Preventive Maintenance (PM) is the regular and routine maintenance of equipment and assets to keep them running and avoid costly unplanned downtime due to unexpected equipment failures. Examples of preventive maintenance include equipment inspections, cleaning and lubricating critical equipment, and tidying the production floor.
Digital Maintenance Software From a Leading Provider
Empower your workforce with image- and video-based maintenance checklists. Perform your maintenance planning intelligently, provide maintenance knowledge paperless and in real time and set global process standards.
Get to know the software in just 3 minutes and get an overview of the functionalities and application areas of Operations1.
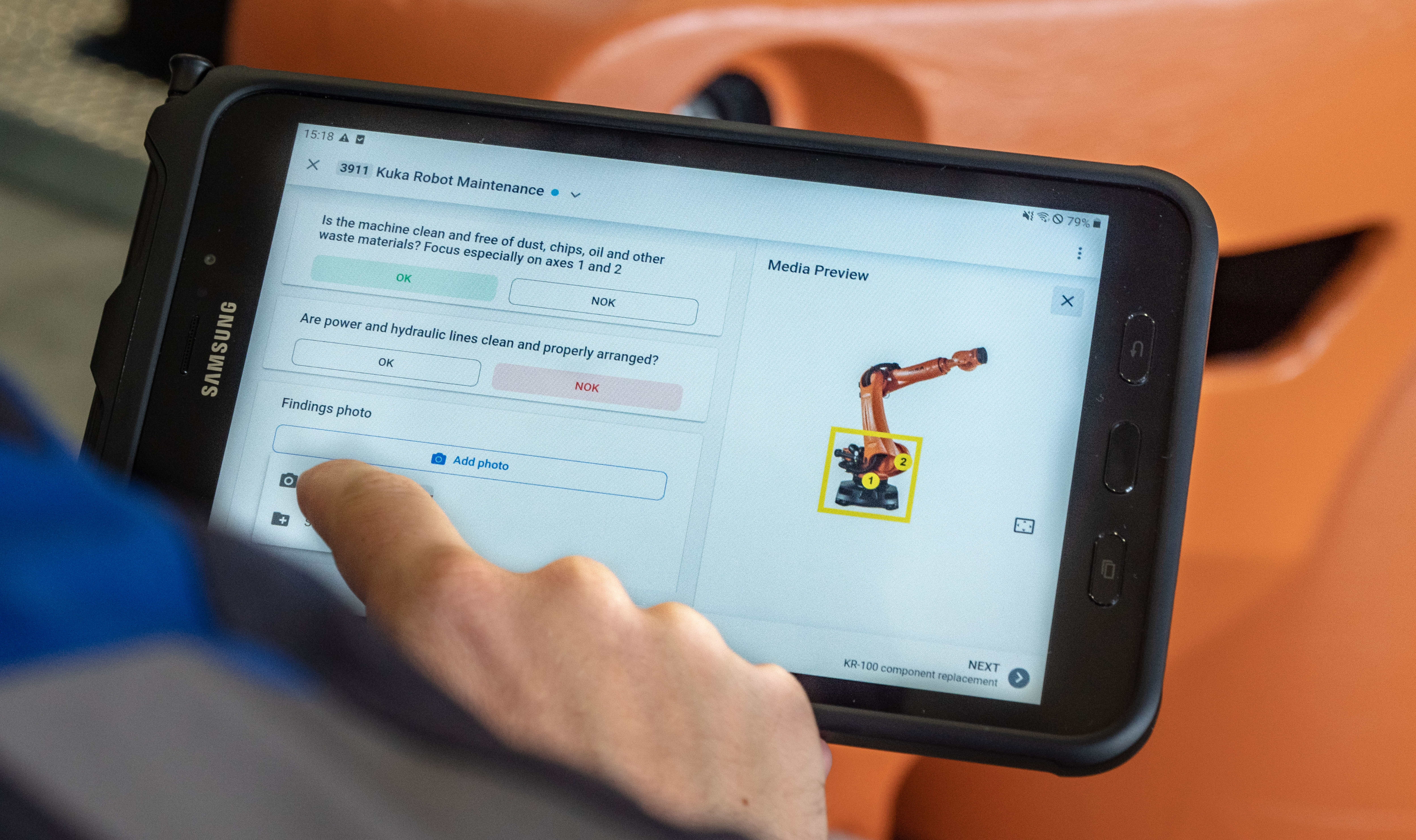
- -85% reduced downtime
- +21% higher productivity
- -95% less effort for documentation
The Operations1 software in maintenance
With Operations1 you enable intuitive and simple execution of maintenance processes. Provide your employees with intuitive instructions and checklists, plan your activities and benefit from comprehensive transparency.
Maintenance software: Features for industrial use
Drag and Drop
Simplify the creation and updating of your documentation
Pictures and videos
Include images and videos in your documents to increase comprehension
QR-code scanning
Start processes via search function or by scanning a QR code on your machine
Recurring orders
Schedule recurring maintenance tasks fine granularly in Operations1
End-to-end integration
Use orders from your ERP, MES or CMMS and work operationally in Operations1
Incident management
Create tasks, assign them and ensure implementation
Structural classes
Organize your work based on your machines, locations or teams
Digital reports
Get full transparency on performed activities and findings
Cloud approach
Standardize processes and leverage your process knowledge from the cloud
Maintenance Success Story
Learn how the Hirschvogel Automotive Group, a global automotive supplier, uses digital maintenance instructions and checklists to make knowledge available globally, increase reaction times and reduce costs.
Maintenance software: Frequently asked questions
What is preventive maintenance?
What is predictive maintenance?
Predictive maintenance refers to the use of data-driven proactive maintenance methods designed to analyze equipment condition and predict when maintenance should be performed. Predictive maintenance software uses data science and predictive analytics to estimate when equipment is likely to fail so corrective maintenance can be scheduled before failure occurs. The goal is to schedule maintenance at the most convenient and cost-effective time in order to optimize equipment life before it becomes damaged.
What is the best maintenance software?
The most suitable maintenance software depends on your individual use case. The Operations1 software is the leading software for highly automated enviroments where companies strive for maintenance knowledge retainment, increased workforce productivity, a reduction in downtimes and fully transparent maintenance logs.
What is maintenance management?
Maintenance management comprises all operational measures to prevent machine failures and increase plant availability. At the same time, maintenance measures ensure optimized operating processes and increased operational reliability.
Can maintenance orders be emailed to my team?
Work orders get automatically assigned to the respective maintenance team member within the Operations1 software. Therefore, workers don’t need to switch systems any longer between planning, execution and reporting. Work planning can be conducted within Operations1 or through integration with other systems such as the ERP System or MES.
Why maintenance software?
Maintenance activities are a fundamental part of safe and effective production. The activities of the teams in maintenance prevent production errors or even production downtimes, which can occur due to wear and tear on the machine or tool, for example. Maintenance software helps companies to plan these activities for the respective machines and employees, to guide them through the activities with the help of intuitive process instructions, to solve problems collaboratively and to make maintenance activities evaluable. Especially with regard to audits, it is elementary to enable complete traceability of maintenance activities.
What is in a maintenance plan?
Maintenance teams use a maintenance plan to ensure that maintenance activities are carried out properly and at the right time in order to keep overall equipment effectiveness high and spare parts and personnel costs low. Maintenance planning can be time-based, cycle-based or condition-based.