Preventive Maintenance (PM) is the regular and routine maintenance of equipment and assets to keep them running and avoid costly unplanned downtime due to unexpected equipment failures. Examples of preventive maintenance include equipment inspections, cleaning and lubricating critical equipment, and tidying the production floor.
Maintenance planning software: The intuitive last mile
Perform your maintenance planning intelligently, provide maintenance knowledge paperlessly and in real time, and set global process standards. Connect Operations1 with your leading systems such as ERP and MES if required.
Get to know the software in just 3 minutes and get an overview of the functionalities and application areas of Operations1.
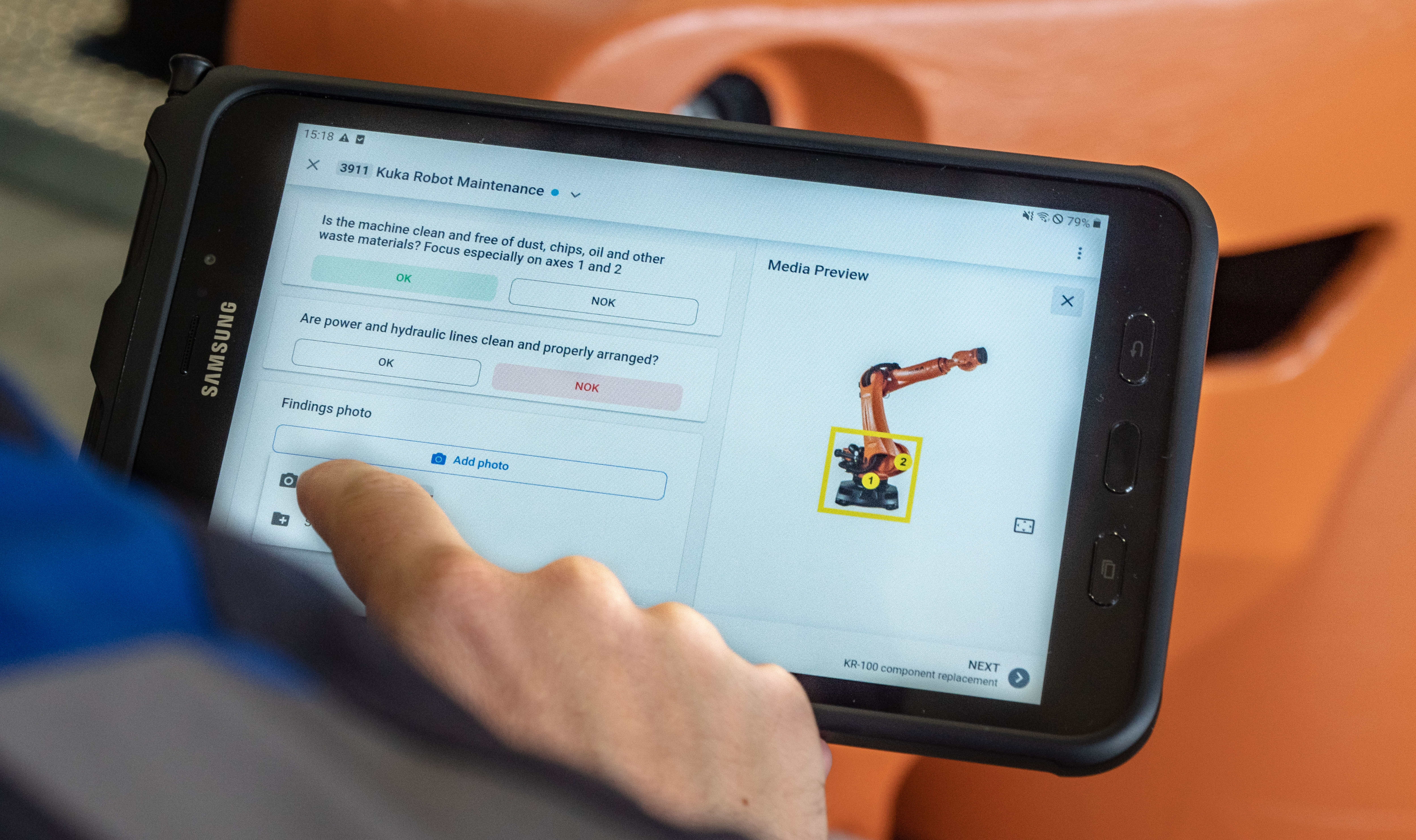
- -85% reduced downtime
- +21% higher productivity
- -95% less effort for documentation
The Operations1 software in maintenance
With Operations1, you enable easy planning, execution and record keeping of maintenance work. Create detailed maintenance calendars digitally, link intuitive maintenance instructions and checklists, and automatically document your activities and findings.
Maintenance planning software: Features for industrial use
Drag and Drop
Simplify the creation and updating of your documentation
Pictures and videos
Include images and videos in your documents to increase comprehension
QR-code scanning
Start processes via search function or by scanning a QR code on your machine
Recurring orders
Schedule recurring maintenance tasks fine granularly in Operations1
End-to-end integration
Use orders from your ERP, MES or CMMS and work operationally in Operations1
Incident management
Create tasks, assign them and ensure implementation
Structural classes
Organize your work based on your machines, locations or teams
Digital reports
Get full transparency on performed activities and findings
Cloud approach
Standardize processes and leverage your process knowledge from the cloud
Maintenance planning: Success Story
Learn how the Hirschvogel Automotive Group, a global automotive supplier, uses digital maintenance instructions and checklists to make knowledge available globally, increase reaction times and reduce costs.
Maintenance software: Frequently asked questions
What is preventive maintenance?
What is maintenance management?
Maintenance management comprises all operational measures to prevent machine failures and increase plant availability. At the same time, maintenance measures ensure optimized operating processes and increased operational reliability.
Can maintenance orders be emailed to my team?
Work orders get automatically assigned to the respective maintenance team member within the Operations1 software. Therefore, workers don’t need to switch systems any longer between planning, execution and reporting. Work planning can be conducted within Operations1 or through integration with other systems such as the ERP System or MES.
What is in a maintenance plan?
Maintenance teams use a maintenance plan to ensure that maintenance activities are carried out properly and at the right time in order to keep overall equipment effectiveness high and spare parts and personnel costs low. Maintenance planning can be time-based, cycle-based or condition-based.
Why is maintenance planning important?
Suboptimal maintenance planning often results in so-called over-maintenance or under-maintenance. With over-maintenance, maintenance capacities are scheduled unnecessarily, expensive spare parts and operating resources are consumed, and valuable production time is wasted. Insufficient maintenance can lead to unnecessary wear, resulting in unplanned production downtime and time-consuming and expensive temporary repairs. This in turn disrupted the entire production schedule and resulted in enormous costs.