Worum es geht
Wir möchten in diesem Blogbeitrag die fünf Grundprinzipien der Lean Production im Zeitalter der Digitalisierung beleuchten. Wie gelingt die Einhaltung der Prinzipien mithilfe intuitiver Werkerassistenzsysteme und welche Vorteile ergeben sich daraus?
Was bedeutet Lean Production?
Lean Production, oder auch Lean Manufacturing, ist ein Teilbereich des Lean Managements, der sich auf die Minimierung von Verschwendung bei gleichzeitiger Maximierung der Produktivität in Fertigungsunternehmen konzentriert. Lean bedeutet „schlank“. Im Kern hilft die Methode produzierenden Unternehmen dabei, Durchlaufzeiten und Produktionsprozesse zu optimieren und damit schneller auf volatile Marktentwicklungen zu reagieren.
Die Methode ist auf das erfolgreiche Toyota-Produktionssystem, das infolge einer Rohstoffknappheit - also durch einen externen Schock – entstand, zurückzuführen. Dem japanischen Konzern gelang es dank besonders ressourcenschonender Prozesse erfolgreich zu sein und sogar während der Ölkrise in den 70ern erfolgreich zu bleiben. Die Methoden der Lean Production wurden seitdem mehrfach erweitert und angepasst. So geht es nicht mehr ausschließlich um Produktionsprozesse, sondern auch um die Befähigung der Mitarbeiter und den stetigen Blick auf die Kundenbedürfnisse.
Lean Management und Lean Production sind also Management-Philosophien. Sie lassen sich in verschiedene Einzelinstrumente runterbrechen, die alle das Ziel haben, nicht wertschöpfenden Tätigkeiten einzudämmen und Prozesse stetig zu optimieren. Zu den Instrumenten gehören z.B. die kontinuierliche Prozessverbesserung (KVP), Gemba Walks, 5S Audits oder auch die Identifikation der sieben Arten der Verschwendung (Muda).
Was sind die 5 Grundprinzipien der Lean Production?
Unternehmen, die eine schlanke, agile Produktion anstreben, sollten stets nach 5 Grundprinzipen handeln:
1. Kundenmehrwert in den Mittelpunkt stellen (Value)
Der Kunde ist König – das gilt besonders für die anspruchsvollen und preissensiblen Abnehmer von Fertigungsunternehmen. Die Fokussierung auf den konkreten Kundenmehrwert (Produktqualität, Preis) führt automatisch zur Eliminierung nicht wertschöpfender Tätigkeiten.
2. Wertstrom identifizieren (Value Flow)
Der Wertstrom bezeichnet alle Arbeitsschritte, die zur Erstellung eines Produkts durchgeführt werden. Diese müssen zunächst einzeln auf nicht wertschöpfende Aktivitäten untersucht werden. Alle verschwenderischen, vermeidbaren Tätigkeiten, die während der Fertigung entstehen, sind zu identifizieren und zu eliminieren. Dabei hilft z.B. das Instrument der 7 Muda.
3. Fluss-Prinzip (Flow)
Das Fluss-Prinzip zielt darauf ab, eine unterbrechungsfreie Wertschöpfungskette während des Produktionsprozesses zu schaffen. Alle Räder im Wertstrom-Uhrwerk müssen reibungslos ineinandergreifen, damit keine Produktionsverzögerungen oder Ausfallzeiten entstehen.
4. Pull-Prinzip (Pull)
Bei der schlanken Produktion wird der traditionelle Fertigungsansatz, Produkte auf der Grundlage von Prognosen herzustellen, durch einen Pull-Ansatz ersetzt. Dieser besagt, dass nichts „auf Lager“ hergestellt wird, bevor der Kunde bestellt. Das erfordert von Fertigungsunternehmen allerdings enorm hohe Flexibilität und gut funktionierende, kurze Lieferzyklen.
5. Perfektions-Prinzip (Perfection)
Lean Production ist kein finaler Zustand, nach dessen erfolgreicher Erreichung man sich zurücklehnen kann. Das Perfektions-Prinzip besagt, dass immer etwas verbessert werden kann. Das Instrument, dass diesem Prinzip zugrunde liegt, nennt sich „Kaizen“ – oder, im deutschsprachigen Raum, Kontinuierlicher Verbesserungsprozess (KVP).
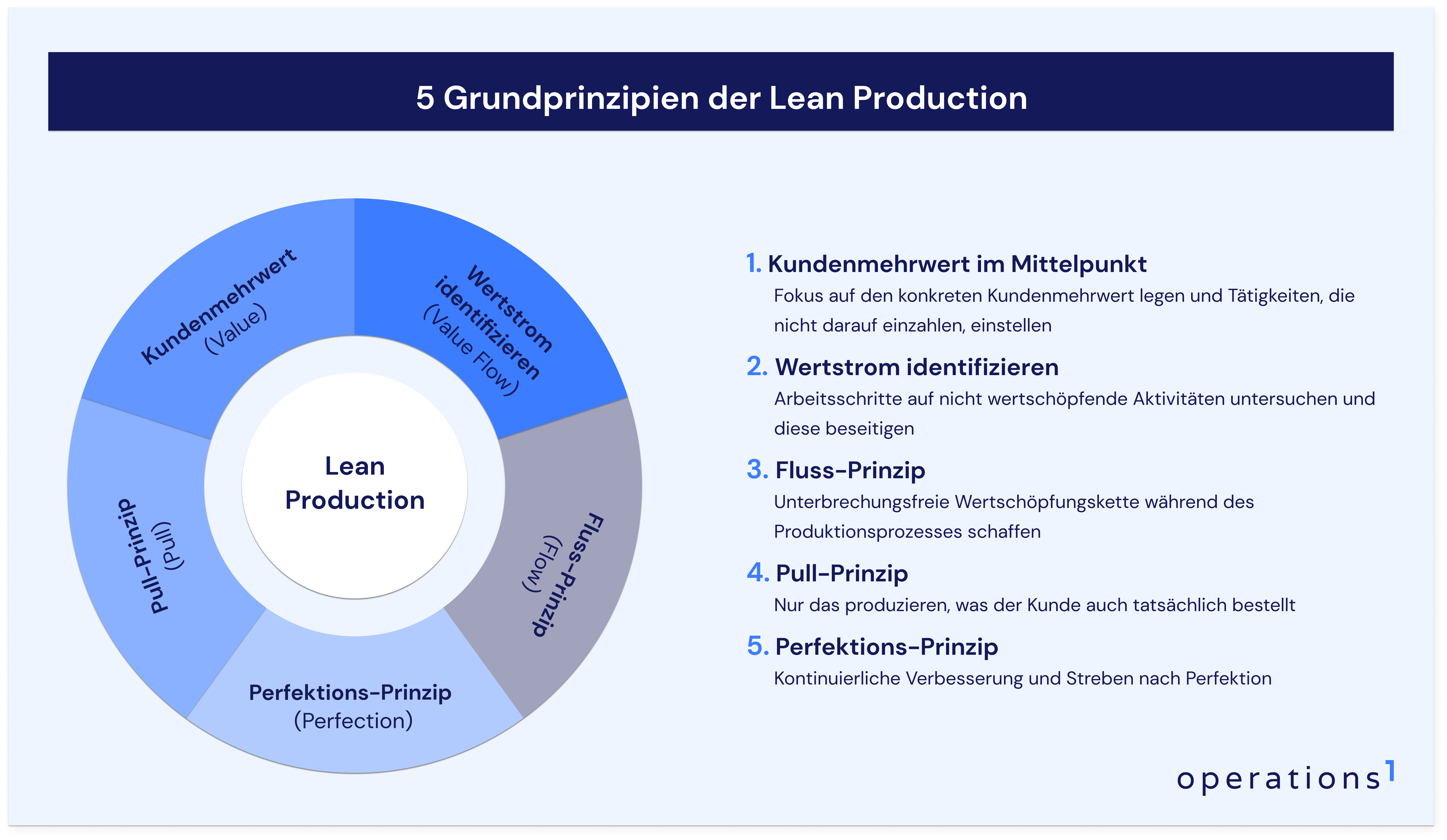
Digitalisierung und Lean Production
Im 21. Jahrhundert helfen vor allem Technologien beim Einhalten der 5 Grundprinzipien der Lean Production. MES-, ERP- und Warenwirtschaftssysteme helfen bei der Ressourcenplanung von Wertströmen, Kapital, Betriebsmitteln und Material. CRM-Systeme unterstützen den Vertrieb bei der Identifikation von Kundenmehrwert. Doch in einem Bereich haben Fertigungsunternehmen noch Nachholbedarf: bei mitarbeitergeführten Prozessen auf dem Shopfloor selbst.
Werkerassistenzsysteme: Die effektivste Art, Optimierungspotentiale zu heben
Allein in Deutschland arbeiten 8 Millionen Erwerbstätige im produzierenden Gewerbe. Ein großer Teil von ihnen ist „schreibtischlos“. Diese Mitarbeitergruppe, auch Werker genannt, übernimmt operative Fertigungs- und Montagetätigkeiten und ist deshalb darauf angewiesen, dass Informationsaustausch, Prozesse und Arbeitsabläufe perfekt funktionieren. Die Realität sieht aber häufig anders aus.
Fertigungsaufträge, Arbeitsanweisungen oder Prüf- und Montageanleitungen werden trotz einer ausgereiften IT-Systemlandschaft papierbasiert an sie übergeben. Das fehleranfällige, träge Medium der papierbasierten Arbeitsanweisungen und Checklisten führt dazu, dass die Grundprinzipien des Lean Manufacturings nicht optimal befolgt werden können. Veraltete und missverständliche Anweisungen führen zu Fehlern. Entdeckt ein operativer Mitarbeiter den Fehler und bemüht sich selbst um die Beschaffung der richtigen Information, leidet die Produktivität. Das Fluss-Prinzip wird unterbrochen. Das hat unmittelbaren Einfluss auf die anderen Prinzipien: Dysfunktionale Wertströme, Ausschussproduktion, Nacharbeit und Kundenreklamationen sind die Folge.
Vorteile digitaler Werkerführung
Dabei existieren bereits Werkerassistenzsysteme, die Fertigungsmitarbeiter optimal unterstützen. Schritt-für-Schritt führt Assistenz-Software operative Mitarbeiter durch Prozesse. Informationen gelangen in der richtigen Form, zur richtigen Zeit und am richtigen Ort in die richtigen Hände. Die Informationen speisen sich direkt aus den unternehmenseigenen ERP-Systemen, wie z.B. aus SAP. Produktspezifische Daten werden direkt aus dem System gezogen und strukturiert und variantenspezifisch zur Verfügung gestellt. Werker können sich somit ohne Reibungsverluste in der Wertschöpfungskette auf das Wesentliche konzentrieren.
Weitere Vorteile:
Prozessverständnis: Die Informationsbereitstellung findet mit Werkerassistenzsystemen mehrsprachig und visuell statt, Bilder, Videos und Grafiken machen die Anleitung leicht verständlich
Zufriedenheit: Dank des reibungslosen Arbeitsablaufs steigt die Motivation und Zufriedenheit bei operativen Mitarbeitern. So kann dem Fachkräfte-Mangel proaktiv entgegengewirkt werden. Neue Mitarbeiter werden zudem schneller eingearbeitet.
Transparenz: Werkerassistenz-Software ermöglicht nie dagewesene Transparenz in Unternehmensabläufe, weil wertvolle Prozessdaten zurückgespielt werden
Resilienz: Aus dem neuen Datenpool können zahlreiche KVP-Maßnahmen abgeleitet werden, Unternehmen können flexibler und agiler auf Veränderungen und externe Schocks reagieren
Fazit
Fertigungsunternehmen arbeiten bereits mit zahlreichen Lean-Methoden, um ihre Operations vor dem Hintergrund volatiler Marktbedingungen resilienter zu machen. Die Einhaltung der fünf Grundprinzipien der Lean Production wird dabei teilweise mit einer ausgereiften IT-Infrastruktur unterstützt. Einzig im Bereich der Werkerführung gibt es noch Nachholbedarf. Papierbasiertes Arbeiten birgt Effizienz- und Qualitätsrisiken, denen mit dem Einsatz eines Werkerassistenzsystems entgegengewirkt werden kann. Insbesondere das Fluss-Prinzip, das auf eine unterbrechungsfreie Wertschöpfungskette abzielt, kann dadurch optimal eingehalten werden. Mit digitalen Werkerassistenzsysteme können Produktionsunternehmen enorme Optimierungskräfte in ihren Lean Production-Bemühungen freisetzen.
Erfahren Sie mehr die Vorteile digitaler Werkerassistenzsysteme
Operations1 wirkt nicht wertschöpfenden Prozessen und Verschwendungen im Produktionsumfeld entgegen. Die einfache, intuitive Werkerführungs-Software unterstützt Produktionsmitarbeiter in ihrer täglichen Arbeit. Lesen Sie, wie Ihre Produktion mithilfe digitaler Arbeitsanweisungen schlanker, effizienter und effektiver wird:
Benjamin Brockmann
Benjamin Brockmann (M. Sc., Management & Technology) gründet 2017 gemeinsam mit Daniel Grobe (ebenfalls M. Sc., Management & Technology) Operations1. Die Software-Lösung entwickeln die Gründer auf Basis diverser Praxisprojekte, u. a. am Fraunhofer Institut, und aufgrund ihrer Erfahrungen in der Industrie, Wirtschaftsprüfung und Unternehmensberatung. Benjamin Brockmann war bereits für Unternehmen wie KPMG und Arthur D. Little tätig.