What it's about
In this blog post, we would like to highlight the five basic principles of lean production in the age of digitalization. How do intuitive worker assistance systems help to comply with the principles and what are the benefits?
What does Lean Production mean?
Lean production, or lean manufacturing, is a subset of lean management that focuses on minimizing waste while maximizing productivity in manufacturing companies. At its core, the method helps manufacturing companies optimize lead times and production processes to respond more quickly to volatile market developments.
The method can be traced back to the successful Toyota production system, which came about as a result of a shortage of raw materials - in other words, as a result of an external shock. The Japanese company managed to be successful thanks to particularly resource-efficient processes and even remained successful during the oil crisis in the 1970s. The methods of lean production have been expanded and adapted several times since then. Thus, it is no longer exclusively about production processes, but also about employee empowerment and a constant focus on customer needs.
Lean management and lean production are therefore management philosophies. They can be broken down into various individual instruments, all of which have the goal of eliminating non-value-adding activities and continuously optimizing processes. The instruments include, for example, continuous process improvement (CIP), gemba walks, 5S audits, and the identification of the seven types of waste (muda).
What are the 5 basic principles of lean production?
Companies striving for lean, agile production should always act according to 5 basic principles:
1. Focus on customer added value (value)
The customer is king - this is especially true for the demanding and price-sensitive customers of manufacturing companies. The focus on concrete customer added value (product quality, pricing) automatically leads to the elimination of non-value-adding activities.
2. Identify value flow (value flow)
The value flow refers to all the work steps that are carried out to create a product. These must first be examined individually for non-value-adding activities. All wasteful, avoidable activities that occur during production must be identified and eliminated. The 7 Muda instrument, for example, can help with this.
3. Flow principle (flow)
The flow principle aims to create an uninterrupted value chain during the production process. All the wheels in the value stream clockwork must mesh smoothly so that no production delays or downtimes occur.
4. Pull principle (pull)
Lean manufacturing replaces the traditional manufacturing approach of producing products based on forecasts with a pull approach. This means that nothing is produced "in stock" until the customer orders it. However, this requires manufacturing companies to be enormously flexible and to have well-functioning, short delivery cycles.
5. Perfection principle (perfection)
Lean production is not a final state, after the successful achievement of which one can lean back. The principle of perfection states that there is always room for improvement. The instrument on which this principle is based is called "Kaizen" - or, in German-speaking countries, Continuous Improvement Process (CIP).
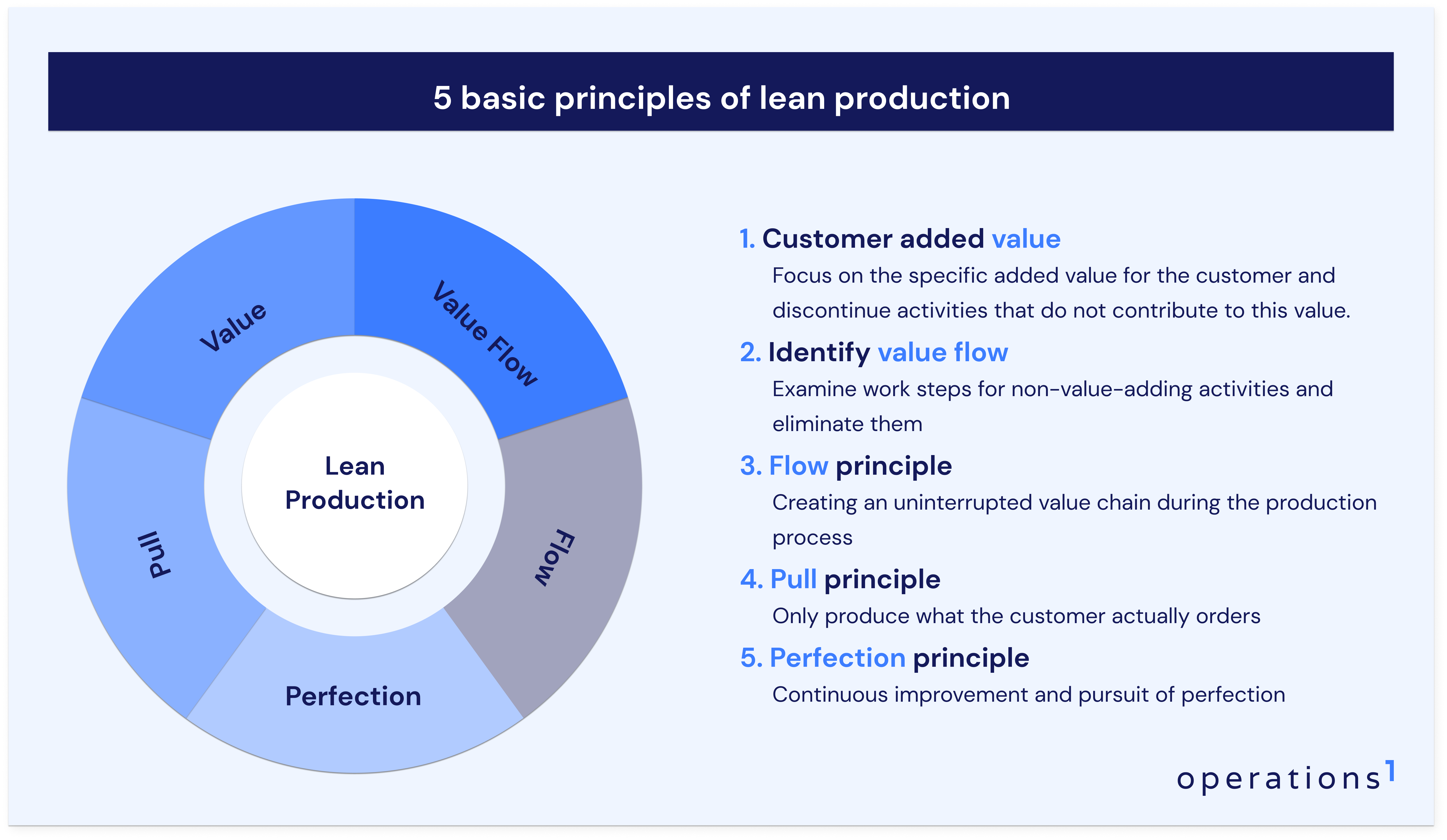
Digitalization and Lean Production
In the 21st century, technologies in particular help to adhere to the 5 basic principles of lean production. MES, ERP and enterprise resource planning systems help with resource planning of value streams, capital, resources and materials. CRM systems help sales identify added customer value. But in one area, manufacturing companies still have some catching up to do: employee-led processes on the shop floor itself.
Worker assistance systems: The most effective way to leverage optimization potential.
In Germany alone, 8 million people are employed in the manufacturing sector. A large proportion of them are "deskless". This group of employees, also known as workers, performs operational manufacturing and assembly activities and is therefore dependent on information exchange, processes and workflows functioning perfectly. The reality, however, is often different.
Despite a mature IT system landscape, production orders, work instructions or test and assembly instructions are passed on to them in paper-based form. The error-prone, sluggish medium of paper-based work instructions and checklists means that the basic principles of lean manufacturing cannot be followed optimally. Outdated and misunderstood instructions lead to errors. If an operational employee discovers the error and tries to obtain the correct information himself, productivity suffers. The flow principle is interrupted. This has a direct impact on the other principles: Dysfunctional value streams, scrap production, rework and customer complaints are the result.
Advantages of digital worker guidance
Intuitive worker assistance systems already exist and provide optimum support for production employees. Step-by-step, assistance software guides operational employees through processes. Information reaches the right hands in the right form, at the right time and in the right place. The information is fed directly from the company's own ERP systems, such as SAP. Product-specific data is pulled directly from the system and made available in a structured and variant-specific manner. Workers can thus concentrate on the essentials without frictions in the value chain.
Other advantages:
Process comprehension: With worker assistance systems, information is provided in multiple languages and visually; images, videos, and graphics make the instructions easy to understand.
Satisfaction: Thanks to the smooth workflow, motivation and satisfaction among operational employees increases. In this way, the shortage of skilled workers can be proactively counteracted. New employees are also trained more quickly.
Transparency: Worker assistance software enables unprecedented transparency in company processes, because valuable process data is fed back to the system
Resilience: Numerous CIP measures can be derived from the new data pool, companies can react more flexibly and agilely to changes and external shocks.
Conclusion
Manufacturing companies are already working with numerous lean methods to make their operations more resilient against the backdrop of volatile market conditions. Adherence to the five basic principles of lean production is supported in part by a mature IT infrastructure. Only in the area of employee-led processes is there still a need to catch up. Paper-based work harbors efficiency and quality risks that can be countered by using a worker assistance system. In particular, the flow principle, which aims for an uninterrupted value flow, can be optimally adhered to as a result. With digital worker assistance systems, production companies can unleash enormous optimization forces in their lean production efforts.
Learn more about the advantages of digital worker assistance systems
Operations1 counteracts non-value-added processes and waste in the production environment. The simple, intuitive worker assistance software supports production employees in their daily work. Read how digital work instructions can make your production leaner, more efficient and more effective.
Benjamin Brockmann
Benjamin Brockmann (M. Sc., Management & Technology) founded Operations1 in 2017 together with Daniel Grobe (also M. Sc., Management & Technology). The founders developed the software solution based on various practical projects, including at the Fraunhofer Institute, and on their experience in industry, auditing and management consulting. Benjamin Brockmann has already worked for companies such as KPMG and Arthur D. Little.