Increased productivity for global competitiveness
Constantly growing demands on products, employees, supply chains and processes continuously pose new challenges for globally active OEMs and suppliers. Operations1 helps you to strengthen process reliability and create flexibility in the rapidly changing environments with digital work instructions and checklists.
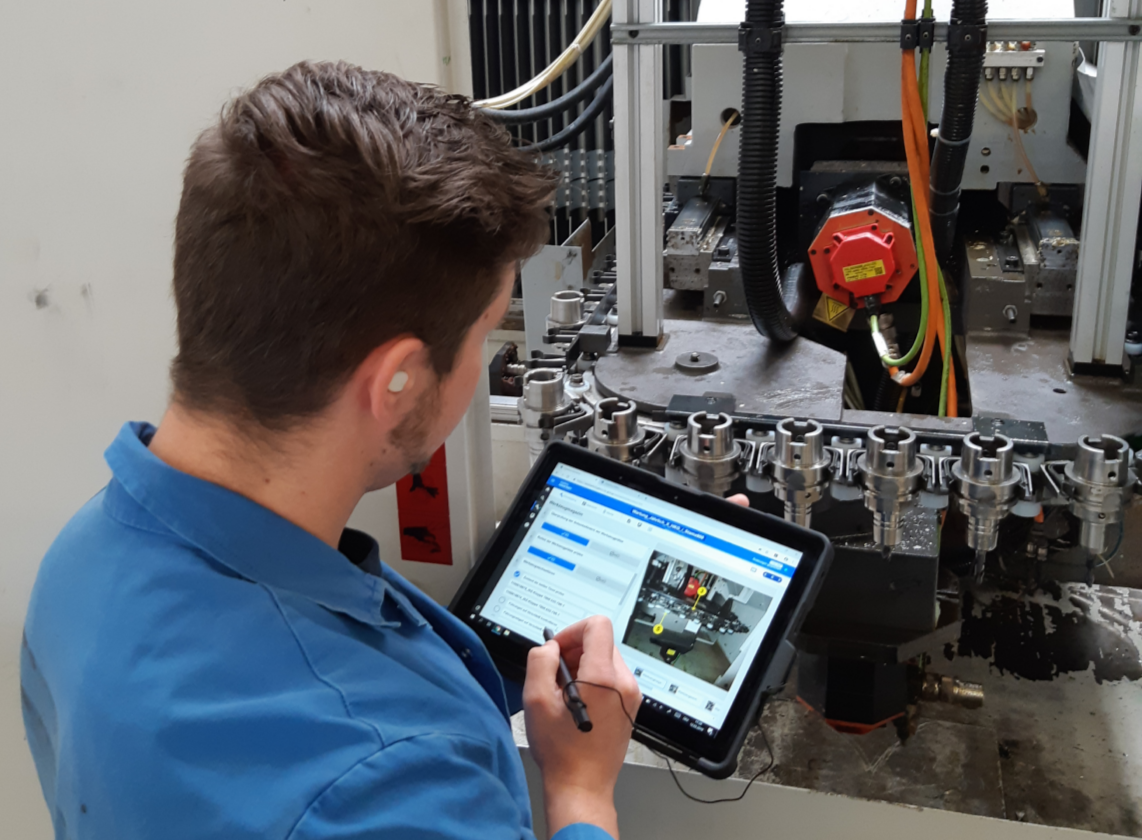
The benefits of digitalization for operational excellence
Quickly established global process standards
Make optimized process knowledge for standardized processes immediately available digitally to all plants.
High OEE for more output with excellent quality
Improve your maintenance and audit processes to keep the performance of your machines and the proportion of good parts high.
Increased compliance and occupational safety
Operations1 strengthens your audits and reporting with increased process reliability reliability and complete documentation.
Flexible workforce for increasing complexity
Use modular, multimedia work instructions and software-supported qualification management for faster and more effective instruction.
Flexible deployment options for existing employees
Up to -67% reduction in training times
Activities carried out in accordance with qualifications and guidelines
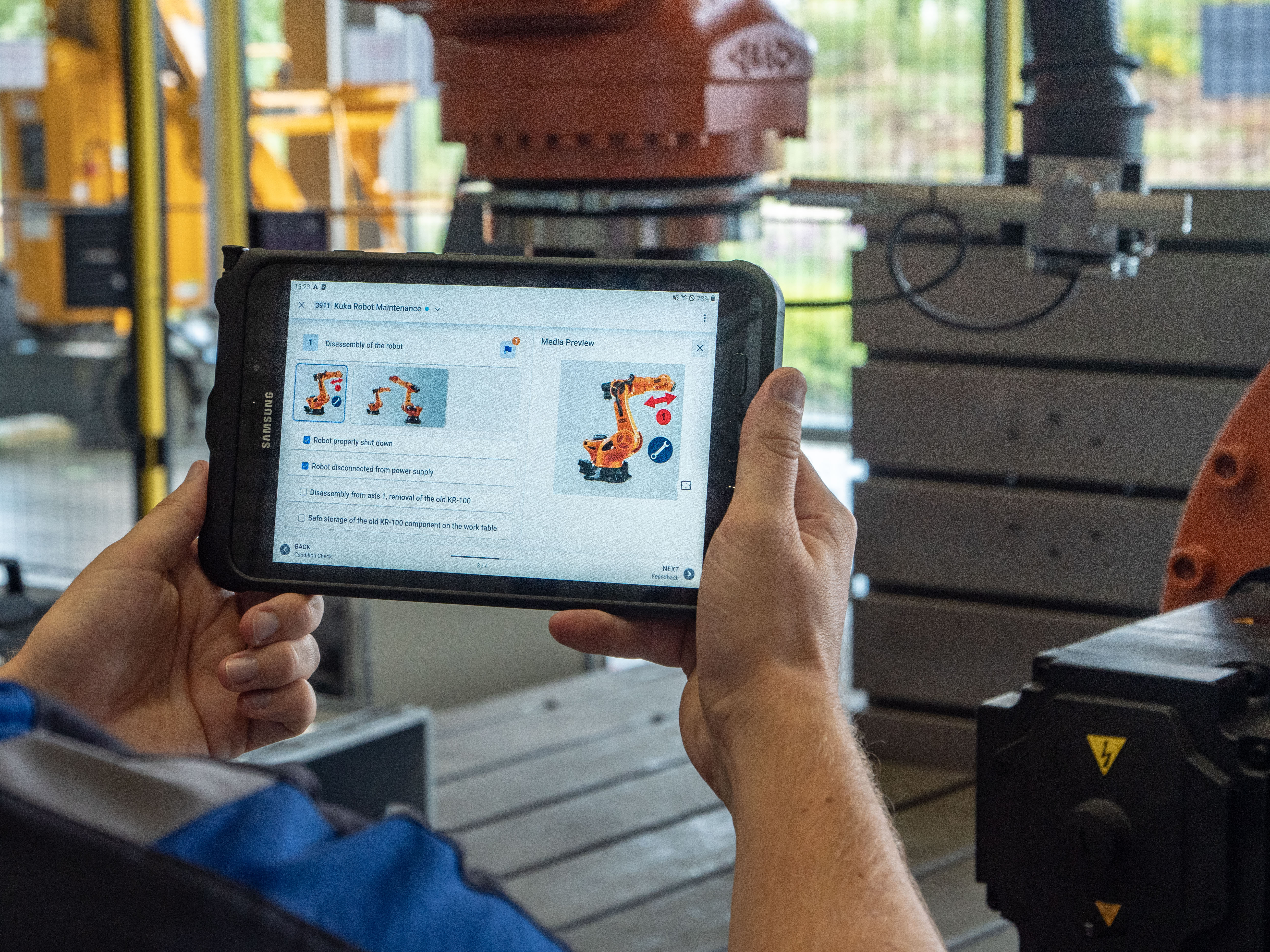
Increased machine availability for increased productivity
Improve your maintenance with digital checklists and integrated maintenance planning. Relieve technicians and reduce maintenance costs.
Increasing Overall Equipment Effectiveness
Predictive maintenance replaces troubleshooting
Ensuring just-in-time requirements
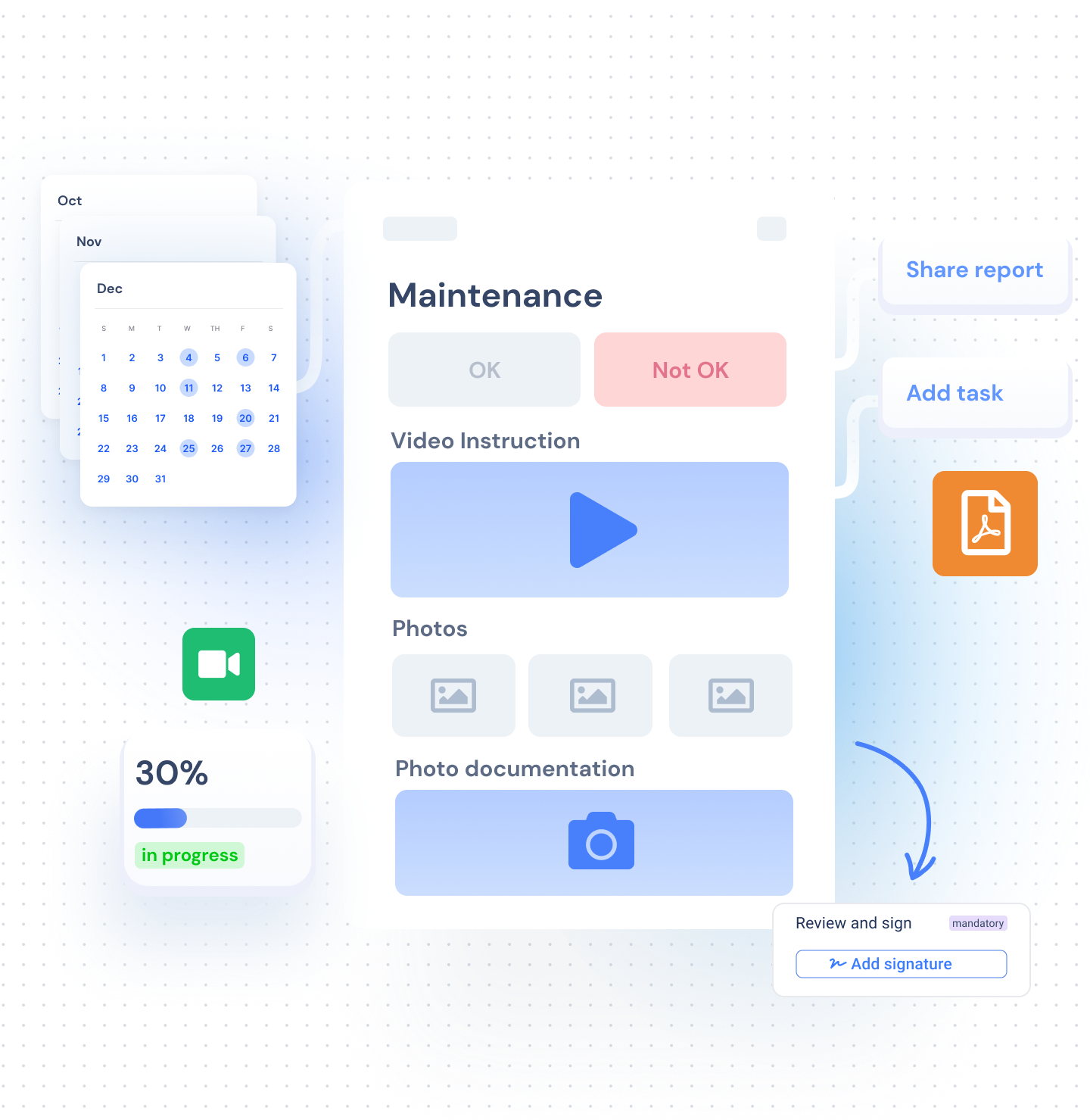
Quality efficiently checked and seamlessly logged
Ensure the highest quality standards through process-reliable and standardized quality inspections. Results and metrics are documented in the step-by-step logs and are easy to track.
Quality tests according to defined process standards
Reduction of errors by up to -25%
Reduce the effort involved in test documentation by -67%
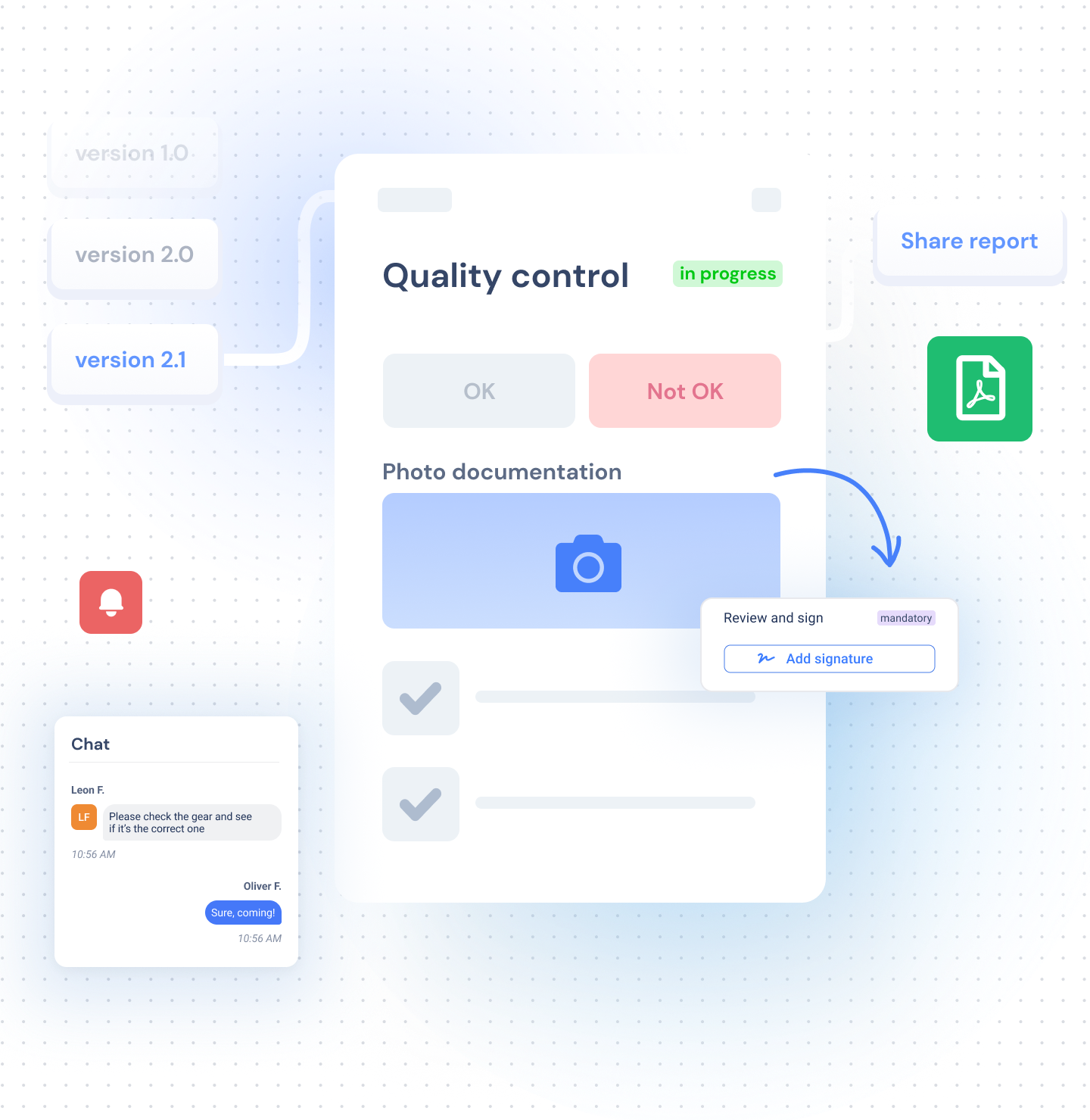
CIP lived simply and digitally documented
Digital checklists for 5S/6S audits, Gemba Walks and safety walks: Have findings recorded directly in Operations1 via photo and video. Use recorded findings for data-driven CIP.
Flexible and employee-based CIP and audit processes
Up to -80% effort for 6S documentation
Increased occupational safety in production
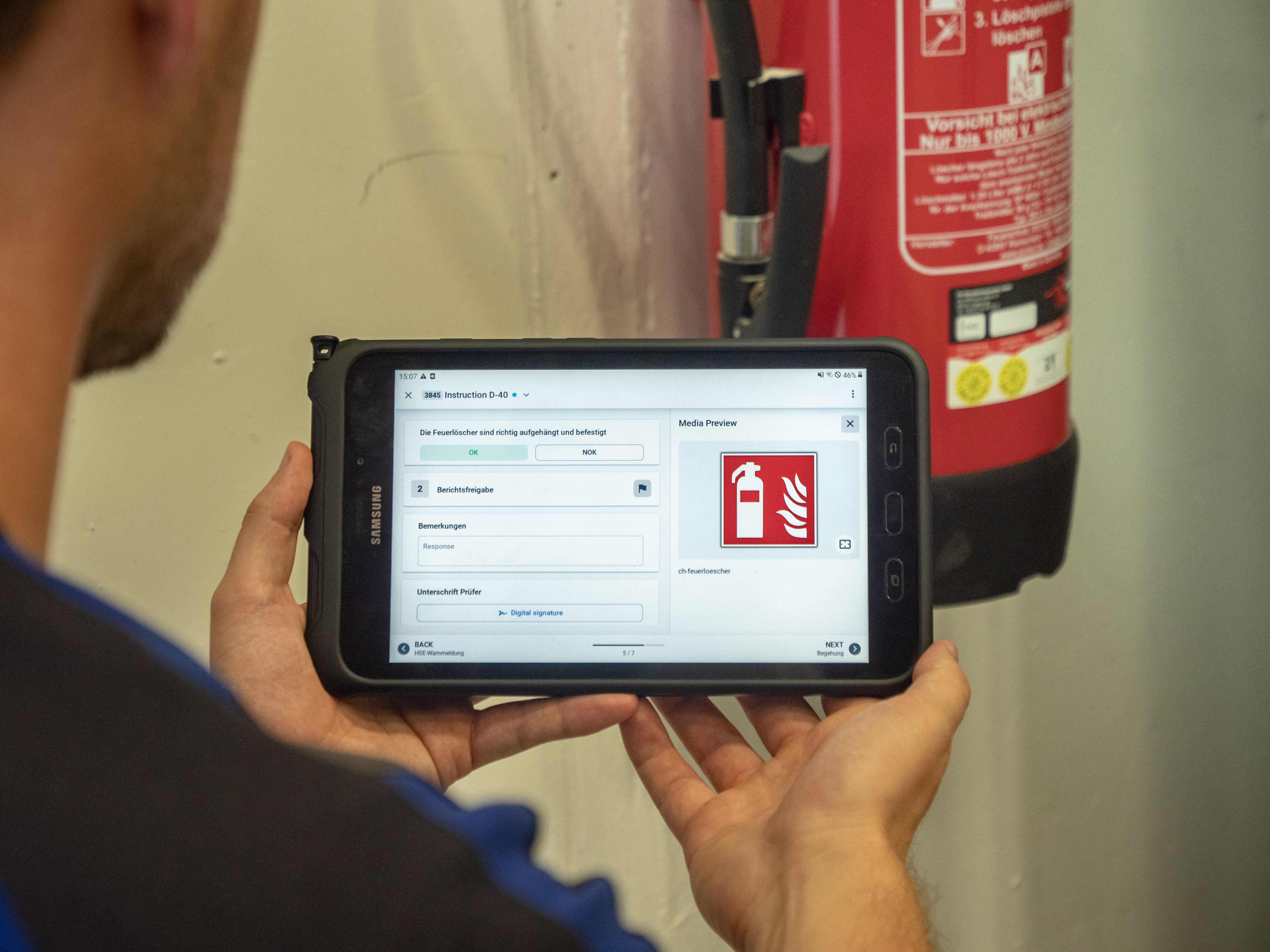
How leading companies benefit from Operations1
Hirschvogel
-60% downtine in international plants and savings of €250,000 per location
Oetiker
+11%P OEE after 6 months and -23% mean-time-to-repair (MTTR)
BWF Profiles
Gain of +80% time savings and 50% quality control efficiency
Schwäbische Härtetechnik Ulm
Reduction of machine downtimes through automated maintenance planning
Schedule a meeting
Use the exchange with our product experts to find out how you can benefit from Operations1.
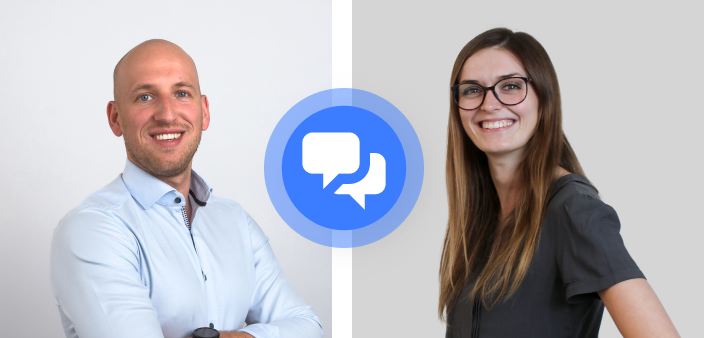
Fill out the form and we will get back to you in a short time.