Is it clear who is allowed or required to do what within the process (e.g. decision-making authority and approvals)?
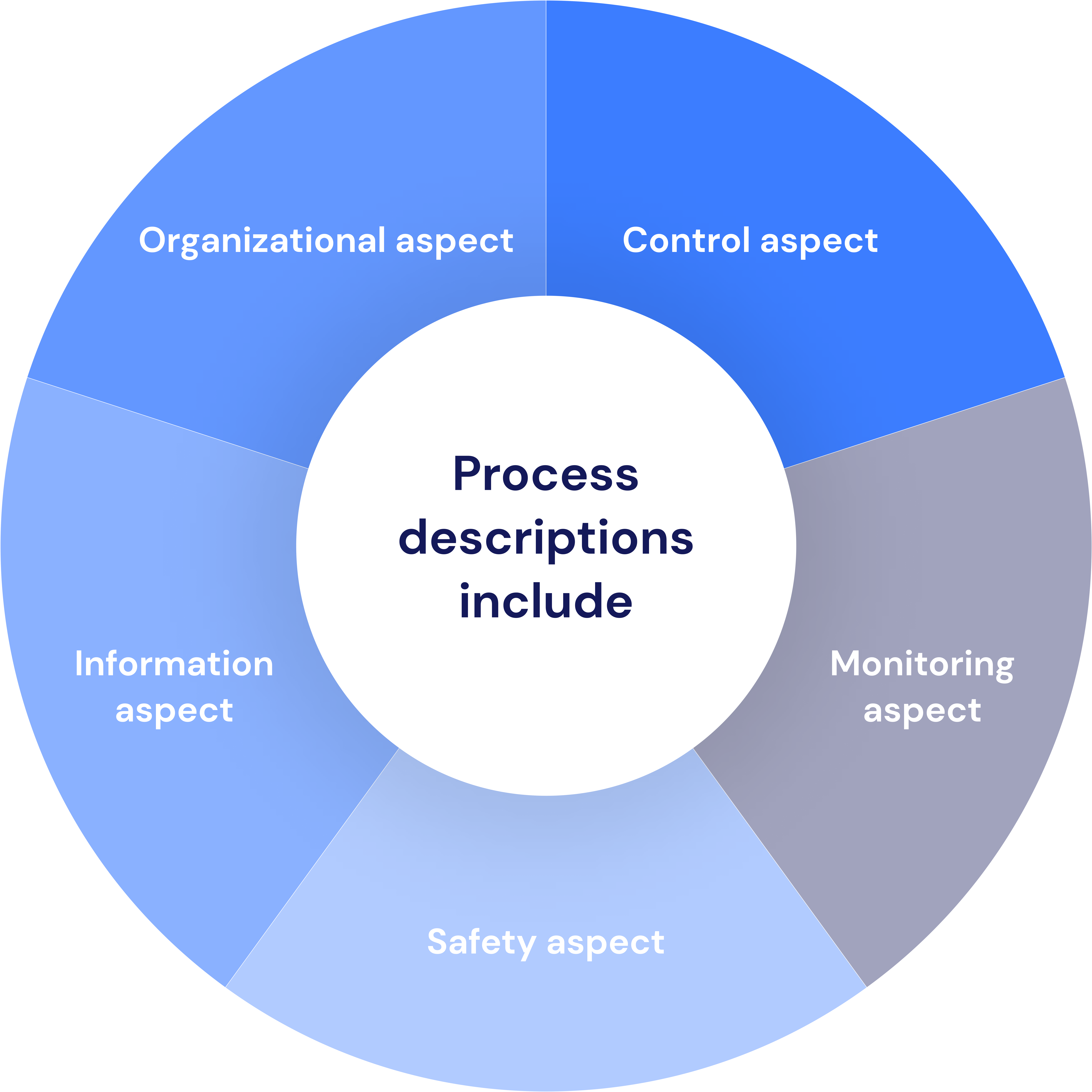
Process descriptions can be both descriptive and graphical. Visual and interactive communication through images and videos is particularly suitable.
What do you need process descriptions for?
The question of why companies need process descriptions is easy to answer: Processes should be presented in detail and transparently and thus made permanently accessible to everyone. At the same time, this preserves knowledge in the long term.
Process descriptions are also particularly relevant when processes are complex or there is a legal requirement to set them up. In Chapter 4.4, ISO 9001:2015 requires companies to determine and describe only those processes that are necessary for the QM system. All value creation processes are considered to be QM system-relevant in this context. For each core process, various points must then be questioned and specifically listed. These include:
Required inputs and expected results
Sequence and interaction of processes
Criteria and procedures, including measurements and related performance indicators
Required resources and ensuring their availability
Responsibilities and authorities
Risks and opportunities as well as appropriate measures
Process evaluation
Opportunities for process improvement
In addition, there are several other reasons why process descriptions are necessary. We look at them from three angles.
1. Benefits of process descriptions concerning the flow of manufacturing activities:
Creating uniformity and ensuring a smooth and consistent workflow
Regulation of the task, work method, temporal and spatial work process, the use of suitable work equipment and the processing of the work objects.
Process optimization and standardization of processes
Avoid inefficient work and increase productivity
Reduction of the error rate and cost reduction
Occupational safety and ensuring a consistently high level of quality
2. Benefits of process descriptions for employees:
Simplified and homogeneous training of new employees
Knowledge transfer instead of dependence on the process knowledge of a few
Reduction of complexity in multi-layered work processes
Increase employee retention and satisfaction
3. Benefits of process descriptions for the company:
Faster ramp-ups
Future-proof production
Resilience to skills shortages, employee turnover and external shocks
The individual aspects make it clear: The documentation of a company's most important production processes is an integral component of its value creation.

How is a good process description structured and how is it created?
In general, a good process description contains the following information:
Process designation
Process objective with brief description of the purpose and benefits
Scope of application
Listing of inputs and results of the process
Presentation of the process (for example as a flow chart)
Process owner
Process key figures used to monitor and supervise the process
Specifications such as references to associated process and work instructions
Graphically it could look like this:
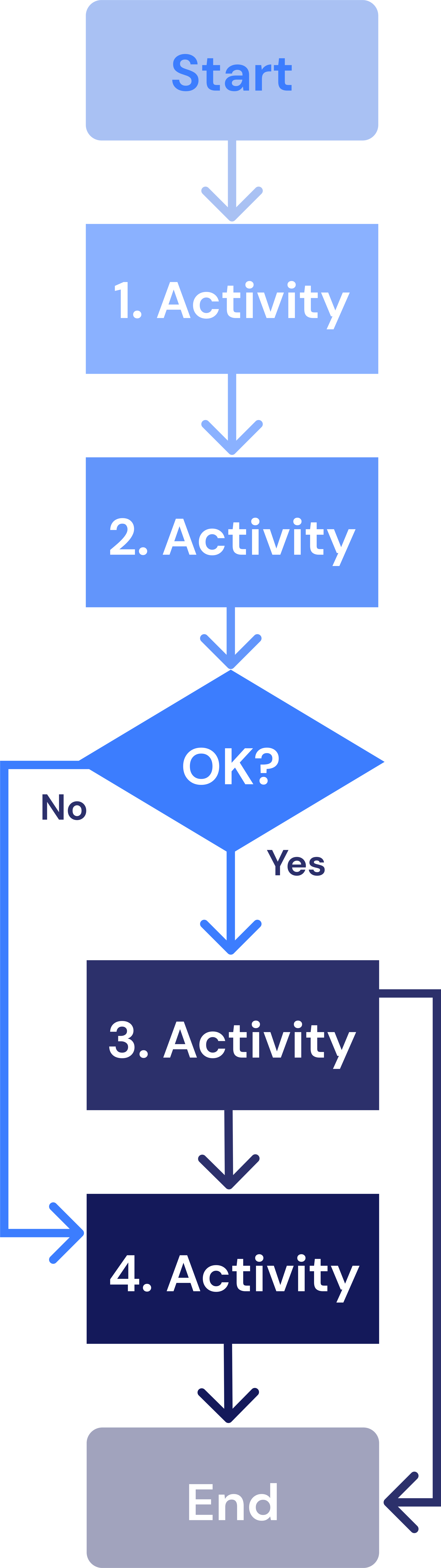
Creation phases of a process description
A process description is usually roughly divided into 3 creation phases: the planning, the actual creation and the use in the operative day-to-day business.
Phase 1: Planning a good process description
Before you invest a lot of time in creating a process description, you should ask yourself the following 3 questions in phase 1 - planning:
Who is the process description aimed at? If it is for a non-specialist employee, it will be prepared differently than for an expert.
How complex is the process? The rule of thumb here is to consider the processes in the sequence in which they flow through the company and subdivide the processes along this chain in a meaningful way.
Are there already existing process descriptions for the corresponding workflow? How up-to-date are they? Before writing a process description, examine existing processes by forming teams from the relevant departments - QM officers, industrial engineering and direct process owners. These teams should critically examine the current processes with regard to optimization potential. In this way, you avoid inefficiencies and duplication of work.
Phase 2: The creation of a good process description
Phase 2 highlights the actual creation and first of all explains the purpose of the process description in the introduction.
If you then respect the following tips when creating a process description, nothing will stand in the way of efficient implementation on the part of the employees:
Formulate clearly and understandably according to the principle "As many details as necessary, as few as possible."
Set up process descriptions in form and content according to a uniform pattern.
Use bullet points instead of running text.
Use short sentences.
Formulate actively.
Document regular cases and not special cases.
Clearly separate operations from process steps.
Arrange process steps linearly according to the chronological order of the steps.
Keep process steps to under 20 to avoid overwhelm.
Use interactive elements such as graphics and videos for better comprehension and easier learning.
Phase 3: Deployment and validation of the process description
By evaluating the key figures productivity, process duration and scrap production in the validation phase, you ensure that the process description bears fruit in the work application.
An additional tip for even greater efficiency: set up a feedback process for your employees. This will not only help you to check the status quo, but also to continuously optimize process descriptions in the long term.
The diagram provides a clear summary of the individual phases.
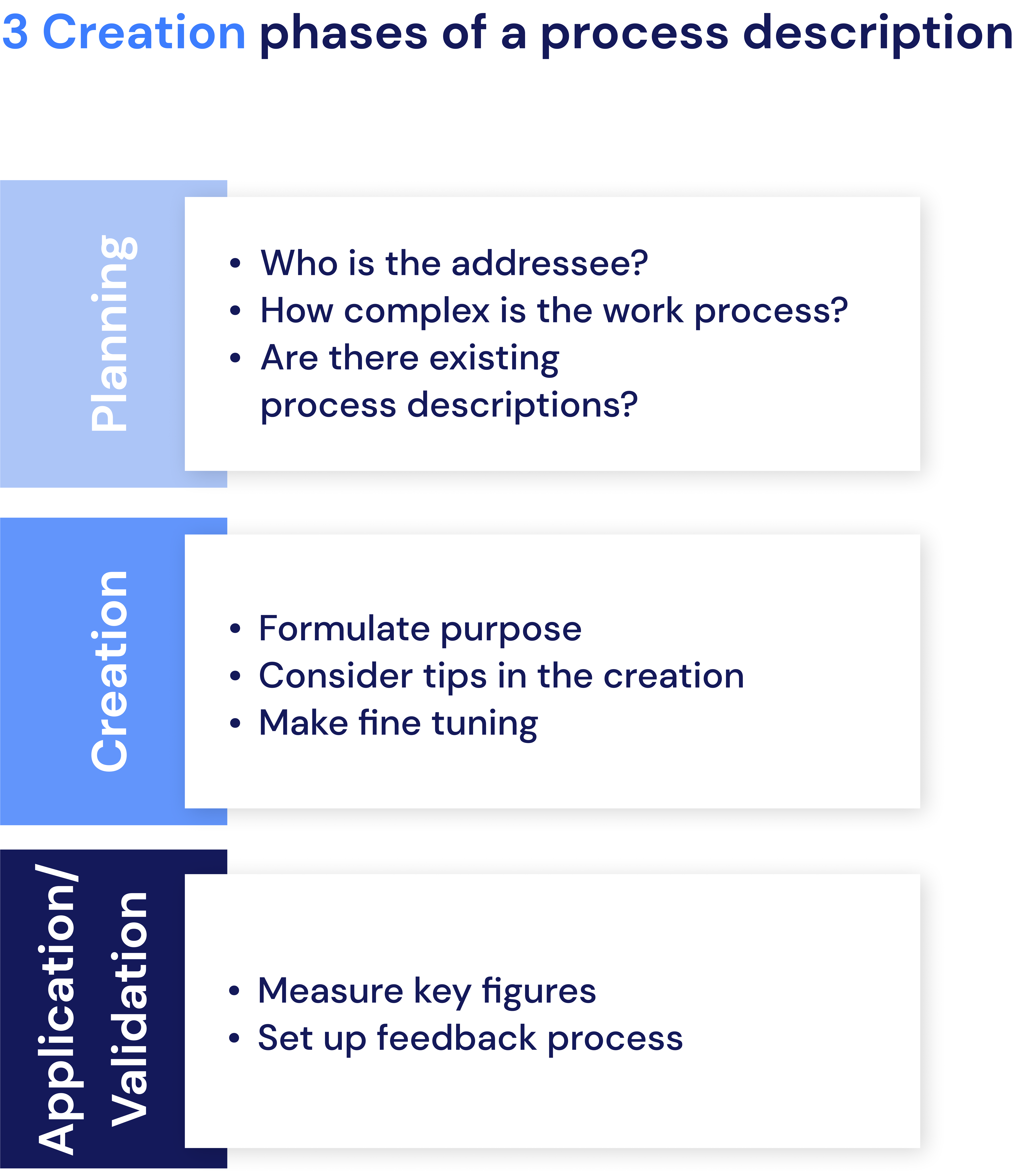
Difficulties of paper-based process descriptions
Paper-based process descriptions run the risk of being forgotten after a certain time in some QM manual. Their full potential then remains unused. And even if paper-based process descriptions are used in the company, they have a lot of disadvantages compared to digital ones.
You will certainly find yourself in at least one of these disadvantages:
Very text-heavy, difficult to understand process descriptions due to lack of explanatory images and videos
High formatting effort
High effort due to media breaks: from digital (Word, Excel, ERP, etc.) to paper and vice versa
High manual effort in compiling variant-specific process descriptions
High effort with multilingualism
Little overview of current order progress
Increased risk of errors due to different versions of the process description (e.g. depending on language, location and product variant → "version chaos")
Little transparency about the detailed progress of activities
The relief that mobile apps, wearables and the like bring to our everyday lives does not therefore extend consistently to the working world of manufacturing companies.
What is the difference between a process description and a work instruction?
There is a lot of overlap between a work instruction and a process description: both record work procedures and processes that are repeated regularly with the aim of ensuring efficiency and safeguarding knowledge in the long term. The difference, however, is that work instructions describe very specific work or work steps in detailed form, while process descriptions tend to describe more complex processes that often have cross-departmental relevance and are usually used in quality assurance. Consequently, the process description is freer in form and content and can also be used to document general processes or best practices in a company.
This means in other words: If you want to guide your employees through individual work steps in a structured and very detailed manner, the work instruction is more suitable as an instrument. The best way here is the digital work instruction, because it has invaluable advantages over the paper-based one.
7+1 advantages of digital documentation with Operations1
Compared to a paper-based work instruction, a digital one has many advantages:
Easy creation of work instructions via drag & drop and predefined function modules
Multilingual work instructions that intuitively guide employees through individual work steps with image and video support
Increased comprehensibility through text, markings, pictograms in images, integrated checkpoints, transparency on manufacturing progress, efficiency and transparency
Automatic creation of variant-specific work instructions through connection to ERP system
Global organization and standardization of process knowledge via structure classes and modular structure of work instructions
Problems can be reported by employees directly in the work step via task function and solved collaboratively via live chat
Overview of work progress can be viewed in real time
Creation of a central and at the same time flexible point of process truth of all employee-led processes
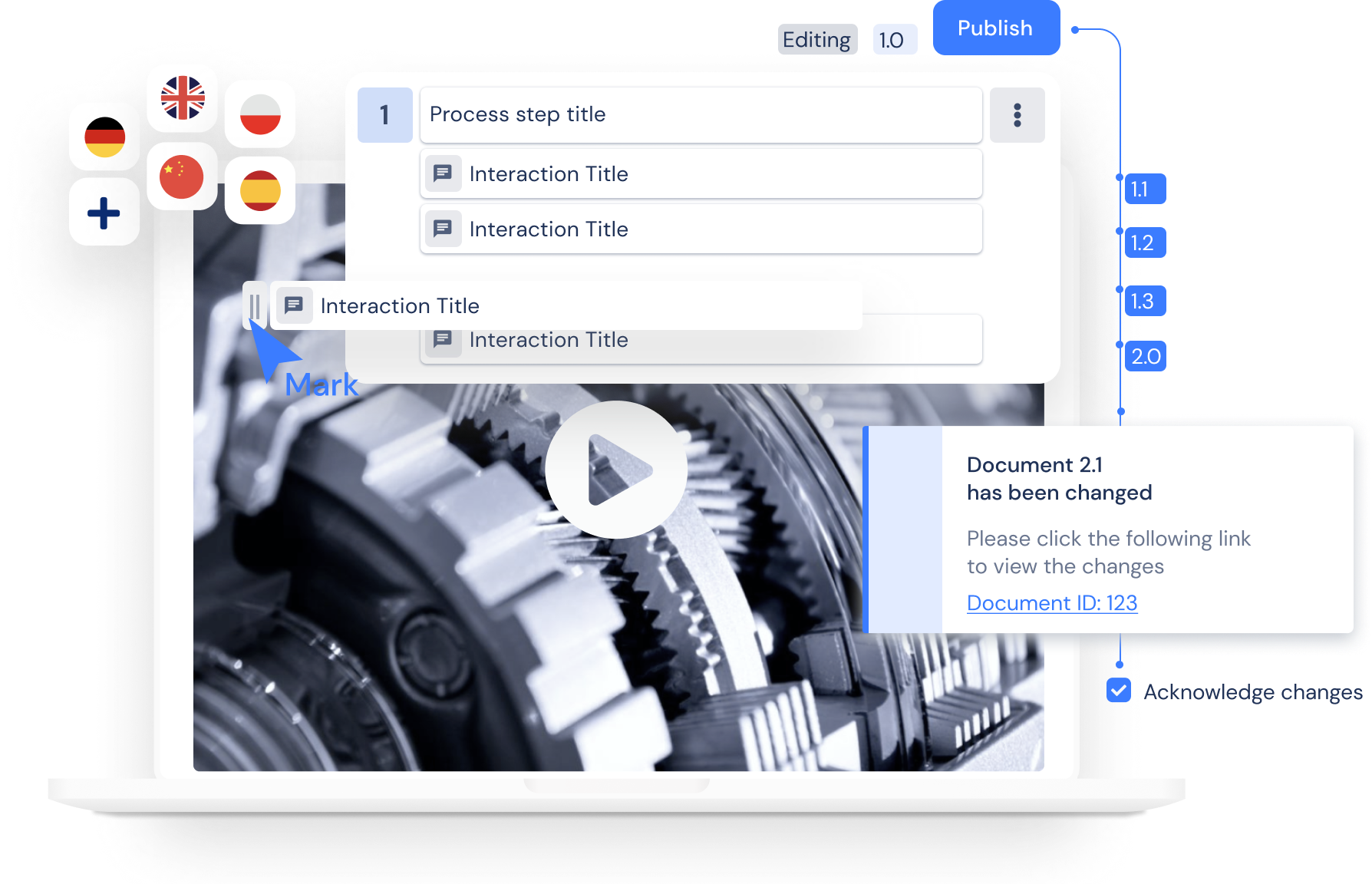
The Operations1 software solution offers your company the following added value:
Avoidance of media discontinuities through digital linking of systems (ERP-Operations1-ERP)
Effort reduction through simple, digital updating and versioning of work instructions
Global standardization of work instructions for sites/plants
Faster training of new employees and reduction of errors
Sustainable knowledge retention
Higher productivity for problems in work steps through collaborative solution approach
The explanations show: Process descriptions are important, for process optimization, knowledge transfer and resilience of an operation. By introducing a Connected Worker Platform, process descriptions become interactive and intuitive, so that they come to life on the shopfloor instead of being forgotten unused in QM manuals.
Conclusion: Digital documentation builds the bridge to connected working.
Want to learn more or even test Operations1's Connected Worker Platform?
Please fill out the contact form with your thoughts and goals. We will get back to you immediately.
Editha Bertsch
Editha is an experienced project management expert for manufacturing companies. With a clear understanding of the specific challenges of the industry, she is passionate about developing innovative solutions.