Increase output through optimal provision of knowledge in production
The European economy is falling further behind the USA and China. Too little innovation, too high energy prices, too little investment. However, companies from the DACH region in particular also stand for quality leadership at a high level and are respected worldwide for this.
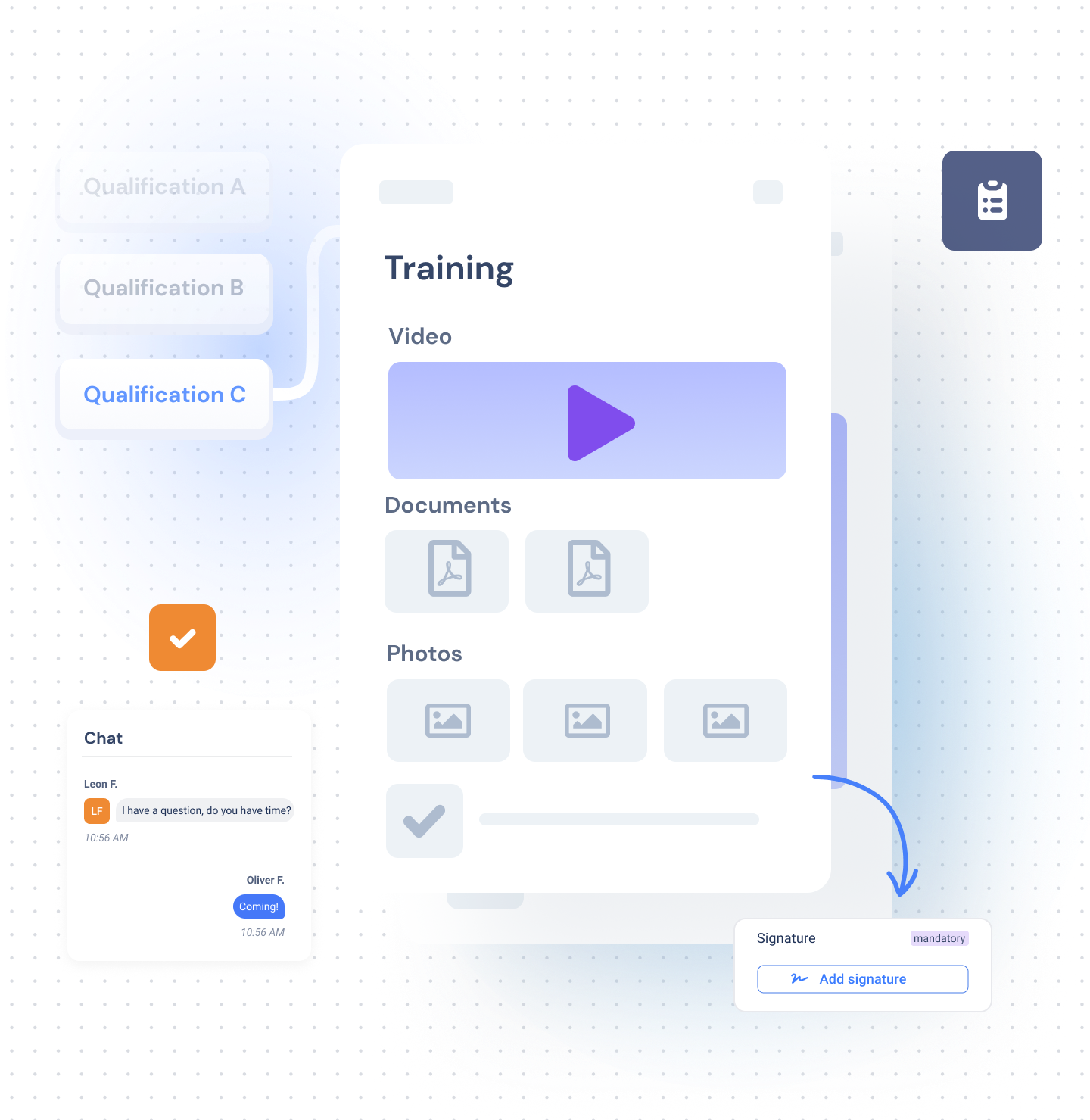
Current status of quality leadership in DACH
In many conversations, we are currently finding that manufacturing companies in the DACH region are finding it increasingly time-consuming and costly to maintain the quality of the goods they produce. One of the reasons for this is insufficient knowledge management and the resulting errors in production. The need for this has intensified in recent years due to factors such as
faster employee turnover
relocation of parts of production abroad and
a steadily increasing product complexity that has grown over the years
Companies counter these quality killers with 100% end-of-line inspections and often a high degree of rework. Both are measures that reduce productivity and ultimately output in production, but are necessary to compensate for the loss of knowledge caused by the above-mentioned points and the resulting lower quality. To break this vicious circle, it helps to make knowledge accessible to employees at a low threshold. By making knowledge easily available, you can quickly return to spot checks and significantly reduce your rework.
Status quo of knowledge transfer
Today, employees are often trained in a buddy system in which an experienced employee shows a new employee how to carry out the specified tasks. More and more, however, the situation is creating a whispering effect because there are too few “knowledgeable” employees and second- or third-hand information is becoming increasingly inexact. What's more, for employees who are considered to have been trained, the hurdle of asking questions when something is unclear is very high. None of us likes to admit that we don't know something.
How knowledge can be provided at a low threshold
Define the appropriate level of information: Today, highly complex products are sometimes assembled on the basis of drawings and simple checklists. We often find that what an employee is supposed to do is very well defined, but how he or she is supposed to do it is not. Make sure you provide your employees with the how to do complex tasks so that they can follow them step by step.
Choose a suitable medium for knowledge provision: Companies that have already documented the how to in production for their employees often do this in text instructions with pictures. These are difficult for employees to consume. People often learn activities better through visual support, such as short video clips, as these appeal to the human brain more vividly and intuitively. Small portions also make it easier and quicker to absorb information.
Make the knowledge easily accessible to your employees: If you successfully implement steps 1 and 2, this unfortunately does not automatically mean that your employees will also consume the knowledge. The good information, which can easily be used in video clips for the activity to be carried out, ends up on large sharepoints or in specialized systems where employees first have to log in and search for the knowledge. Operations1 offers the ideal platform to provide employees with all the information they need for their work and to consume the knowledge easily and at any time.
Incidentally, another advantage of providing knowledge is the standardization of processes. Clear and uniform instructions ensure that all employees work according to the same standards. The low-threshold provision of knowledge enables you to achieve consistently high quality over the long term.
Editha Bertsch
Editha is an experienced project management expert for manufacturing companies. With a clear understanding of the specific challenges of the industry, she is passionate about developing innovative solutions.
Would you like to get to know Operations1 or do you have questions?
Simply fill out the contact form with your thoughts and goals. We will get back to you as soon as possible.