Webinar recap: Set up machines more efficiently: How to reduce changeover times with digital solutions
Changeover is one of the key, yet often underestimated, levers in manufacturing. When optimized properly, it can significantly boost efficiency, flexibility, and machine availability. This webinar recap shows how companies like Greiner Packaging have reimagined their changeover processes using digital tools.
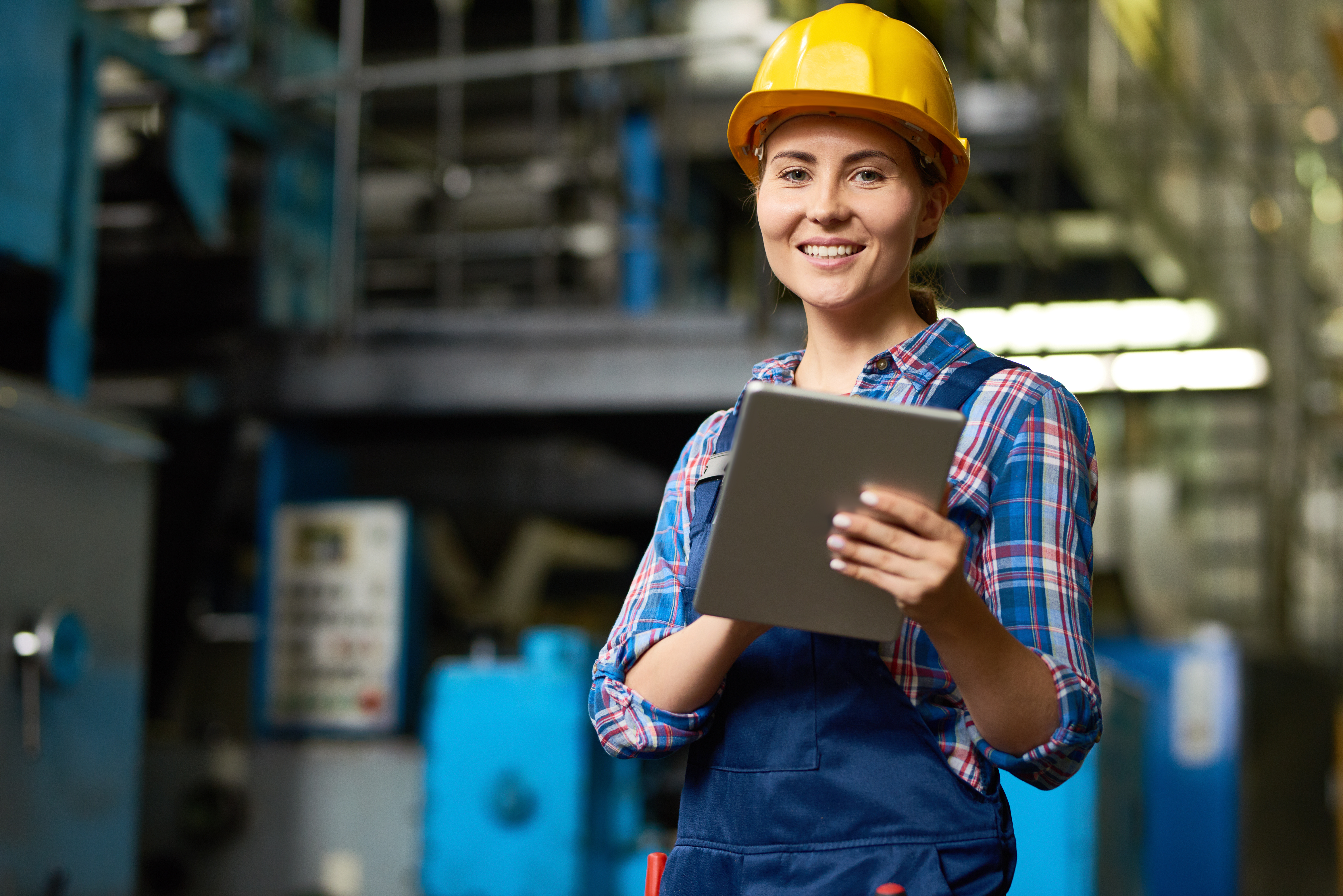
What it's about
In this post, we summarize the key takeaways from our recent webinar, using Greiner Packaging as a real-world example. We explore the challenges surrounding machine setup, practical digital solutions, and the measurable impact of implementation—all aimed at answering one crucial question: How can digital work instructions help reduce changeover times?
The Status Quo: Changeover Costs Time, Effort, and Efficiency
Many companies face the same issue: changeover processes are complex, error-prone, and heavily dependent on the experience of individual employees. Especially in environments with high product variation and a lack of standardization, machine downtimes increase—along with costs.
Greiner Packaging was no exception. Documentation required significant effort, instructions were open to interpretation, and teams were highly reliant on experienced technicians or maintenance personnel.
“In many production environments, paper-based documents create a high administrative and documentation burden. On top of that, critical information is often compressed onto a single A4 sheet. This leads to frustration, errors, and data gaps.” Rami Makhlouf, Global Senior Expert Operational Excellence, Greiner Packaging
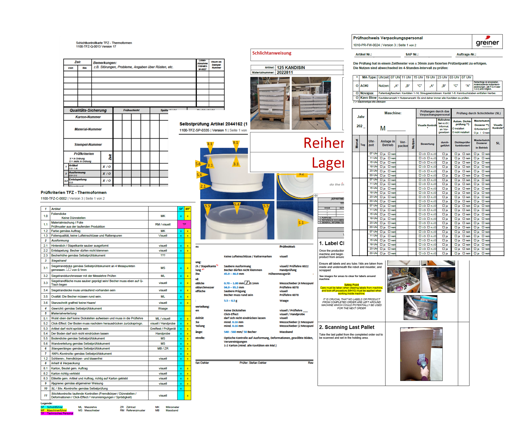
The Solution: Digital Work Instructions with a System
Together with Operations1, Greiner redefined its changeover processes—placing digitalization at the core. Instead of paper-based instructions and manual steps, they now rely on digital, multimedia-rich work instructions. These are automatically assigned to machines via the MES, are standardized in structure, and guide employees step by step through the setup process.
Two key principles proved especially impactful:
Efficient changeover procedures:
Tailored setup instructions combined with seamless worker self-inspection ensure smooth transitions and minimize downtime. Employees know exactly what to do—regardless of experience or language.Event-triggered process:
Digital instructions are automatically linked to the correct machine and task. This significantly reduces complexity on the shop floor and increases process reliability.
The platform is intuitive, multilingual, and visually enhanced. The result: fewer errors, fewer questions—and faster machine restart times.
“We simplified complex setup instructions using easy-to-understand video tutorials with Operations1—this significantly eased the workload for our employees.” Stephan Wagner, Head of Quality Assurance, BBW Lasertechnik GmbH
Why It Works: Integration, Standardization, Usability
One critical success factor at Greiner was the seamless integration with existing systems. The setup instructions are not isolated but fully connected to the Manufacturing Execution System (MES). Work orders are automatically generated, assigned to the correct machine, and fed back with documentation in real-time.
Thanks to structured, standardized, and multimedia-rich content, even new employees can quickly contribute to operations—without relying on expert-level knowledge. Setup quality improves, training time decreases.
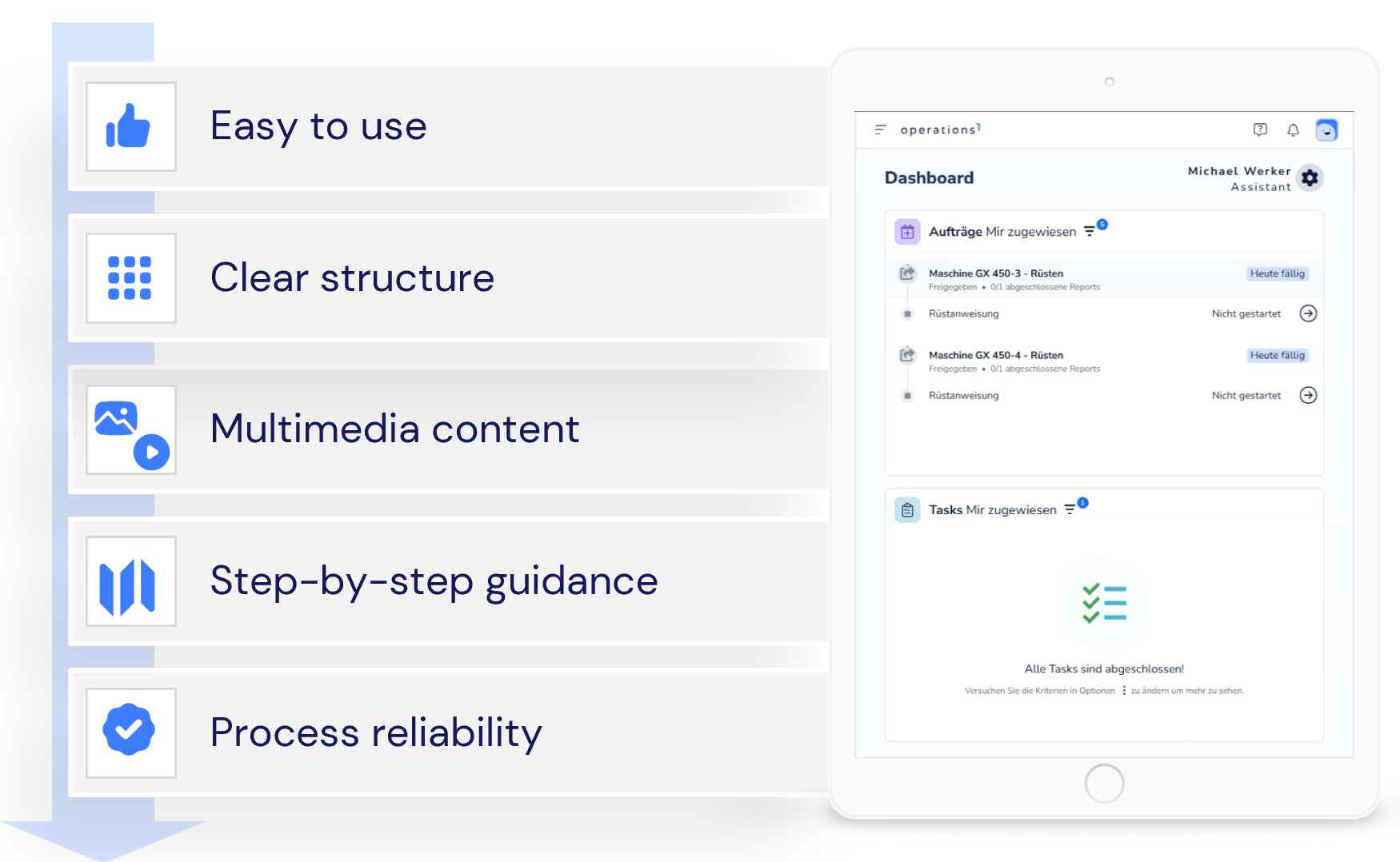
The Results: Higher Availability, Less Downtime
Introducing digital solutions like Operations1 can deliver measurable impact across production environments:
+5 percentage points machine availability – through structured, standardized processes
+11% OEE (Overall Equipment Effectiveness) – by reducing downtime and improving transparency
Fewer questions and corrections – enabled by clear, visual instructions
Faster onboarding – thanks to step-by-step video tutorials
“Operations1 helped us provide focused information to our employees and enabled more accurate documentation of work results.” Rami Makhlouf, Global Senior Expert Operational Excellence, Greiner Packaging
A standout benefit: this solution ensures consistent quality even with high employee turnover or less experienced staff—no longer relying solely on maintenance technicians or setup specialists.
Thanks to the image documentation directly in the digital checklist, professional error image analyses can be carried out to rectify problems and improve the process and quality.
One of the most important aspects for machine and plant manufacturers is the complete digital documentation of the activities and checks carried out: Automatically generated reports can not only be used for efficient verification in the event of customer inquiries, but can also be shared with customers, for example as a PDF file, as transparent evidence of a properly performed assembly and quality control.
A Global Standard for Efficient Changeover
What’s truly impressive about Greiner Packaging’s approach is the global scalability. The digital solution from Operations1 is now in use at multiple sites—across Europe, North America, and beyond—creating a company-wide standard for setup excellence.
The advantages of this global rollout:
Centralized, sustainable, and multilingual knowledge management – standardized content accessible to all employees worldwide
Consistent quality standards for setup and inspection – internationally applicable, locally adaptable
Increased process reliability and productivity – enabled by harmonized workflows and digital changeover management
Transparent benchmarking across sites – to identify optimization potential and replicate best practices
Greiner Packaging demonstrates how smart digitalization not only improves processes, but also establishes a common operational language across borders.
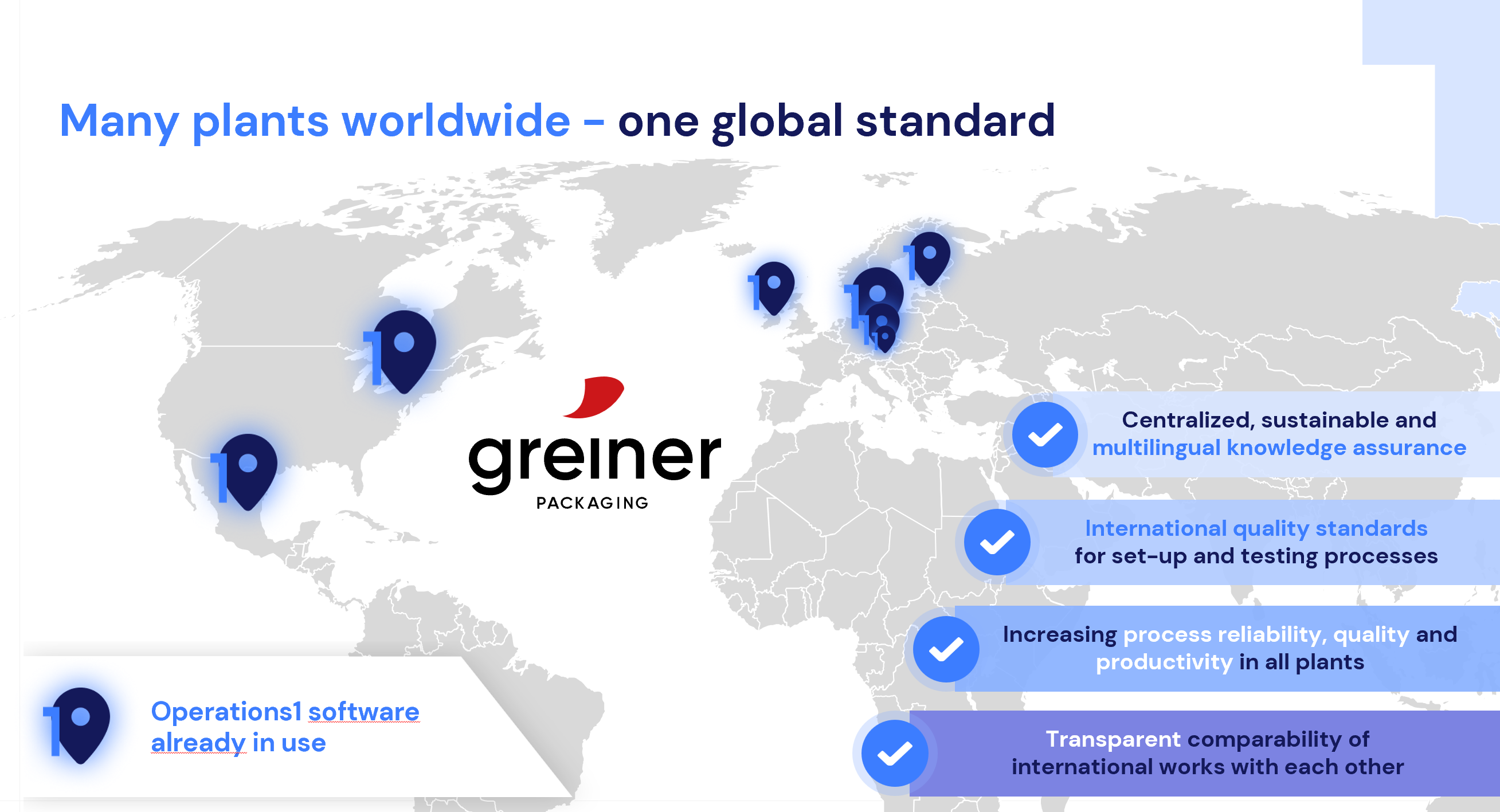
Conclusion: Rethinking Setup – Digital, Flexible, Efficient
The example of Greiner Packaging clearly shows how digital solutions can enable efficient changeover in serial production. Manufacturers still relying on paper-based workflows are leaving valuable potential untapped.
Modern platforms like Operations1 enable companies to standardize and accelerate changeover processes while making their workforce more agile—independent of staff shortages or individual expertise.
Now’s the time to modernize your setup process
Couldn't attend the webinar? Simply fill out the form and you will be taken to the complete webinar recording.
Anna-Karina Dawkins
Anna-Karina Dawkins is Team Lead Marketing at Operations1 and is your contact for press, social media and events. Before joining Operations1, Anna worked in marketing at SimPlan AG, a simulation service provider. Prior to that, Anna discovered her passion for marketing at Deutsche Tele Medien GmbH and while employed there, she completed her Bachelor in Business Administration at FOM in Frankfurt.