Company-wide standardization through global work instructions
Die Standardisierung von Prozessen ist ein zentraler Faktor für die Effizienz, Qualität und Wettbewerbsfähigkeit produzierender Unternehmen. Wir zeigen Ihnen, wie Sie Ihre Prozesse durch globale Arbeitsanweisungen standardisieren können.
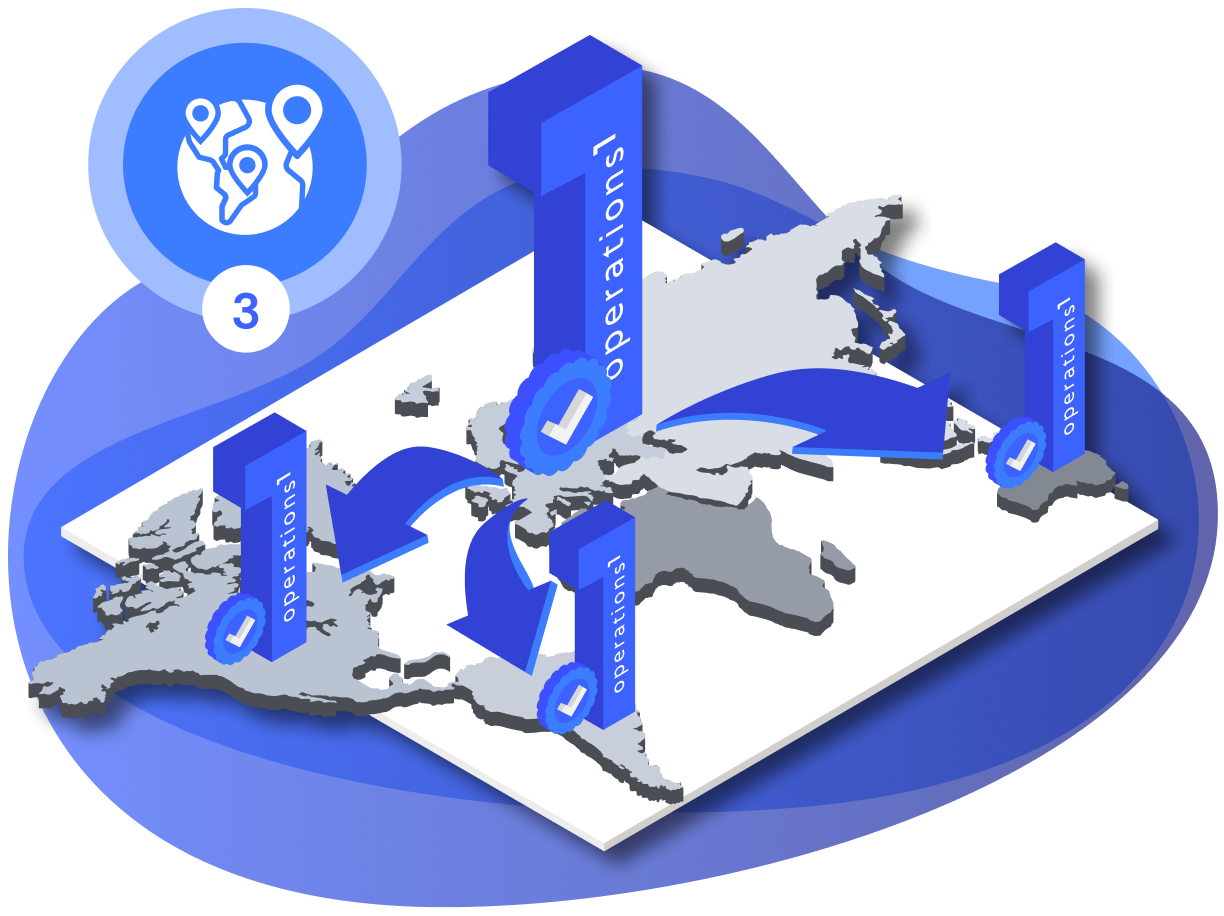
The 10 steps at a glance
Standards ensure that all products are produced in the same quality and in a process that is deemed efficient. However, in a globally networked production environment with multiple locations, it can be difficult to ensure uniform processes everywhere, as information between different locations in different languages is often difficult to transfer. Global instructions offer an effective solution to achieve company-wide standardization and increase the efficiency of all production sites. By sharing knowledge, companies can learn faster and each site does not start with its own self-optimization, which costs time and is unnecessary when processes are shared across sites. But how can global instructions be successfully implemented and used?
Define a pilot area: Define an initial line or product that you want to standardize globally
Determine who is responsible: Global standardization of processes is very important and not a side project. Clear responsibilities help to structure and drive the project forward.
Carry out a process analysis: Analyze the processes of the selected pilot area at the various locations to identify differences and develop a common standard.
Set up a digital platform: Providing global instructions requires software where they are centrally stored and accessible to each location in real time. Ideally, the software should translate the instructions into the different languages of the production sites in real time. Specialized software saves you the tedious distribution of knowledge via Sharepoint or similar.
Create standardized instructions: Experienced employees and experts can now create instructions directly in the newly implemented platform. Use short video sequences wherever possible to present process knowledge in an understandable way.
Take the pilot area live: After successfully completing the creation of instructions for a small, defined sub-area, the production sites can test the instructions live. Set up a feedback process, preferably via your digital platform, so that necessary changes can be identified quickly across national borders.
Incorporate feedback: Review employee feedback and incorporate it into the work instructions where appropriate. Make sure to inform all employees about the changes, preferably directly the next time they carry out the activity via your digital platform.
Monitor implementation regularly: Use the evaluation options to analyze that instructions are being followed in all plants.
Make continuous improvements: Instructions need to be updated based on new feedback, new technologies or changing requirements, to keep them current.
Ensure communication: Communicate the importance of global instructions clearly to all employees and ensure an open and transparent information policy about changes.
The successful implementation of global work instructions requires clear structures, well thought-out planning and the integration of suitable technologies. By standardizing processes, companies can not only increase their efficiency and product quality, but also improve knowledge management and ensure consistent production across all locations. The steps listed for the introduction of global work instructions provide the basis for introducing standards across locations in your company and thus increasing your quality and efficiency.
Editha Bertsch
Editha is an experienced project management expert for manufacturing companies. With a clear understanding of the specific challenges of the industry, she is passionate about developing innovative solutions.
Would you like to get to know Operations1 or do you have questions?
Simply fill out the contact form with your thoughts and goals. We will get back to you as soon as possible.