Worum es geht
In diesem Blogartikel erläutern wir den Mehrwert einer digitalen autonomen Instandhaltung auf dem Shopfloor.
Folgende Fragen werden im Blogbeitrag behandelt:
- Was ist autonome Instandhaltung?
- Welche Vorteile hat sie?
- Wie wird sie eingeführt?
- 9 Vorteile einer digitalen autonomen Instandhaltung mit Operations1
Was ist autonome Instandhaltung?
Die autonome Instandhaltung, die auch als „selbstständige Instandhaltung“ bezeichnet wird, verfolgt das Ziel, dass Maschinenbediener in der Lage sind, die Anlage selbstständig zu betreiben. Hierzu werden sie derart geschult, dass sie Reinigungs-, Inspektions- und Wartungsarbeiten unabhängig vom Instandhalter durchführen können. Die dadurch erfolgte Auflösung der strengen Aufgabenteilung zwischen Werker und Instandhaltung führt produktionsseitig zu einer Sensibilisierung in der Fehlerfrüherkennung und entlastet zugleich die Instandhaltungsmitarbeiter, die ihren Fokus stattdessen auf komplexe Instandsetzungsmaßnahmen und deren Optimierungsmöglichkeiten lenken können.
Dadurch wird ein Fundament geschaffen, das auf 3 Prinzipien gründet:
Es wird ein positives Verhältnis zwischen dem Werker und seiner Maschine geschaffen.
Der Produktionsmitarbeiter soll sich für sein Werkzeug selbst verantwortlich fühlen können.
Die Leistung des Mitarbeiters kann nur so gut sein, wie der Zustand seiner Maschine.

Das Konzept der autonomen Instandhaltung hat seinen Ursprung in Japan und ist Teil der Total Productive Maintenance (TPM). Hiermit wir ein Konzept in der Instandhaltung bezeichnet, das darauf abzielt, die Anlageneffektivität und die Lebensdauer der Anlagen zu steigern und so ein möglichst störungsfreies Produktionssystem zu realisieren. Durch eine wirkungsoptimierte, kostenoptimale Instandhaltung sollen Verluste und Verschwendung eliminiert werden, so dass „Null-Defekte“, „Null-Ausfälle“, „Null-Unfälle“ und „100 Prozent Qualität“ sichergestellt werden.
Die autonome Instandhaltung bildet die zweite von insgesamt acht Säulen von TPM, wie die Grafik zeigt.
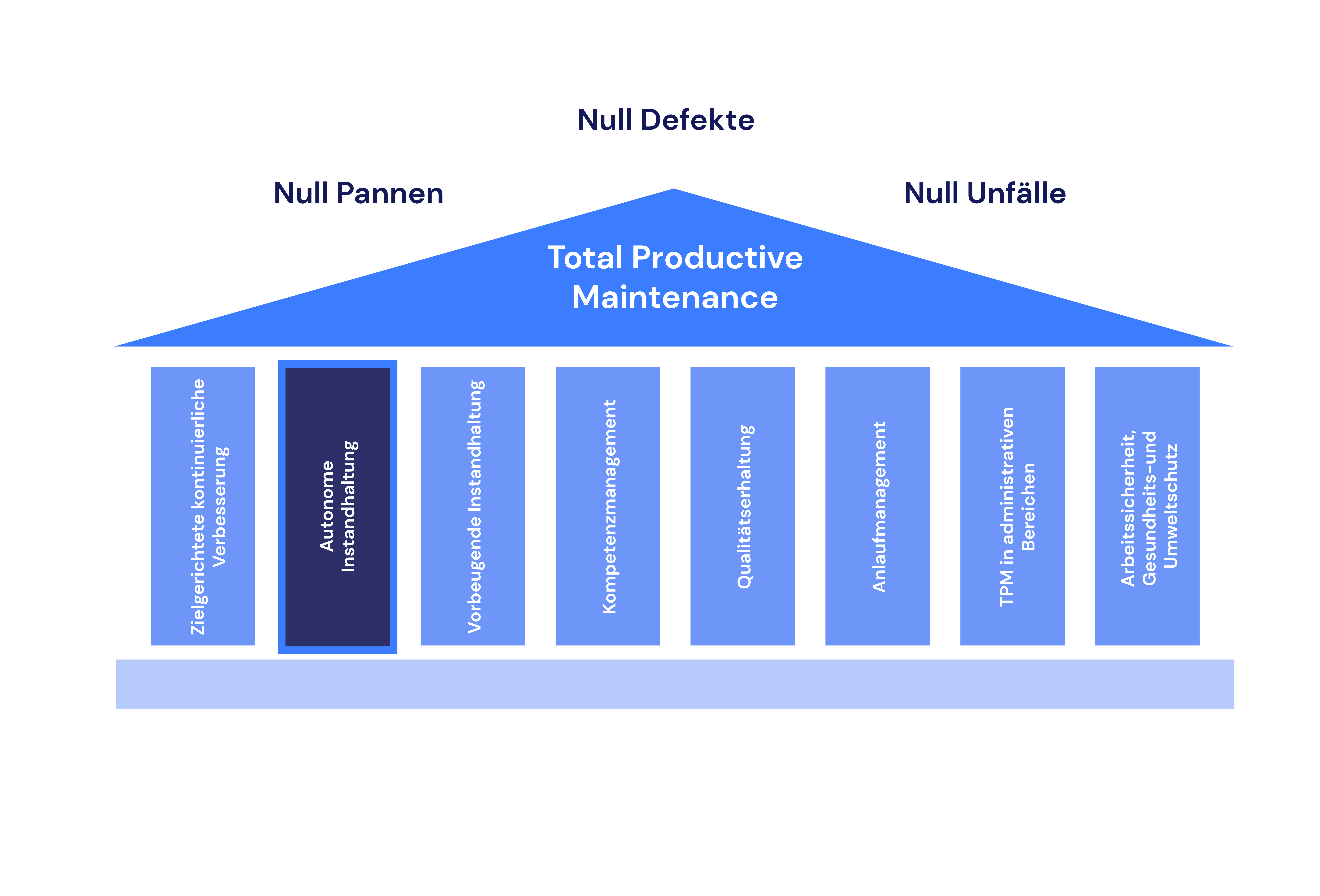
Detaillierte Informationen zum Konzept von TPM, ihren Ursprüngen, den Vor- und Nachteilen auf dem Shopfloor, der Umsetzung sowie dem Mehrwert von digitaler TPM gibt unser Blogbeitrag.
Welche Vorteile hat autonome Instandhaltung?
Wenn die Einstellung „Jeder sorgt für seine Maschine“ von den Produktionsmitarbeitern verinnerlicht und im Alltag gelebt wird, entsteht ein Paradigmenwechsel mit zahlreichen Vorteilen für alle beteiligten Stakeholder. Diese 9 Vorteile sind das Resultat von autonomer Instandhaltung:
Steigerung der Produktivität und Qualität Das Konzept „Mehr Sorgfalt durch Eigenverantwortung“ führt zu weniger Rückkoppelungsschleifen und erhöht so die Leistungsfähigkeit von Mensch und Maschine.
Reduktion von Kosten Während externe Wartungstechniker häufig von außen anreisen müssen, sind die Bediener ohnehin stets in der Nähe ihrer Maschine.
Geringe Downtime Wenn lange Reaktionszeiten bei der Wartung und eine hohe Abhängigkeit von Dienstleistern entfallen, reduziert sich auch die Maschinenausfallzeit. Unser Kunde Hirschvogel konnte die Downtime um 60% minimieren.
Höhere Resilienz In Zeiten von Fachkräftemangel erweist sich die höhere Kompetenz von Werkern als besonders zukunftsfähig für das Unternehmen – auch und gerade im Hinblick auf den Faktor Wettbewerbsfähigkeit.
Höhere Mitarbeiterbindung Wird den Werkern mehr Kompetenz für ihre Maschine zugetraut und übertragen, bleiben sie dem Unternehmen länger erhalten, weil sie sich mehr wertgeschätzt und „ihrer“ Maschine verbunden fühlen.
Entlastung des Wartungspersonals Instandhaltungsmitarbeiter können da eingesetzt werden, wo sie wirklich gebraucht werden bzw. ihren Fokus auf komplexere Arbeiten richten.
Fehlerfrüherkennung Dadurch kann einer dauerhaften Schädigung der Anlage vorgebeugt werden.
Erhöhung der Arbeitssicherheit Das Verletzungsrisiko für die Mitarbeiter sinkt, wenn Maschinen regelmäßiger gewartet werden und es seltener zu Fehlfunktionen oder Problemen kommt.
Steigerung der Gesamtanlageneffektivität (OEE) Die Grundfrage lautet: Wie produktiv war eine Anlage real im Verhältnis zur Betriebszeit? Die Gesamtanlageneffektivität (OEE) beschreibt die Leistungsfähigkeit einer Anlage und setzt folgende 3 Faktoren in ein Verhältnis: 1) Maschinenverfügbarkeit (= Verhältnis geplante Produktionszeit zu realer Laufzeit), 2) Maschinenleistung (= Output) und 3) Qualitätsgrad (= Anzahl nutzbare Teile zu Gesamtzahl produzierter Teile). Das Schaubild illustriert diesen Zusammenhang.
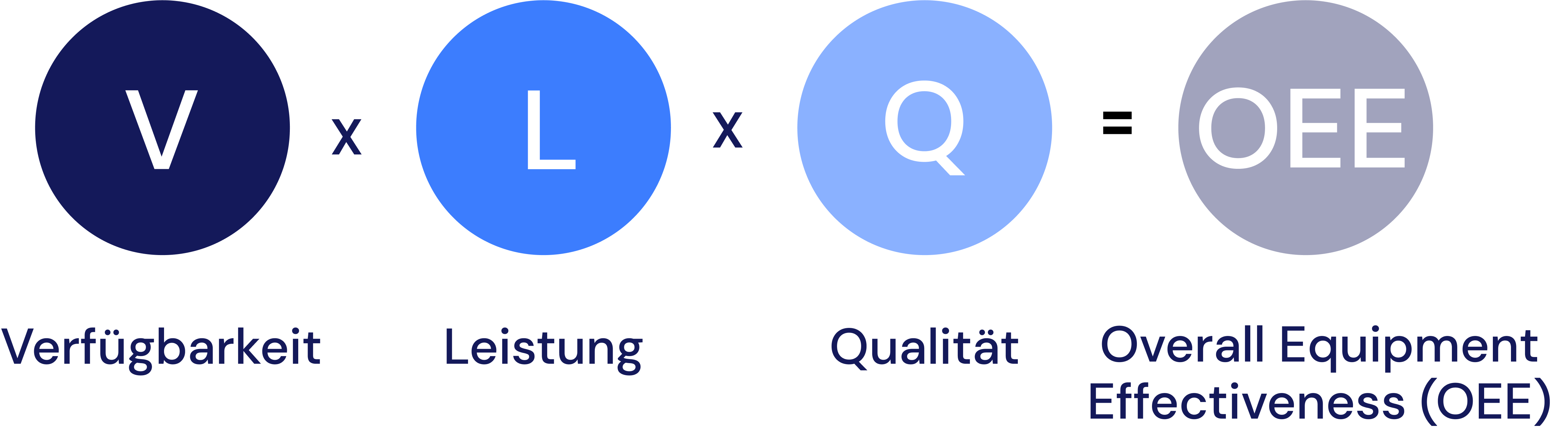
Die vielen Vorteile verdeutlichen: Der Einsatz von autonomer Instandhaltung steigert die Effizienz und Sicherheit eines Unternehmens beträchtlich.
Wie wird autonome Instandhaltung eingeführt?
Wie wird autonome Instandhaltung eingeführt?
Autonome Instandhaltung lässt sich mithilfe eines 7-Stufen-Ansatzes strukturiert einführen:
Stufe 1: Gemeinsame Grundreinigung & Erstinspektion
In Stufe 1 wird mit den Produktionsmitarbeitern eine gemeinsame Grundinspektion der gesamten Anlage durchgeführt, um die Maschine auf Mängel zu überprüfen. Letztere werden kenntlich gemacht und anschließend behoben. Außerdem werden gemeinsam neue Reinigungs- und Wartungspläne erstellt und die Umsetzung sichergestellt.
Stufe 2: Herstellen optimaler Bedingungen für effiziente Reinigungsarbeiten
Dies gelingt, indem Verschmutzungsquellen gemeinsam identifiziert und behoben werden. Daneben werden Fehlerquellen und schwer zugängliche Bereiche eliminiert. Auf diese Weise lassen sich Reinigungs-, Inspektions und Wartungszeiten reduzieren.
Stufe 3: Festlegen von Standards für die Reinigung und Schmierung
In dieser Stufe werden verbesserte Standards für die Reinigung, Inspektion und Wartung in Form von Checklisten definiert. Unterstützt wird das Ganze durch die Einrichtung von funktionsübergreifenden Verbesserungsteams.
Stufe 4: Entwicklung von Trainingsmodulen für die autonome Instandhaltung
In Stufe 4 wird den Werkern in Trainingsmodulen das nötige Wissen zur selbstständigen Übernahme von Instandhaltungsaufgaben vermittelt.
Stufe 5: Erste autonome Anlagenüberprüfungen
In dieser Stufe sind die Maschinenbediener mit ihren neuen Aufgaben ausreichend vertraut und können die Reinigung, Inspektion und Wartung der Anlagen nach angepassten Plänen eigenständig durchführen. Wichtig ist in dieser Phase, standardisierte Prüflisten und Instandhaltungspläne zu erarbeiten, die die Wartungsintervalle und Verantwortlichkeiten festlegen. Die erarbeiteten Standards sollten zudem stetig hinterfragt und optimiert werden.
Stufe 6: Standardisierung in der Prozesslandschaft
In dieser Stufe können die Werker die Anlagen selbstständig betreiben und Reinigungs-, Inspektions- und Wartungsaufgaben autonom durchführen. Ebenso können sie einfache Reparaturen eigenständig durchführen. Ziel dieser Stufe ist es außerdem, den gesamten Arbeitsplatz im Hinblick auf Sauberkeit, Ordnung und möglichst geringe Verluste zu optimieren.
Stufe 7: Selbstständige Anwendung der autonomen Instandhaltung
In Stufe 7 ist die autonome Instandhaltung vollumfassend eingeführt. Ziel ist die kontinuierliche Weiterentwicklung der bestehenden Abläufe. Dies gelingt, indem die Verlustzeiten dokumentiert und anschließend analysiert werden.
Wichtig ist, das Erreichen jeder einzelnen Stufe durch interne Audits zu überprüfen und sicherzustellen. Nur so kann autonome Instandhaltung tragfähig eingesetzt und gelebt werden. Die Grafik fasst die einzelnen Stufen nochmals übersichtlich zusammen.
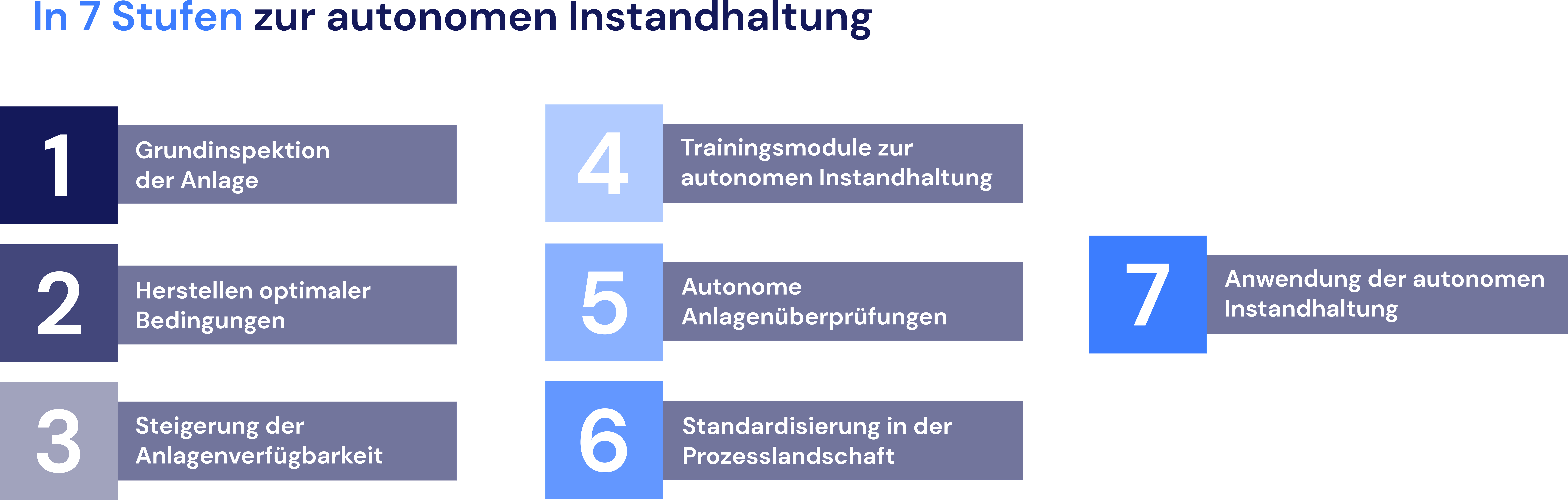
Autonome Instandhaltung – 9 Vorteile einer digitalen Umsetzung mit Operations1
Wir haben gesehen, wie es gelingt, die Effizienz, Sicherheit und Zuverlässigkeit eines Unternehmens mittels autonomer Instandhaltung zu steigern. Mit einer digitalen Umsetzung von autonomer Instandhaltung können Sie Ihre Operations auf ein neues Exzellenz-Level heben.
Diese 9 Vorteile verschafft Ihnen eine digitale Umsetzung autonomer Instandhaltung mit Operations1:
Einfache und intuitive, Text- und Video-basierte Informationsbereitstellung – papierlos, in Echtzeit und mehrsprachig
Einfaches und flexibles User Interface
Bei Bedarf Anbindung von Operations1 mit Ihren Bestandssystemen wie CMMS, ERP und MES
Schnelle und kollaborative Problemlösung via Task Management und Live-Chat
Unkomplizierte Dokumentation von nicht behebbaren Mängeln mittels Video- und Bildaufnahmen für den Instandhalter
Einfache Erstellung von Wartungsplänen und unkomplizierte Verknüpfung mit digitalen Arbeitsanweisungen und Checklisten
Abbildung von Wartungsintervallen mithilfe einer Feinplanung, bei denen Tätigkeiten festgelegt und Mitarbeitern zugewiesen werden
Flexible Umsetzung von Live-Monitoring durch Überwachung des Tätigkeitsfortschritts im Dashboard
Automatische Erstellbarkeit und Transparenz in der Auswertung von digitalen Wartungsberichten
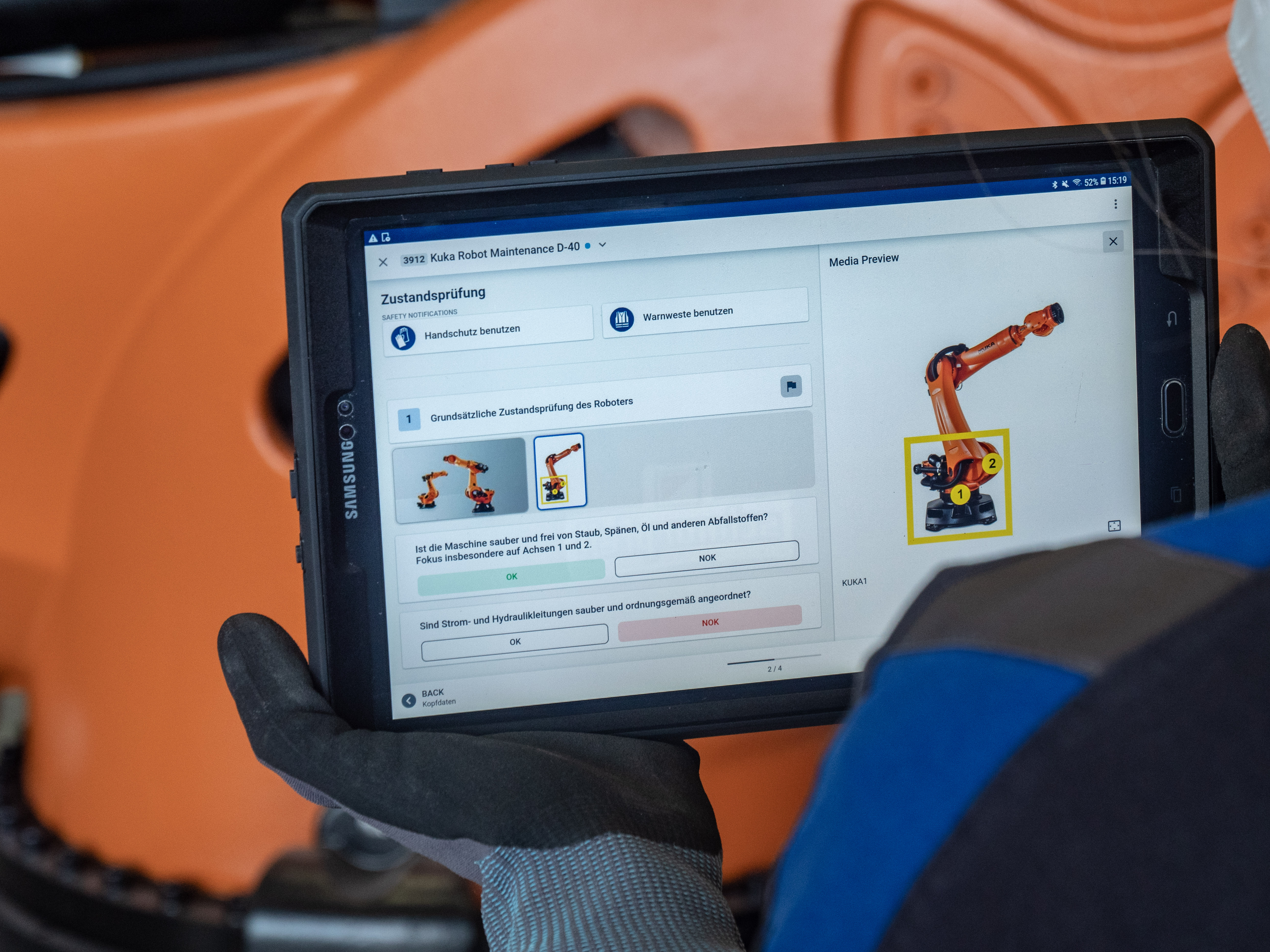
Es wird deutlich: Autonome Instandhaltung ist der Schlüssel zu einer Erhöhung der Produktivität, Kostenreduktion und mehr Resilienz. Mithilfe einer digitalen Umsetzung stellen Sie Prozesswissen in Echtzeit bereit und steigern langfristig Ihre Wettbewerbsfähigkeit.
Fazit: Autonome Instandhaltung bildet die Basis für Operative Exzellenz auf dem Shopfloor.
Sie möchten arbeiten wie Hirschvogel, Oetiker und viele weitere Marktführer?
Dann füllen Sie gerne das Kontaktformular mit Ihren Gedanken und Zielen aus. Wir melden uns umgehend bei Ihnen zurück und tauschen uns mit Ihnen über einen möglichen digitalen Instandhaltungsansatz aus.
Markus Glotzbach
Während seiner beruflichen Laufbahn sammelte Markus tiefe Einblicke bei Unternehmen und Konzernen unterschiedlicher Industrien und kennt die Digitalisierungshürden und Probleme auf dem Shopfloor. Vor seinem Wechsel zu Operations1 studierte er International Management (MA) und war im Cloud Computing- sowie im SaaS-Telematik-Bereich tätig.