Worum es geht
In diesem Blogartikel erläutern wir den Mehrwert einer digitalen präventiven Instandhaltungsstrategie auf dem Shopfloor.
Folgende Fragen werden im Blogbeitrag behandelt:
- Was ist präventive Instandhaltung, welche Instandhaltungskonzepte gibt es und welche Formen von präventiver Instandhaltung lassen sich unterscheiden?
- Welche Vor- und Nachteile hat präventive Instandhaltung und welche Umsetzungstipps helfen?
- Welche Nachteile hat ein papierbasiertes präventives Instandhaltungsmanagement?
- Digitale präventive Instandhaltung als Schlüssel zu höherer Produktivität
Was ist präventive Instandhaltung?
Die Produktion ist das Herzstück der Fertigungsbranche. Darum sind Ausfälle und Störungen an der Maschine ebenso wie ungeplante Instandhaltungsmaßnahmen ein Worst-Case-Szenario, das es zu vermeiden gilt. Der Instandhaltung kommt somit eine besondere Rolle bei der nachhaltigen Effektivitäts- und Produktivitätssteigerung zu.
Bei der so genannten „präventiven“ oder „vorbeugenden Instandhaltung“ werden Instandhaltungstätigkeiten durchgeführt, bevor es zu Anlagefehlern oder Ausfällen kommt. Dadurch sollen Maschinenausfälle vermieden und Instandhaltungskosten für Reparatur oder Ersatzteile möglichst niedrig gehalten werden. Zu Maßnahmen der präventiven Instandhaltung zählen beispielsweise Inspektion und Wartung, vorbeugende Reparatur oder vorbeugender Austausch und sonstige vorbeugende Maßnahmen.
In einem größeren Zusammenhang betrachtet ist präventive Instandhaltung die dritte von insgesamt acht Säulen von Total Productive Maintenance (TPM). Bezeichnet wird damit ein Konzept in der Instandhaltung, das darauf abzielt, die Anlageneffektivität und die Lebensdauer der Anlagen zu steigern und so ein möglichst störungsfreies Produktionssystem zu realisieren. Durch eine wirkungsoptimierte, kostenoptimale Instandhaltung sollen Verluste und Verschwendung eliminiert werden, so dass „Null-Defekte“, „Null-Ausfälle“, „Null-Unfälle“ und „100 Prozent Qualität“ sichergestellt werden.
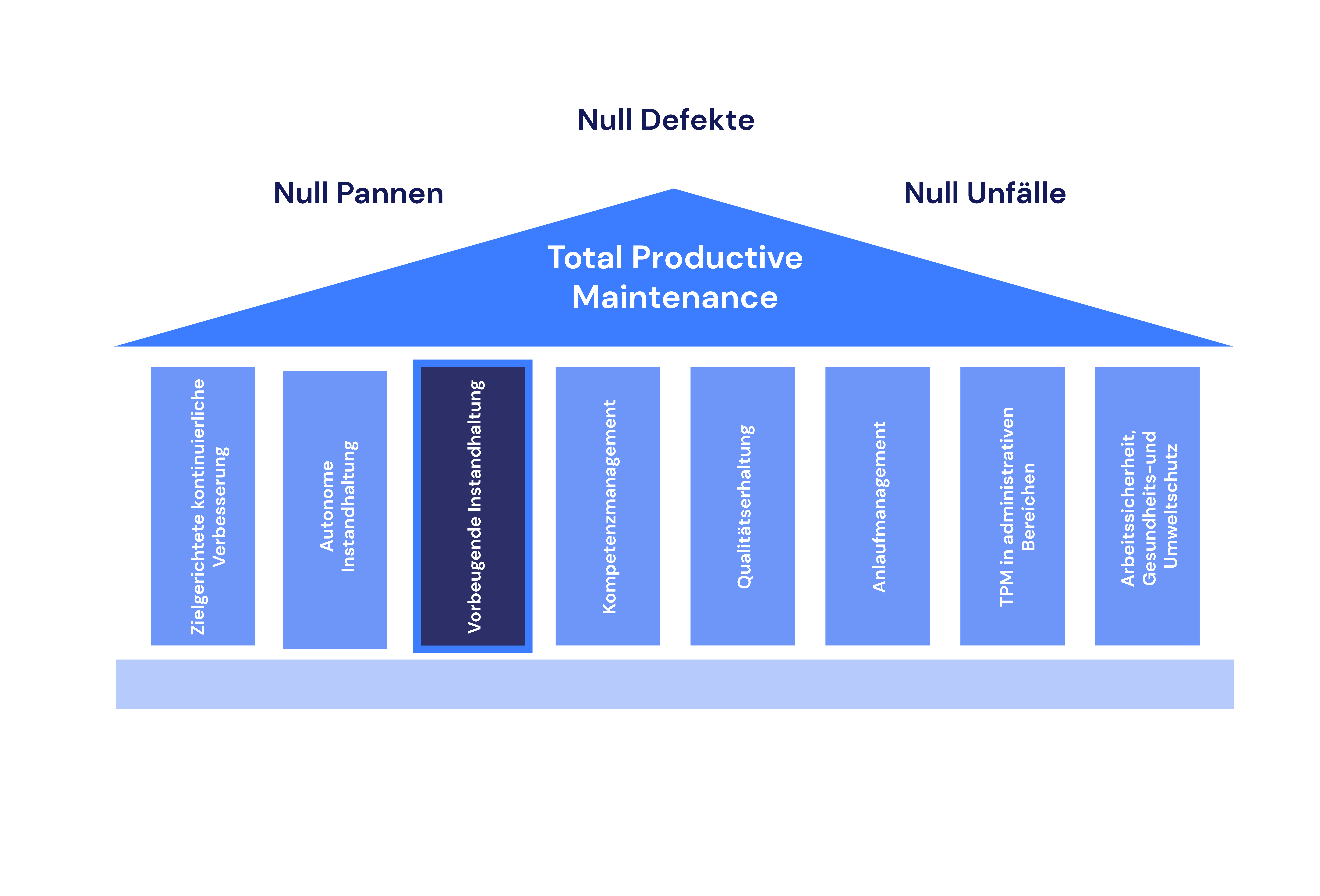
Detaillierte Informationen zum Konzept von TPM, ihren Ursprüngen, den unterschiedlichen Aktionsfeldern sowie Vor- und Nachteilen, der Einführung und digitaler TPM gibt unser Blogbeitrag.
Formen der präventiven Instandhaltung
Präventive Instandhaltung unterteilt sich in zwei verschiedene Formen, die in jeweils unterschiedlichen Bereichen Anwendung finden: die periodische Instandhaltung und die zustandsorientierte Instandhaltung. Die periodische Instandhaltung basiert auf Wartungen nach Wartungskalender mit Intervallen nach Herstellervorgaben und/oder Erfahrungswerten. Sie kommt vor allem bei Maschinen zum Einsatz, die kostengünstig ersetzt und repariert werden können und bei solchen, die selten ausfallen.
Wie der Name bereits sagt, überprüft die zustandsorientierte Instandhaltung zusätzlich zu den geplanten Wartungen wie bei der periodischen Instandhaltung die Zustände der Maschinen. Ziel ist es hierbei, Fehlerquellen rechtzeitig zu entdecken und zu eliminieren. Dies wird entweder über regelmäßige Inspektionen realisiert oder mittels kontinuierlicher Messung und Erfassung von Parametern wie Geschwindigkeit, Lautstärke, Temperaturen, Füllstände, Druck oder Schwingungen. Diese Werte dienen dann als physikalische Indikatoren, um den Maschinenzustand zu ermitteln und bei Abweichung vom Sollzustand nachzubessern. Aus diesem Grund eignet sich die zustandsorientierte Instandhaltung besonders für Maschinen, an denen es viele Verschleißteile gibt. Die Abnutzung dieser Teile kann dann zuverlässig und rechtzeitig festgestellt werden, bevor es zu größeren Schäden kommt.
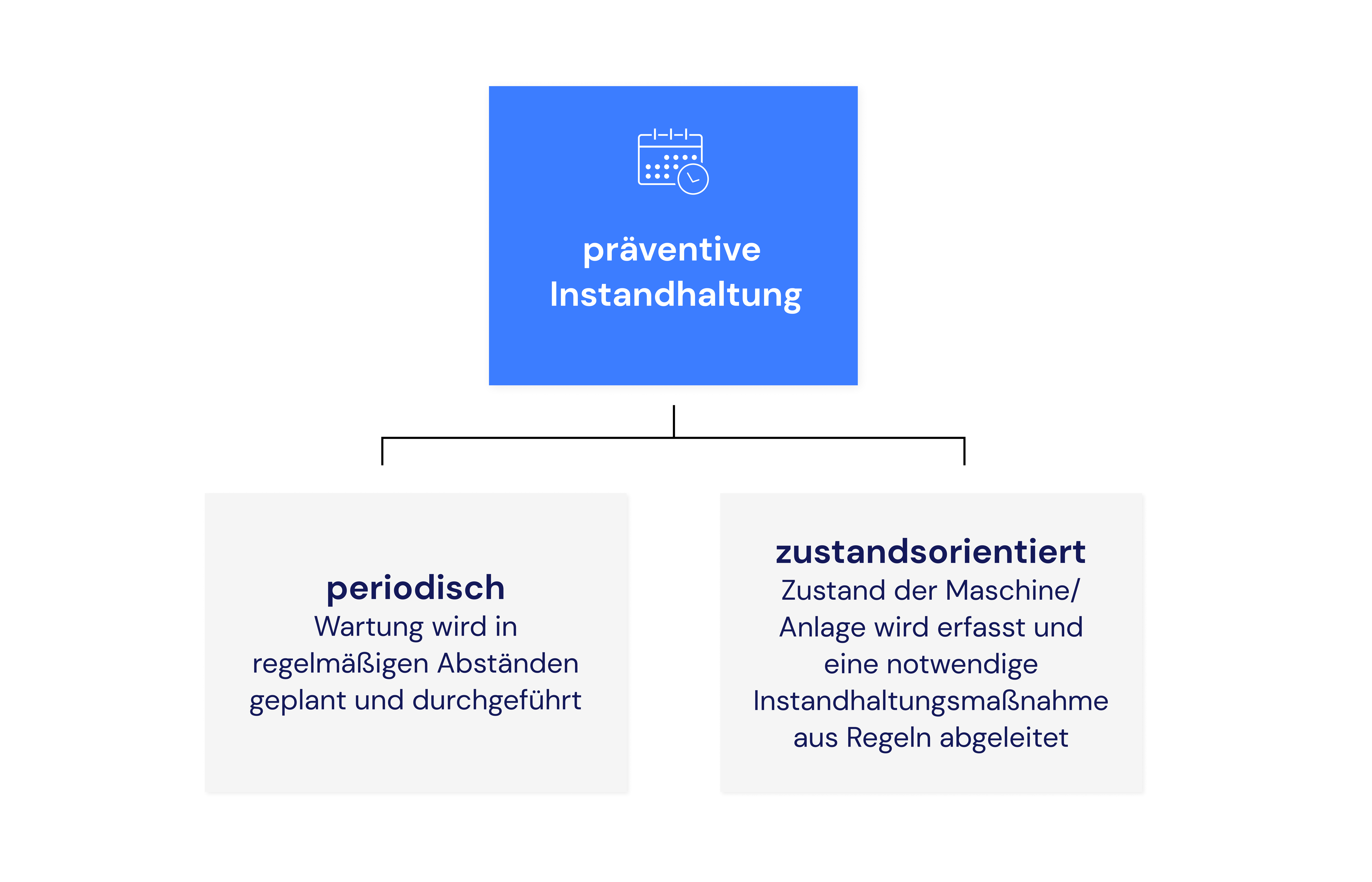
4 Bereiche der Instandhaltung
Nach DIN 31051 und DIN EN 13306 werden vier Grundmaßnahmen der Instandhaltung unterschieden: Inspektion, Wartung, Instandsetzung und Verbesserung. Damit ein Unternehmen bestmöglich vom Instandhaltungsmanagement profitiert, ist es wichtig, dass diese vier Bereiche eng aufeinander abgestimmt sind. Denn wenn eine systematische Überwachung der Betriebsmittel sowie eine organisierte und terminierte Wartung durchgeführt werden, fallen die Instandhaltungsmaßnahmen in Form von Reparaturen bereits sehr gering aus. Trotzdem lassen sich Reparaturen naturgemäß nicht vollständig vermeiden, weil Verschleiß und altersbedingte Abnutzungen technisch und physikalisch bis zu einem gewissen Grad dazugehören.
Ein gutes Instandhaltungsmanagement sorgt also für eine prozess- und produktionsoptimierte Instandhaltung, Inspektion und Wartung und stellt so die bestmögliche Maschinenverfügbarkeit sicher.
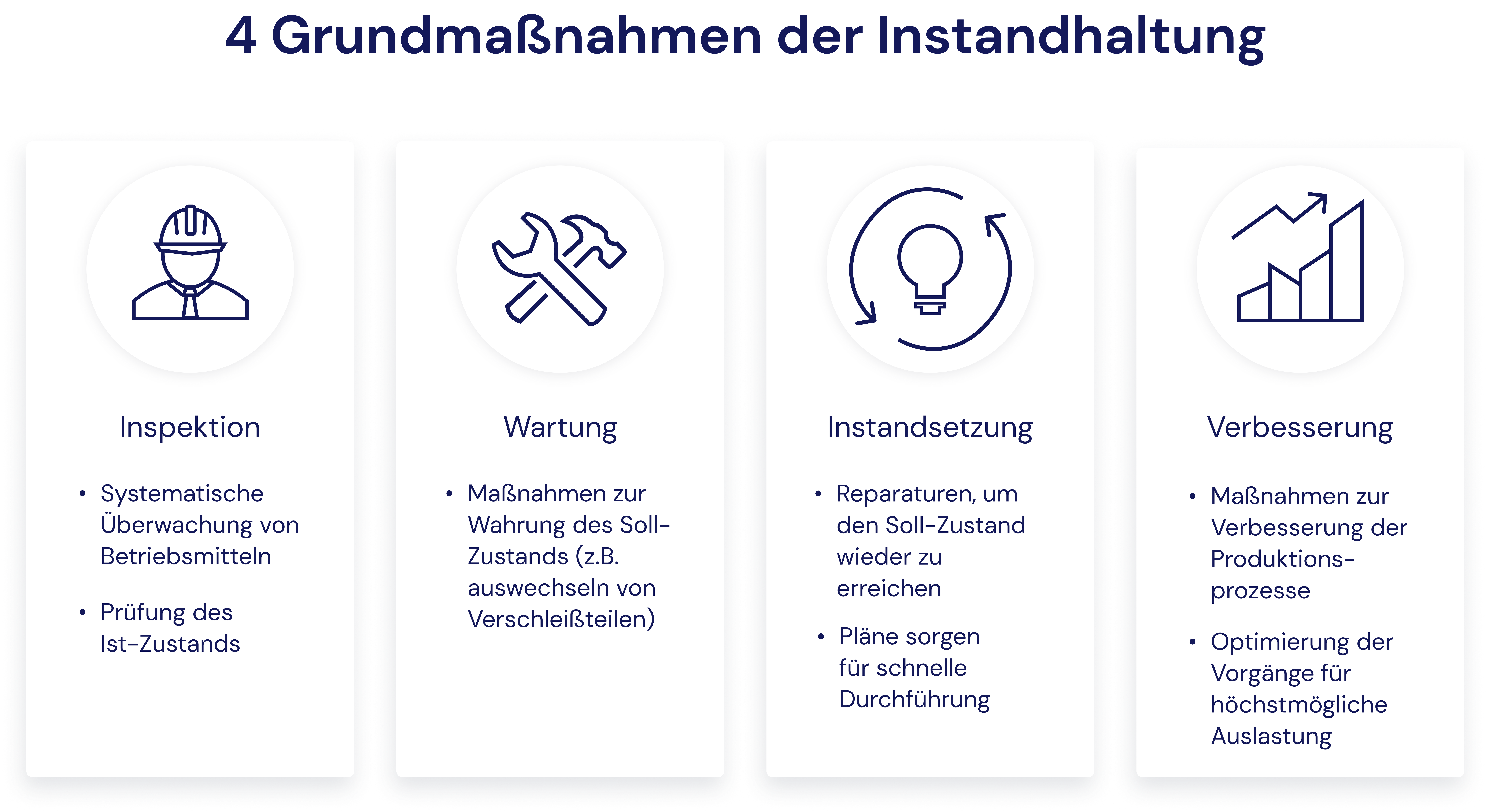
3 unterschiedliche Instandhaltungskonzepte
In der Produktion werden generell drei unterschiedliche Instandhaltungskonzepte unterschieden: die korrigierende, die hier im Fokus stehende präventive und die vorausschauende Instandhaltung.
Während bei der „korrektiven“ oder auch „reaktiven Instandhaltung“ nach dem Prinzip „Reparieren, wenn etwas kaputtgeht“ gehandelt wird, verfolgt die vorausschauende Instandhaltung den Ansatz „Wissen, wann etwas kaputtgeht“. Ein Beispiel für einen konkreten Anwendungsfall von reaktiver Instandhaltung gibt unser Blogartikel über das Unternehmen Vetter.
Präventive Instandhaltung nach der Devise „Reparieren, bevor etwas kaputt geht“, basiert gegenüber der korrektiven Instandhaltungsstrategie auf einem Paradigmenwechsel, denn der Arbeitsprozess ist auf eine ganzheitliche und vorbeugende Betrachtungsweise ausgerichtet. Allgemein lässt sich feststellen, dass sich mit einem weiter in die Zukunft gerichteten Instandhaltungsansatz die Gesamtanlageneffektivität (OEE) einer Maschine maßgeblich verlängert. Das Schaubild vermittelt einen guten Einblick in diesen Zusammenhang.
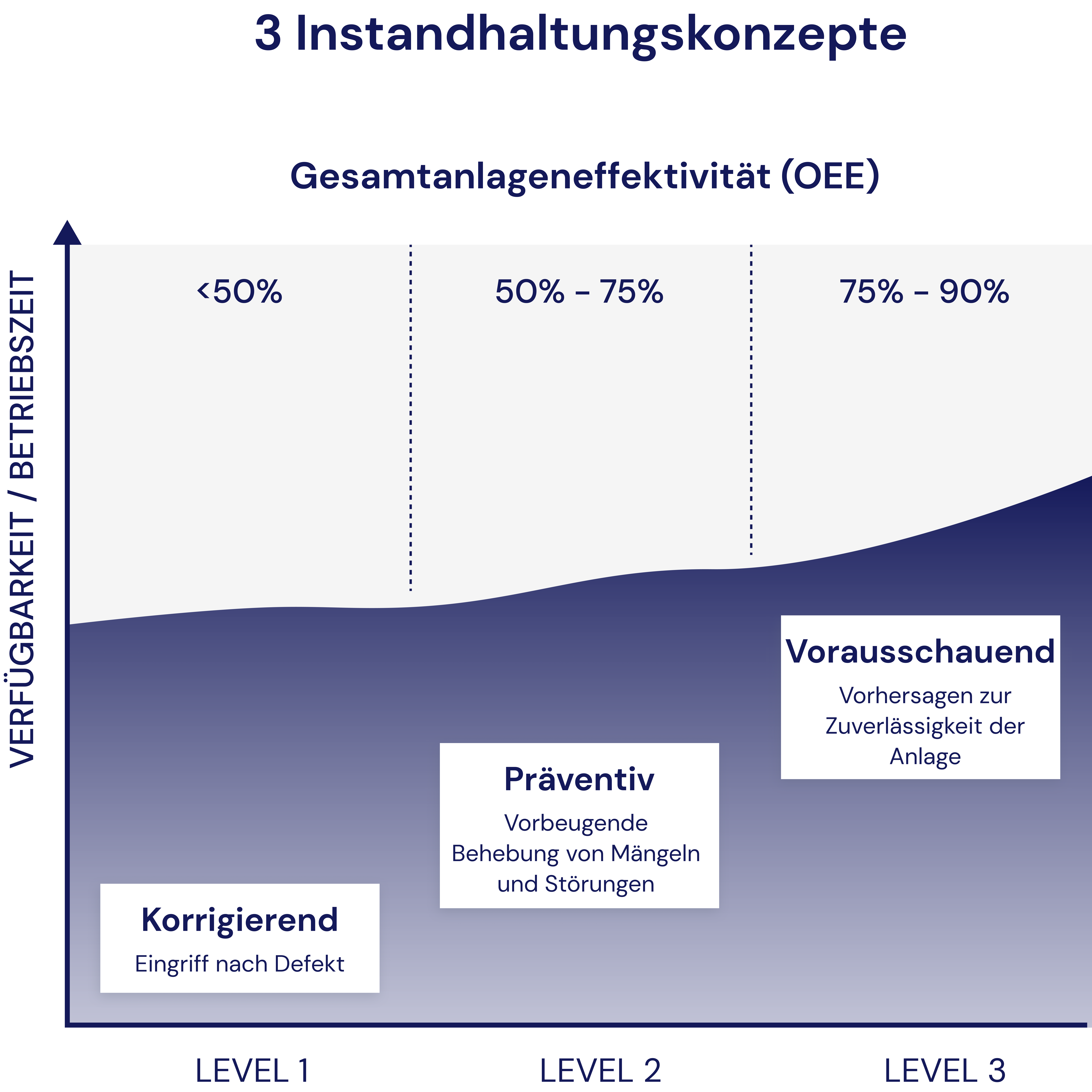
Vor- und Nachteile von präventiver Instandhaltung sowie Tipps zur Umsetzung
Präventive Instandhaltung mit geplanten Instandhaltungsmaßnahmen nach einem bestimmten Turnus hat gegenüber einem reaktiven Instandhaltungsansatz zahlreiche Vorteile.
Vorteile von präventiver Instandhaltung
Vermeidung ungeplanter Stillstände und dadurch höhere Produktivität
höhere Arbeitsqualität und -effizienz, da dieselben Arbeiten auf regelmäßiger Basis wiederholt werden
Reduzierung teurer Reparaturkosten dank regelmäßiger Instandhaltung
bessere Planbarkeit der Kosten für Wartung und Instandhaltung
Zeitersparnis, da das Entstehungsrisiko von Problemen im Vorfeld drastisch reduziert wird
Längerer Lebenszyklus der Gesamtlebensdauer der Anlage im Vergleich zur korrigierenden Instandhaltung
Die präventive Instandhaltung ist somit ein essenzielles Kriterium für eine zukunftssichere, resiliente Produktion. Ihre Erfolge lassen sich anhand von zwei Kennzahlen messen: der MTTR (= mean time to repair/mittlere Reparaturzeit) und der MTBF (= mean time between failures /mittlere Laufzeit zwischen zwei Stillständen). Ziel ist die Minimierung der MTTR und die Maximierung der MTBF.
Nachteile von präventiver Instandhaltung
Trotz der vielen Vorteile bringt der präventive Instandhaltungsansatz auch Nachteile mit sich, die mit berücksichtigt werden sollten. Hierzu zählen:
unnötige Instandhaltungszyklen sind wahrscheinlich
Störungen lassen sich auch durch vorausschauende Instandhaltung nicht vollständig ausschließen
höherer personeller Aufwand
Hilfreiche Fragen bei der Umsetzung von präventiver Instandhaltung
Dass die Vorteile vorbeugender Instandhaltung die Nachteile überwiegen, ist sicherlich nachvollziehbar. Bei der praktischen Umsetzung möchten wir Ihnen folgende Leitfragen als Inspiration und Hilfe für die Platzierung der Themen bei Ihren Mitarbeitern an die Hand geben:
Wer aktualisiert und pflegt die Wartungs- und Inspektionspläne?
Muss das Instandhaltungspersonal besonders geschult werden?
Können einige der Instandhaltungsarbeiten auch durch die Mitarbeiter der Produktion im Sinne einer autonomen Instandhaltung durchgeführt werden? Näheres zu diesem Konzept erläutert unser Blogartikel.
In welchen Time Slots stehen die Produktionsanlagen für vorbeugende Instandhaltungsarbeiten zur Verfügung?
Welche personellen und zeitlichen Ressourcen stehen generell für präventive Instandhaltungsmaßnahmen zur Verfügung?
Wenn Sie diese und evtl. weitere für Ihr Unternehmen relevante Fragen bei der Umsetzung Ihrer präventiven Instandhaltungsstrategie berücksichtigen, behalten Sie die wesentlichen Dinge stets im Blick.
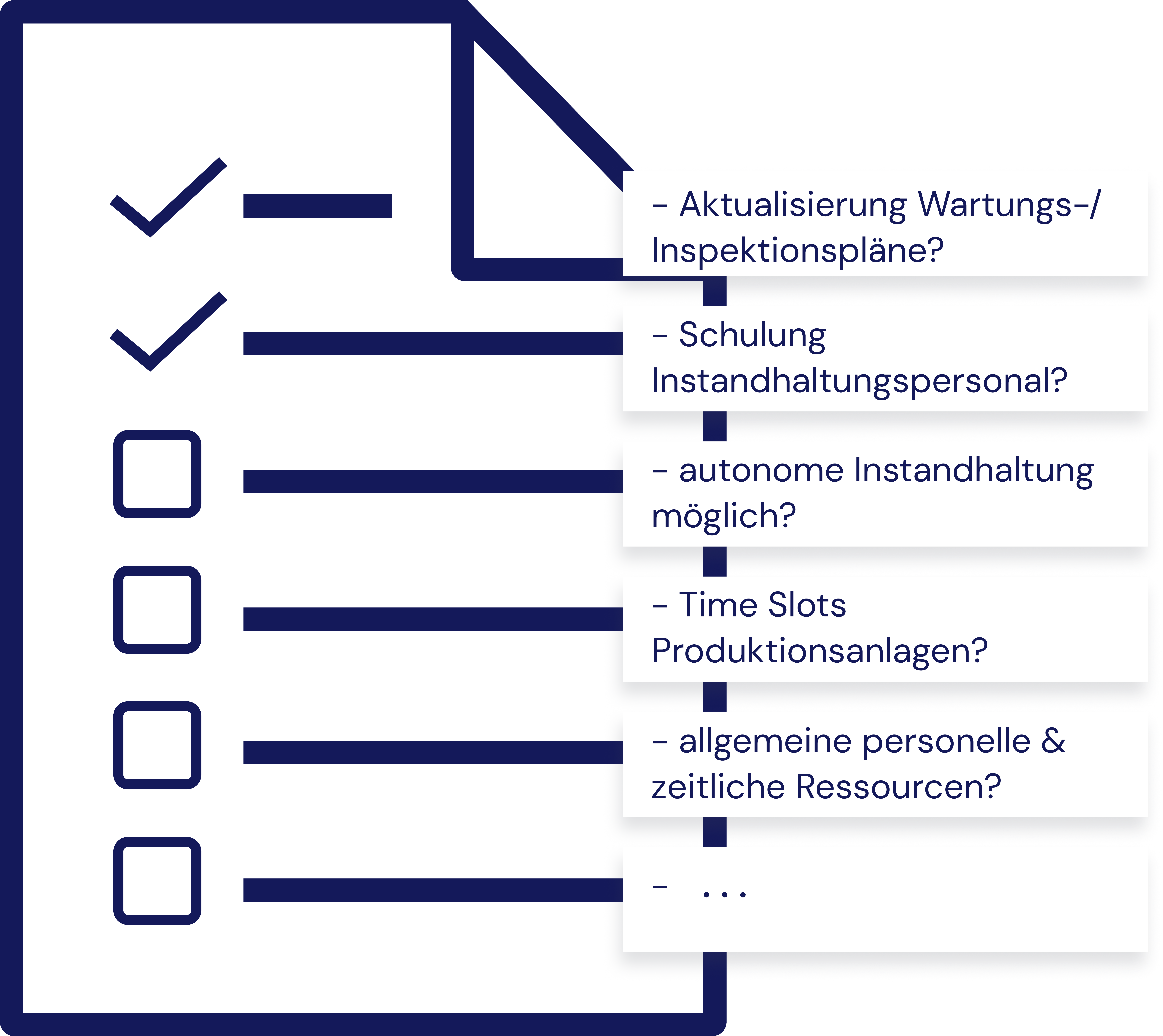
Nachteile eines papierbasierten präventiven Instandhaltungsmanagements
Damit präventive Instandhaltung Früchte trägt, ist eine effiziente Wartungsplanung unerlässlich. Das Problem dabei: Wartungs- und Servicepläne müssen individuell und zeitintensiv erstellt werden. In vielen Betrieben geschieht dies Excel-basiert, was einen hohen Dokumentationsaufwand mit sich bringt. In der Praxis sieht das dann so aus, dass zugehörige Wartungsanweisungen aus Handbüchern aufwändig in MS Office zusammenkopiert und erweitert werden müssen. Dies ist umso anspruchsvoller, wenn Wartungschecklisten- und -anweisungen anlagenspezifisch sind. Die Nachbearbeitung erweist sich dann als ressourcenstrapazierend und fehleranfällig und die Medienbrüche, die bei der manuellen Datenübertragung von Papier ins ERP-System entstehen, kosten viel Zeit und sind vielfach nicht vollständig, so dass wichtige Informationen beim Transfer von einem Medium ins andere verloren gehen.
Eine weitere Implikation papierbasierter präventiver Instandhaltung ist die fehlende Rückverfolgbarkeit über durchgeführte Instandhaltungsarbeiten. Dies stellt ein Risiko bei Audits bzw. Zertifizierungen dar und ist vor allem dann problematisch, wenn Rückverfolgbarkeit eine Grundvoraussetzung für Geschäftsbeziehungen ist, wie in bestimmten Branchen üblich. Mit der fehlenden Nachverfolgbarkeit der Daten geht eine allgemeine mangelnde Transparenz einher. Hierdurch werden dem Management eine korrekte Bewertung der Ist-Situation sowie eine bedarfsgerechte, zukünftige Planung sehr schwer gemacht.

Digitale präventive Instandhaltung – Schlüssel zu höherer Produktivität
Die Herausforderungen, die Fertigungsbetriebe meistern müssen, die ihre Produktionsanlagen noch ohne eine Softwarelösung für präventive Instandhaltung betreiben, entfallen beim Umstieg auf eine digitale Lösung.
Vorteile von digitaler präventiver Instandhaltung mit Operations1
Folgende Vorteile bietet Ihnen der Einsatz unserer Connected Worker Lösung:
Wartungspläne lassen sich direkt in Operations1 erstellen oder aus ERP, MES oder CMMS übergeben
Sie können Ihren Mitarbeitern intuitive Checklisten mit bild- und videogestützten Anleitungen bereitstellen und dadurch auch autonome Instandhaltungstätigkeiten unterstützen
Dank der Möglichkeit individuell für Sie angepasster Variantenkonfigurationen lässt sich eine hohe Variantenvielfalt bei Anlagen abbilden
Wartungsberichte werden automatisch erstellt
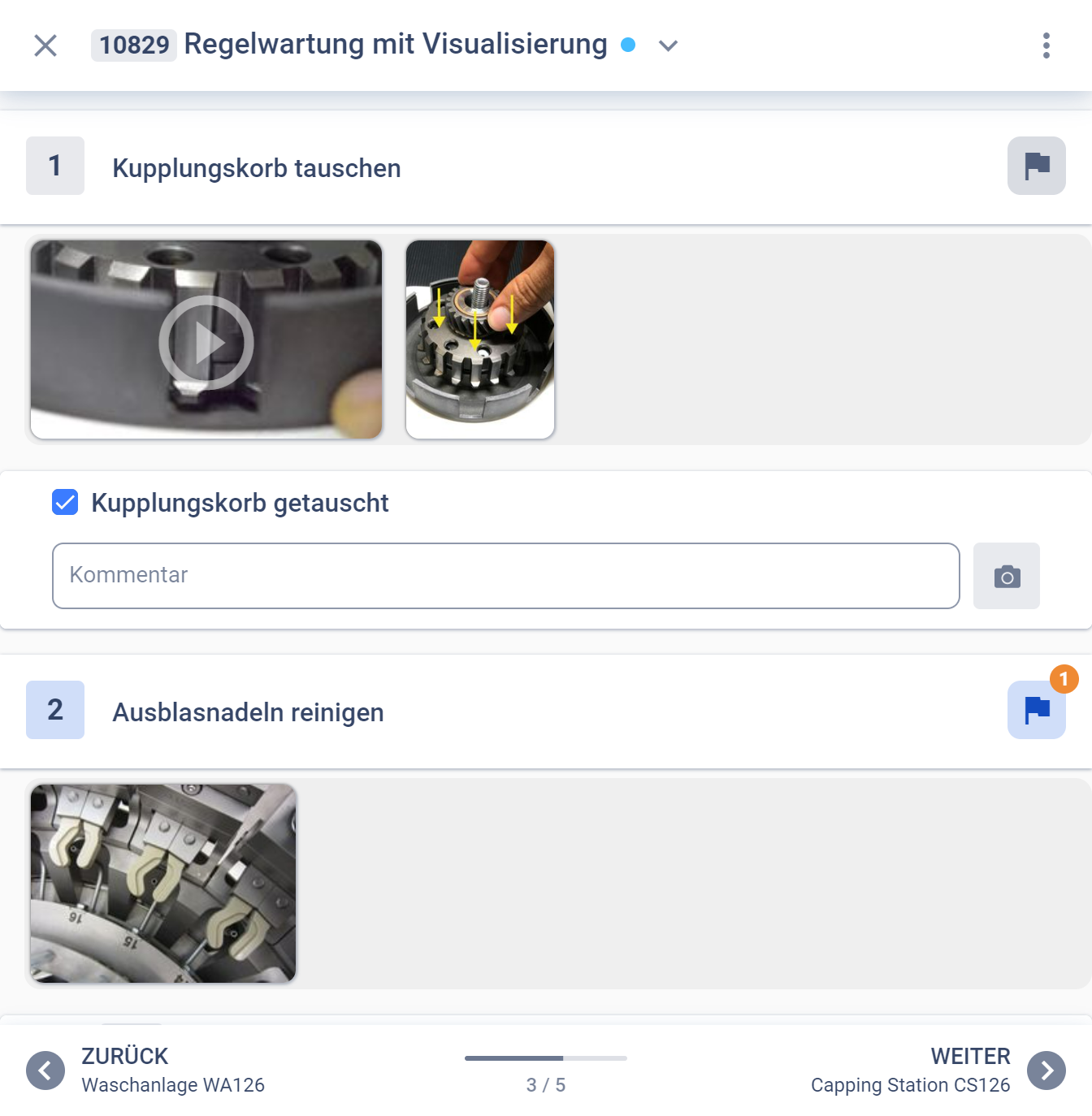
Diesen Gewinn zieht Ihr Unternehmen aus digitaler präventiver Instandhaltung mit Operations1:
Vermeidung von Maschinenausfällen, hohen Reparatur- und Ersatzteilkosten sowie nicht wertschöpfenden Dokumentationstätigkeiten
Ein moderneres und sicheres Arbeitsumfeld für Ihre Mitarbeiter infolge weniger Unfälle
Effizientere Instandhaltungsprozesse in Planung und Durchführung
Höhere Flexibilität beim Mitarbeitereinsatz durch autonome Instandhaltung
Gesteigerte Auditsicherheit dank vollumfänglich transparenter Wartungstätigkeiten
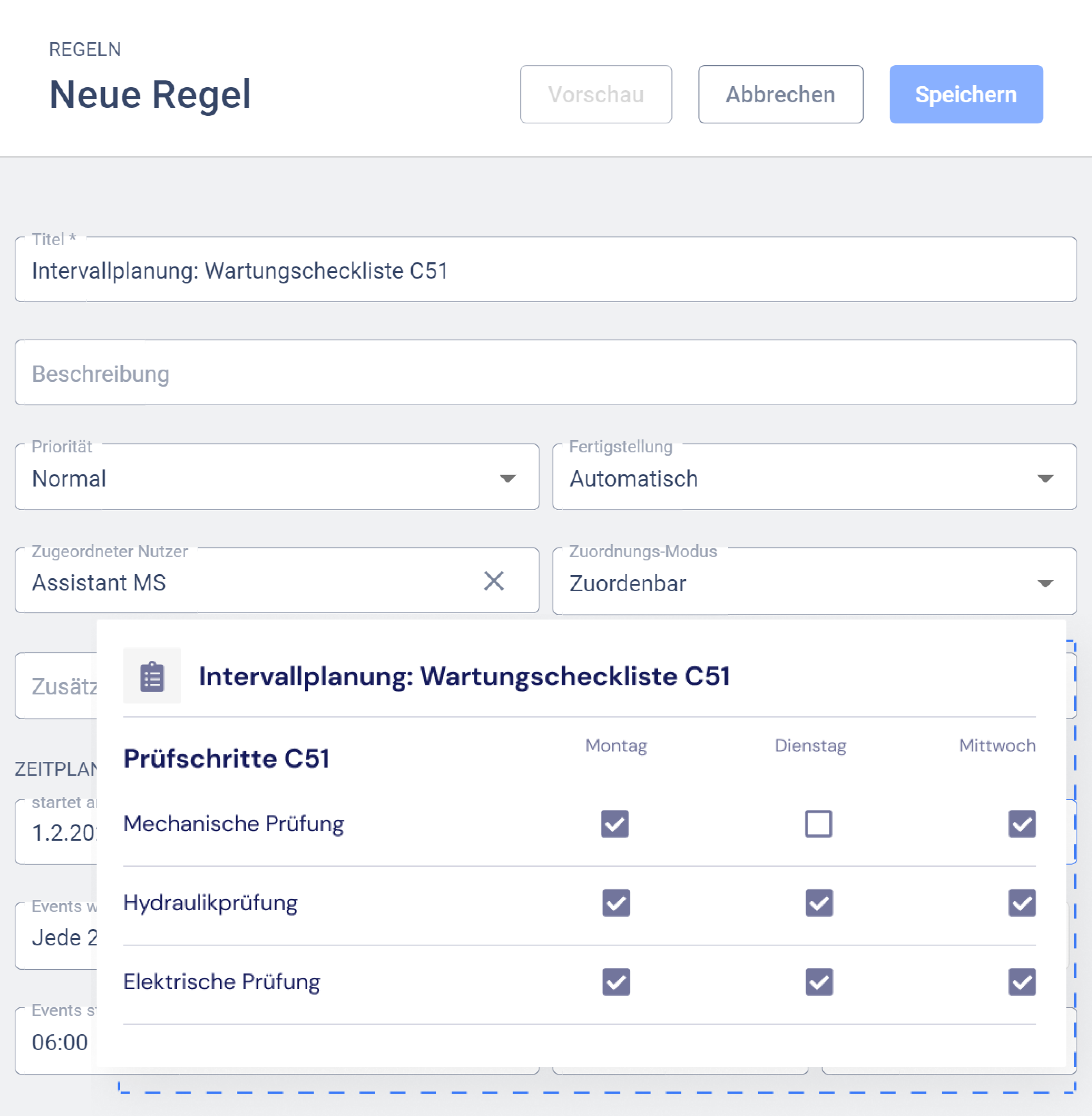
Bündelt man all die Vorteile, die digitale präventive Instandhaltung auf dem Shopfloor bietet, lassen sich im Kern gleich mehrere Gewinne aus einer Digitalstrategie ziehen: Die Anlagenverfügbarkeit wird gesteigert und langfristig kann sich dadurch die Produktivität eines Betriebs erhöhen, was wiederum das Fundament für unternehmerische Zukunftsfähigkeit legt. Grund genug, einen papierbasierten präventiven Instandhaltungsansatz nochmal kritisch zu überdenken, oder?
Fazit: Richtig eingesetzt legt digitale präventive Instandhaltung den Grundstein für Resilienz und Operative Exzellenz.
Sie interessieren sich für digitale präventive Instandhaltung?
Dann füllen Sie gerne unser Kontaktformular mit Ihren Gedanken, Wünschen und Zielen aus. Wir melden uns umgehend bei Ihnen zurück und diskutieren gemeinsam mit Ihnen den für Sie bestmöglichen Ansatz.
Markus Glotzbach
Während seiner beruflichen Laufbahn sammelte Markus tiefe Einblicke bei Unternehmen und Konzernen unterschiedlicher Industrien und kennt die Digitalisierungshürden und Probleme auf dem Shopfloor. Vor seinem Wechsel zu Operations1 studierte er International Management (MA) und war im Cloud Computing- sowie im SaaS-Telematik-Bereich tätig.