Lead new employees quickly and effectively to target productivity
In production, a company's ability to train new employees quickly and effectively is crucial to its success. Fast induction increases productivity and reduces errors, waste and rework. If a company manages to train employees quickly and effectively, new employees can reach their target productivity up to 70% faster.
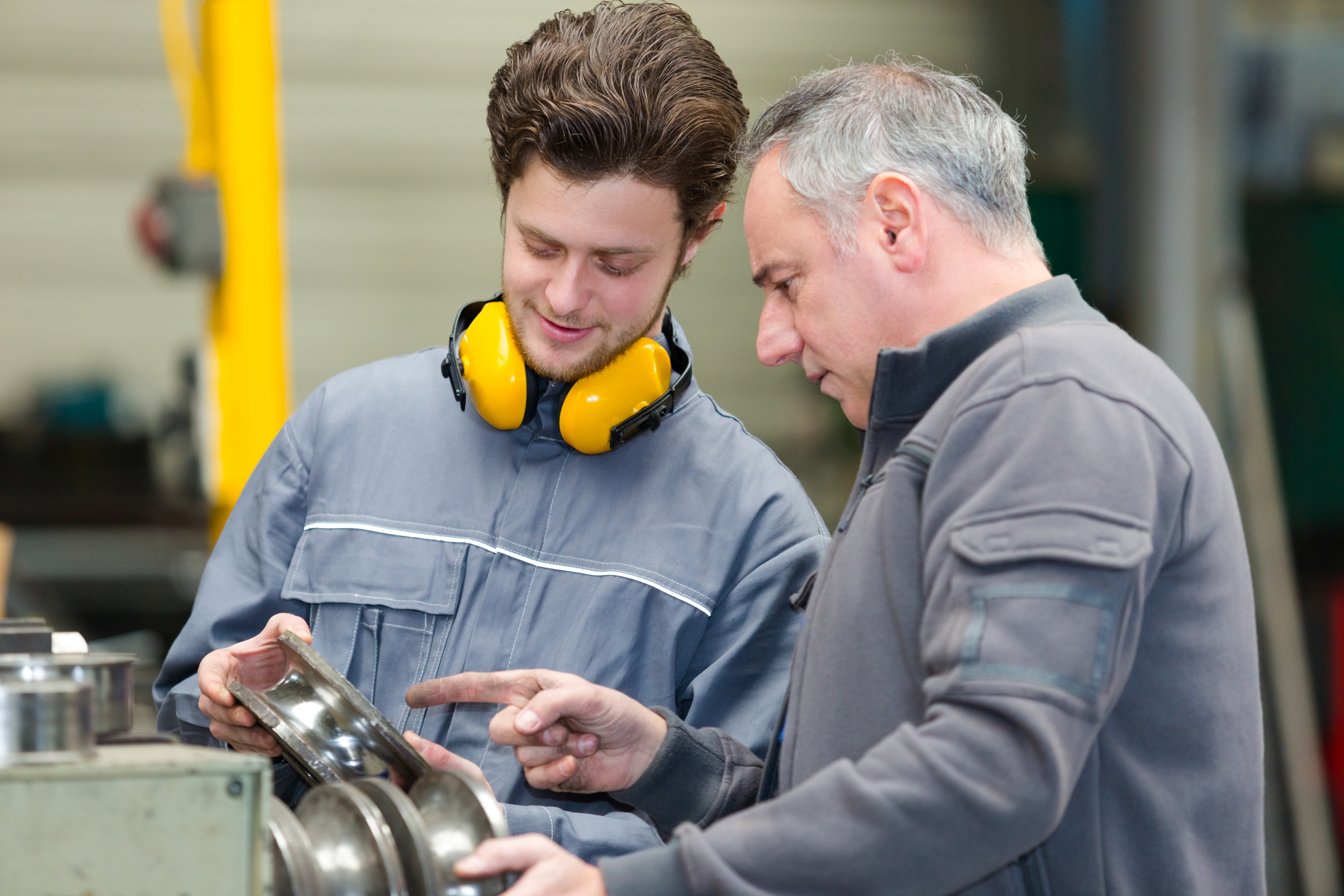
Current challenges in training
Traditional training processes in production are often time-consuming. They are often based on a large Leitz folder with documentation that new employees have to fight their way through. This documentation is sometimes misleading or difficult to interpret. Other companies second experienced employees to train the new employees. This not only leads to a dependency on a small number of skilled workers, but also results in even lower productivity, as the experienced employee, who has a high level of productivity in regular business, loses this through the training activity. In addition to knowledge transfer, there is also the challenge of variant diversity. In many production companies, employees have to be regularly familiarized with new product versions. This significantly increases the complexity of training processes and can unnecessarily slow down the induction of new employees.
Fast and effective achievement of target productivity as a competitive advantage
Compared to today's status quo, the use of a digital solution can leverage a great deal of potential for improvement. The digital provision of process instructions with up-to-date images and videos means that new employees are no longer overloaded with long texts, but instead receive easy-to-understand step-by-step instructions to help them carry out their tasks. These instructions can be accessed directly at the workplace via tablets or stationary terminals. This means that all relevant information is accessible at all times.
In this way, using a digital solution for training offers you a variety of benefits. The top 5 are:
Reduction of dependency on the knowledge of individual experienced employees: New employees can access standardized and up-to-date information at any time and are no longer dependent on other employees. This not only makes training easier, but also ensures that all employees work according to the same guidelines. This also increases process reliability and your first-time-right rate.
Faster productive cooperation of new employees: The use of easy-to-consume, step-by-step instructions ensures that new employees can work productively very quickly by working their way through the good instructions and the training runs automatically at the same time as the actual work.
Faster release of experienced employees: New employees who can work productively faster naturally also help to ensure that your valuable, experienced employees can work productively. The time you have spent in the past training new employees is minimized by Operations1.
More flexible employee deployment: In addition to productivity, rapid training also increases your flexibility. As every employee benefits from the provision of tailored information, you can deploy your employees flexibly in areas or product groups in which you are not an expert.
Smooth introduction of new product versions: New product versions are disruptive for production. Thanks to easily consumable knowledge, new versions of a product can be introduced into production without stress and produced to a high quality by all employees.
POLIPOL has also recognized these challenges and taken a significant step towards digitalization with the introduction of the Operations1 software. This solution enables the company to standardize its training processes and make them more efficient. By introducing Operations1, POLIPOL was not only able to reduce training time by 67%, but also achieve savings of over 2.2 million euros per year. These impressive results show how effective digital training processes are and how they contribute to securing the company's long-term success.
Editha Bertsch
Editha is an experienced project management expert for manufacturing companies. With a clear understanding of the specific challenges of the industry, she is passionate about developing innovative solutions.
Would you like to get to know Operations1 or do you have questions?
Simply fill out the contact form with your thoughts and goals. We will get back to you as soon as possible.