Operations1 templates for your processes
At the heart of Adaptive Process Execution (APE) is the context-based and interactive document for your employees. APE is widely applicable across departmental boundaries and document types. This exemplary selection of adaptive templates gives an insight of the application breadth. The templates can be adapted to your use case on site simply via drag & drop, newly created or imported based on your documents.
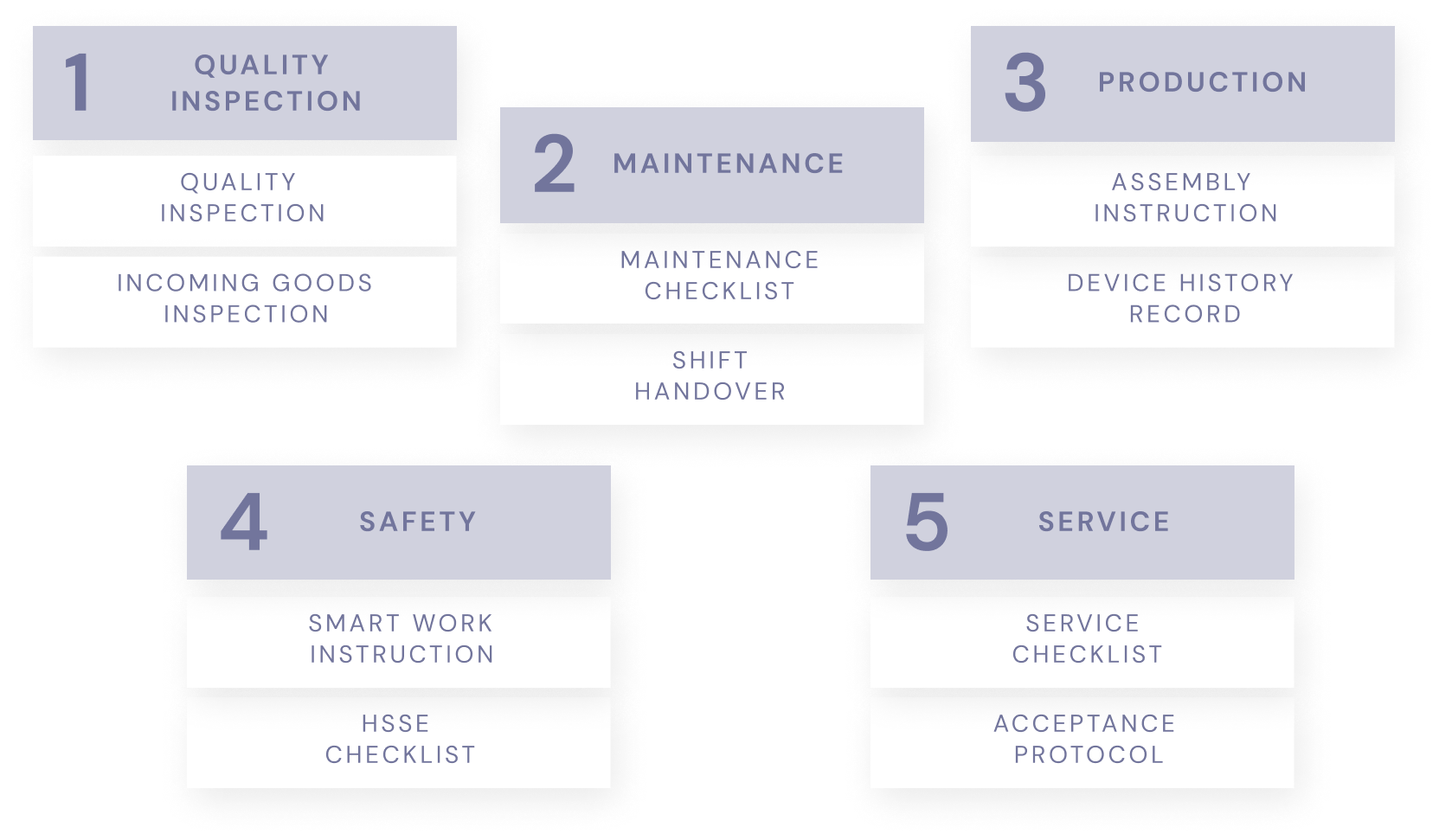
1. Quality inspection
Complex and paper-based checklists, inspection plans and protocols are a thing of the past. With the Operations1 cloud software, you provide your employees with intuitive software that makes any inspection process simple, efficient and insightful.
Let’s talk about your specific use case.
2. Maintenance
Empower your workforce with image- and video-based maintenance checklists. Perform your maintenance planning intelligently, provide maintenance knowledge paperless and in real time and set global process standards. Connect Operations1 with your existing systems such as ERP and MES if required.
Let’s talk about your specific use case.
3. Production
Using image and video-based assembly instructions, your employees deliver highest quality and efficiency regardless of location, language or qualifications. Integrated checkpoints and media return make worker self-testing digitally evaluable.
4. Safety
Compliance with environmental, safety and health standards can only be maintained through easy-to-understand guidance and continuous audits. With Operations1, you make this happen. Company-wide and in only a few weeks time.
Let’s talk about your specific use case.
5. Service
Prevent duplication of effort and complexity. Replace paper-based service logs, retrospective digitization, and complex manuals with digital image- and video-based instructions and automatically generated logs.
Which template is particularly relevant for you?
Have you discovered a template that is particularly relevant to you? Let’s talk about your specific use case. Let us know your goals and we’ll get back to you right away!