What it is about
In this blog article, we share with you our real-life experiences about the challenges of document management in the commissioning area. We intentionally take a focused look at the commissioning upstream process because there is often a high level of non-value added activities found here. We will cover other topics such as inefficient commissioning and record keeping in separate articles.
The following aspects are covered in this blog post:
- What are the current challenges in document management in commissioning?
- What are the solutions to these challenges?
- What are the benefits of digital document management with a Connected Worker Platform?
What are the current document management challenges in commissioning?
Those responsible for documents in the commissioning, quality assurance or work preparation departments encounter a wide variety of challenges when creating, updating, providing and managing commissioning documents:
Laborious creation of test reports, checklists, etc. in Word, Excel or PowerPoint Creating test documents for commissioning can be very time-consuming in MS Office: tables have to be readjusted manually, images have to be placed in the right position and scaled with several clicks. The insertion of images in particular can prove to be a complicating factor during creation. In addition, if several employees are working on documents, a uniform document style and structure can often only be established with an enormous amount of manual effort.
In order to avoid additional editing and formatting efforts, information is also presented by a lot of text and in a very imprecise, non-intuitive way, which later complicates the commissioning activities for the employees due to the complicated document.Inefficient paper handling by printing digital documents on paper This is where the first media break occurs: Digital documents become analog. Printing MS Office documents on paper not only incurs unnecessary costs, but also reduces flexibility in the process. If changes are made to digital documents at short notice, they have to be printed out again and obsolete paper documents have to be disposed of - resources and costs that could have been put to better use in other ways.
High manual effort for updating, checking as well as approving commissioning documents If work steps or information have to be updated in the existing Word, Excel or PowerPoint files, this can take up unnecessarily valuable time for reformatting the pages until the document is perfectly formatted again for printing on paper.
If the approval process still includes manual versioning, then old documents usually have to be saved separately in an archive folder so that changes can be traced back if necessary.
In addition, it should be mentioned that changes in documents are often not historically documented, so that editors cannot trace the further development of a document and change histories. In addition, if employees are not informed of updates in the document, this can lead to confusion, uncertainty and process instability for the executing employees.Time-consuming search and compilation of required commissioning documents in entire order folders It is often the responsibility of the work preparation staff to compile the correct documents for series- or customer-specific orders. In practice, this usually involves a great deal of searching and processing, as the correct documents are first searched for on the server, printed out on paper and filed together in folders. Before being handed over to the employee, the order folder or machine folders still have to be checked for completeness. If there is insufficient preparation time or if there are changes at short notice, stressful situations may arise for employees and the potential for errors in the compilation of documents increases.
Decentralized management of commissioning files on SharePoint or company server If a company has several company locations, "silo thinking" often still prevails when it comes to document management. If the company decides to manufacture similar machines and series in different plants, the manufacturing and commissioning processes must be carried out in the same way in order to achieve the same quality standards. If, for example, documents are not managed centrally from the company headquarters, but are maintained plant-specifically by each individual location, this often leads to unequal process standards and, in the worst case, to differences in quality.
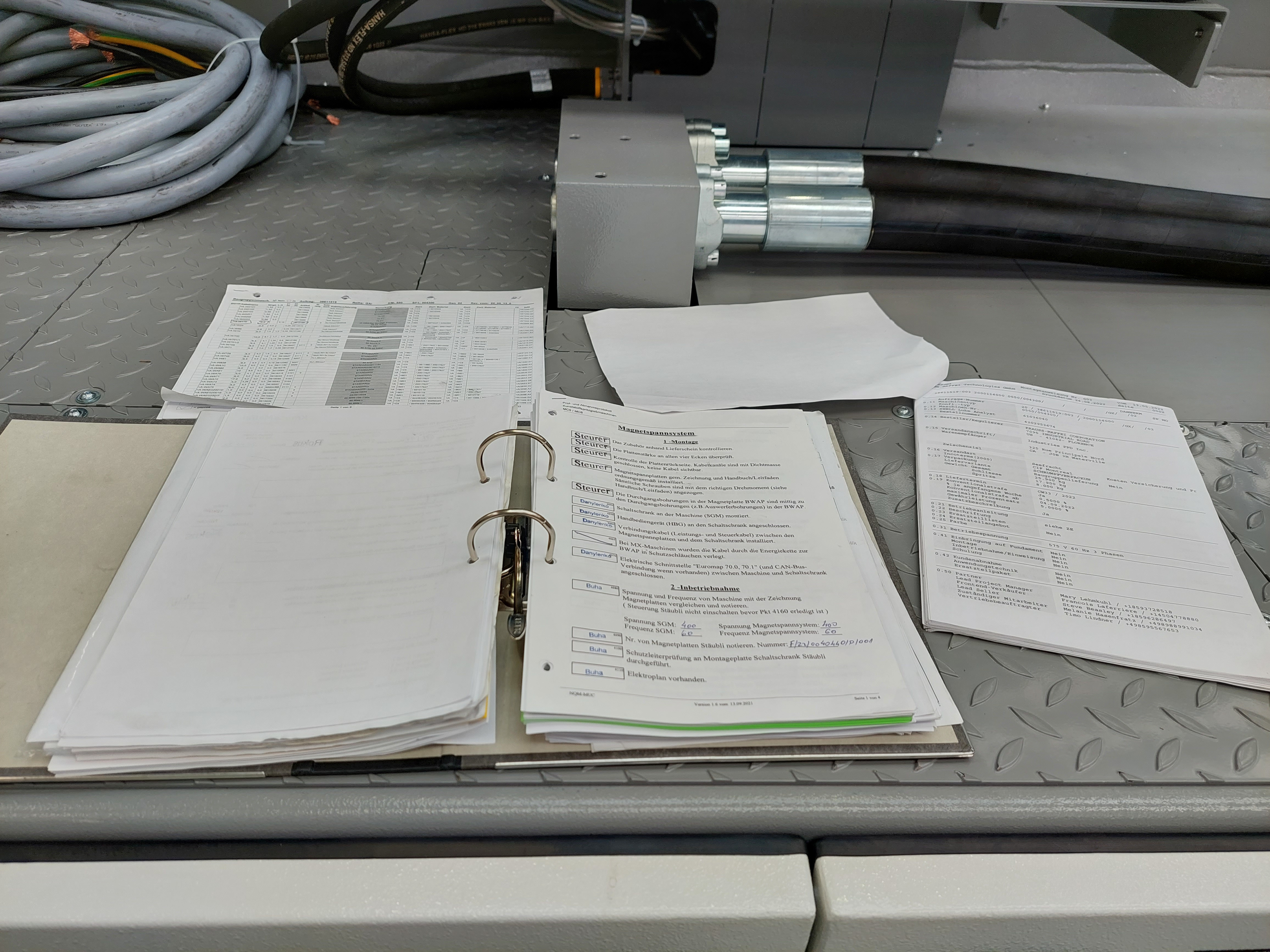
What are the possible solutions?
Digitizing the commissioning process with a Connected Worker platform can eliminate inefficiencies, media and system discontinuities, and data silos, and leverage tremendous improvement potential:
Easy creation of multimedia digital test protocols with drag & drop editor centrally in one software Compared to Word, Excel or PowerPoint files, an integrated editor in a Connected Worker Platform often dictates the design and document structure. In the specific example of Operations1, the document structure is based on many years of collaboration and continuous feedback interviews with customers. This ensures from the creation of a commissioning document that work steps are structured as well as clearly presented and that employees can easily consume the information presented.
Using drag & drop elements, work steps can be created quickly and easily and provided with a wide range of interactions such as IO confirmation, checkboxes, number feedbacks, multiple choice, free text fields etc. Above all, the inclusion or simple insertion of interactive media such as images and videos allows you to easily communicate complex content to employees. With the simple functionality of an integrated document editor, you have created an intuitive digital commissioning document with just a few clicks and media.
Avoiding media and system breaks By digitizing your document management, you primarily avoid printing on paper and save further printing and office supplies costs. This fact is not only very interesting for companies with environmental or sustainability goals, but also streamlines your processes by avoiding unnecessary administrative activities that occur in the paper-based process.
Direct assignment of work orders, tasks, and documents to employees via employee-individual dashboard Whereas with paper-based processes, employees on the shopfloor may have to search for the appropriate order folders themselves or be provided manually by the work preparation department, QA and AV can use a Connected Worker Platform to assign the orders and appropriate documents directly to employees. The orders are clearly displayed on a dashboard with order status and due date information. This means that employees know immediately which orders they have to complete and when, and can concentrate fully on executing the order and carrying out the commissioning.
Digital versioning of documents with integrated release process Series and machine specifications are subject to constant changes and adaptations in the context of product developments, changing customer requirements, etc. - as a result, commissioning documents are also affected. Whereas previous hybrid revision and release processes, consisting of MS Office and paper, proved to be very labor-intensive, a CWP, in contrast, offers an integrated release process. This is initiated even before documents are published by giving the editor the option of storing change notes, determining the version number logic and requesting approval by a supervisor or colleague. This not only ensures greater process reliability, but also greater release transparency, since, among other things, updates can be traced back through change notes in the historical document history.
Central document management of all commissioning documents If documents are maintained centrally in a software, not only a uniform format as well as design can be realized, but above all a central provision of documents. Structural classes such as location, department, machine, document type, etc. allow documents to be structured and organized very clearly right from the start. This not only supports findability in search functions, but also enables access authorizations to documents.
The possibility of establishing a uniform, global process standard for construction line-specific commissioning through standardized documents in the plant-specific national languages holds enormous potential for increasing quality and process efficiency.
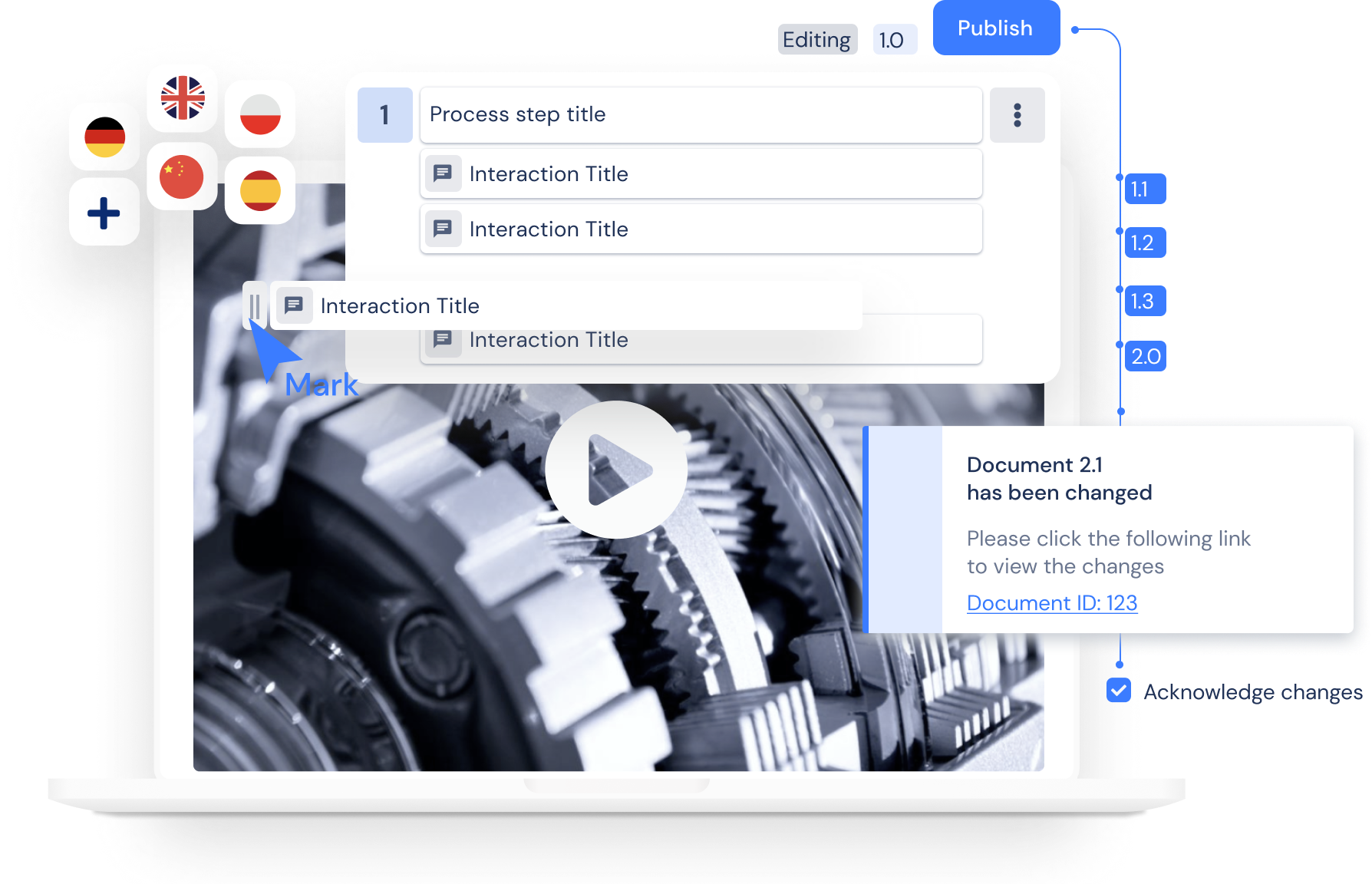
What are the benefits of digital document management?
Reduction of effort in the creation, updating, versioning and provision of commissioning documents
Avoidance of media and system discontinuities
Increase sustainability and avoid paper costs
Instead of data silos: One point of truth
Increase process stability in document management and delivery
Suppor for employees on the shopfloor
Establishment of a cross-departmental and cross-plant process and document standardization
Conclusion
Digitizing document management in commissioning with a Connected Worker Platform (CWP) eliminates many inconsistencies in the maintenance, management and provision of series-specific documents. A CWP offers a wide range of benefits to take your commissioning process to the next level as well as making it future-proof. By managing documents in one software, you can not only establish a single point of truth and a process standard across plants, but also strengthen your quality promise to your customers.
Digital commissioning is also relevant for you?
Simply fill out our contact form and share your goals and wishes with us. We will be happy to get back to you immediately and support you in implementing a digital commissioning approach.
Markus Glotzbach
During his professional career, Markus gained deep insights at companies and large groups in different industries and knows the digitalization hurdles and problems on the shopfloor. Before joining Operations1, he studied International Management (MA) and worked in the Cloud Computing as well as SaaS telematics sector.