What it's about
In the live webinar, which took place in German on November 14, 2023, webinar participants were able to find out the following information:
· Which topics are currently occupying machine and plant manufacturers
· How to benefit from the holistic digitalization of quality control processes
· How to digitalize employee-managed and quality-specific activities along the value chain
· How to reduce non-value-adding efforts and complexities and implement seamless documentation and simple verification management
This recap takes a look at the content of the previous webinar and addresses the challenges and possible solutions for machine and plant manufacturers.
High cost pressure and an increased shortage of skilled workers characterize the market environment
The speakers, Editha Bertsch and Stefan Philipp, began the webinar by presenting the current challenges that characterize the market environment in mechanical engineering. Not only the trade press, the personal exchange at this year's German Maschinenbau-Gipfel in Berlin, but also the regular discussions with customers highlighted the following two challenges: the high cost pressure and the increasing shortage of skilled workers.
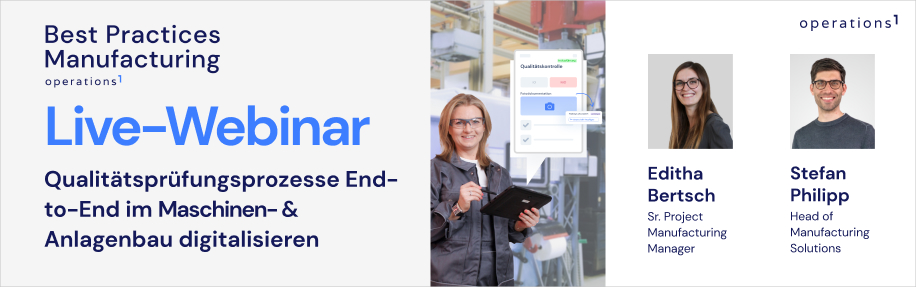
In the context of international competition, inflation and high resource and energy costs, machine and system manufacturers must pay particular attention to the various cost aspects - whether these are process costs, personnel costs or warranty costs. In the context of quality control processes, the objective is to reduce costs by avoiding errors within the process chain and the resulting consequential costs at an early stage through possible recalls or warranty claims.
Quality affects the entire value chain
Although the quality awareness exists, the actual assurance of quality is only seen in the final quality inspection. Quality is an issue for the entire value chain:
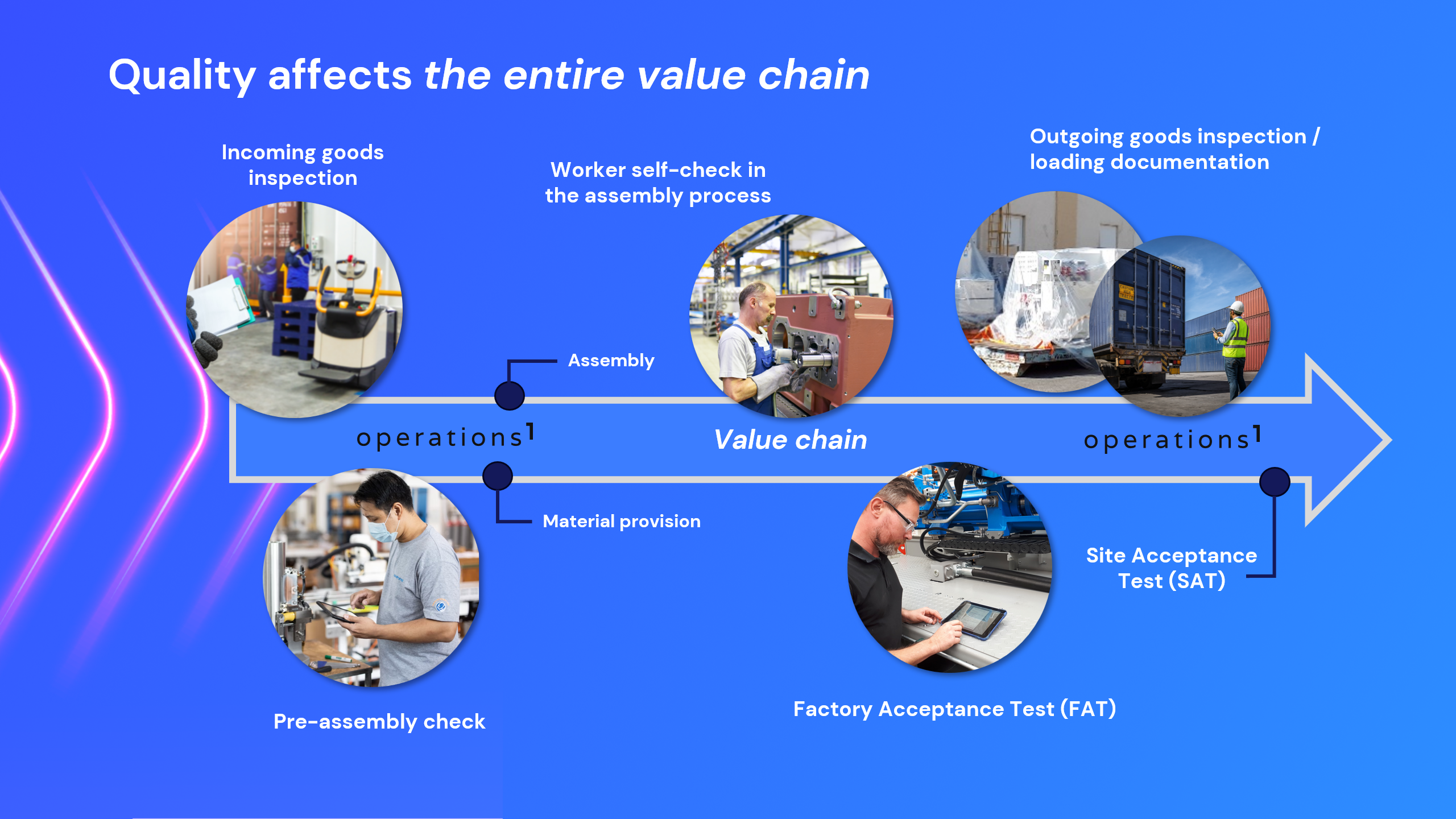
Incoming goods inspection: Employees can use the digital solution to identify errors in incoming goods at an early stage and document them professionally using photos. This documentation then helps to transparently prove delivery errors or problems to suppliers.
Pre-assembly check: Small components - big impact: If faults are detected and documented at an early stage during component assembly, these faulty components cannot be incorporated into the overall machine and, in the worst case, lead to rework, recalls or warranty costs.
Worker self-check in the assembly process: Employees can also ensure transparent documentation and error picture capture here. Errors found in this process step can also be communicated to upstream departments if they are responsible for the errors.
Factory acceptance test / final test: The functionality test or factory acceptance of the machine or system can be fully documented for the customer using digital commissioning or digital final inspections.
Outgoing goods inspection / shipment documentation: With the help of video and image documentation, machine and plant manufacturers receive sound evidence in the event of customer inquiries or complaints that the machines were handed over to the carrier in perfect packaging and that any damage must have occurred during transportation.
Site Acceptance Test: If commissioning is carried out on site at the customer's premises, it can also be proven in the event of warranty claims by the customer through complete documentation that the fault was not caused by the manufacturer.
Flexibilization of employees
By digitizing employee-led processes and introducing digital control protocols and digital test instructions, machine and system manufacturers can contribute to several factors:
Where paper-based instructions often present information that is too complex for employees, digital inspection instructions can communicate complex issues very simply by integrating explanatory videos and images. This can reduce the training time for new employees by up to 40% and relieve the burden on instructing supervisors: Due to the easy-to-understand step-by-step instructions, they do not have to continuously take care of the new employees, but only have to be available in case of questions or problems. Mandatory checkpoints within the digital inspection instructions also ensure process compliance and a uniform standard for quality checks.
Manufacturing companies also report that they can deploy employees more flexibly thanks to intuitive inspection instructions and inspection checklists - especially where they are needed to "get the machine or plant to the customer" due to staff shortages.
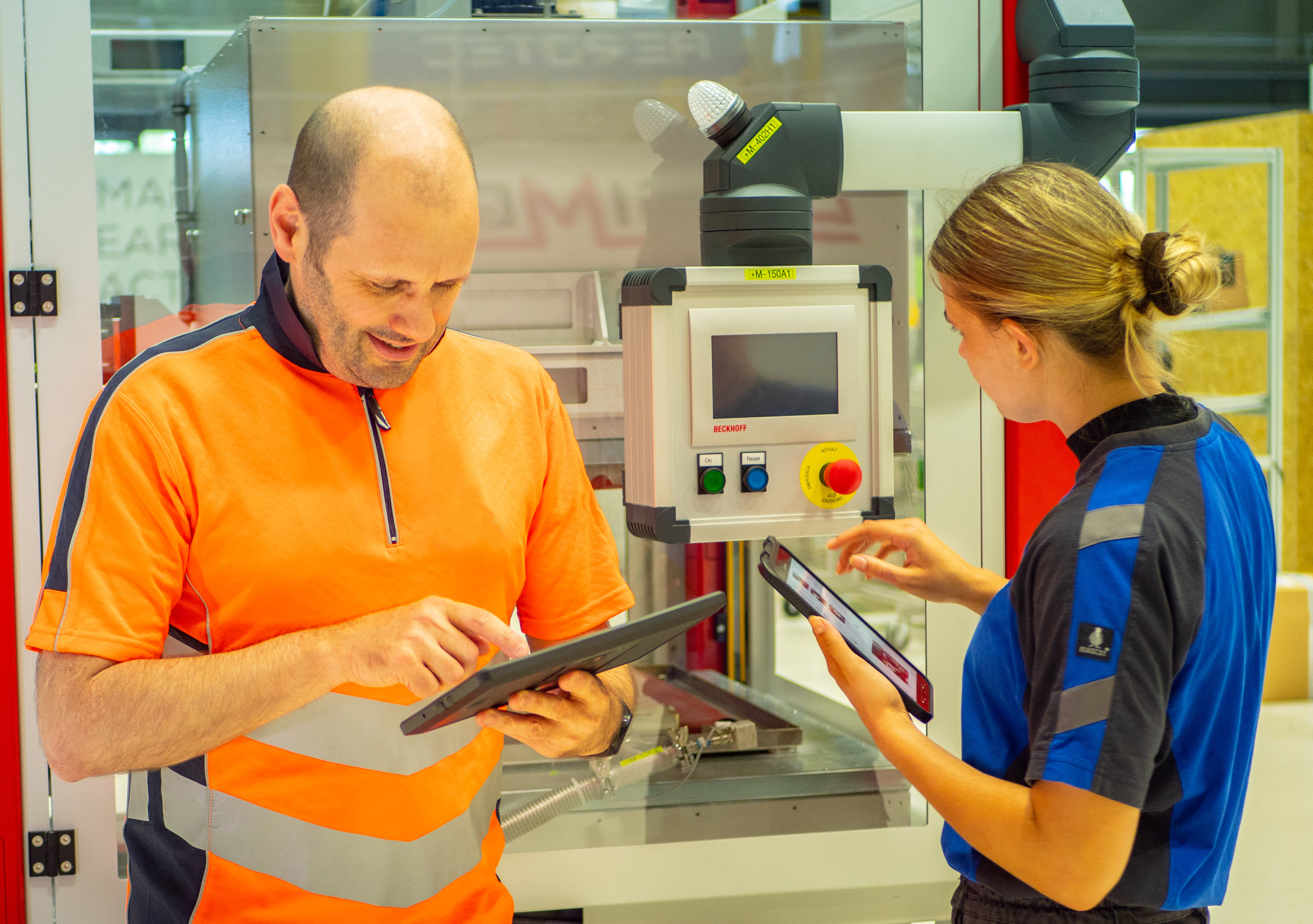
Strengthening quality leadership
The digitalization of employee-led quality inspection processes through a Connected Worker platform can help machine and plant manufacturers to achieve quality assurance and strengthen their quality leadership in various aspects:
Administering document management at a central point of truth and thus centrally for several locations enables processes to be standardized for all production areas: One standardized digital instruction in multiple languages for multiple locations. This allows manufacturers to ensure that the quality standard is the same at every production site.
By integrating conditions and mandatory work steps, process reliability and process stability can also be strengthened in the long term. Errors that occur due to employee habits or carelessness can thus be eliminated. In addition, the documentation quality can be raised to the same level through mandatory interactions and work steps that are displayed depending on the condition: If an error or deviation occurs during an inspection, the digital control instruction can oblige the employee to document the error using video or images.

Thanks to the image documentation directly in the digital checklist, professional error image analyses can be carried out to rectify problems and improve the process and quality.
One of the most important aspects for machine and plant manufacturers is the complete digital documentation of the activities and checks carried out: Automatically generated reports can not only be used for efficient verification in the event of customer inquiries, but can also be shared with customers, for example as a PDF file, as transparent evidence of a properly performed assembly and quality control.
Conclusion
The digitalization of employee-led processes is and will become more and more important for manufacturing companies. The choice of the right software for end-to-end digitalization is a decisive factor in mastering the current challenges in the manufacturing environment and in employee-led processes. When selecting a Connected Worker platform or a CAQ system (Computer-Aided Quality Assurance), there is often a debate. CAQ systems are very well suited to the tasks for which they are intended: The acquisition and evaluation of large collections of measured values. However, as they do not focus on the employee and the instruction aspect, they are only of limited use for employee-led processes, such as the reliable and intuitive execution of quality inspections.
Markus Glotzbach
During his professional career, Markus gained deep insights at companies and large groups in different industries and knows the digitalization hurdles and problems on the shopfloor. Before joining Operations1, he studied International Management (MA) and worked in the Cloud Computing as well as SaaS telematics sector.