What it's about
At the live event, which entered its second round on April 17, 2024 in Frankfurt, over 60 experts from the manufacturing industry met to discuss the following topics in panel discussions, customer presentations and showcases:
· Status quo in manufacturing: How far has digitalization progressed?
· Shopfloor processes: What innovative solutions are driving digitalization?
· Artificial intelligence: How can AI make manufacturing processes more efficient?
· Integration with SAP technologies: How does seamless integration keep a clear system landscape manageable?
In this event, we have highlighted some of the groundbreaking topics and discussions that show how industrial companies can benefit from advanced technologies and smart manufacturing strategies. Let us summarize some of the highlights and key learnings.
How far along is digitalization in manufacturing?
Much of the panel discussion at the start of the event revolved around the status quo of digitalization in manufacturing. Mr Guido Reimann, Deputy Managing Director VDMA Software and Digitalization, gave us an insight into the mechanical and plant engineering industry in particular: "The state of digitalization in mechanical and plant engineering has developed significantly in recent years and is now a central aspect of the industry. Digitalization efforts not only include connected machines, but also increasingly focus on connecting employees. There is still a long way to go, but the first steps have been taken."

Artificial intelligence as a competitive advantage
We discussed numerous use cases of Artificial Intelligence (AI) in manufacturing, including impressive presentations such as the "AI Shopfloor Assistant". These technologies demonstrate how AI is being implemented in the real world to make our production processes more efficient and adaptive. It was fascinating to see how AI is not only optimizing our operational processes, but also helping to make manufacturing intelligent and predictive.
More and more companies are being asked by their management to implement improvements through AI in all departments, reports Daniel Grobe before the panel discussion "Intelligent manufacturing: Challenges, opportunities and the journey to an AI-driven future" at the Future Manufacturing Event. The question remains, how can this be done?
Lena Weirauch, CEO & Co-Founder at ai-omatic solutions, clarifies: "The barrier to entry for the use of generative AI is so low that there are no excuses. After all, you don't want to be the only restaurant in town that doesn't have a fridge."
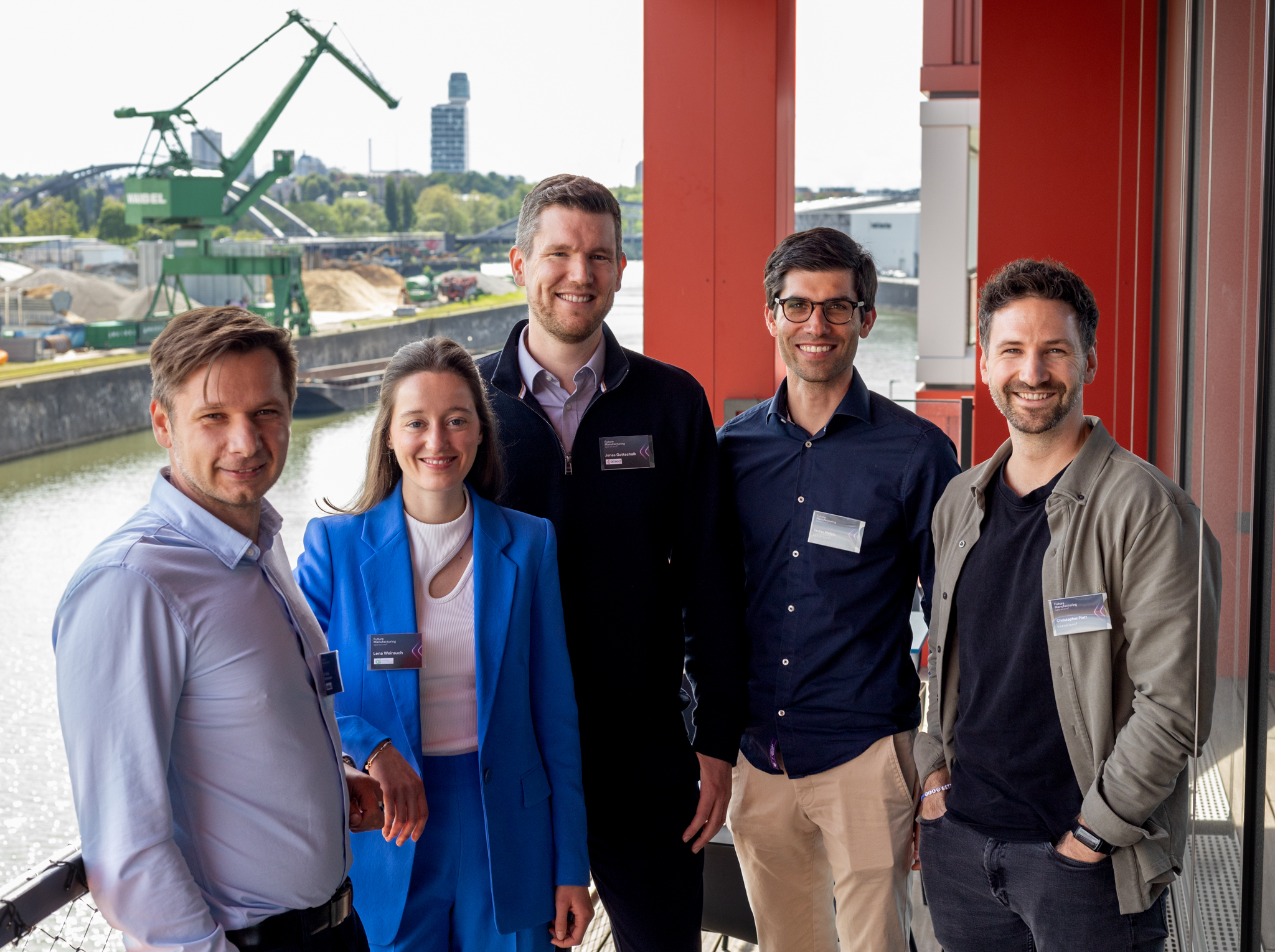
For Jonas Gottschalk, Partner at Deyan7, there are three steps to getting started:
Find a use case.
Try out the use case yourself with a ChatGPT Teams license.
Implement the prototype in 2-6 weeks with an experienced service provider.
It shouldn't take any longer than that.
Growing acceptance of cloud solutions and standardized tools
Another highlight was the discussion on end-to-end digitalization, presented by Quantum-Systems GmbH, which showed how digital process integration is revolutionizing quality assurance and assembly processes. This underlined the industry's growing confidence in cloud solutions and the need to integrate standardized digital tools into our daily processes.
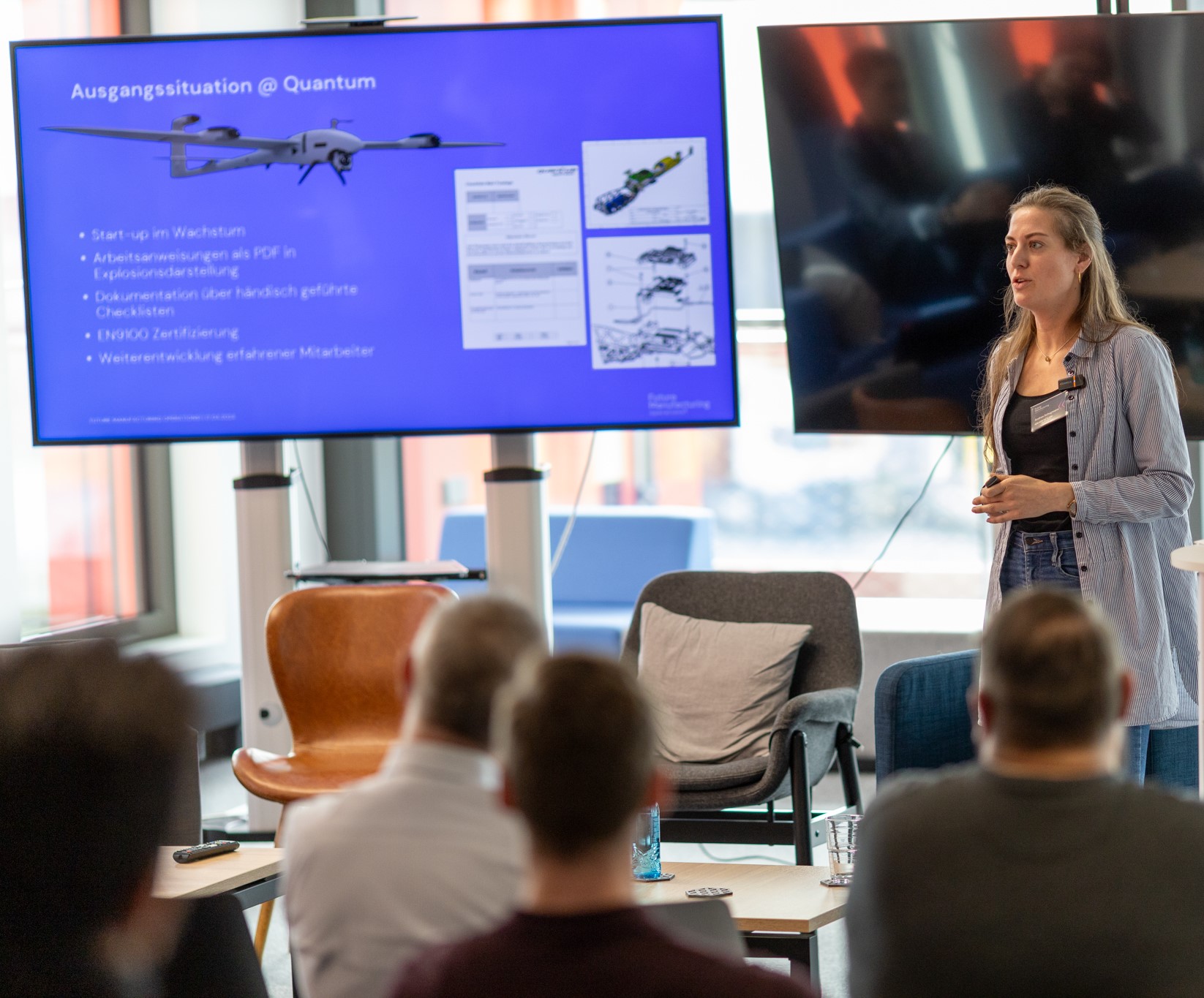
New momentum for transformation and digitalization
The practical presentation on "From Analog to Digital: The Quality Management Revolution" with representatives from ProMinent GmbH highlighted the transformative journey from traditional to digital quality management. We were able to learn how the company has moved from traditional methods to digital checklists, work instructions and defect collection cards to improve efficiency, accuracy and transparency. Christian Braun shares valuable insights into the successful implementation of digital tools and the associated challenges and successes.

At another customer presentation by the Schunk Group, a global technology group and market leader in the field of materials technology and mechanical engineering, we learned how the use of Operations1 has improved the quality of their training processes and significantly reduced the training period.
In the best practice presentation, the implementation strategies and the process of knowledge transfer were explained in detail. This enables Schunk to guarantee high quality standards and fast induction times despite the imminent departure of experienced employees and an extensive employee ramp-up at various locations.
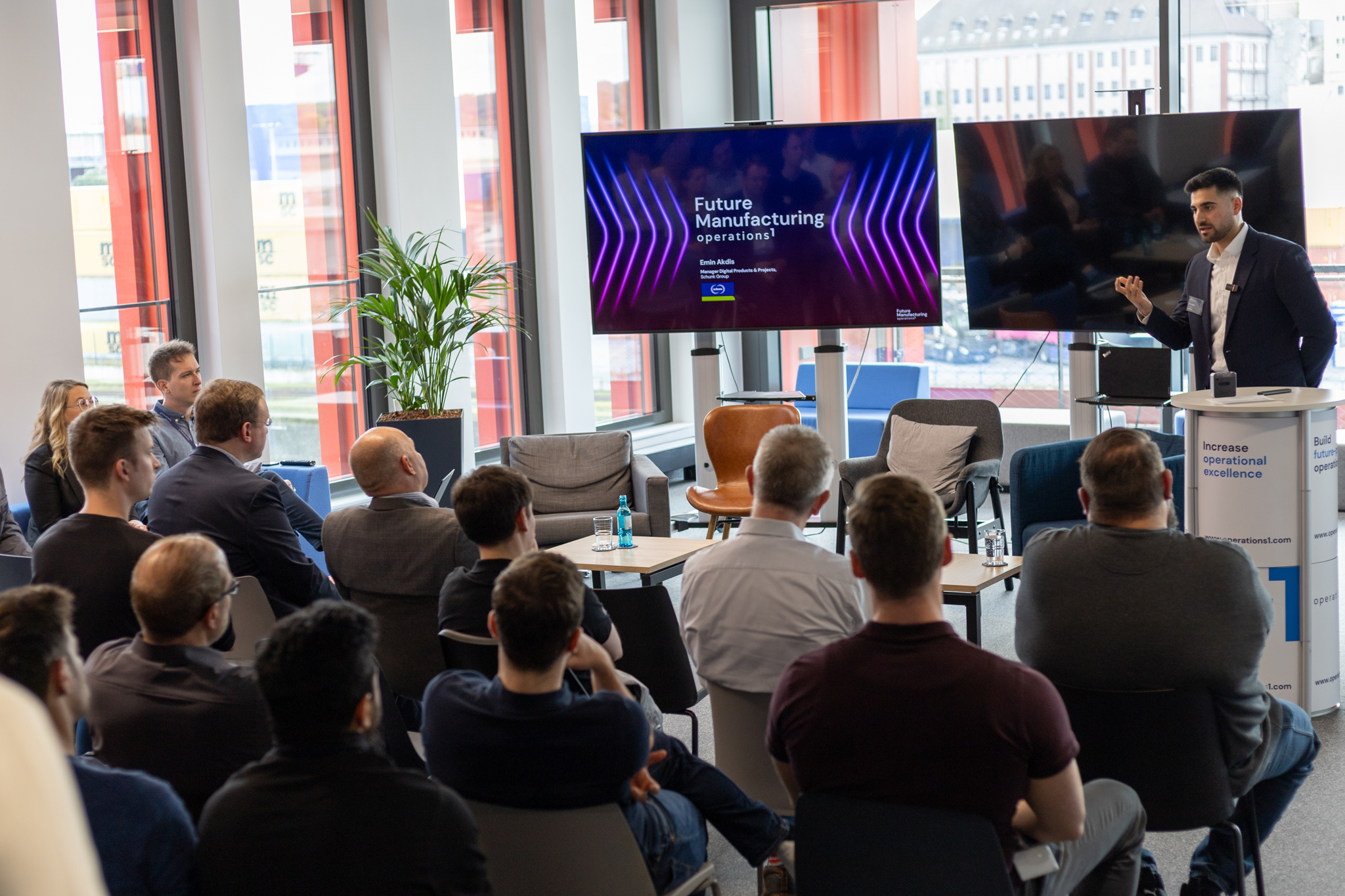
Connecting and integrating systems
Another key aspect of our event was the importance of integrating different technology platforms. Yannik Moser from Operations1 explained how seamlessly integrated system landscapes, by linking Operations1 with SAP technologies, can lead to more efficient and error-free workflows.
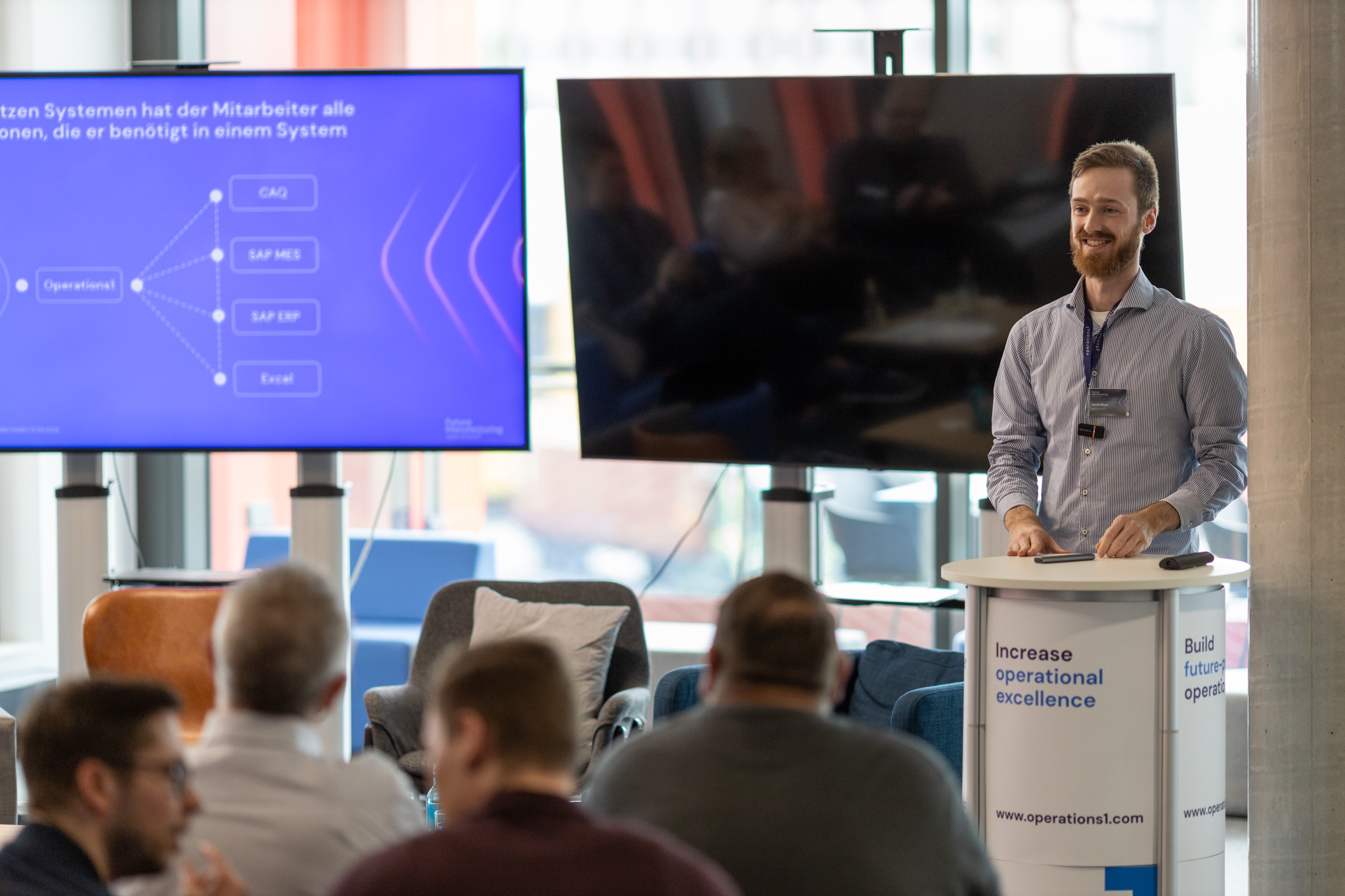
Conclusion: Strengthened for the future of manufacturing
The Future Manufacturing Event 2024 not only showed that the manufacturing industry is at a turning point, but also that it is ready to master it with determination and a spirit of innovation. The diverse discussions and presentations underlined how critical the integration of advanced technologies such as AI, cloud solutions and digital transformation tools is for the future of our industry. These technologies are no longer distant visions, but concrete tools that are already creating competitive advantages and increasing industrial efficiency.
Our event impressively demonstrated that the fear of new technologies is fading and giving way to a pragmatic and goal-oriented acceptance. This reflects a global trend that is gaining importance across industry boundaries.
I am proud that we at Operations1 are at the forefront of this movement and grateful for the dedicated community that has joined us on this journey. The next event will provide further opportunities to expand our knowledge, strengthen our networks and shape the manufacturing industry together.
Would you like to find out how you too can take your manufacturing to the next level?
Simply fill out the contact form. We will contact you immediately with the next steps and a proposed date.
Benjamin Brockmann
Benjamin Brockmann (M. Sc., Management & Technology) founded Operations1 in 2017 together with Daniel Grobe (also M. Sc., Management & Technology). The founders developed the software solution based on various practical projects, including at the Fraunhofer Institute, and on their experience in industry, auditing and management consulting. Benjamin Brockmann has already worked for companies such as KPMG and Arthur D. Little.