"Digital processes enable 6-digit savings potential" – Interview with Stefan Philipp from Operations1
Companies that believe that the only chance of digitization lies in finally getting rid of the mountains of documents are thinking too short of the issue. Digital processes are just the tip of the iceberg, as Stefan Philipp knows. The Head of Solutions at Operations1 and his team have already successfully supported many companies on their way toward connected work. In this interview, he provides in-depth insights into how networked working can optimize processes to such an extent that productivity and employee satisfaction increase significantly and six-figure sums can be saved at the same time.
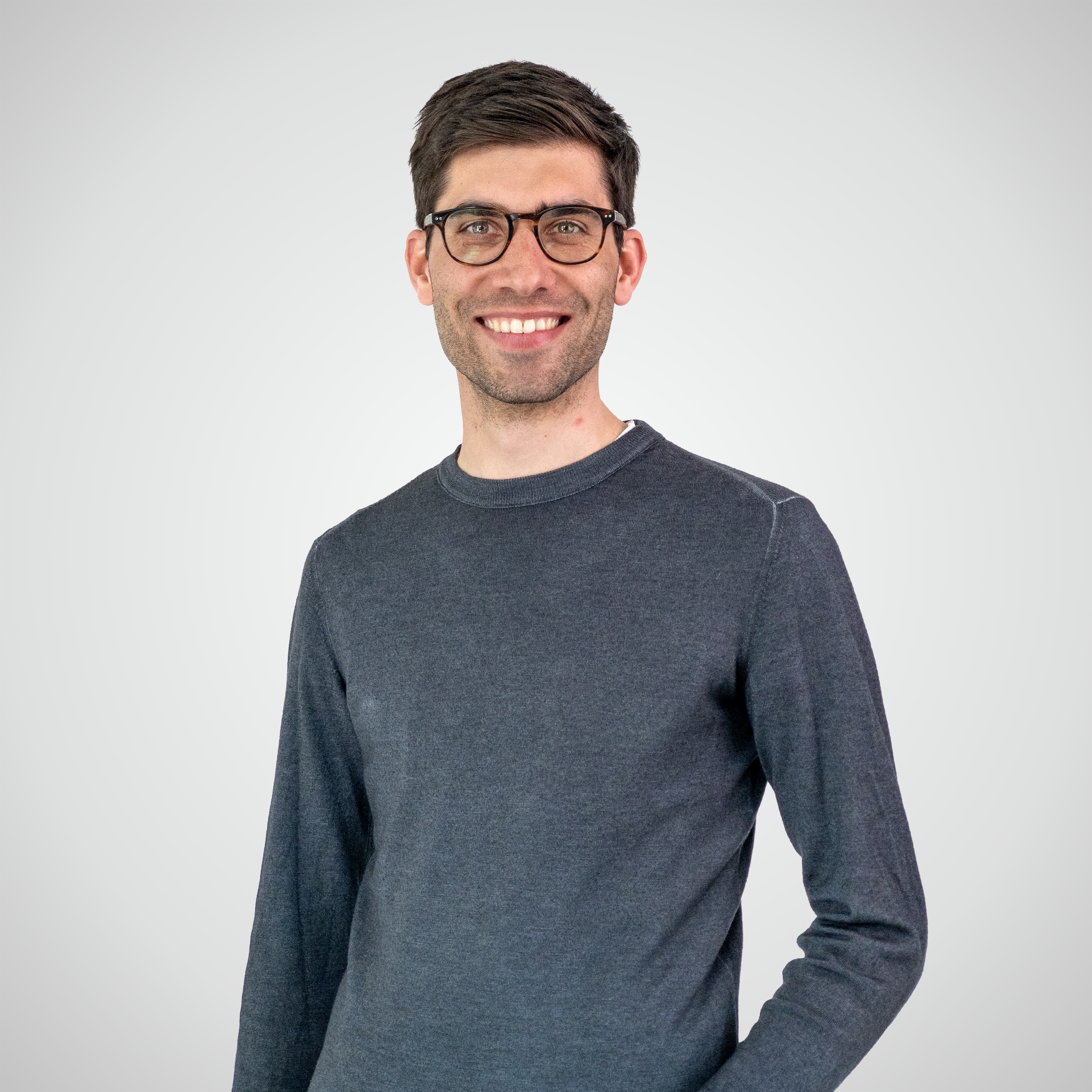
What the interview is about
In his role as Head of Solutions at Operations1, Stefan Philipp and his team support companies in successfully digitizing their processes. In this interview, he explains why companies usually only factor in the obvious costs, such as paper and creation effort, when deciding on the topic of connected work. However, there are far greater challenges that add up to much more.
Read on to find out what these are and why manufacturing industries can expect average savings potential in the six- to seven-figure range through connected work.
Misleading thoughts on paper costs
Stefan, in the connected work study, which will be published exclusively by us at the end of January, we found that 23% of respondents gave a cost estimate in the high 5-digit range per site. As an expert, how do you rate this figure?
In fact, this assessment is very typical. For me, it is clear that for many companies, the topic of paper-based processes is currently still undervalued. In my role as Head of Solutions, I talk to many customers and interested companies from manufacturing industries. In our experience, the costs incurred by paper-based processes are actually much higher than the study participants indicate.
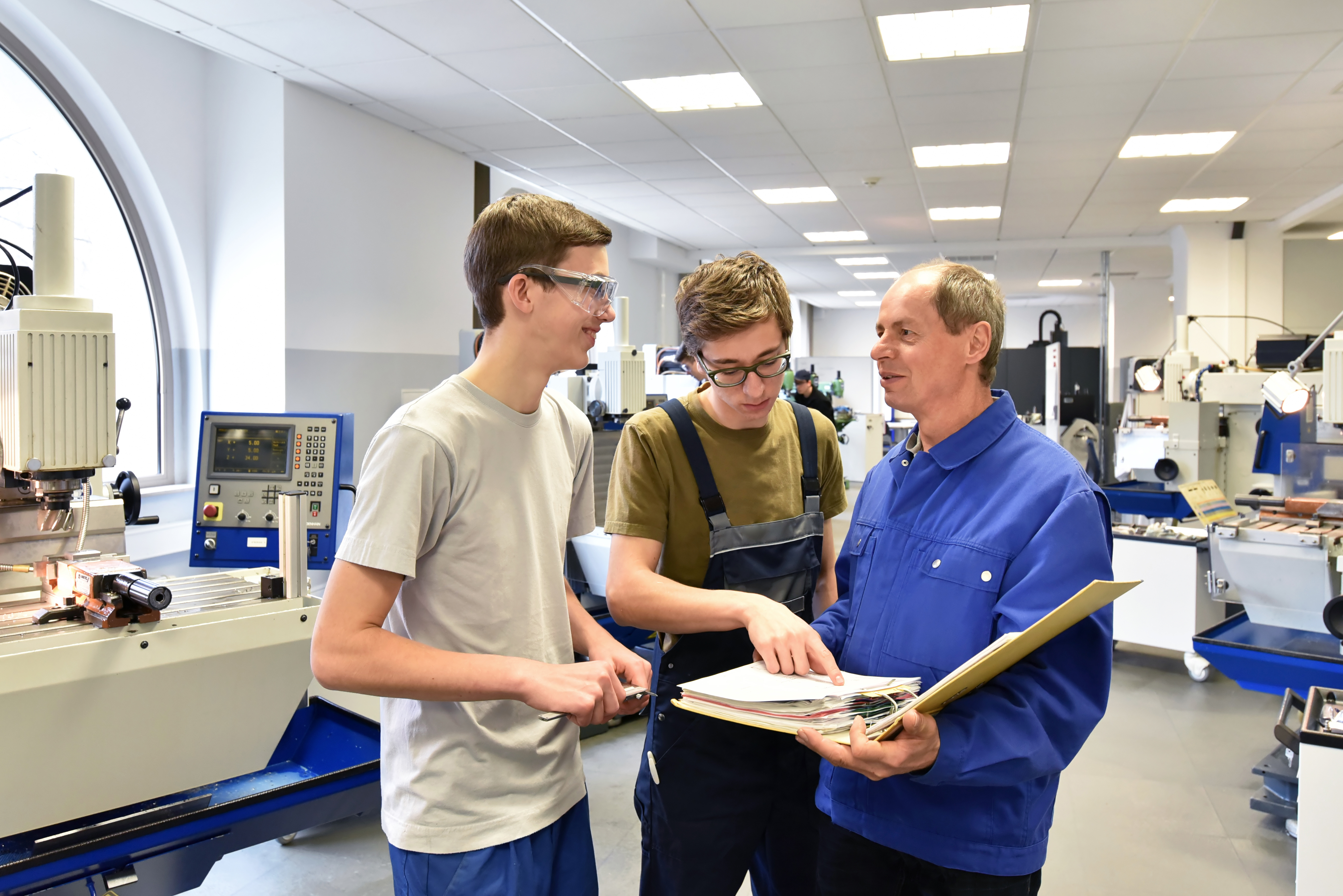
The real cost drivers
Is saving paper costs the main argument for you why companies should digitize their processes?
It is a very important argument in favor of moving in the direction of connected work. However, creation efforts and paper costs are only on the surface and therefore catch the eye directly. In addition, there are less obvious cost drivers hiding below the surface that many companies have yet to see.
Does this explain why many underestimate the actual costs of paper-based processes, as you said?
Right. When companies cite paper costs as the only factor in their digitization efforts, they don't realize that there are far more opportunities in digitization than simply getting rid of mountains of documents. That's because the full extent of the cost is not transparent. In order to determine it, it is important to carry out well-founded analyses and, in case of doubt, to calculate with estimated values if the data situation does not provide any actual figures.
Can you explain this in more detail?
In order to approximate costs, companies need a starting point. For being able to estimate the actual extent of the costs incurred, it is important to carry out a kind of "digital value stream analysis", specifically along the employee-led processes. If you do this, it becomes clear that, abstractly speaking, the costs of paper-based processes are made up of 5 cost items.
What are these?
5 factors
First of all, of course, the direct costs that arise in connection with the use of paper. In addition to the paper itself, these are the costs of toner, ink, etc. Then there are the personnel costs that add up due to activities such as printing, copying and the filing of paper documents. They can be calculated by multiplying the time spent on these tasks by the hourly wage of the employees involved. Another factor is storage costs. This is just as much a capital expense as managing and organizing the paper documents. In addition to the costs of paper usage, personnel and storage, there are also error and opportunity costs.
What is meant by this?
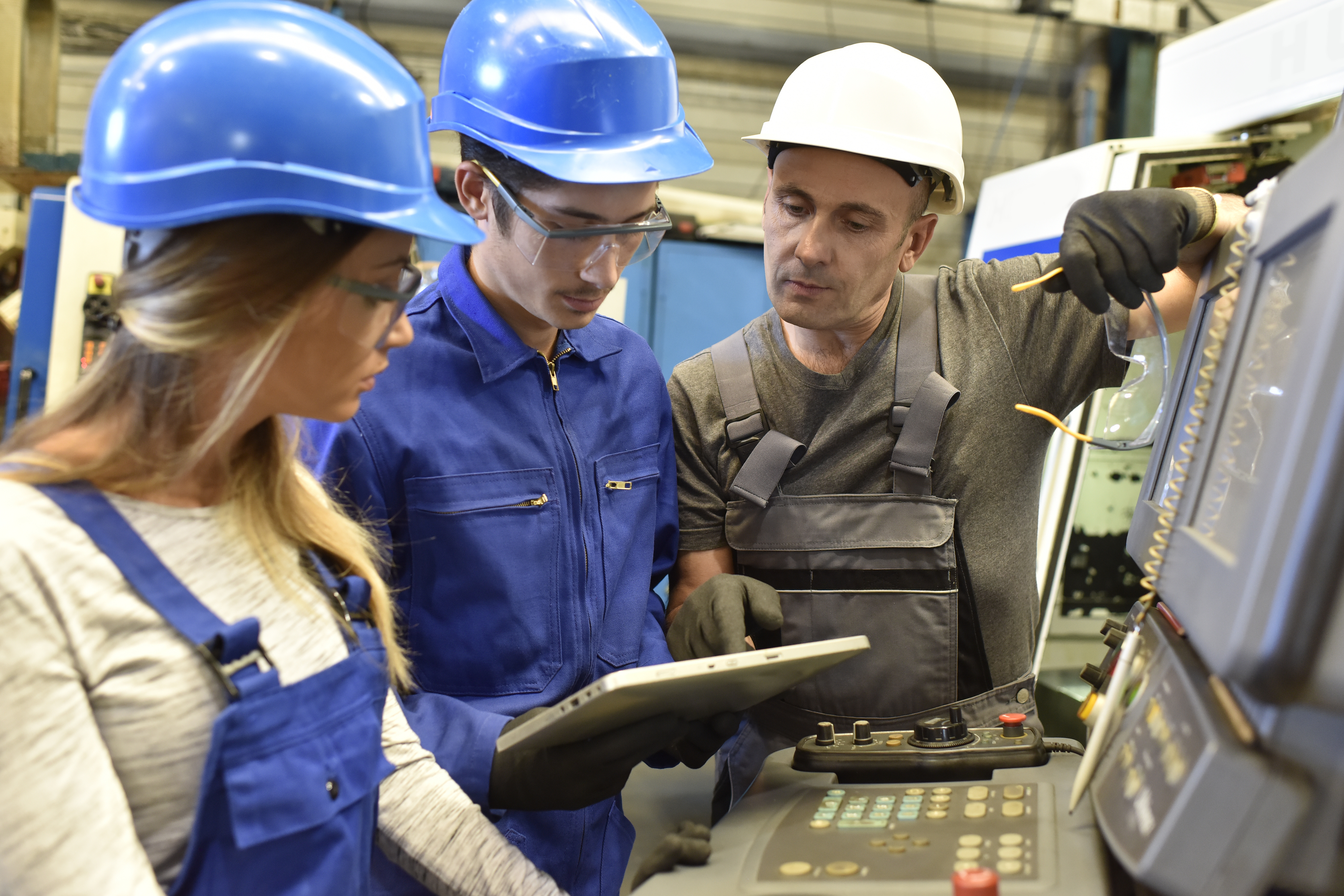
Error and opportunity costs
Error costs occur when, for example, operational processes are carried out incompletely due to misinterpretation of text-heavy documents and then lead to scrap and rework. Finally, opportunity costs are the lost profits, because if I choose paper-based processes, I miss out on the opportunities that digitized processes bring, first and foremost increased efficiency and productivity gains. Adding up all these factors adds up to a tidy sum, and it becomes apparent that there are a great many other insufficiencies besides paper costs that cause unnecessary costs.
Can you give us specific examples of this?
Many non-value-added activities that operational staff are involved with. I'm thinking specifically of such things as media breaks that occur when employees create and maintain checklists and inspection records, for example in commissioning processes. In many companies, this is still done in Word and Excel documents. Especially when documents are to be available in multiple languages and in a standardized form across all plants, and when they have to be updated and versioned in the event of changes, this results in a handling effort that should not be underestimated. After the commissioning documentation has been completed, the paper documents are then scanned again and stored in SAP - often hundreds of pages. If there are queries, the employee has to conduct a manual search in the physical document, which is time-consuming and error-prone and results in increased search efforts. Particularly against the backdrop of an increasing shortage of skilled workers, it is important to free production employees from such inefficient tasks. This not only increases their productivity, but also their personal well-being, because they can use their skills to add value.
Hidden drivers
What are concrete other cost drivers besides non-value-added activities?
Another example is increased reaction times in the event of errors. After all, if an employee identifies errors or defects for which a quick solution or immediate consultation with the supervisor is required, in many companies he or she has to leave the plant or resort to other systems such as telephone, smartphone, paper or similar. This then leads to unnecessary travel times, long response times and operational costs. Such communication efforts can be significantly streamlined with the help of digitization through task management. Employees can then assign a task to their supervisor or colleague or communicate directly with them via live chat and solve problems in real time.
What would you advise companies to do if they want to take a closer look at their actual costs based on the examples you gave?
It's important to draw the right conclusions. This means taking a close look at an argument such as increased susceptibility to errors and individually assessing what costs are incurred if the quality data is not analyzed. Based on this assessment, solutions must be sought that leverage the unused potential.
Enormous savings potential
How high are the average costs that can be saved by digitizing production processes?
Typical savings potential is in the six- to seven-digit range, although this naturally depends on the application, the size of the company and the acute nature or impact of current challenges - such as current reject rates due to faulty process execution. An impressive example of massive cost savings in the seven-digit range is provided by our customer POLIPOL, a leading manufacturer of upholstered furniture. An increasing variety of products and non-transparent paper-based processes made it difficult for the company to maintain its high quality and productivity in the future.
By eliminating paper and digitizing all production processes, a large number of non-value-added activities were eliminated. The annual savings potential was enormous: a total of more than 2.2 million euros while at the same time reducing the training time for new employees by 67 percent.

How the path succeeds
What tip do you have in conclusion for companies that want to set out in the direction of digitization?
In addition to deciding on the right technology, which should be considered with well-founded research, it can help if you stick to the guiding principle of "think big, start compact" during implementation. This means that you don't have to start implementation right across the board, but you can develop use cases one after the other. In our experience, it makes sense to start with high-impact use cases such as maintenance or commissioning. This is where efficiency gains can make a big contribution due to the high level of employee qualification and the lack of qualified personnel. This then in turn gives the further roll-out a decent boost.
Stefan, thank you very much for your detailed explanations and the useful advice, which will certainly benefit many companies!
You can get more detailed information on the cost drivers based on a specific use case in our whitepaper "Paper-based vs. digital commissioning: the 7 levers to success". The success stories of our customers will also provide you with deeper insights and perhaps serve as inspiration for your own digitization journey.
Markus Glotzbach
During his professional career, Markus gained deep insights at companies and large groups in different industries and knows the digitalization hurdles and problems on the shopfloor. Before joining Operations1, he studied International Management (MA) and worked in the Cloud Computing as well as SaaS telematics sector.