Inspection Software by Operations1
With digital inspection protocols in the Operations1 software, you simplify any inspection process through an intuitive interface for your employees, automatic report generation and comprehensive evaluability. This way, you know at any time about the progress of the inspection processes, can solve incidents collaboratively and use results to improve your processes.
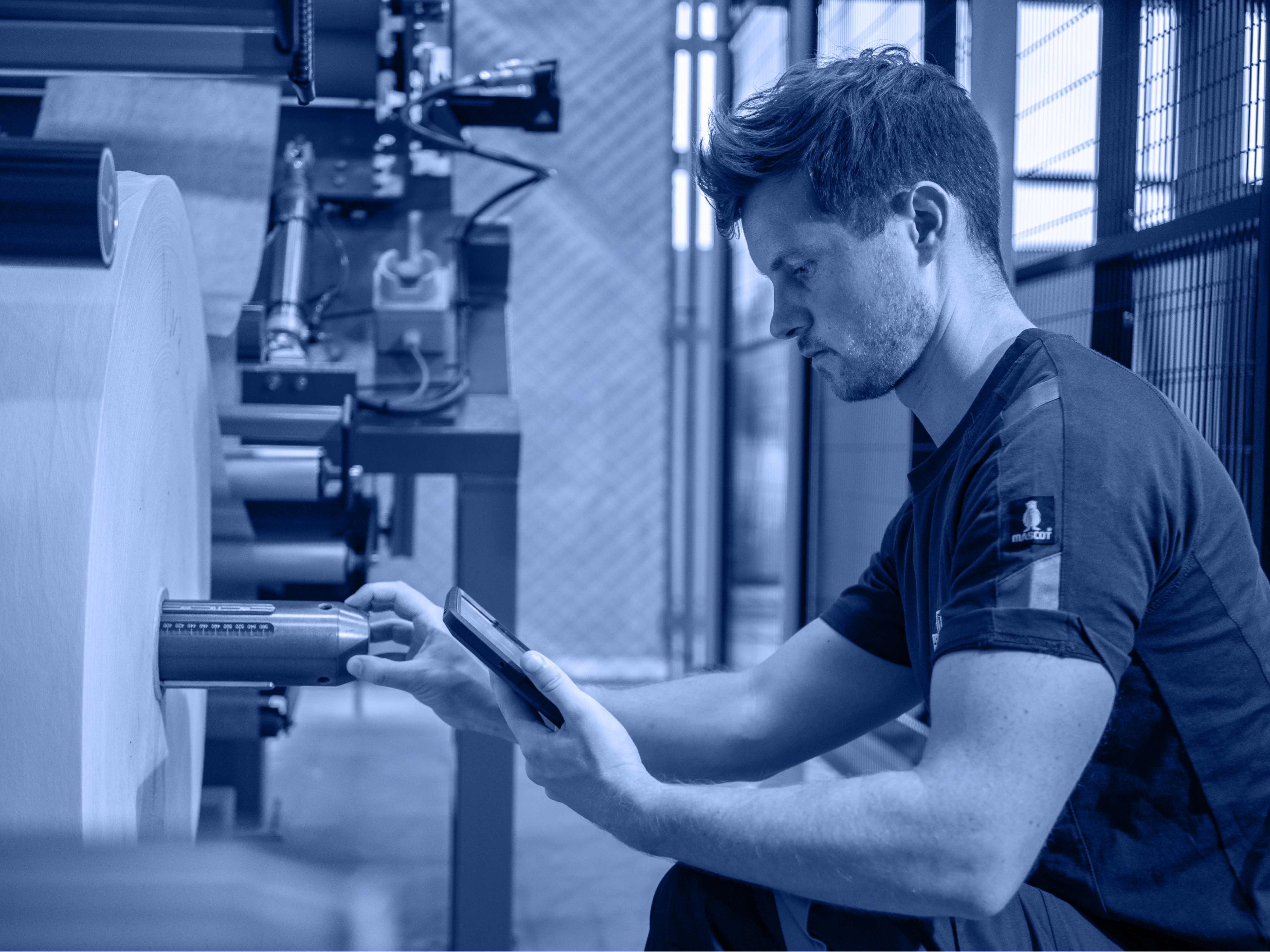
- -95% Effort for Docu
- +21% Higher productivity
- +55% Higher quality
Central functionalities for inspection processes
With Operations1 you eliminate any paper in your inspection processes. Protocols can be created simply by drag & drop and released digitally. Thanks to the cloud approach, your operational employees always receive the current version of your inspection report on the mobile device of their choice. In the process, you simply call up the document via a search function, QR code scan or through a job link. Any data points generated in the inspection as well as information on the process progress are made evaluable in a central overview. This ensures that all checks are carried out, incidents are resolved and data is used for continuous improvement.
Read in serial numbers
Scan serial numbers with your mobile device or external scanner via barcode or QR code and insert them digitally and automatically into logs.
Apply metadata
Add order data or other metadata via interfaces from ERP systems or MES. Integrate their logs into your IT system landscape in a short period of time.
Carry out batch testing
Use conditions to perform inspections based on batch or sample size. This is how your inspection report automatically adapts to your entries.
Let's put an end to paper-based inspection protocols.
Further functionalities of the software
Change Notification
Change notifications in review protocols are received by employees before the process is started. Ask your employees to acknowledge them.
Version control & approval
Your documents retain the same identity across versions, enabling consistent analysis.
Multilingualism
Use your audit trails in all major languages. You can even work on one protocol in different languages at the same time.
Central media library
Organize and edit images and videos centrally. Provide a single source of truth for your protocols.
Process monitoring
Keep track of the process progress of your audits in a clear dashboard and respond to incidents faster.
Offline capability
Use the software offline as well. As soon as you are online again, you can make your protocols centrally available.
Organization
Use structure classes for your sites, teams, products or machines. This allows you to easily organize your protocols.
Modular test protocols
Create audit trail templates and use them as modules. End the copy-and-paste work.
Job management
Schedule inspection jobs and attach relevant inspection documents. Ensure that all tasks are completed.
Analytics
Easily visualize your inspection statistics and increase the significance with locally captured images and videos.
Variant configuration
Automate the creation of variant inspection documentation. This saves you time and provides additional security.
Task management
Create and assign individual tasks and track their progress. React faster to incidents.