What it's about
In this article, we'll explain how outgoing goods inspections are typically performed and why they're important for businesses. We talk about the risks of using manual checklists and explain how digitizing them can save costs.
What is Outgoing Goods Inspection?
The outgoing goods inspection is an important and often underestimated area of manufacturing companies such as machine and plant manufacturers. It is the last stop in the company before the goods make their way to the customer.
In addition to picking, packing, and the preparation of documents such as delivery bills, inspection and testing play an important role in outgoing goods. This is where checklists come into play, which in many companies are still paper-based.
In concrete terms, this means: creating checklists in Excel, printing them out, filling them in by hand and digitizing them manually. In the outgoing goods department, checklists help the employee to verify whether the goods correspond to the customer order in terms of type and scope. The employee in the outgoing goods department should definitely work through these checklists systematically and carefully, because…
… the outgoing goods inspection plays an important role in the company
Outgoing goods inspection is more important than first thought: it is essential to ensure and maintain your customers’ satisfaction. With a proper outgoing goods inspection, you ensure that orders are complete, properly packaged and without damage. After all, if parts are missing or the goods were damaged during transport, in the worst case scenario your customer’s production will come to a standstill. After the goods have arrived at the customer’s premises, the customer usually carries out an incoming goods inspection.
The outgoing goods inspection is the last link in the internal logistics chain. After all, the goods issue process is completed when the goods are handed over to the carrier. However, just because the goods have left your warehouse in perfect condition does not mean that they will arrive at your customer in the same condition. A lot can still happen on the way and this is out of your hands. In this case, the documented outgoing goods inspection serves as important evidence.
The savings potential through the outgoing goods inspection is large
Correct and careful documentation in the outgoing goods inspection pays off. Let’s assume you have properly handed over the customer order to the carrier and yet a complaint arises: parts are missing or have arrived damaged. Of course, you don’t want to jeopardize the customer relationship you may have spent years building. So you resend the missing or defective parts at your own expense. A Operations1 customer project shows how high the resulting damage can be: There, goodwill towards customers cost a six-figure amount annually. Parts of deliveries regularly disappeared. In the end, the lack of evidence against the contracted forwarding company cost several hundred thousand euros.
Lack of evidence due to paper-based checklists
A paper-based checklist consisting only of checkpoints to be checked off has little probative value. The inspecting employee may accidentally check off an item even though the order is not complete. If, on the other hand, your employee has taken a photo of the complete order in the carrier’s truck, you have strong evidence. If damage or other problems occur, you can make your shipping company pay for the damage. This is because you can clearly prove that you handed over the goods complete and intact.
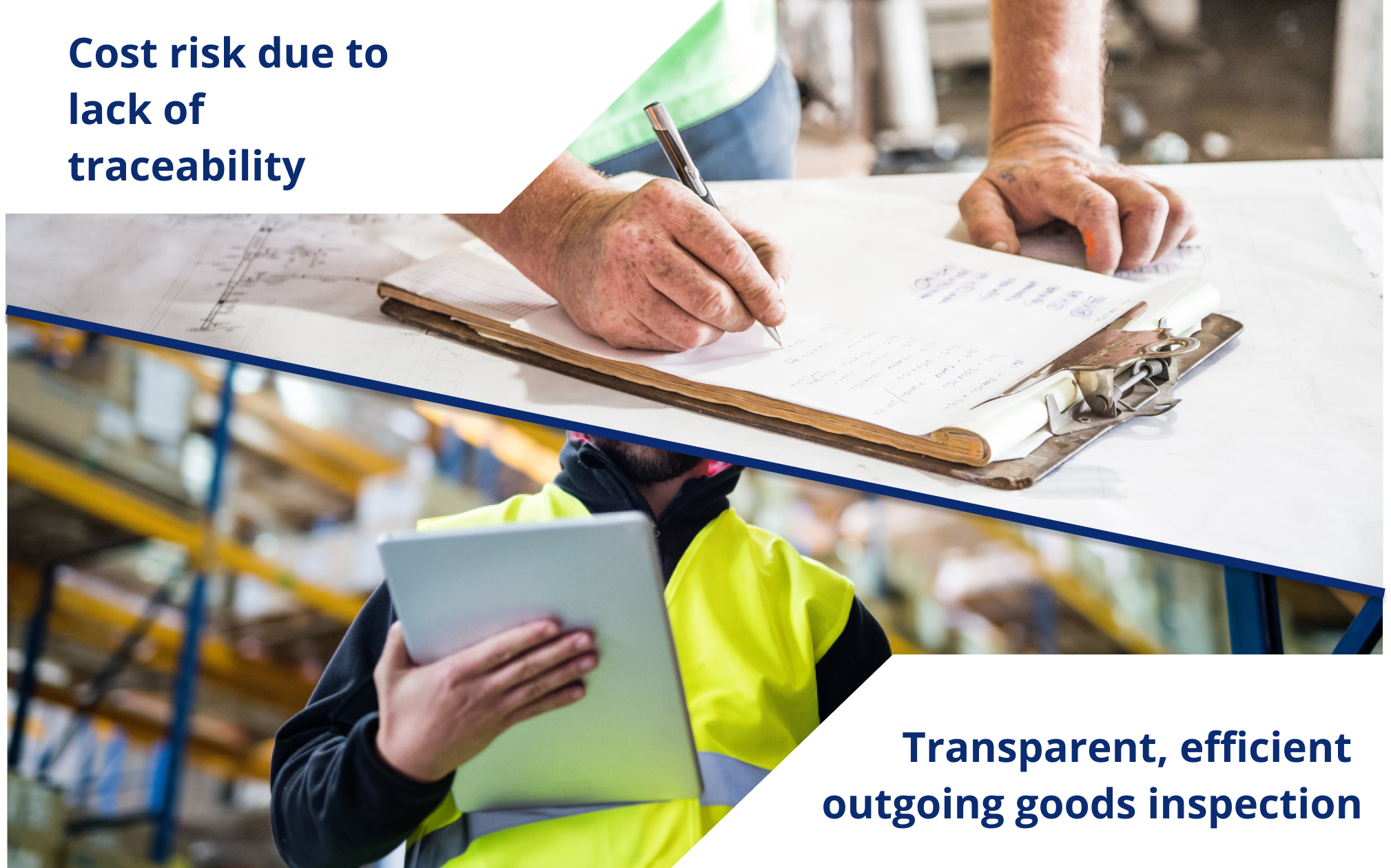
How companies benefit from digital checklists in their outgoing goods inspection
A digital checklist software helps you with an efficient and safe outgoing goods inspection. A digital checklist guides your employees through the process step by step. This way, they know exactly what needs to be checked and recorded on photos or videos. The photos and videos can be taken directly in the software on the respective device, e.g. the tablet. The advantage: easy archiving. With little effort, you bundle all the important data in one tool and can respond quickly in the event of complaints and claims by customers. The images, checkpoints and value entries are directly linked to the customer order. So you can search the software in seconds: for example, you simply enter the order number in the search field and you have all the data you need in order to check and process a complaint. Thanks to the classification option, you can search all reports by carrier, for example. This gives you complete traceability, retraceability and, above all, protection against unjustified complaints.
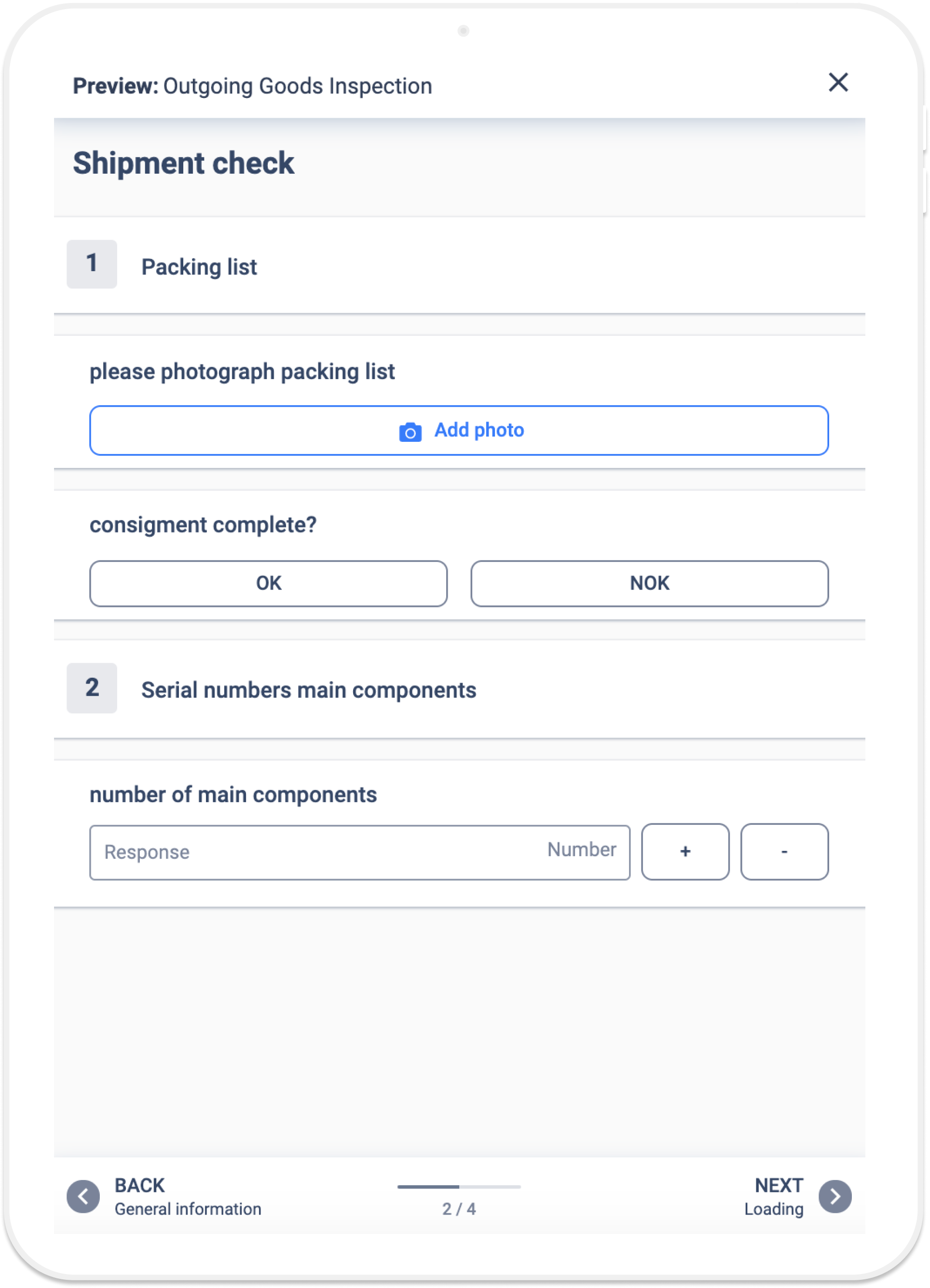
What should an outgoing goods inspection checklist contain?
General order information, such as order number, customer number, etc.
Name of the shipping company and license plate number of the transport vehicle
Date of goods issue, i.e. handover to the forwarder
Ordered goods in correct quantity (target/actual comparison with delivery bill)
If applicable, text field for entering weight and number of packages or pallets
Check of packaging (documentation of packaging material, presence of shipping labels, etc.)
Check for visible damage
Image feedback showing goods complete and undamaged in the carrier’s truck
As you can see, you can benefit from digital documentation of your outgoing goods inspection and save money. With the Operations1 software, you have all important information in one place and thus a powerful means of proof in case of unjustified complaints.
Checklist 4.0
With digital checklists, you increase efficiency and make better decisions. Read in our whitepaper how our software solution can help you!
Markus Glotzbach
During his professional career, Markus gained deep insights at companies and large groups in different industries and knows the digitalization hurdles and problems on the shopfloor. Before joining Operations1, he studied International Management (MA) and worked in the Cloud Computing as well as SaaS telematics sector.