Paper-based processes: Efficiency killers in production
International competitive pressure, cost pressure, a shortage of skilled workers and increasing demands from customers or regulations are constantly interfering with the corporate value creation process.
Especially in production processes such as maintenance, assembly, quality inspection, etc., these rapidly increasing challenges must be mastered. Despite all the difficulties, your operational employees ensure added value for your company day after day.
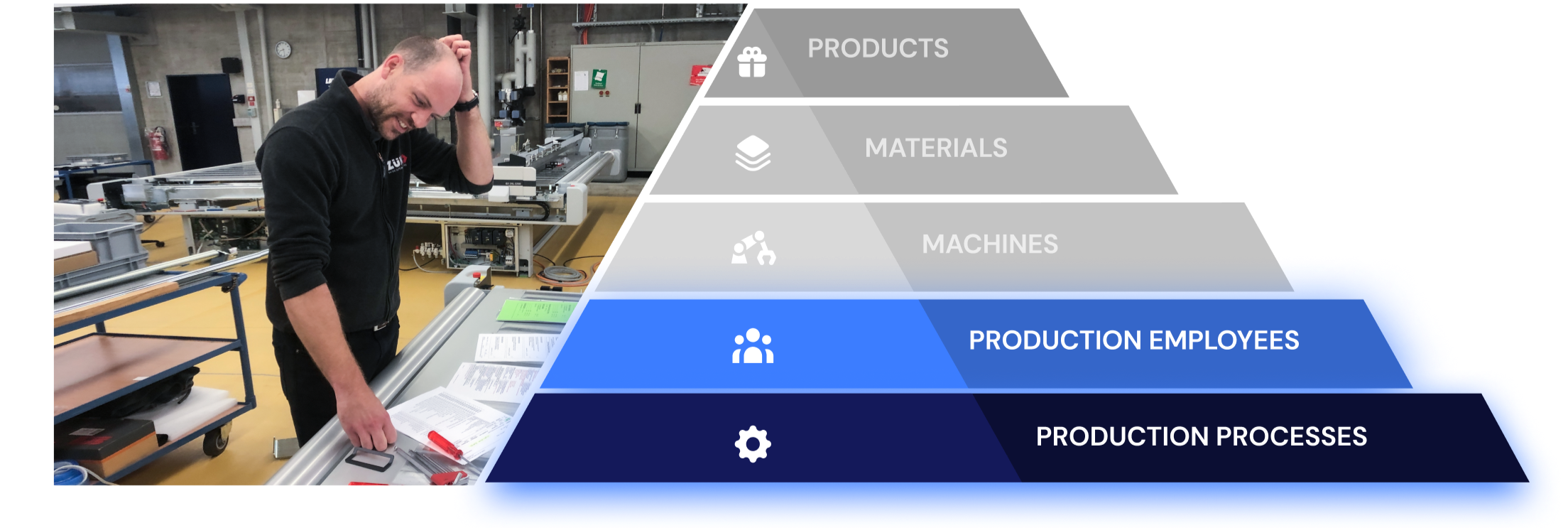
The status quo in production
While industrial companies have already understood
that digitalization can help them meet the high demands, production employees continue to work with
paper-based work instructions and checklists.
The status quo in production is often as follows:
Too much paper in production
High manual effort
No standardized process knowledge
The problems through paper-based work instructions
Work instructions created in Word, Excel, PowerPoint etc. and printed out on paper prove to be very inflexible in practice. This combination of MS Office and paper-based processes leads to a number of operational problems and disadvantages:
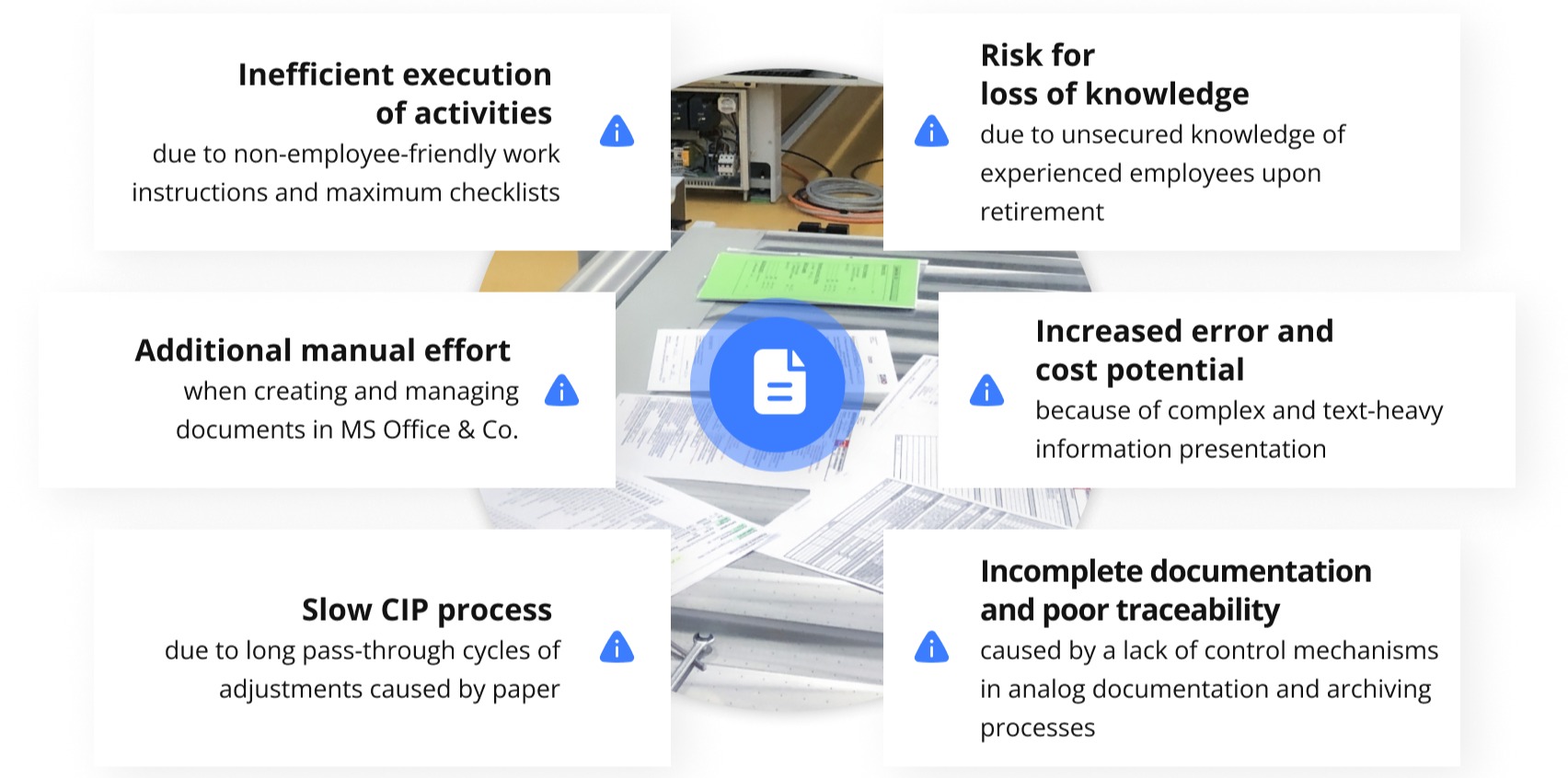
Our employees' time is precious. They shouldn't have to use it searching through documents.
Project Engineer Process Excellence, KraussMaffei
All of this prevents manufacturing companies from establishing more efficient and high-performance production processes to increase company growth.
The good news: digital work instructions can be used to digitize employee-led activities and provide more comprehensible information as a real game changer in production.
Digital work instructions...
... are characterized by the fact that work steps are simply displayed using images and videos and interactive elements such as mandatory interactions guide the employee safely through the process.
Workers who carry out their activities using digital work instructions report enormous simplifications and increased safety in process execution and appreciate the ease of use of the multilingual software.
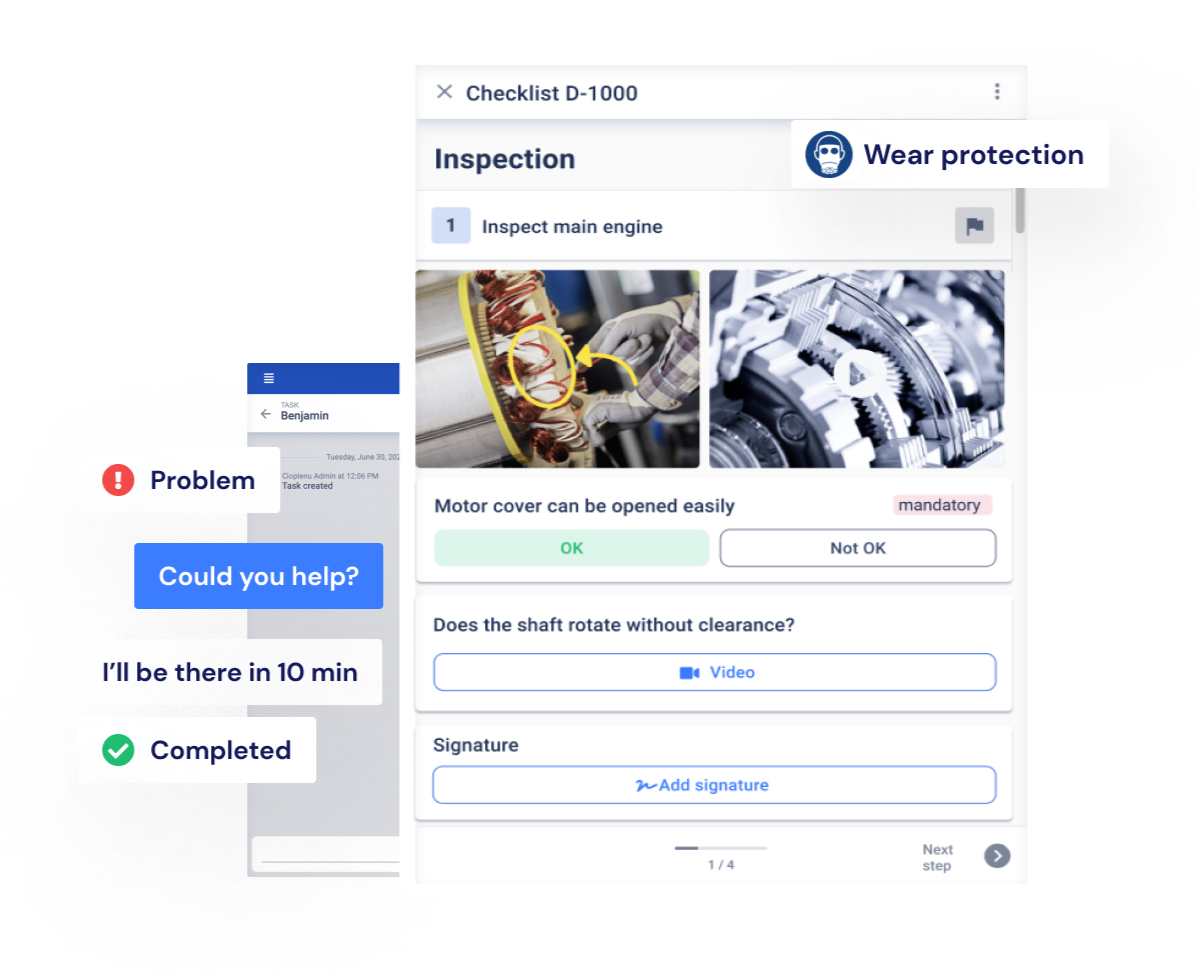
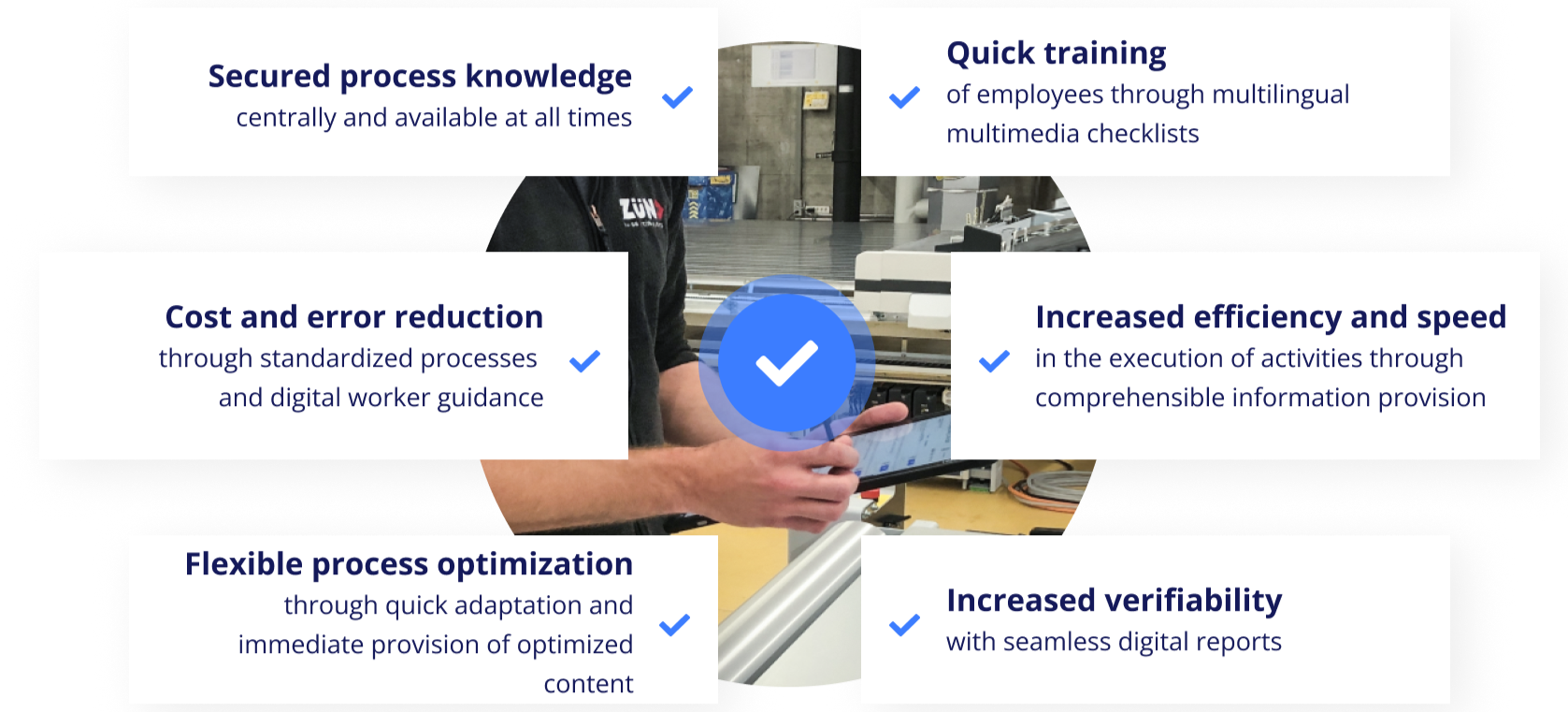
The Operations1 software is so easy to understand that it can be used by employees within 10 minutes training.
Head of Assembly Line, Krones
A field-proven software
Operations1 not only helps to reduce non-value-adding activities in production, but also supports companies in saving costs and unlocking previously tied-up time resources so that they can be used to create value for more growth.
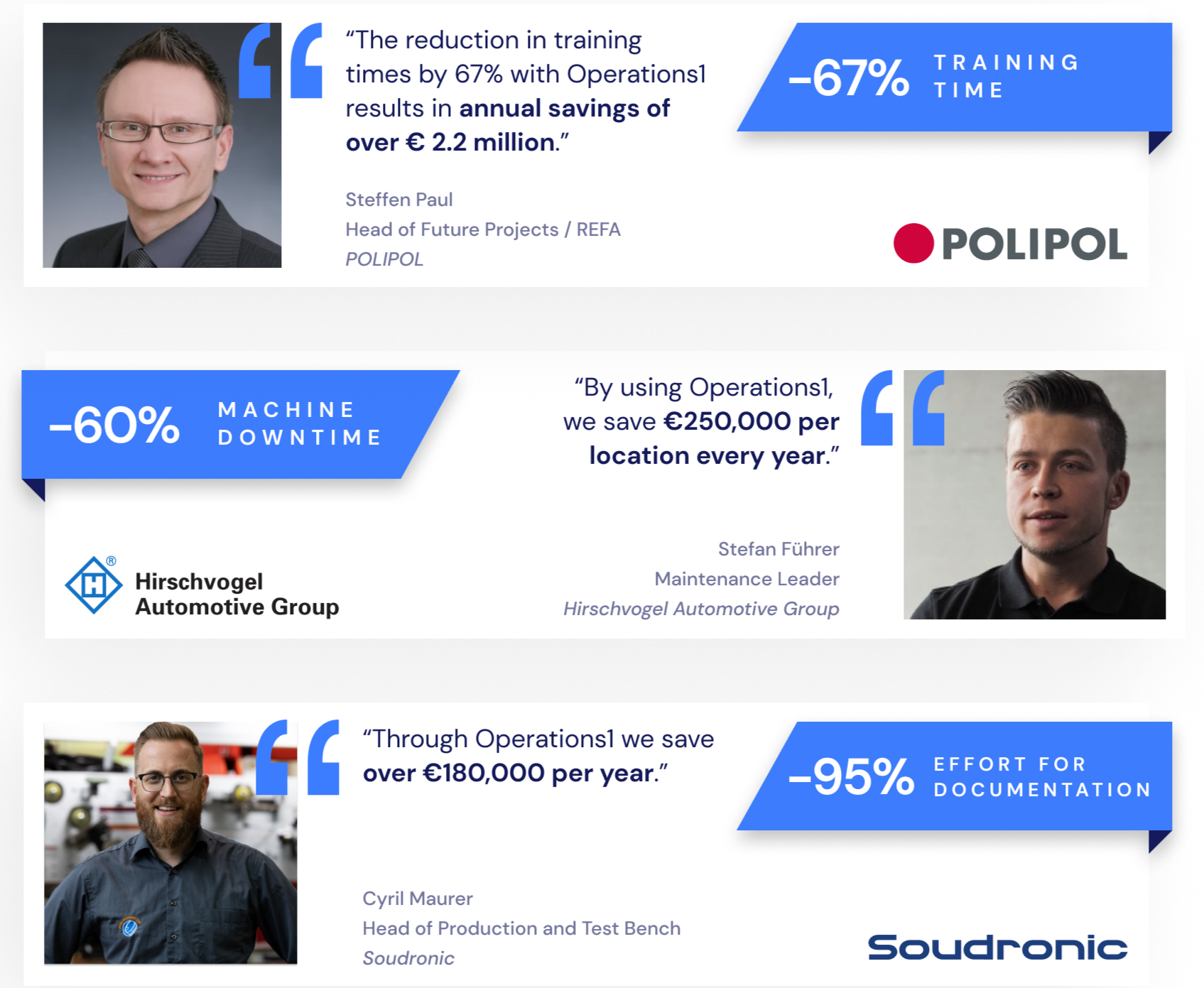
Always adding value - as a stand-alone solution or connected
Thanks to our integration solutions such as REST API, Operations1 can be connected to leading systems such as ERP, ME etc. on request. This allows you to exploit the full potential of your system landscape and your available order and process data.
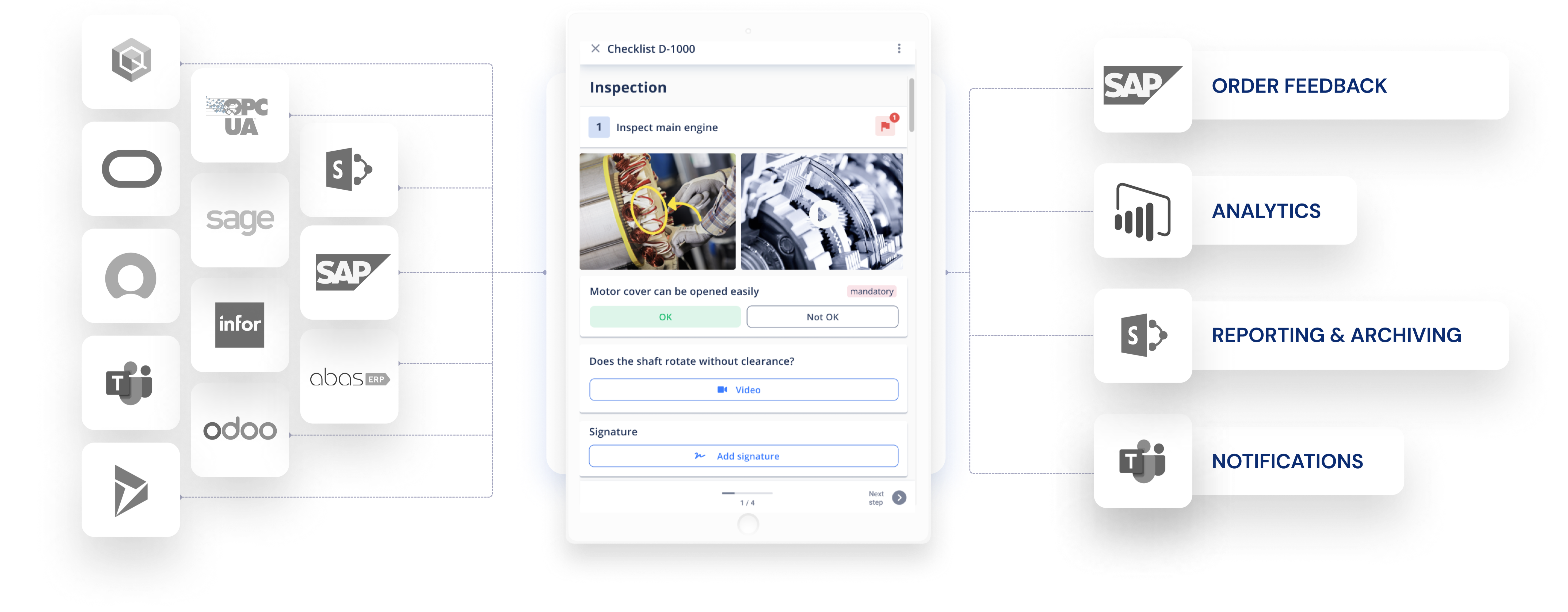
Well advised and supported
by our product experts
Take advantage of our team's years of experience and get in touch with our product experts:
Discussion of your use case
Analysis of existing problems in your process
Presentation of solution options with the Operations1 software
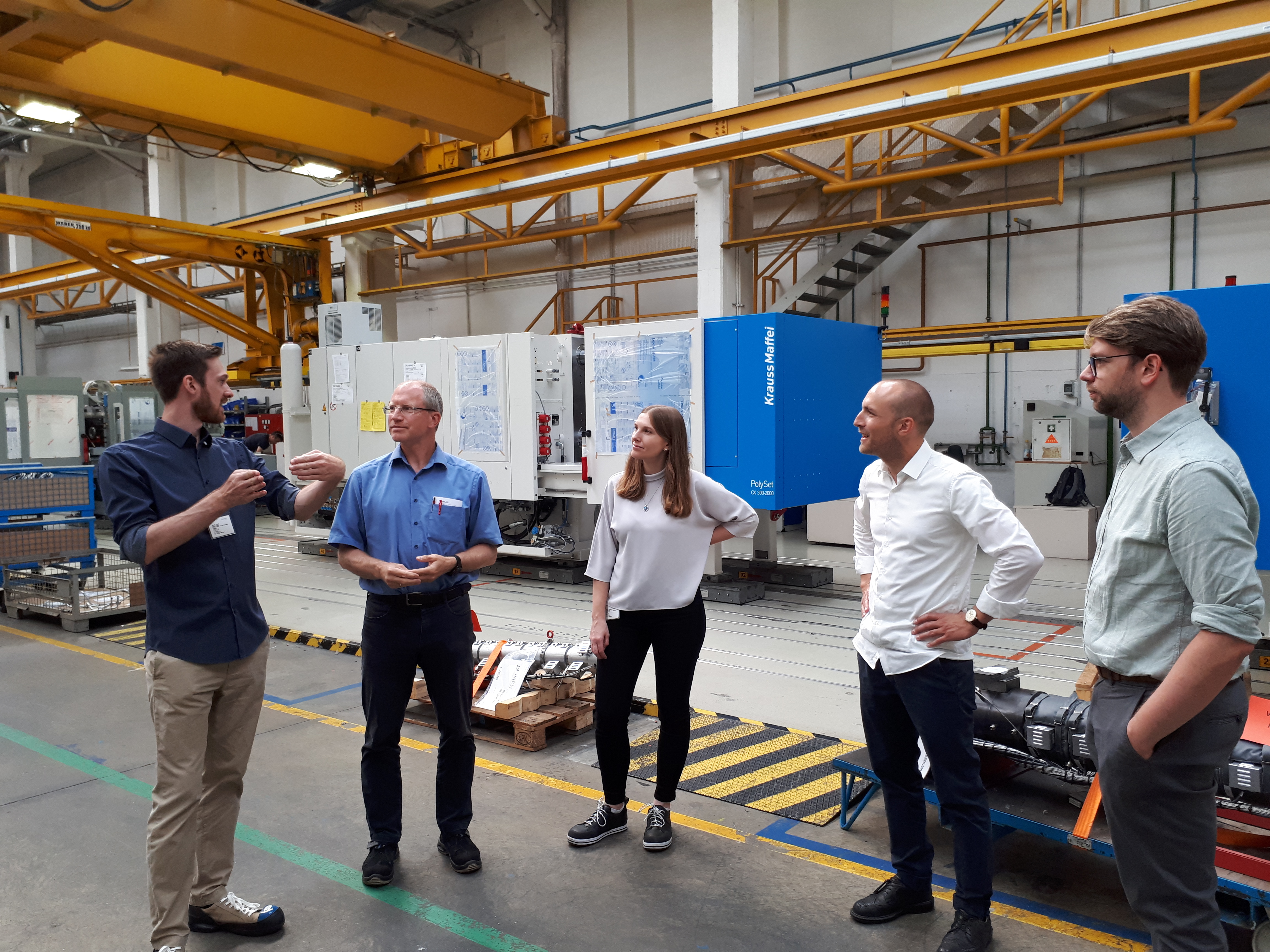
Get into conversation with us
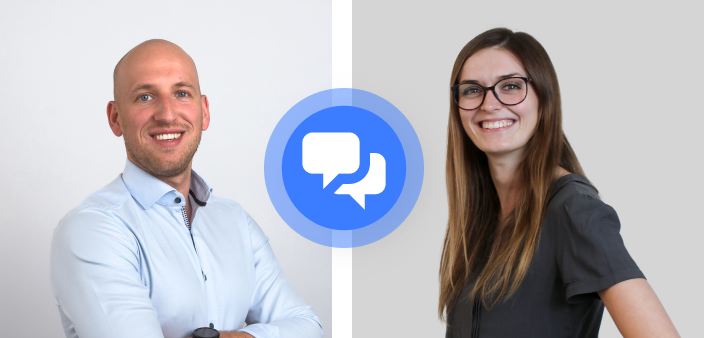
Use the exchange with our product experts to find out how you can benefit specifically from Operations1.