What it's about
In this article, you'll learn what a check sheet is, its role in quality control, and its advantages and disadvantages. We will also show how to avoid common sources of errors of static error collection cards with the use of Operations1 software.
Check sheet as part of the seven quality tools
As a tool for failure recording, the check sheet also fits into the seven quality tools compiled by the Japanese Kooru Ishikawa. He selected them for the handling of quality problems in business processes. Today, they are used in quality management, more specifically in quality circles such as the PDCA cycle (Plan-Do-Control-Act), and help companies with quality assurance. The aim of the tools is to collect failures and data from workflows and processes by quality control inspectors and then analyze them as simply as possible. Depending on their usefulness, the tools can be divided into the areas of failure recording (check sheets, histograms and control charts) and failure analysis (Pareto diagram flow chart, correlation diagram and cause-effect diagram).
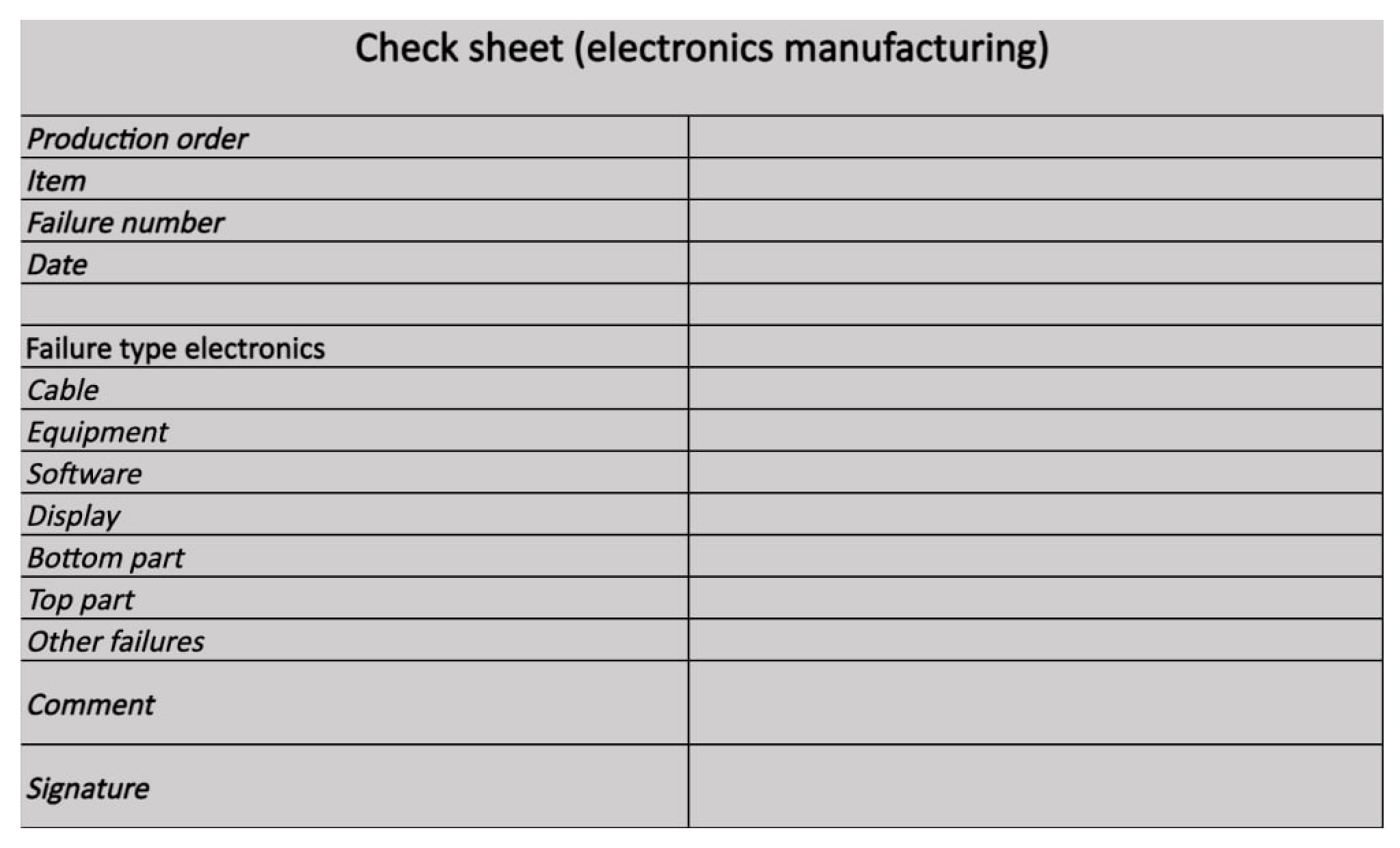
The advantages and disadvantages of the check sheet
The control check sheet brings some advantages that speak for the application of this quality tool. On the one hand, the check sheet can be used quickly on site for the current and temporary collection of data that functions as a basis for analysis later on. On the other hand, the data can be recorded not only for technical process sequences but also for services and administrative processes. One disadvantage, however, is that if data is to be collected at previously unfamiliar or atypical locations, data quality and thus evaluation can suffer, e.g., due to forgetting or late completion. Challenges and difficulties such as these occur primarily in connection with the paper-based, static check sheet that is created in Microsoft Excel, printed out and filled in by hand on the shop floor.
Pain Points: Disadvantages of a static check sheet
The check sheet refers, as already mentioned, to the frequency of failures. It is usually presented as a table in which, on the one hand, the failure designations and, on the other hand, the frequencies of the respective failures are listed or collected. Basically, the work with the quality tool Excel check sheet is easy to implement and not very time-consuming. Instruction is hardly necessary due to the easy comprehensibility. The disadvantages and challenges rather lie in the next step. In the paper-based and static version, the check sheet is isolated and stand-alone. The inspection sheet, which is created by hand, is often filled out by employees by hand in the process. This reveals the number of defects, but an overarching analysis of the causes in connection with the noted failure count involves immense manual effort for data transfer to the digital world. This means that the Excel check sheet, as a significant effort driver, can only fulfill its original purpose to a limited extent. Temporary blind spots are created in quality inspection: due to a lack of transparency and traceability, CIP can only be driven slowly or delayed.
Objective: Potential of a check sheet
As a tool for process optimization, the check sheet requires easy and immediate evaluability. This is the only way to fulfill the purpose of the inspection sheet for quality assurance. Paper-based quality tools are simply not integrated and cause additional delays in the definition of quality measures due to manual efforts in the transfer of data. The “isolation” and separation of static check sheets from the system landscape of companies can be solved easily: through state-of-the-art technologies that ban paper from the shop floor on the one hand and overcome manual data transfer efforts on the other hand – through full integrability, dynamics and flexibility.
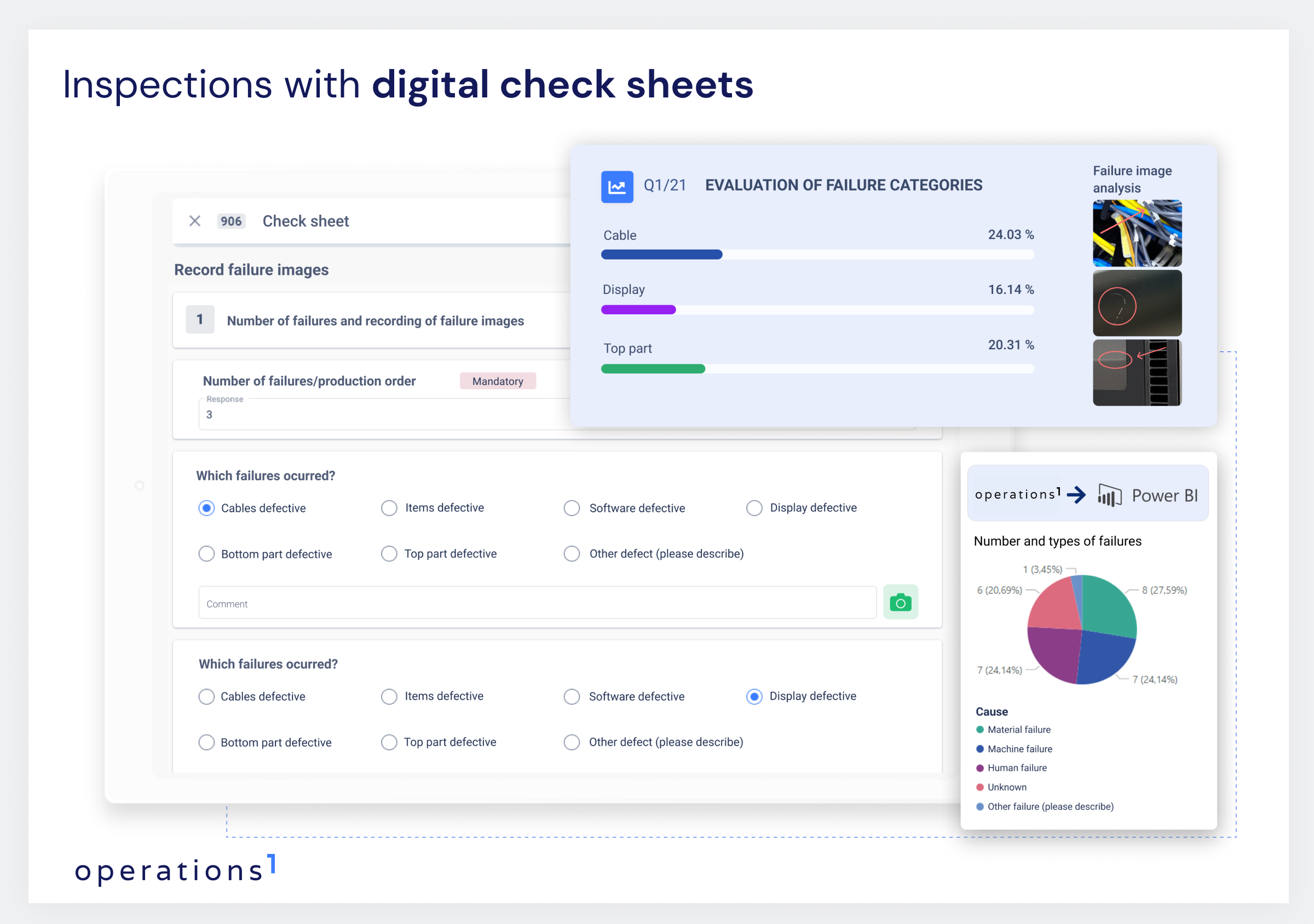
Digital check sheet: interactive, dynamic, informative
Checks with software-based check sheets not only simplify work for employees in process execution. Beyond that, the analysis and evaluation of the transferred data from the process can be enriched with additional information and be executed without delay.
How Digital Check Sheets Work in a Software?
1. select production order
2. enter total number of failures
3. select a type and a cause for each failure
4. if required, take a photo of the findings directly, edit it on site and comment on it
5. analyze failure types and causes after completion of the job
6. benchmark failure statistics across products, shifts, etc.
The worker conducting the quality control check first selects the production order on the tablet, laptop or smartphone. The measured failure number by the quality inspector automatically triggers a selection of possible failure types, for which images can be easily and quickly captured, measured values returned and comments added. Quality findings are thus recorded in real time. Quality managers can access the results of inspections across sites ad hoc in the live dashboard, analyze them and, if necessary, react immediately. In case of findings, quality managers are permanently able to act and problems are solved faster.
Conclusion: A static inspection sheet becomes an integrated quality tool
When implementing the check sheet with Operations1, the input of all failure-related information of the respective production order can be evaluated in real time via the analysis dashboard. An export of all generated data to Power BI is also possible automatically. By that, failure types are matched with failure causes and can be discussed in comprehensive comparative analyses. Non-value-adding steps such as manual transfers of data or media are eliminated. The potential can be fully leveraged thanks to the digital check sheet. Failure rates can be fundamentally reduced. Thus, the digital check sheet represents an important pillar of effective and dynamic failure management. A simple step towards continuous improvement through a powerful, digital as well as simple quality tool.
You would like to digitise your check sheets?
We look forward to hearing from you via the contact form. We would be happy to advise you on the introduction of digital checklists, test protocols, check sheets and many other documents.
Editha Bertsch
Editha is an experienced project management expert for manufacturing companies. With a clear understanding of the specific challenges of the industry, she is passionate about developing innovative solutions.