Hurdles to operational excellence
With operational excellence (OPEX), manufacturing companies pursue the goal of continuously increasing their efficiency, quality and flexibility in order to compete successfully in the global market. This requires lean, robust and transparent processes.
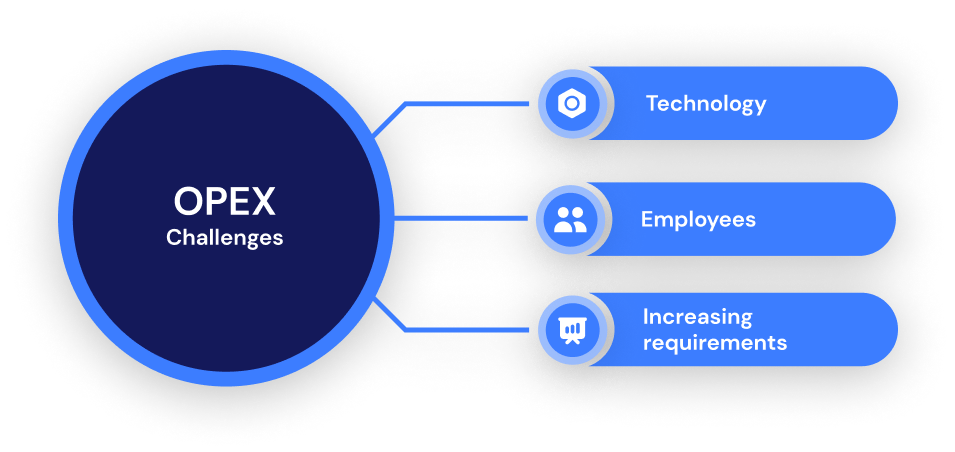
Technological challenges
Unstable and complex system consisting of ERP, MS Office products and paper
Low transparency and speed for CIP due to digitalization gaps
No standard software for document management, employee training and execution of activities
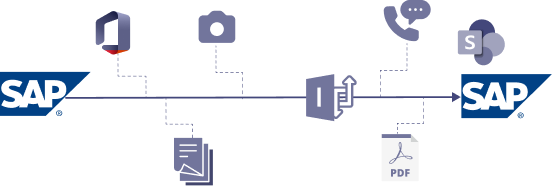
Employee-related challenges
Process knowledge is in the heads of employees and flows out when employees leave the company
Knowledge is not standardized and cannot be accessed centrally and uniformly
Slow training process and inefficient execution of tasks
Employee feedback for the CIP is not recorded uniformly
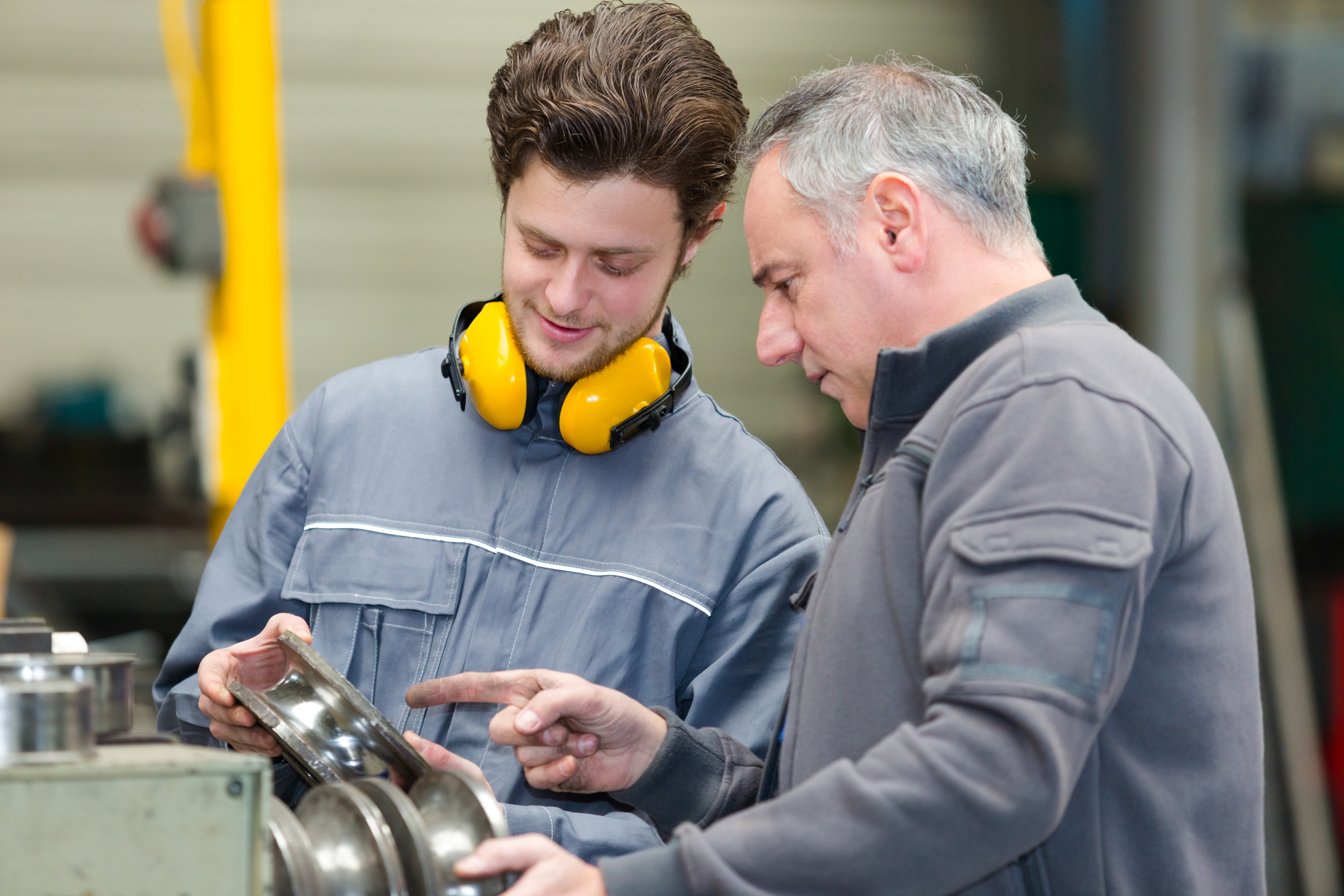
Increasing requirements
Customers, partners and auditors are placing increasing individualization demands on manufacturing companies in terms of products, process documentation and the provision of evidence. This increasing degree of individualization results in:
More complex information in processes due to increasing number of variants
Increased complexity for employees in variant-specific activities
Increased documentation, archiving and research costs
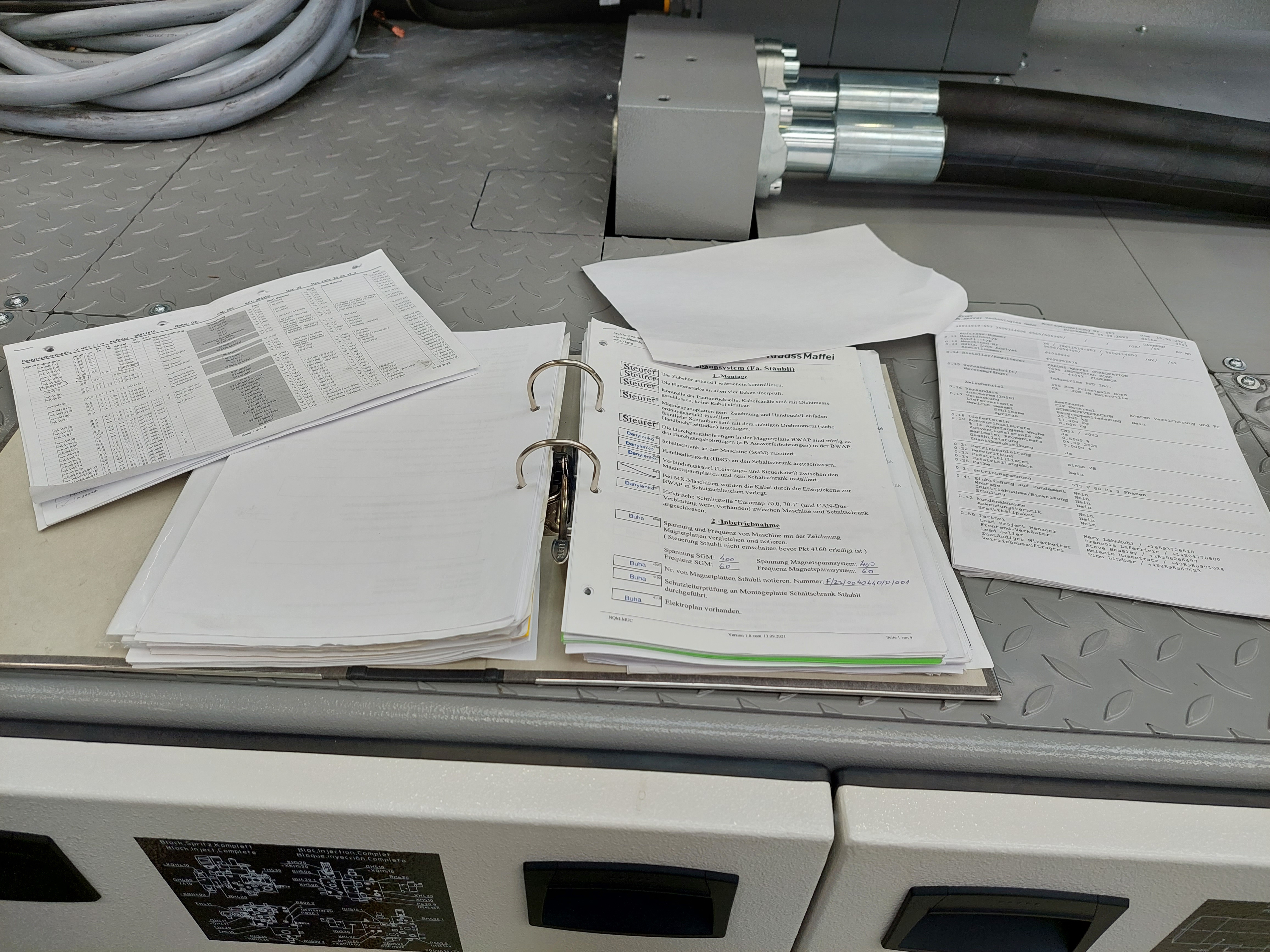
Simplify your IT landscape
Bundling document management and the execution of employee-led activities in a single software enables the introduction of process standards, closes digitization gaps and creates comprehensive process transparency for your CIP.
Reduced effort and centralized document management
Process execution in one software
Accelerated CIP process through process digitization
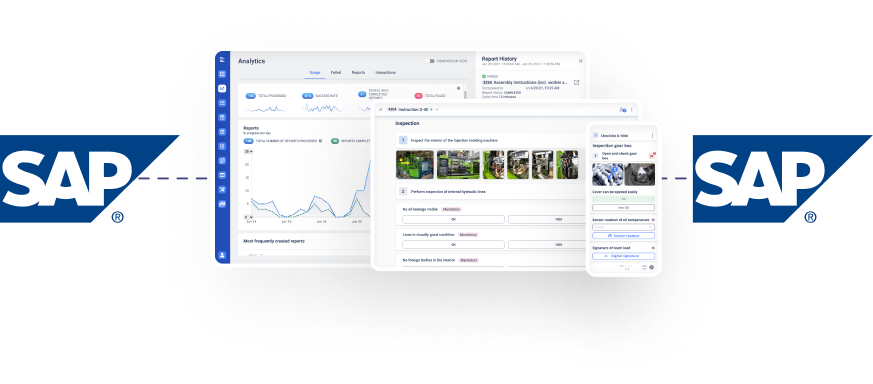
Empower your employees in production
By combining your knowledge management and process execution in one software, you can realize the following potential for improvement:
Securing and standardizing your employees' knowledge in digital work instructions
Quick training of employees and efficient execution of activities
Increase employee flexibility and satisfaction through step-by-step instructions that make work easier
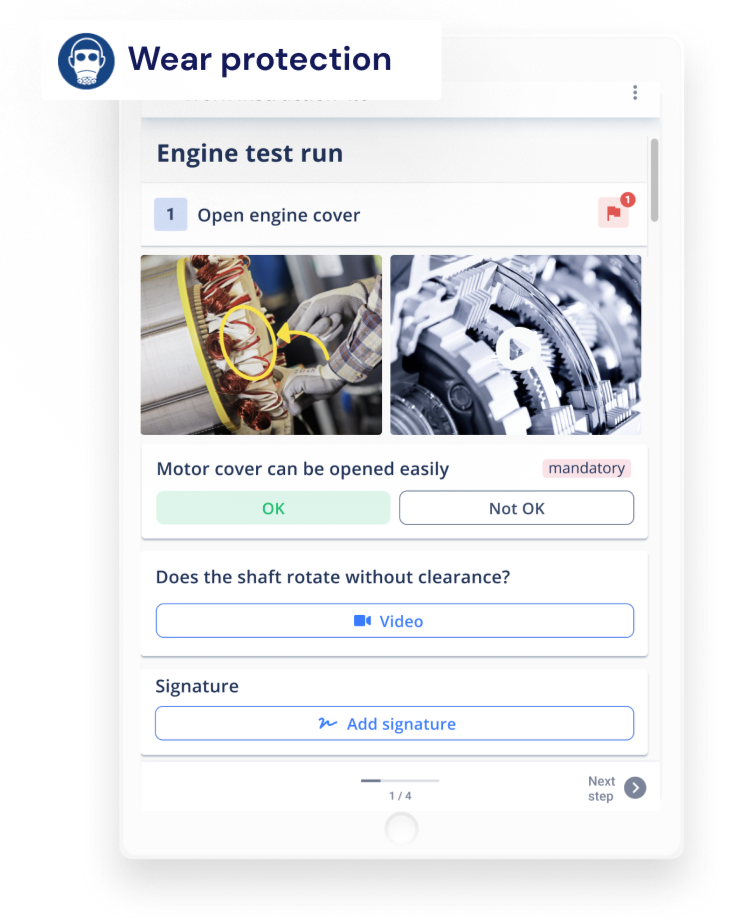
Complexity under control with reduced effort
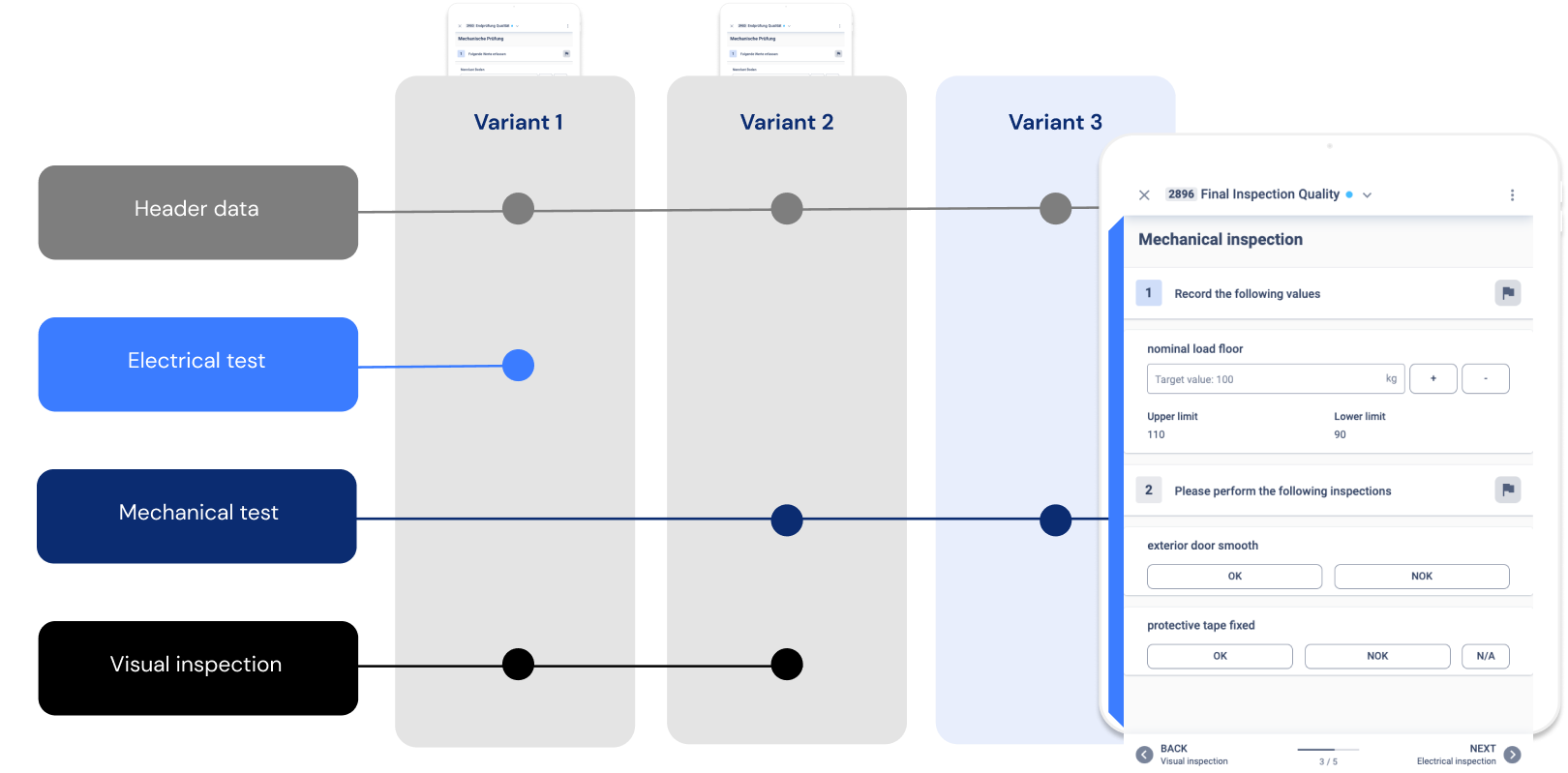
By using variant-specific quality inspection protocols, we reduce interpretation efforts for our employees.
Head of Assembly Line, Krones
Order-specific work information through modularity in software
Reduced complexity for your employees thanks to variant-specific work instructions
Effort reduction through documentation directly in the digital checklist
Increased verifiability through digital reports
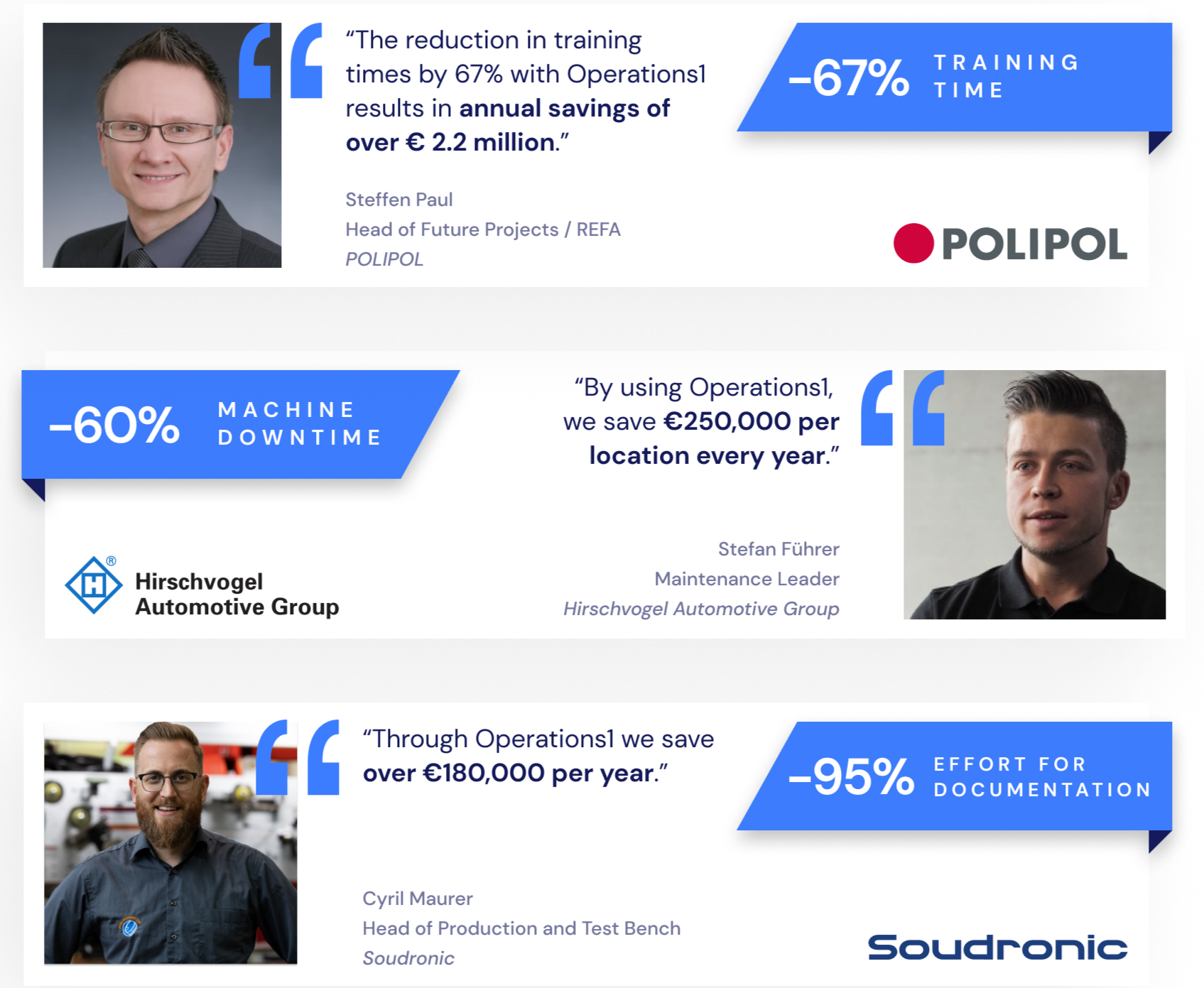
Get into conversation with us
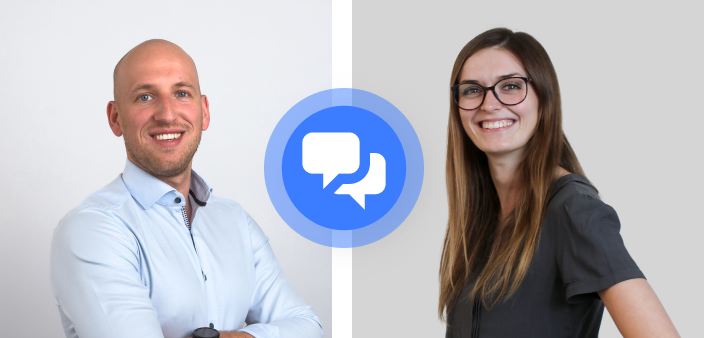
Use the exchange with our product experts to find out how you can benefit specifically from Operations1.