Industry 5.0 - Revolutionizing Manufacturing with Advanced Technologies
Industry 5.0 refers to the latest paradigm shift in manufacturing, characterized by the integration of advanced technologies to optimize production processes and create smarter, more connected factories. Building upon the concepts of Industry 4.0, Industry 5.0 takes a human-centered approach, emphasizing the collaboration between humans and machines to achieve unprecedented levels of efficiency, productivity, and customization.
This transformative industrial concept leverages cutting-edge technologies such as the Internet of Things (IoT), artificial intelligence (AI), robotics, and data analytics to enable real-time data collection, analysis, and decision-making. Industry 5.0 aims to enhance the manufacturing ecosystem by empowering workers with innovative tools and intelligent machines, ultimately resulting in improved product quality, personalized manufacturing experiences, and sustainable production practices.
By embracing Industry 5.0 principles, manufacturing companies can achieve higher levels of automation, connectivity, and agility. The seamless integration of humans and machines fosters greater flexibility, allowing for quick adaptability to changing customer demands and market trends. With the optimization of production processes and the utilization of data-driven insights, Industry 5.0 empowers companies to achieve operational excellence, reduce costs, and deliver innovative products with shorter time-to-market.
In summary, Industry 5.0 represents the next phase of industrial evolution, where advanced technologies converge to create intelligent, collaborative manufacturing environments. By embracing this transformative concept, companies can unlock new levels of efficiency, customization, and competitiveness in the dynamic landscape of modern manufacturing.
Industry 5.0: Transforming Manufacturing Companies Today
Industry 5.0 is already making a substantial impact on manufacturing companies today. With automation, IoT connectivity, data analytics, and customization capabilities, companies can optimize their operations, enhance productivity, and deliver tailored solutions to customers. Embracing the principles of Industry 5.0 allows manufacturing companies to stay competitive in an ever-evolving market landscape, fostering innovation and driving business growth.
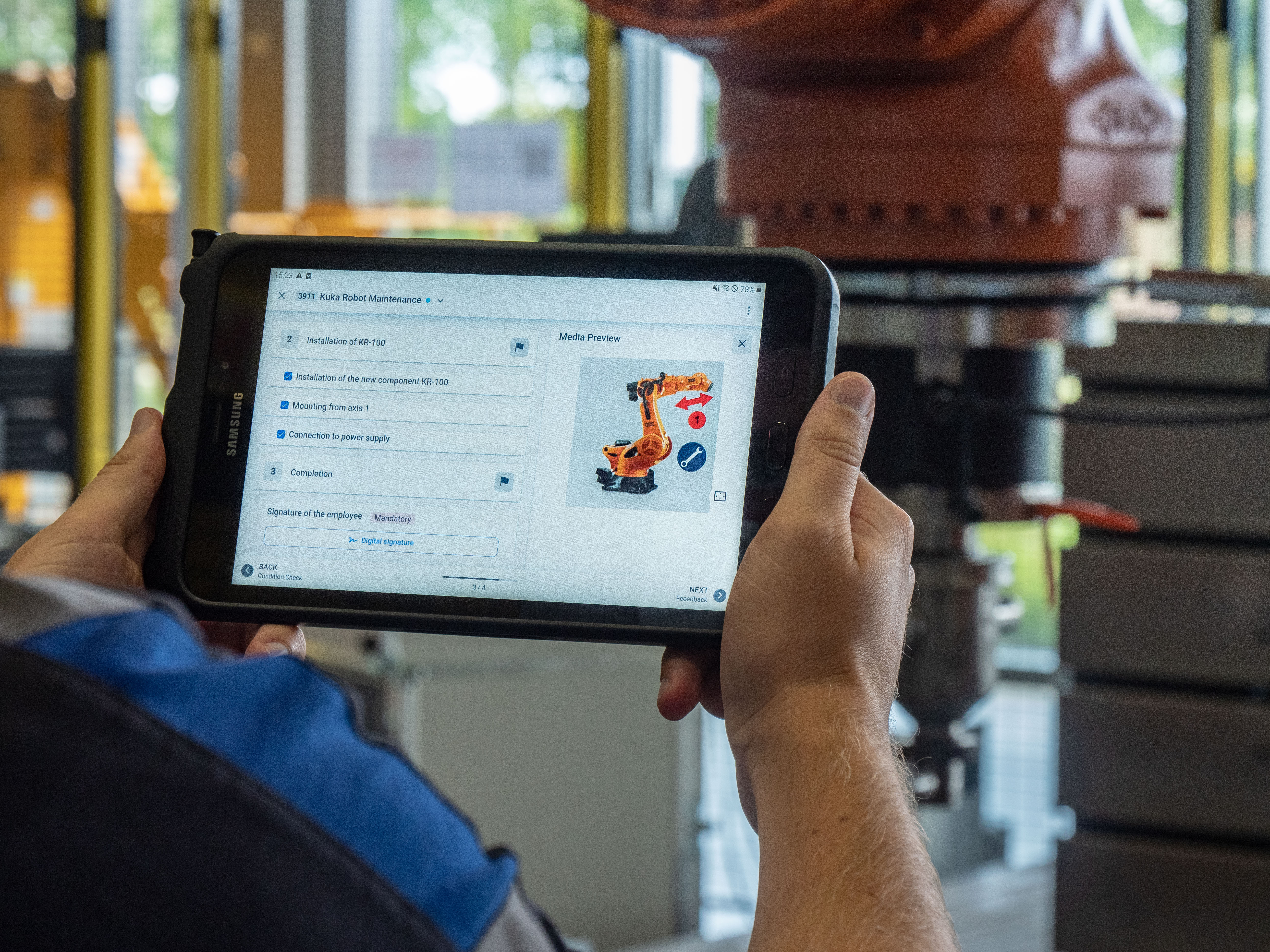
How a Connected Worker Platform Revolutionizes Industry 5.0
In the era of Industry 5.0, a connected worker platform plays a significant role in transforming companies. This advanced technology enables seamless integration between humans and machines, resulting in a more efficient and agile production environment. In this article, we will explore the crucial role that a connected worker platform plays in Industry 5.0.
Real-time Communication and Collaboration A connected worker platform enables real-time communication and collaboration among all stakeholders, whether it's between employees, machines, or systems. By utilizing mobile devices or wearables, employees can exchange important information, coordinate tasks, and solve problems quickly. This leads to efficient teamwork and enhances workforce responsiveness.
Access to Relevant Information A connected worker platform provides employees with instant access to relevant information. This includes work instructions, technical documentation, maintenance guidelines, and training materials. By delivering this information in real-time, employees can perform high-quality work without wasting time searching for information.
Digital Documentation and Data Analysis A connected worker platform facilitates digital documentation and recording of workflows, inspections, and maintenance tasks. All activities are captured and stored in real-time, enabling comprehensive traceability and error analysis. By analyzing this data, companies can gain insights, identify bottlenecks, and make continuous improvements.
Safety and Risk Mitigation A connected worker platform plays a crucial role in enhancing workplace safety. Through the use of sensors and IoT devices, potential hazards can be detected early on. Employees receive real-time alerts and guidance to navigate safety-related situations. This minimizes risks and creates a safer working environment.
Training and Skill Development A connected worker platform also enables employee training and skill development. By utilizing interactive training materials and virtual simulations, employees can enhance their skills and prepare for new requirements. This contributes to the continuous development of employees and increases their effectiveness.
Conclusion:
The role of a connected worker platform in Industry 5.0 is indispensable. It enables real-time communication, improved access to information, digital documentation, risk mitigation, and employee development. By integrating a connected worker platform, companies can enhance productivity, improve efficiency, and adapt to the demands of Industry 5.0.
The key to Industry 5.0: The Connected Worker Platform from Operations1.
With Operations1's Connected Worker platform, you digitize your processes end-to-end: from securing knowledge, to easy planning and intuitive execution of processes, to analysis and problem resolution. Learn more about Operations1's functional modules.
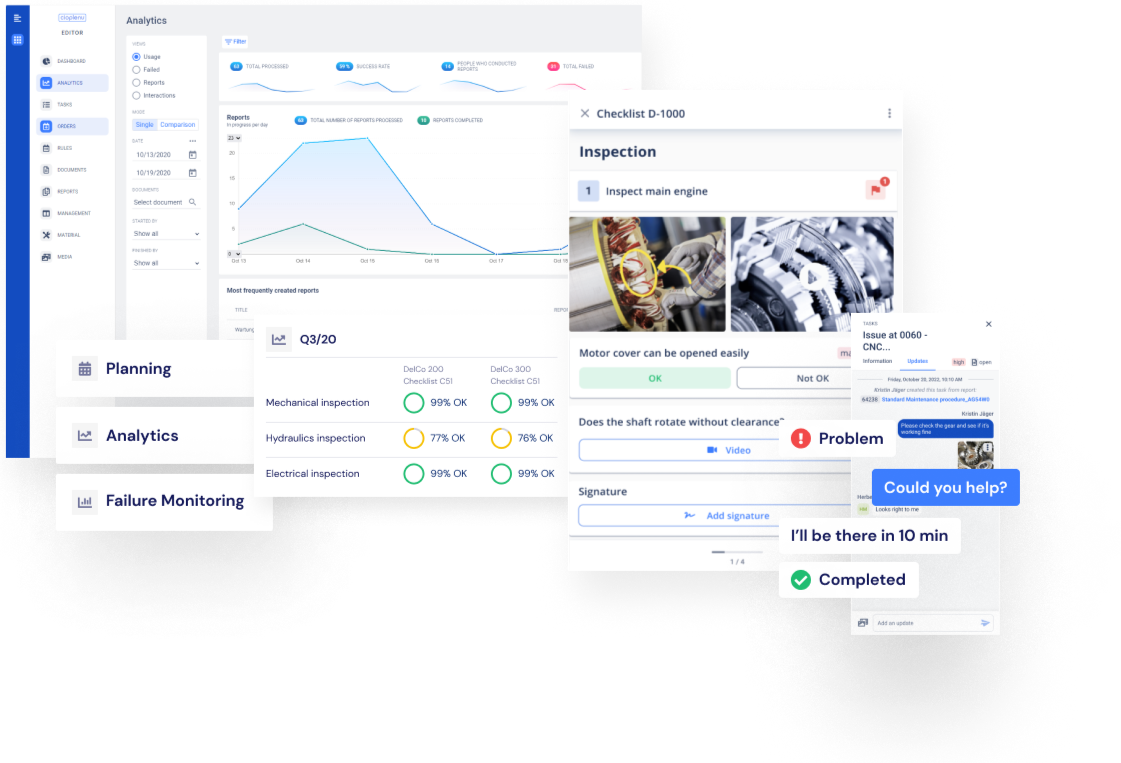