Digital assembly and control processes
Instead of maximum lists, provide your employees with plant-type-specific instructions and checklists, which you can easily create and centrally organize using drag & drop, interaction functions, modules, etc.
Integrate control steps into assembly instructions and document serial numbers and product codes of your components by scanning directly Operations1. Automatically generated reports provide complete documentation of all assembly and inspection steps and enable reliable verification.
See how you can digitize your machinery & plant assembly with Operations1
Get to know the software in just 7 minutes
Get an overview of the functionalities and application areas of Operations1.

Digital machinery & plant assembly: 6 reasons for Operations1
Why do leading mechanical and plant engineering companies choose Operations1 to digitize plant assembly documentation?
Enormous industry expertise
Our dedicated industry experts at Operations1 work with 100+ leading companies from manufacturing day-to-day and are keen to support you.
Proven RoI
With every client, we jointly identify value drivers and collaborate on realization. We are happy to share our rich experience of successful implementations.
Broad functionality
Our comprehensive platform enables you to fully digitize operational processes from planning over execution to analytics.
Easy and risk-free start
Through the SaaS approach, you can start tomorrow without transformation projects and heavy implementation cost. Just get in touch with us.
Great collaboration
We aim to create long-term partnerships with our clients. Our service satisfaction of 99,5% and the splendid customer retention speak for themselves.
High Scalability
Our technical foundation and platform features are made for enterprise customers in order to scale across sites and geographies in an easy way.
Interested? Get to know Operations1 in a live demo
We would be happy to show you the functions of Operations1 in an individual live demo and answer your questions.
Summary: Digital machinery and plant assembly with Operations1
The provision of assembly instructions with integrated worker self-testing as well as the complete documentation of process data in Operations1 can realize many advantages for your machinery and plant assembly:
Reduced effort in work preparation and for the employee
High customer confidence through complete documentation
Simple verification through automatically generated digital reports
Quality assurance and higher process reliability
Subsequent defect image analysis for deriving CIP measures
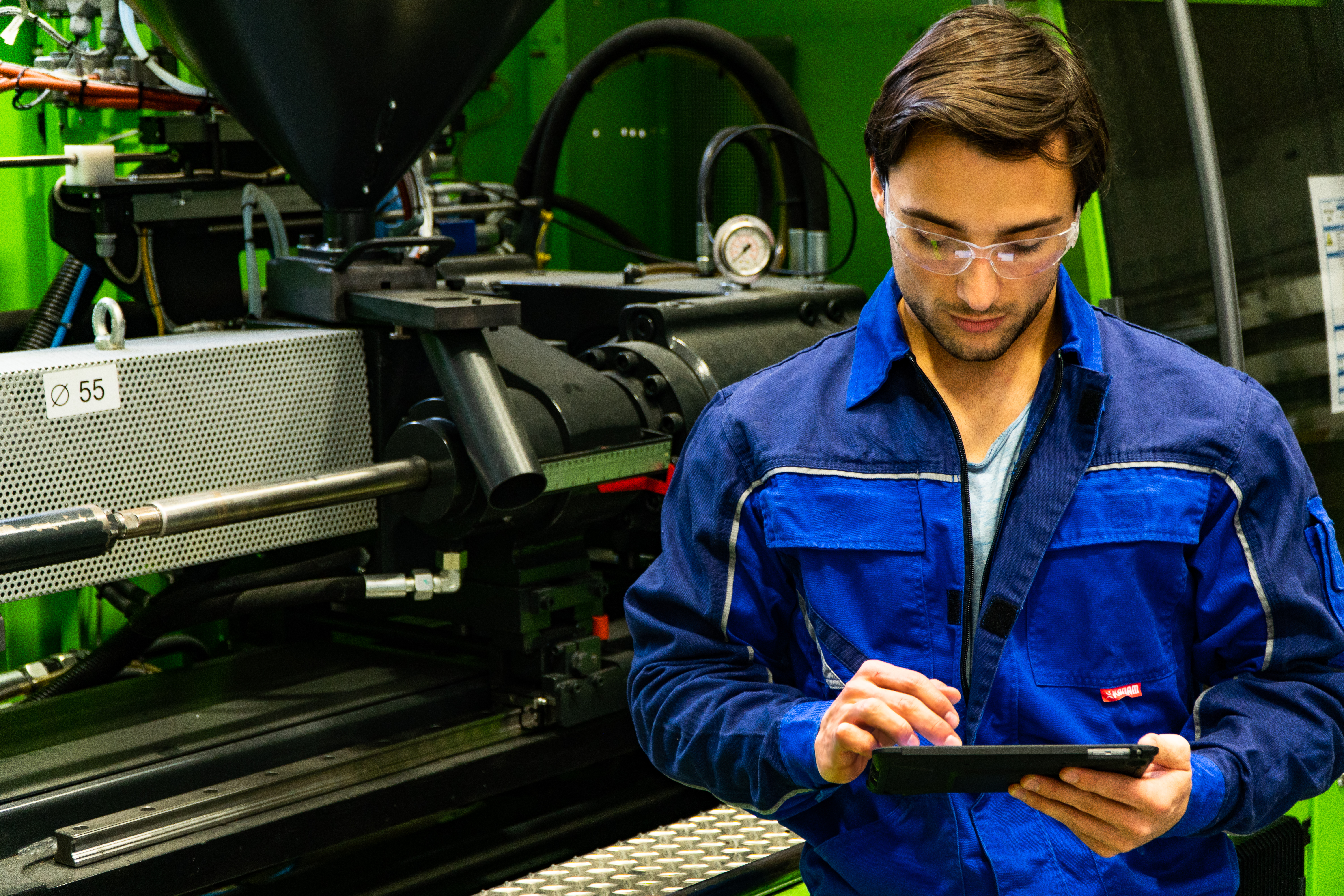