"Operational staff must see digital technologies as partners": Interview with Bernd Hausler (ifm)
The fear that technology will curtail the frontline worker's job as it develops is widespread. However, if the requirement profile of operational employees shifts more towards conceptual activities in the coming decades, this fear is unfounded.
Bernd Hausler, Managing Director at ifm, the leading supplier of innovative automation technology, takes the clear view in an interview with CEO and Co-Founder Benjamin Brockmann: "For me, people will remain the focal point in production in the future."

What the interview is about
What will the role of the frontline worker look like in the next 10 years and what challenges will companies face? Benjamin Brockmann, CEO and Co-Founder of Operations1, discusses these and many other questions with Bernd Hausler.
Hausler is Managing Director at the ifm Company Group, a major and globally active supplier of automation technology systems and components for industrial companies. He is convinced that the digital factory will not put people in the background, but will support them much more in the future with the analysis of important data and correlations when making decisions.
A new role model will change the shopfloor
The following interview excerpt from the Operations1 podcast is about the connection between digital progress and an innovative corporate culture that never loses sight of the individual. The core of the interview excerpt is the question of how the role of the operational employee will change in the coming years in the face of advancing digitalization and how companies can best respond to this. You can listen to the full interview in the Future Proof Operations podcast.
Bernd, Industry 4.0 has been the topic par excellence in the manufacturing industry over the last few decades. Is that still the case, or have we moved on to something completely different in the meantime?
The slogan "Industry 4.0" is of course a very powerful marketing claim. In concrete terms, it primarily means digital optimization. And behind this stands for ifm the continuation of a digital journey that we successfully started years ago by means of lean management. However, to ensure that we can continue to hold our own in international competition in the future, we need imaginative digital tools. This is especially true in the competition with Eastern European countries and with Asia. Creative solutions are needed to achieve their cost-effectiveness in the future as well. That's why Industry 4.0 is more relevant to me personally today than ever before.
In 2020, you were honored by the "Factory of the Year" awards, which is one of the most prestigious industry competitions in Europe, in the category of securing locations through digitalization. What does this award mean to you and why are you particularly proud of it?
First of all, it was incredibly valuable to have our own daily business evaluated by the Kearney audit team from the outside. This external perspective is incredibly important and helpful, because it opens up horizons in a way that an internal perspective never can. In addition, it was very important for us to receive feedback that we are optimally positioned for the future. And last but not least, it was of course a very enriching experience for our employees to see that their work was valued by an impartial institution and to have it reflected to them that we are all working together on the right issues. If you want to continuously improve the corporate culture, I don't think it's enough to only give appreciative feedback internally. The perspective of appreciation from the outside is also an important basis for satisfaction.
What are these "right issues," as you call them, that you are working on?
First and foremost, working with Lean as the basis for continuous improvement of technical processes and as the foundation of the digital factory. In addition, we are pursuing the goal of remaining competitive with our sister groups in the ifm Group. This is especially important because we want to guarantee our employees at the headquarters here in Tettnang a secure job in the future as well.
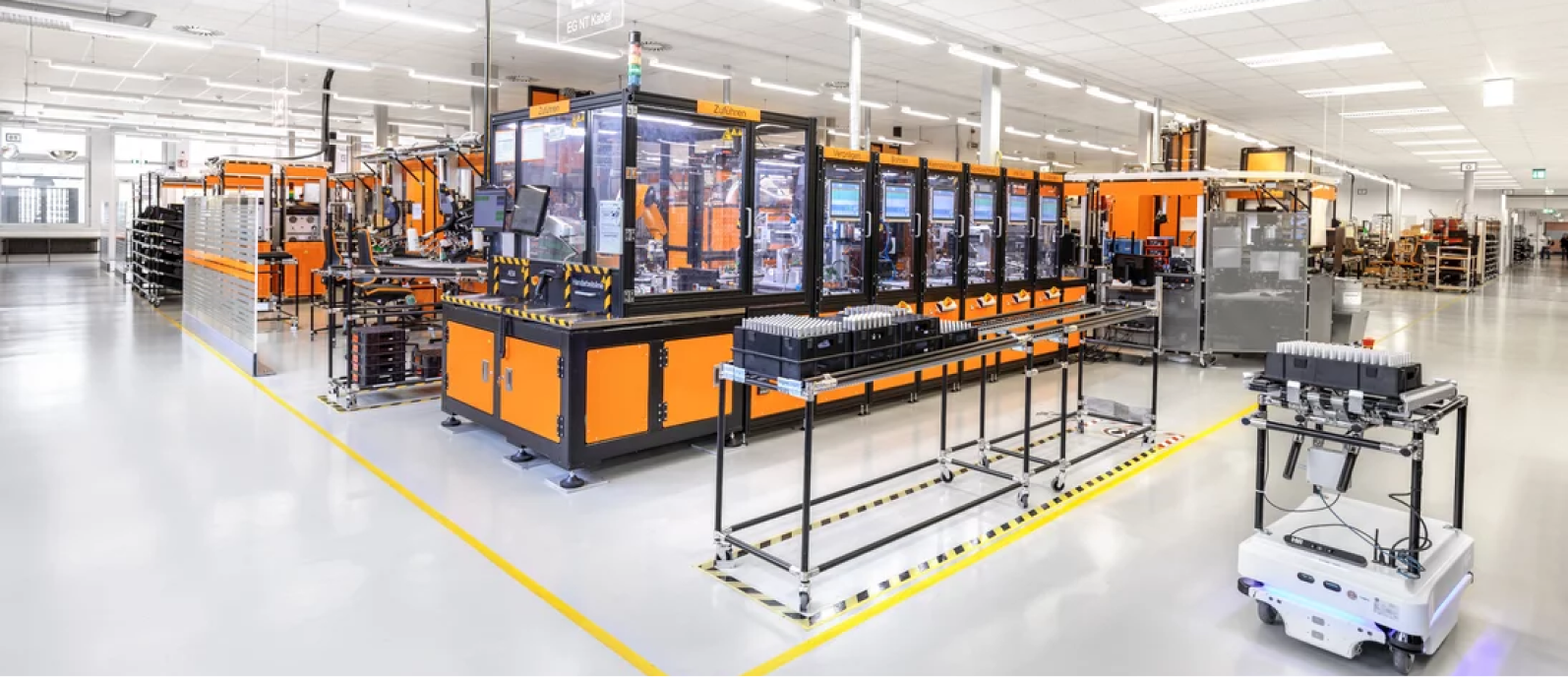
Digital technologies should not be used for surveillance
Can you give us a concrete example of how lean tools contribute to your digitization strategy?
A good example is our "ifm mate" worker assistance system, which makes knowledge quickly available and provides reliable support for individual work steps. Our employees prefer to use it for small series that are only produced for a short period of the year. So it's only understandable if a step is no longer 100 percent remembered. Technological support of this kind then provides enormous help and at the same time offers security. That's why an intelligent workplace will be so crucial in the future. However, the important thing is that digital tools are not misunderstood by operational employees as control instances. This attitude must be clearly exemplified by the company's management.
This brings up a key issue in connection with digital tools: The fine line between control and monitoring on the one hand and support and assistance on the other.
Exactly. Because if digital technologies are used with the aim of controlling and monitoring work performance, the workforce will not recognize them. For us, this is a very clear line from which we will not deviate in the future. We have also achieved significant successes with this approach, because it has been shown that digital tools, when used as an aid and understood as such by employees, have precisely this effect. It's not about monitoring productivity or other metrics. If the workforce is convinced of the importance and relevance of their own work and is provided with the right environment, they will also work profitably and produce at exactly the right rate so that the company remains competitive. This has been my constant experience in the past.
Freedom to develop is important
Based on this, let's take a closer look at the worker, using ifm as an example: What role do they currently play and what role will they play in the next 10 years in digitized production?
First of all, it is important to say something about the corporate culture, because the role of the frontline worker is based on this: The pillar of the corporate culture at ifm is, on the one hand, that we offer our employees the opportunity to identify with the company in the best possible way and, on the other hand, that we offer them great creative freedom.
How can we imagine this in practice?
The corporate culture of the ifm family essentially lives from uniform standards worldwide. This means, for example, that no matter in which of our plants our employees are, the environment always looks visually the same, recognizable by our workbenches, which are orange and black. This means that there is no feeling of foreignness at all, because people feel directly at home at all locations and can dock on to familiar things. Another characteristic of our "orange blood," as I call it, is that each of our employees is supported in his or her personal development and is given the feeling of being a valuable and irreplaceable member of the company. For example, if you start as a production employee, enjoy your job and want to develop further, you can work your way up to the development department. Creativity and the joy of innovation are therefore very important to us. These opportunities for further development are unique in this form and make working at ifm so special. As far as the role of the worker is concerned, in my experience it is very important that the human being always remains in focus. For me, he was and is the center of production. That's why the digital factory doesn't put him in the background, but rather supports him with the analysis of important data and contexts for decisions.
The frontline worker of the future
Do you think there will be a shift in the coming years? What role will the operational employee play when technology is even more sophisticated than it is today?
It will be crucial for the operational employee of the future to have a technical understanding and be willing to constantly develop it. Today, the complex volumes of data supplied by digital tools often still have the air of something mystical because the employee cannot see what processes are behind them in concrete terms. This must change in the future, and operational employees must be able to provide sound feedback on technological processes and assess which digital tools are smart and really help them in their daily work. In addition to this technological knowledge and the willingness to learn continuously, the understanding of digital tools must change quite significantly. Away from the fear that they could curtail the worker's job or even make it unnecessary, and towards supporting and supplementing their own work performance. Operational employees must therefore view digital technologies much more as partners in the future. This is a crucial change in awareness that companies should master in the coming years if they want to remain fit for the future and support their employees in the best possible way.
What is your vision of the factory of the future? What will it look like in 10 years?
Increasing automation on the one hand, and an even closer intermeshing of man and machine on an equal footing on the other. In other words, the digital tools that already surround me at home as a matter of course in the form of Alexa & Co. and make my everyday life easier will also surround me at work. In concrete terms, the workbench gives me instructions and supports me in my daily work in a very targeted way. As a result, the way I work is much more efficient, faster and also more cost-effective, while maintaining the same high quality.
You can listen to the complete interview in our Future Proof Operations podcast.
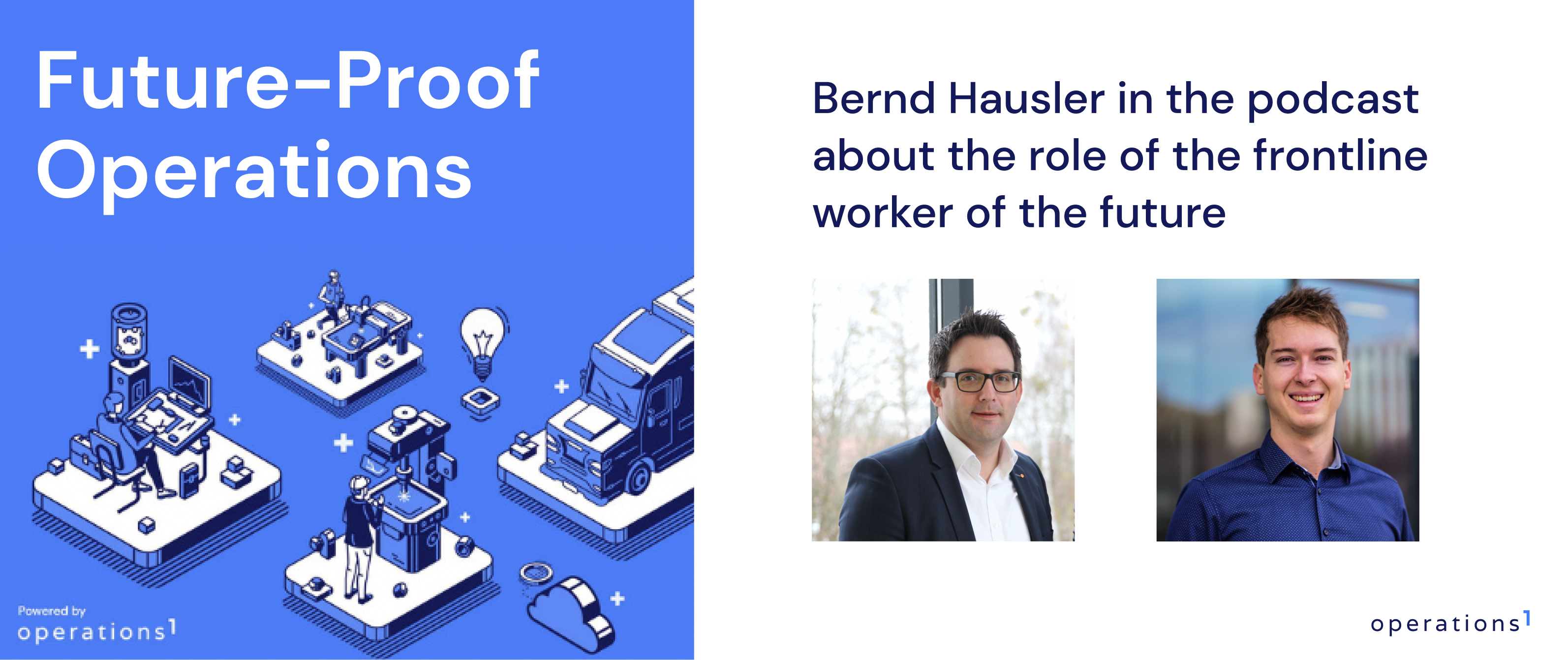
Benjamin Brockmann
Benjamin Brockmann (M. Sc., Management & Technology) founded Operations1 in 2017 together with Daniel Grobe (also M. Sc., Management & Technology). The founders developed the software solution based on various practical projects, including at the Fraunhofer Institute, and on their experience in industry, auditing and management consulting. Benjamin Brockmann has already worked for companies such as KPMG and Arthur D. Little.