High quality and in-time delivery of customer-specific machines
Provide your production staff with easy-to-understand process knowledge. This allows your employees to meet the specific requirements of your customers and deliver the machines on time.
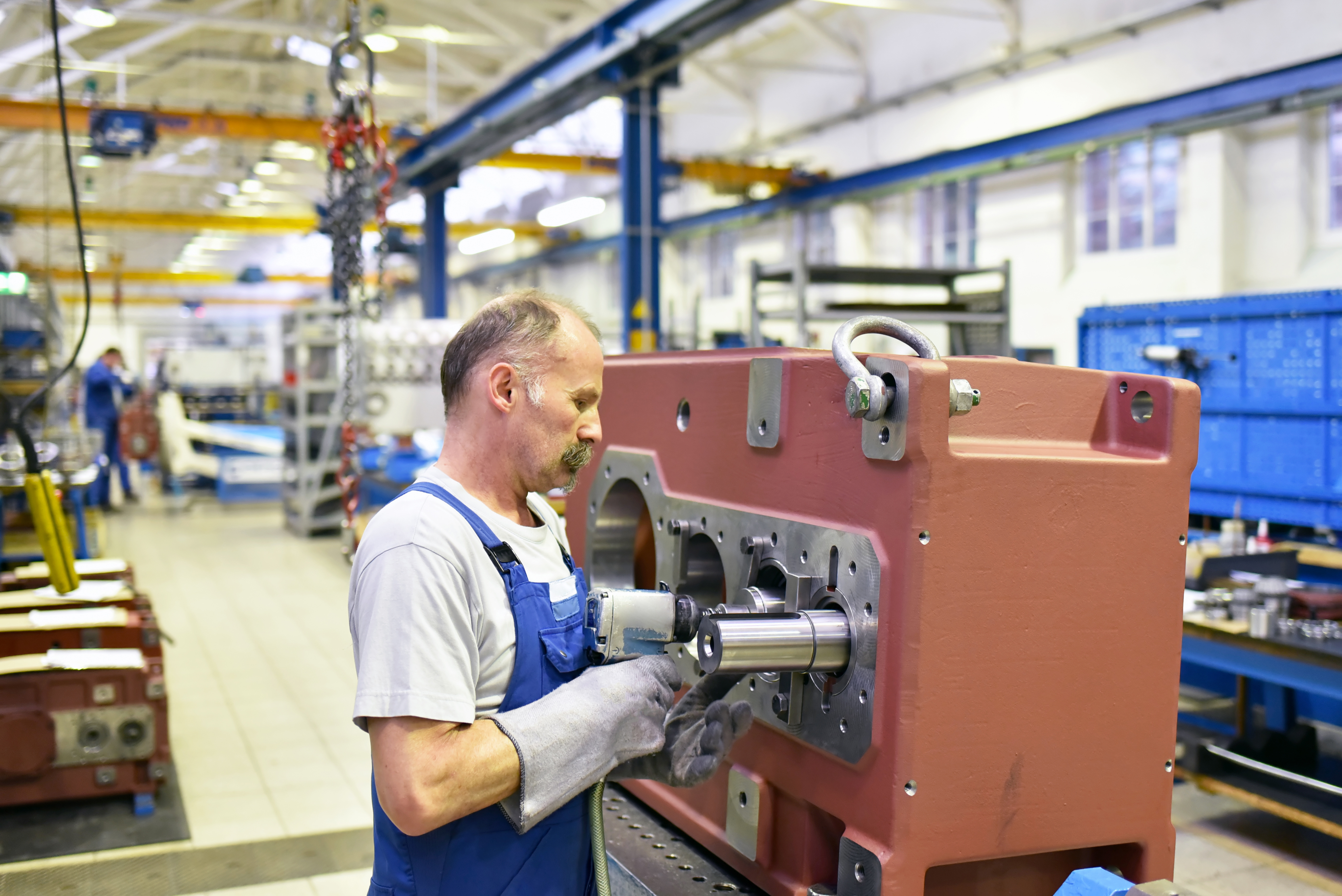
Strengthen your production for the next generation
Increased competitiveness
Avoid unnecessary costs due to unplanned service calls, rework or scrap. Increase your adherence to deadlines and delivery quality through continuously improved processes.
Focus on value creation
Understandable information in digital work instructions makes it easier for your employees to carry out tasks efficiently.
Cross-location quality standards
With Operations1, you can ensure standardized processes and globally uniform quality despite a high product variety and multiple locations.
High yield work through faster training
Whether by image, video or simple process description: provide your employees with the relevant information in an easy-to-understand way. Free up the time of your experienced colleagues and speed up the training of the newcomers.
Easy-to-understand information provision
Mentor relief through more independent training
Reduction of training time by up to -67%
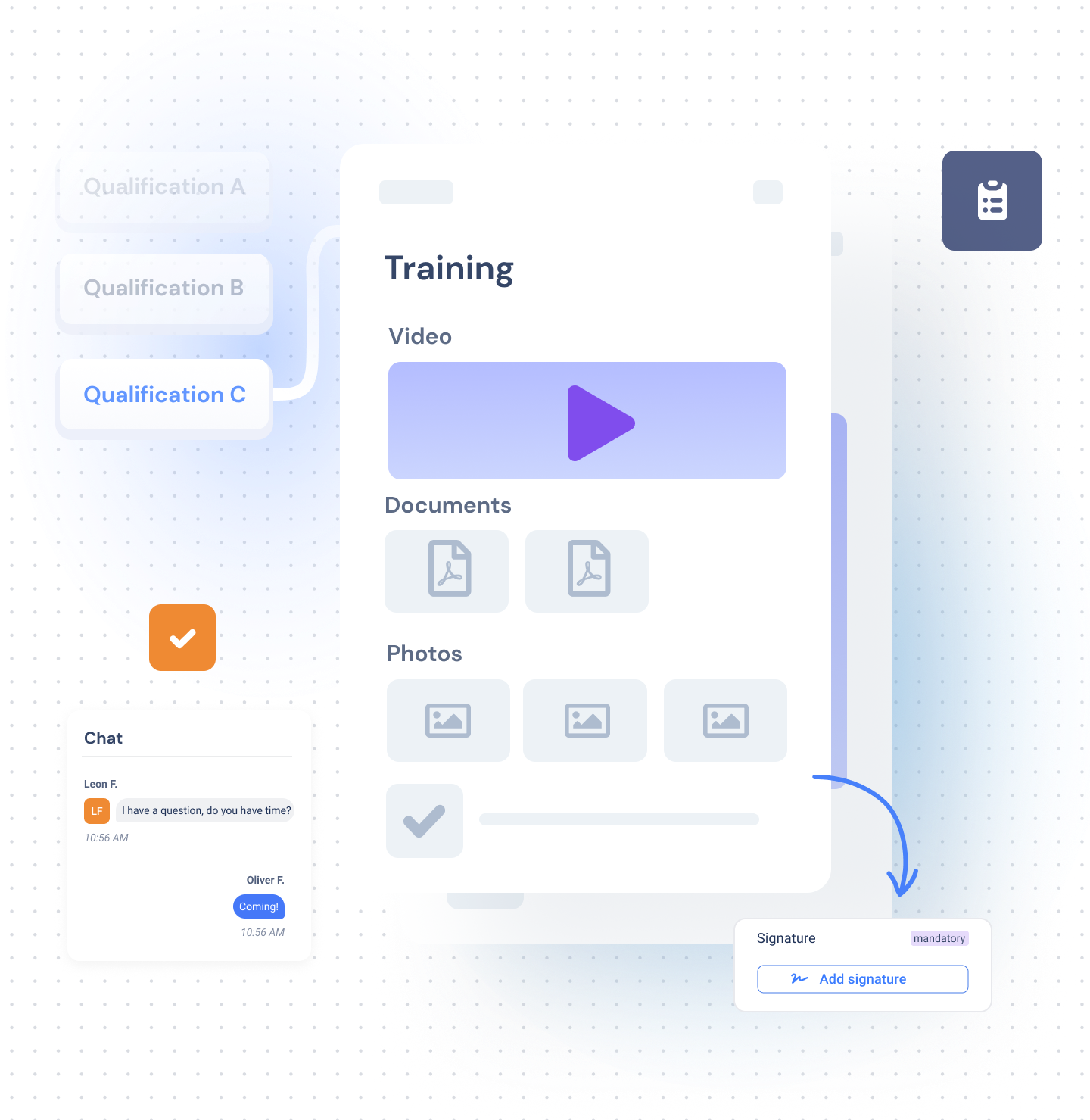
Assembly as reliable as your machines
Modular documents make it easier for your employees to assemble variant-specific products. In digital work instructions, customer-specific information is communicated directly to your employees. This increases process reliability and reduces the potential for errors within assembly steps.
Understandable information through variant-specific instructions
Error reduction of up to -25%
Complete documentation of the assembly steps
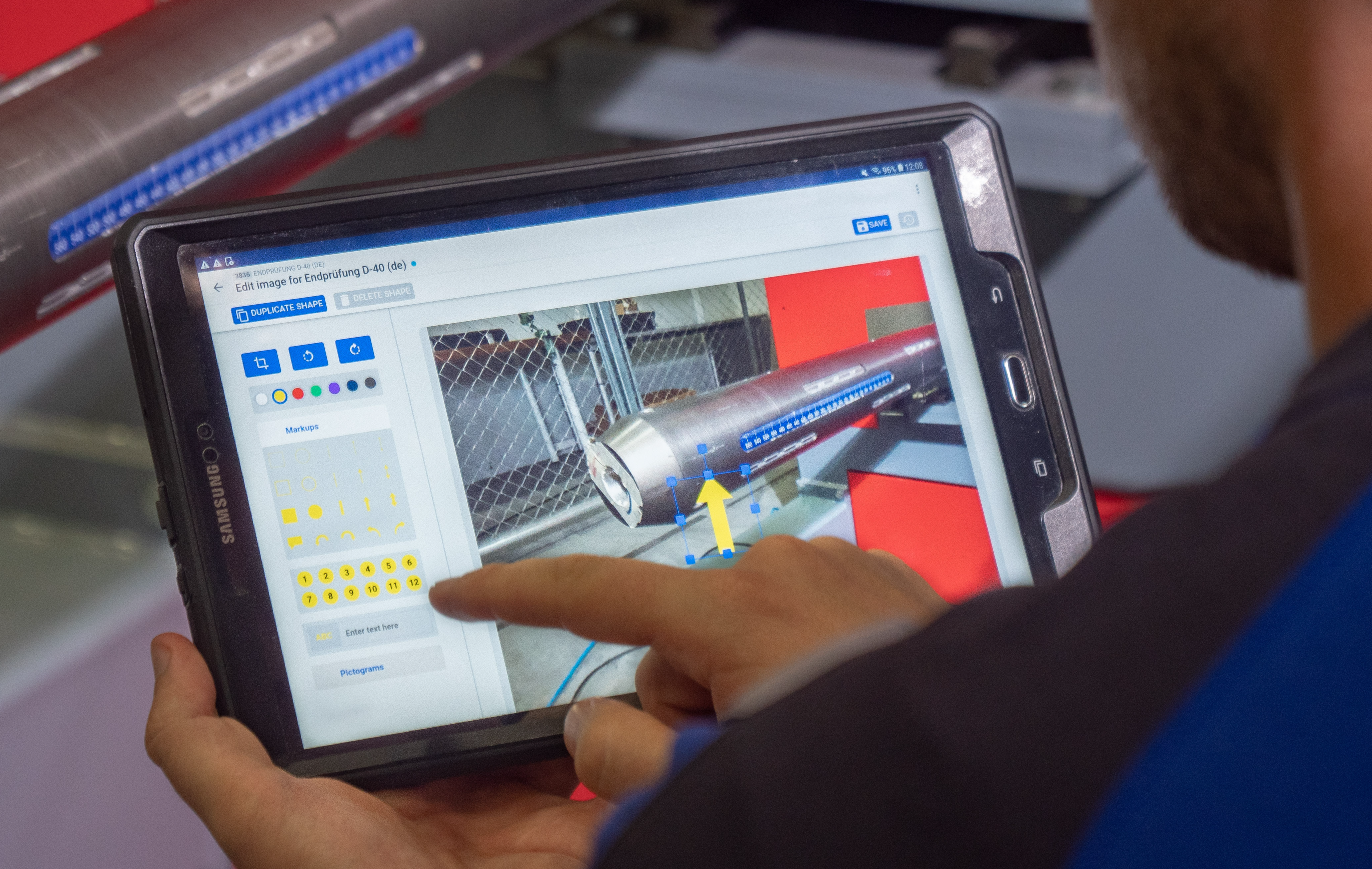
High quality fully documented
Digital checklists make it even easier to document processes from assembly to quality and shipping. Recorded test values, serial numbers and photos can be quickly traced in the software.
Increased adherence reliability for flawless tests
Enormously reduced documentation effort through digital reports
Up to -75% effort for research and tracing
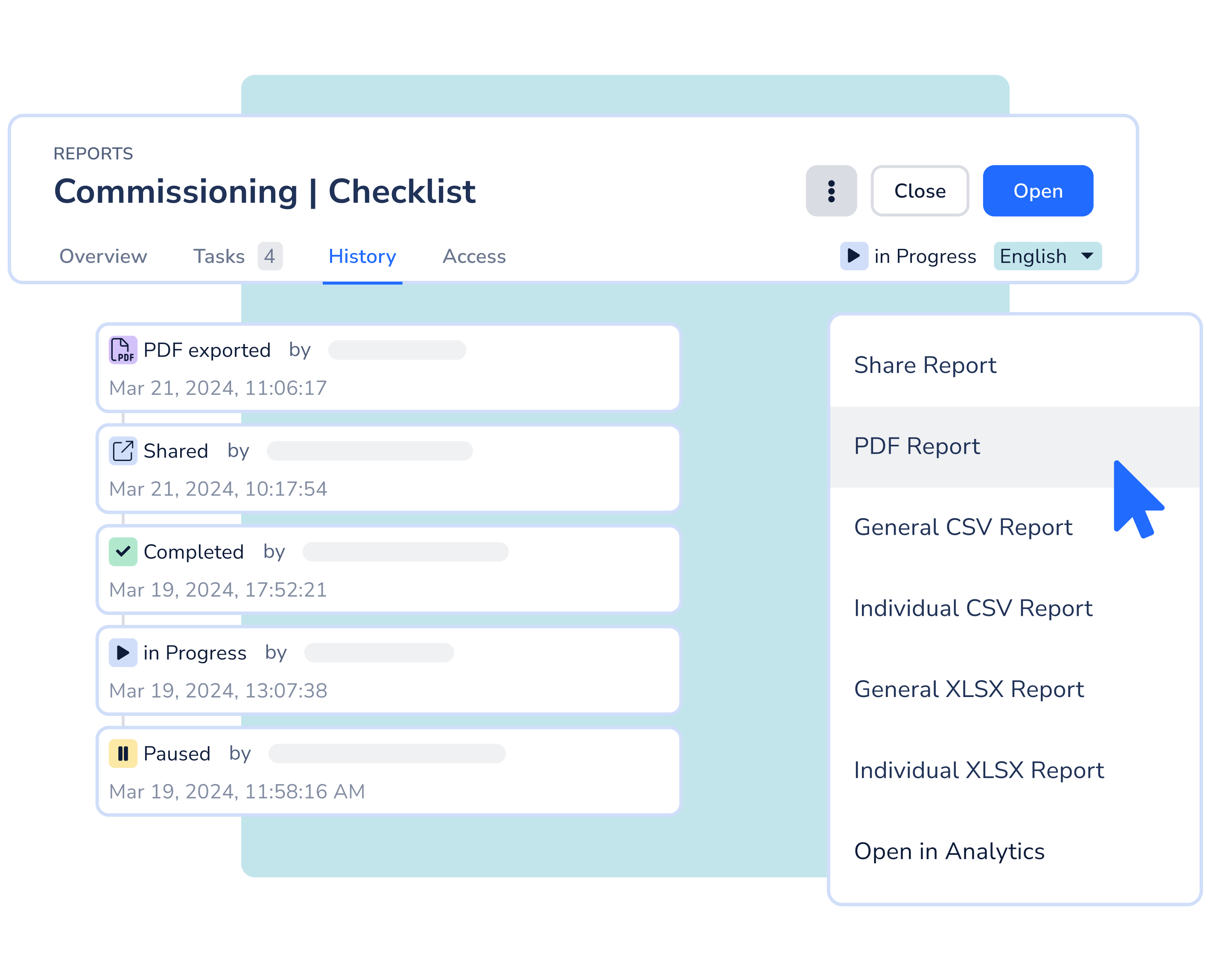
How other premium manufacturers benefit from Operations1
Soudronic
180,000 € savings per year and increase in process reliability
BWF Profiles
Gain of +80% time savings and 50% quality control efficiency
KraussMaffei
-67% documentation effort and savings of 1,200 working hours per year
POLIPOL
-67% shorter training time and savings of €2.2 million per year
Brückner Maschinenbau
Savings of 2,000 hours of travel time and +13% increase in employee productivity
Nabertherm
Strengthening quality assurance and reducing the effort involved in generating test reports
Schedule a meeting
Use the exchange with our product experts to find out how you can benefit from Operations1.
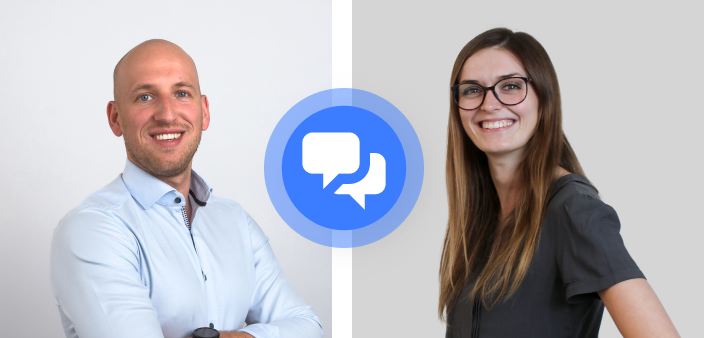
Fill out the form and we will get back to you in a short time.