What it's about
In this article, you will learn how targeted digitization with the help of assistance software not only creates enormous efficiency gains in incoming goods inspection, but also ensures that everything is documented in a legally compliant and error-free manner.
Why are Digital Inspection Checklists the Future?
The incoming goods inspection is important for determining whether a delivery corresponds to the initial order placed in terms of quantity and quality. The delivery bill serves as the basis for checking incoming goods.
Every manufacturing or processing company needs goods in the form of raw materials and supplies, finished products or semi-finished products that they process or sell. Upon delivery, these goods are checked both for completeness and quality.
The incoming inspection checklist is therefore of high importance for every production company. It not only ensures efficiency and an optimum flow of goods, but is also a significant factor in quality management. Here, random samples are taken and checked for the required quality. The continuous documentation of all findings through the incoming goods inspection checklist is of central importance. It has an influence on the entire inventory management and ultimately also on production itself.
Even today, many companies in this area still work increasingly paper-based. Order and delivery bills are usually printed documents. Likewise, quality inspection checklists are usually a stack of pieces of paper – after all, they have to be signed by the inspector and laboriously archived. This involves many risks.
Find your individual way to digital incoming goods inspection
The most important thing first: Both the quantitative incoming goods inspection based on a checklist and the quality control of the delivered goods can be ideally digitized. All processes and cross-company systems, such as ERP and MES, can be seamlessly integrated or connected via various interfaces. The form can also be adapted to the individual needs of your company as well as common norms and standards.
In this blog, we will give you answers to the five relevant questions on the basis of which you can start on the path to your digital incoming goods inspection:
What role does incoming goods inspection play in the company?
What is the impact of traditional paperwork for an organization?
Why do leading companies rely on a digital incoming goods inspection checklist?
How can companies benefit from software beyond digital incoming goods inspection?
How can the path from a paper-based to a digital incoming goods inspection checklist look like?
Why are Incoming Goods Inspections Important?
The goods receiving department is at the beginning of the value chain within a factory. Raw materials, operating resources, finished products and semi-finished products are delivered here, usually from different suppliers. Immediately upon delivery, the goods must be checked for completeness and quality. This includes checking the shipping documents. These include, for example, forwarding records, packing lists, delivery bills or – in the case of deliveries from abroad – possible customs documents. At the same time, new or additional documents are also created. The aim is to document a complete process chain in order to be able to provide information in the event of recourse cases and to be able to provide the necessary legally binding evidence.
Errors that are not detected here can later become very expensive. On the one hand, these can be missing quantities, the absence of which was not noticed and thus not documented. In retrospect, missing goods can only be reclaimed in the rarest of cases. The same applies to insufficient quality of the material or damage that occurred during transport. If the raw materials and supplies delivered do not meet the necessary standards, these must be complained about directly to the supplier. In the event of transport damage, the recipient may refuse to accept the goods.
For this reason, incoming goods inspections are usually carried out in the presence of the supplier. By means of incoming goods inspection, companies thus not only ensure their own defined quality standards, but above all also safeguard themselves economically. According to the German Commercial Code, companies are even obliged to inspect delivered goods for possible defects and completeness without delay, i.e. immediately upon receipt.
If no incoming goods inspection is carried out and defects are thus only discovered afterwards, the delivered party must still pay for the goods in full – regardless of how damaged or defective they are. If defects only become apparent during further processing of the goods, these are so-called hidden defects. These must be reported to the manufacturer without delay. Delayed reporting also leads to the loss of warranty rights in this case.
Companies that forego the incoming goods inspection may have to reckon with further consequences. If undetected defects are accepted, the processing company is liable for damages to its customers when reselling the goods. The supplier may also invoke a breach of the duty to mitigate damages.
The control is carried out by trained personnel in the goods receipt department. On the one hand, it includes the comparison of the order, delivery bill and actually delivered quantity, on the other hand, the inspection of the goods quality is also carried out. In the process, all delivered materials are compared with the associated accompanying documents. Depending on the quantity of goods required, these checks – e.g. measuring, weighing, counting – are carried out by means of a total survey or a random sample. Sampling and material testing are also sometimes part of the normal incoming goods inspection. All results of these checks must be documented – often in handwriting – in protocols.
What is the impact of paperwork for an organization?
Most companies receive deliveries almost daily – many even several truckloads within a few hours. This means that large volumes of documents are quickly generated in the goods receiving departments. Employees often spend a considerable amount of their working time filing and archiving logs and documentation.
On the one hand, this costs valuable time that should actually be spent on the professional inspection of the delivered goods. On the other hand, if no inspection of the delivery is carried out at goods receipt, the customer loses his warranty rights in the event that he has received damaged goods.
But that is not all. If a company carries out incoming goods inspection on a paper-based basis, there are also other major risks for the profitability of the entire company as well as for the production steps that follow later. If information is not tracked digitally, the risk that important information will simply be lost is very high. A piece of paper is simply left somewhere in the heat of the moment or filed away in the wrong folder. When information on a specific delivery is requested again later, the search begins and often ends in vain.
Without data, it is also not possible to evaluate the quality findings. This also makes it difficult to evaluate suppliers, for example. Less good suppliers or repeatedly insufficient goods quality are thus often only recognized after a long time. This has an impact on production and subsequent product quality. Similarly, complaints can be asserted much more quickly and easily with suppliers using digital image evidence, and can be substantiated in the event of a legal dispute.
Another disadvantage of paper-based incoming goods inspection is the great effort involved in creating the documents to be used. Once a protocol or checklist is designed and duplicated, the effort to update or make corrections is extremely high. Not to mention the waste of resources and the question employees are guaranteed to ask themselves: What was the latest version and which paper should I use? The result is inaccuracies and errors as well as inconsistent information in systems and on all paper.
The key risks for paper-based incoming goods inspection are thus:
Inefficient processes in incoming goods inspection
Loss of warranty rights if inspection is not performed in a timely manner
Low traceability of information
No evaluability of quality findings for continuous improvement
Lack of data basis for evaluating supplier performance
High effort to create and update checklists
Why do leading companies rely on digital incoming goods inspection checklists?
The advantages of a fully digitized incoming goods department are obvious. That’s why more and more companies, especially large ones, are opting for targeted, full-scale digitization in this area. A digital incoming goods inspection is significantly more informative than a handwritten one on paper. For one thing, photos can be integrated directly into digital checklists as later evidence. For another, employees save a lot of time when checking off the smart, digital checklist on smartphone or tablet. Furthermore, the easy archivability and later searchability is one of the striking advantages of the digital incoming goods inspection checklist. The filing of inspection records in paper form is completely eliminated and thus also an unnecessary and time-consuming administrative burden.
Countless shelf meters for file folders disappear in the virtuality of the company’s own server landscape or a cloud. As a result, the data can always be viewed from anywhere and by all relevant people at the same time, and can therefore be actually used. For example, when processes need to be evaluated and decisions made.
In addition, all data from the incoming goods department can be transferred directly via interfaces to all company-wide systems, such as ERP or MES. This ensures greater transparency throughout the entire production process – from raw materials to the finished product. But the digital checklists offer even more advantages. They are very easy to use and guide employees through the entire goods receiving process. This makes it virtually impossible for even the smallest inspection step to be forgotten.
Employees can create their own images of damage or other special features and add them directly to the document. In addition, they can also add important comments that are helpful for improving processes in goods receiving. This also shortens the lines of communication between the workforce and management. Important information gets directly to the people in charge. Here, too, nothing is lost.
With the help of scanner- or log-in-based user recognition, it is also very easy to track the work and responsibilities of each individual employee. This is particularly helpful if queries arise later about a delivery or if further tasks arise that absolutely have to be completed by the same person. Illegible signatures or abbreviations are a thing of the past. Signatures are confirmed directly with the digital identity. Dates and especially times are no longer rounded approximate values, but correspond 100 percent to the actual time.
The advantages of a digital incoming goods inspection checklist are thus:
Comprehensive traceability of information and automatic archiving
Direct integration of photos and videos and linking to the order
Connection of sensors such as scales or scanners for dynamic value transfer
Real-time communication of relevant findings for the production process
Less documentation effort in goods receipt
Evaluation of incoming goods data in real time
Increase in employee satisfaction
How can companies benefit from software beyond incoming goods inspection
Presumably, almost all other departments and company divisions will benefit from digitized incoming goods inspection. This starts with the production departments just mentioned. They can coordinate orders better and always know exactly about stock levels and the quality of the available material. Purchasing, controlling and management also gain valuable insights from the information recorded by the incoming goods department and made available to all relevant stakeholders. Negotiations with suppliers are clearly easier to conduct on the basis of valid data. Assessments, possible penalties or price deductions can be easily argued on the basis of digital evidence. Controlling – both for incoming goods and for the entire company – also becomes much more accurate and can be based on concrete values from incoming goods. The benefits are therefore by no means limited to just one department, but entail far-reaching improvements for the entire company.
What can the path from a paper-based to a digital incoming goods inspection checklist look like?
Even today, as soon as the term digitization is mentioned, many employees and decision-makers imagine an elaborate, long-term process that often ends in frustration and without satisfactory results. But there is no reason for this assumption. At this point, it should be said quite fundamentally that the digitization of incoming goods inspection only takes a few weeks. The most important aspect is good preparation. This includes, above all, the collection and structuring of all requirements for a digital incoming goods inspection.
As soon as the requirements have been discussed with the software provider and translated into concrete work packages, things can get started. First, a cleanup of the existing documents for incoming goods inspection should be started. Then, all relevant documents and papers are transferred to the digital world so that they can later be made available to employees on mobile devices or at fixed inspection terminals. Now the interactions must be configured according to the individual tasks that arise in the company. This then becomes the interactive checklists already discussed, which guide employees step by step through each individual inspection process.
Once all documents have been digitized, all required sensors are connected, such as for scales, measuring devices, QR and barcode scanners, and possible other inspection instruments. This allows the automatic recording of values to take place later. The degree of automation of the incoming goods inspection is thus increased many times over. At the same time, the employee effort for transmission, writing and archiving is reduced. Finally, the user’s own dashboard can be created. This can be used to monitor goods receipt metrics. All relevant parameters must be stored here.
Based on the data obtained, important decisions can then be made for goods receipt management. For example, whether the cooperation with a supplier should be terminated due to repetitive or frequent errors. Or whether more or less of a raw material should be purchased per delivery in order to better adapt the storage process to the needs of production.
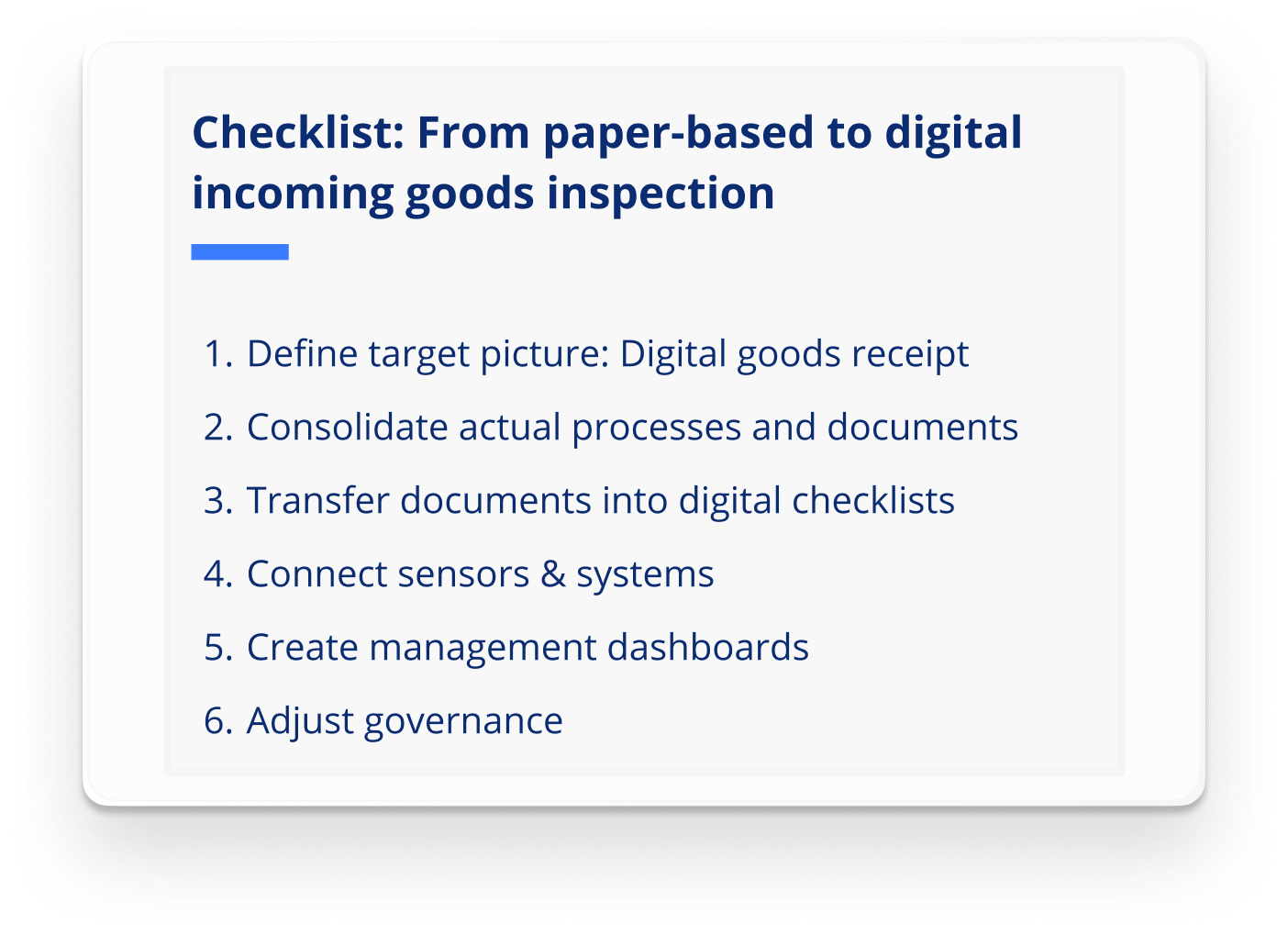
The start of digital incoming goods inspection – better today than tomorrow!
First of all, the digitalization of incoming goods inspection simplifies and accelerates the daily processes in the incoming goods department of every company. But that is only one major, visible effect that an assistance software achieves.
The consistent digitization of all processes, documents and checklists ensures greater transparency and traceability even at the time of delivery of the raw material and preliminary products. It enables simple data collection and evaluation. This not only eliminates the need for tedious handwritten documentation and time-consuming, space-intensive archiving tasks.
At the same time, digitization with assistance software already noticeably reduces costs in the medium and long term. On the one hand, the storage space for the many paper folders is eliminated. On the other hand, valuable working time of the specialists is saved. Thanks to the digital assistance system, they can devote their capacities entirely to quality inspection and the strategic optimization of incoming goods. Likewise, costs for errors that can happen due to lost documents or human errors during goods receipt – such as forgetting an important inspection step – are eliminated.
All these arguments make it clear that companies that still work mainly paper-based in goods receipt should start introducing digital assistance in the form of software sooner rather than later.
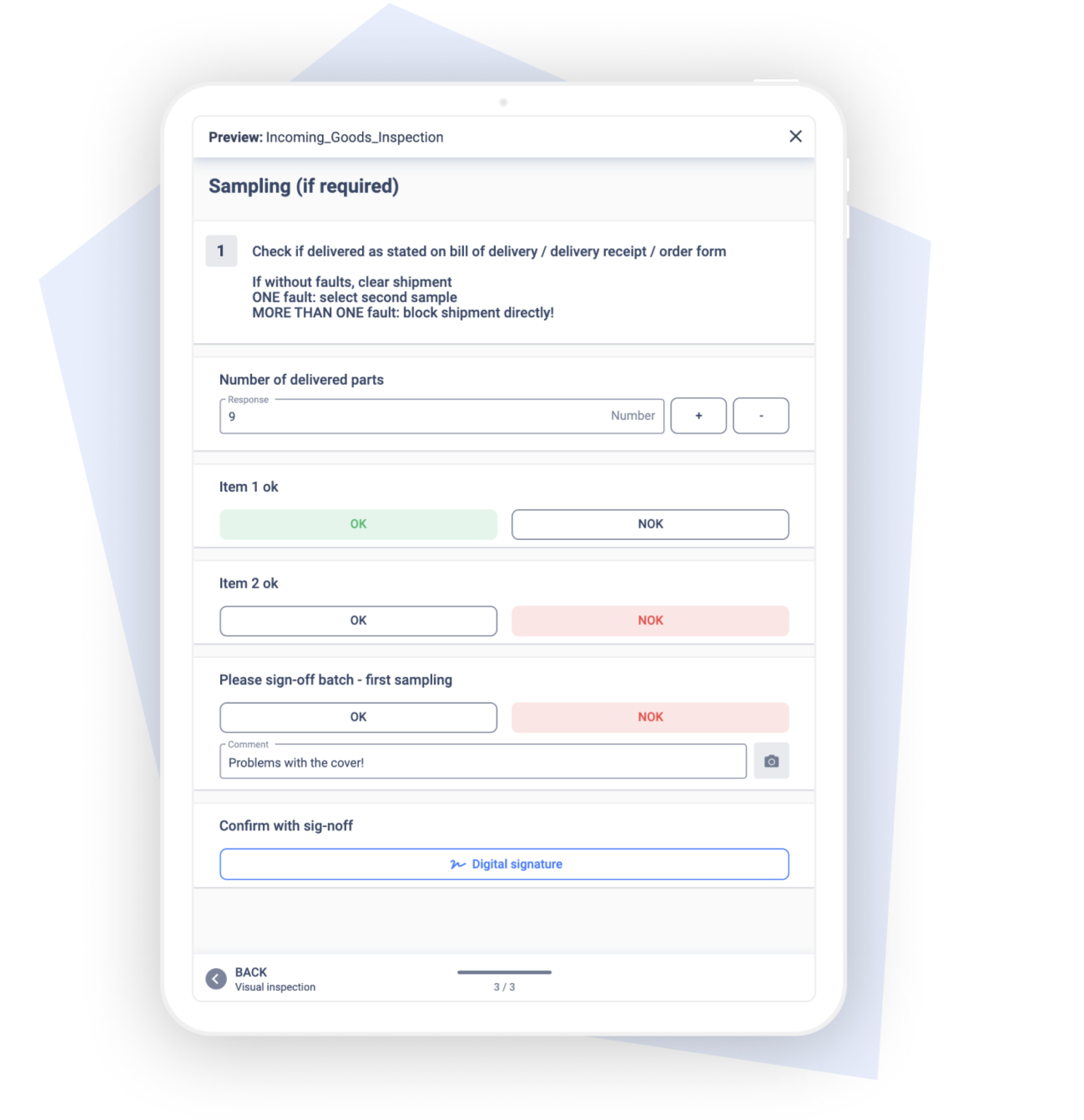
Would you like to learn more about digital incoming goods inspection?
With digital checklists from Operations1, you provide your employees with the optimal companion for incoming goods inspection. You can use Operations1 company-wide and thus work in a cross-departmental network.
Benjamin Brockmann
Benjamin Brockmann (M. Sc., Management & Technology) founded Operations1 in 2017 together with Daniel Grobe (also M. Sc., Management & Technology). The founders developed the software solution based on various practical projects, including at the Fraunhofer Institute, and on their experience in industry, auditing and management consulting. Benjamin Brockmann has already worked for companies such as KPMG and Arthur D. Little.