What it's about
In this blog post, we examine the typical documentation process to determine its potential for error and show you how quality risks can be reduced to a minimum through digital inspection documentation.
The process in static inspection documentation
To understand how inspection documentation relates to poor quality, let’s first look at a typical documentation process. Experience has shown that this process consists of the following three steps:
Step 1: An inspection checklist is created in word processing programs, such as Microsoft Word and Excel.
Step 2: For the inspection, the checklist is printed out and the quality inspection employees fill it out by hand during the inspection or afterwards. Additional inspection instructions are often used for complex inspection processes.
Step 3: After the inspection is completed, the completed document is digitized manually. This is done either by scanning or transferring the handwritten information.
Each of these steps entails a central quality risk.
3 Quality risks in the static test documentation
1. unrecognized deficiencies
A checklist created in Microsoft Word or Excel, for example, as described in Step 1, is usually not very intuitive. This can lead to misunderstandings, especially among inexperienced employees. At the same time, there is a risk that inspection steps will be forgotten, for example if an employee only completes the checklist after the actual quality inspection has been completed because he or she has supposedly already carried out the inspection process many times. In particular, so-called maximum lists, which are used for the quality inspection of variants, bear this risk. This is because employees must know, or read elsewhere, which inspection steps are necessary for each variant. The consequences of misunderstandings and omitted test steps are often undetected defects. If these are not detected until the final inspection, shortly before the goods are on their way to the customer, this leads to rework and possibly to delivery delays. In the worst case, the defects remain undetected and customers do not receive the desired quality. The result is complaints and thus additional costs.
2. incomplete defect description
When quality inspectors fill out printed checklists by hand, space for detailed information is very limited. Pictures of findings require additional effort and small text fields prevent the employee from describing a finding in detail. Subsequently, it is often necessary to re-interview the employee or even re-run the test to understand the reasons or extent of the discovered defect.
3. falsified conclusions
Errors also frequently occur in the third step, the manual transcription of handwritten checklists. Illegible entries pose the risk of transcribing information incorrectly. If these transmission errors accumulate, the analysis and evaluation of the quality inspection are no longer reliable and incorrect conclusions can be drawn.
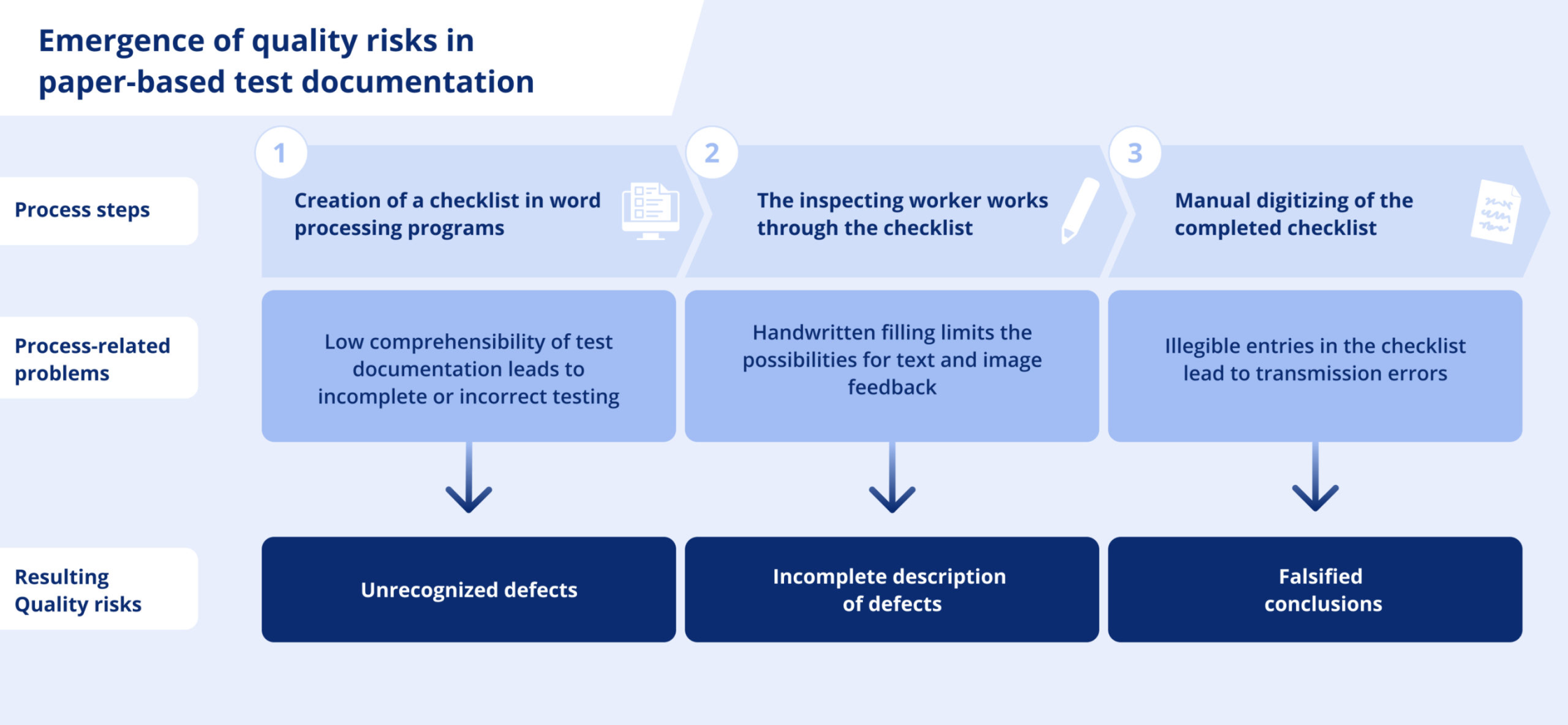
Minimizing quality risks through digital documentation
Software for Adaptive Process Execution can reduce the above-mentioned error potentials to a minimum.
You create intuitive checklists.
Images and videos explain test steps in a simple and understandable way. Mandatory fields ensure that employees do not skip any test step. Thanks to a modular structure, variant-specific test instructions can be created with little effort and the error-prone maximum list becomes superfluous. Intuitive process description ensures thorough quality inspection and thus reduces the number of undetected defects.
You enable a user-friendly information return.
Free text fields provide sufficient space for detailed descriptions of findings. Quality inspectors take photos of findings in seconds with their tablet and save them directly in the checklist. This information enables you to clearly assess the defects discovered.
You benefit from a reliable evaluation.
Transmission errors are a thing of the past. All information and data collected is automatically saved and archived as a digital report. Through the connection to third-party systems, reports can be exported and stored in your ERP systems and MES.

Conclusion
It is important to take a close look at the documentation process in order to identify potential errors. To counteract the quality risks mentioned above, intuitive and user-friendly checklists are needed in particular.
Checklist 4.0
With digital checklists, you increase efficiency and make better decisions. Read in our whitepaper how our software solution can help you!
Daniel Grobe
Daniel Grobe (M. Sc., Management & Technology) founds cioplenu GmbH in 2017 together with Benjamin Brockmann (also M. Sc., Management & Technology). The founders develop the software solution on the basis of various practical projects, including at the Fraunhofer Institute, and their experience in industry, auditing and management consulting. Daniel Grobe is a Junior Board Member of bayme vbm and has already worked for companies such as KPMG and Continental.