Eliminate productivity killers in processes: Clear information. Establish standards. Order-specific info. Quick training. Less effort. More automation.
Manufacturing companies are facing growing challenges in their production.
Loss of knowledge due to employee fluctuations
Increasing international competition
Increasing cost pressure
Identify unused potential in processes
There are many factors in production processes that cause inefficiencies and are real cost and effort drivers.
Process knowledge is in the heads of your employees
Information is not product-specific and difficult to understand
New employees have to be trained in complex processes in a time-consuming way
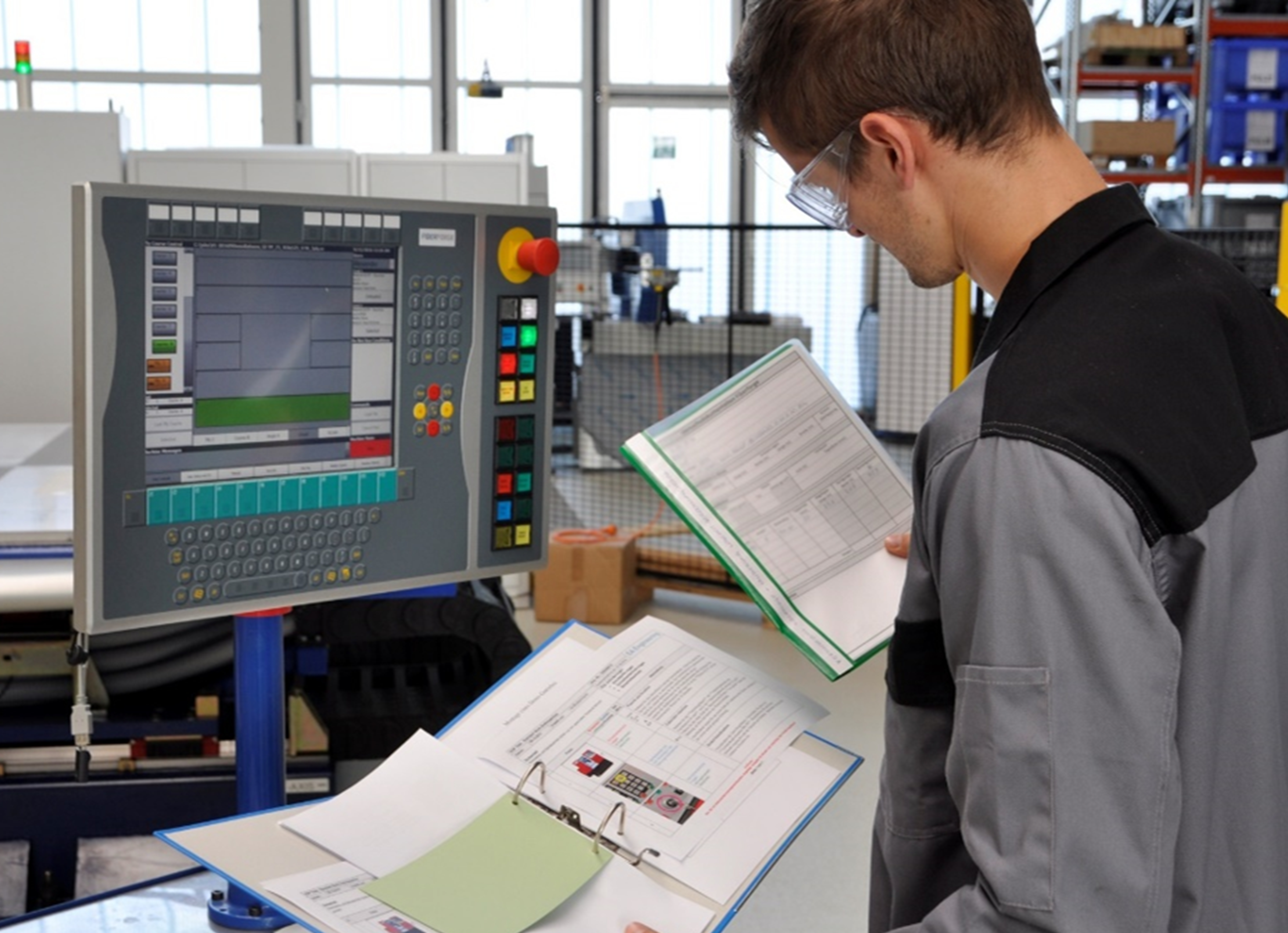
Utilizing productivity potential and strengthening production
Manage process knowledge and standards centrally
Secure your employees' knowledge with smart work instructions centrally in one software. Eliminate unnecessary search, change and provision efforts.
Provide variant-specific information
Provide your employees with instructions and checklists with order-specific information. Use modules or specific order data from your ERP/ME system for this.
Push improvements into processes quickly
Don't let MS Office and paper slow you down: change content directly and activate the improvements for your operational processes without any detours.
Smart documents created quickly
Create your digital work instructions or checklists with just a few clicks using the user-friendly drag & drop editor.
Wide selection of interactions for work steps
Easy integration of media such as images and videos
Efficient and intuitive no-code creation
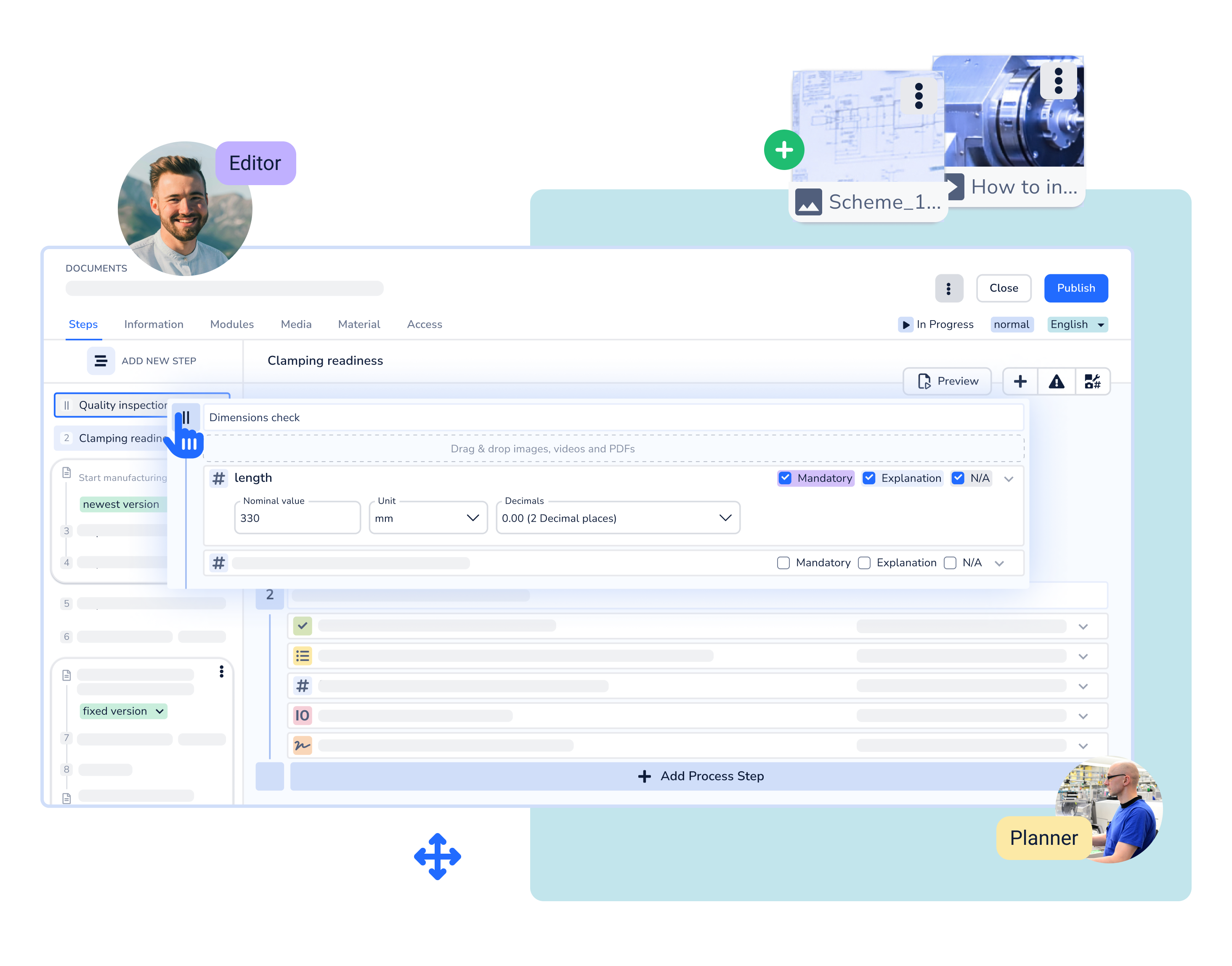
Managing a high variety of variants with reduced effort
Say goodbye to maximum lists: use a document as a module for mapping identical content in multiple documents.
Identical content maintained and updated centrally
Reduced effort and time savings
Less interpretation work for your employees
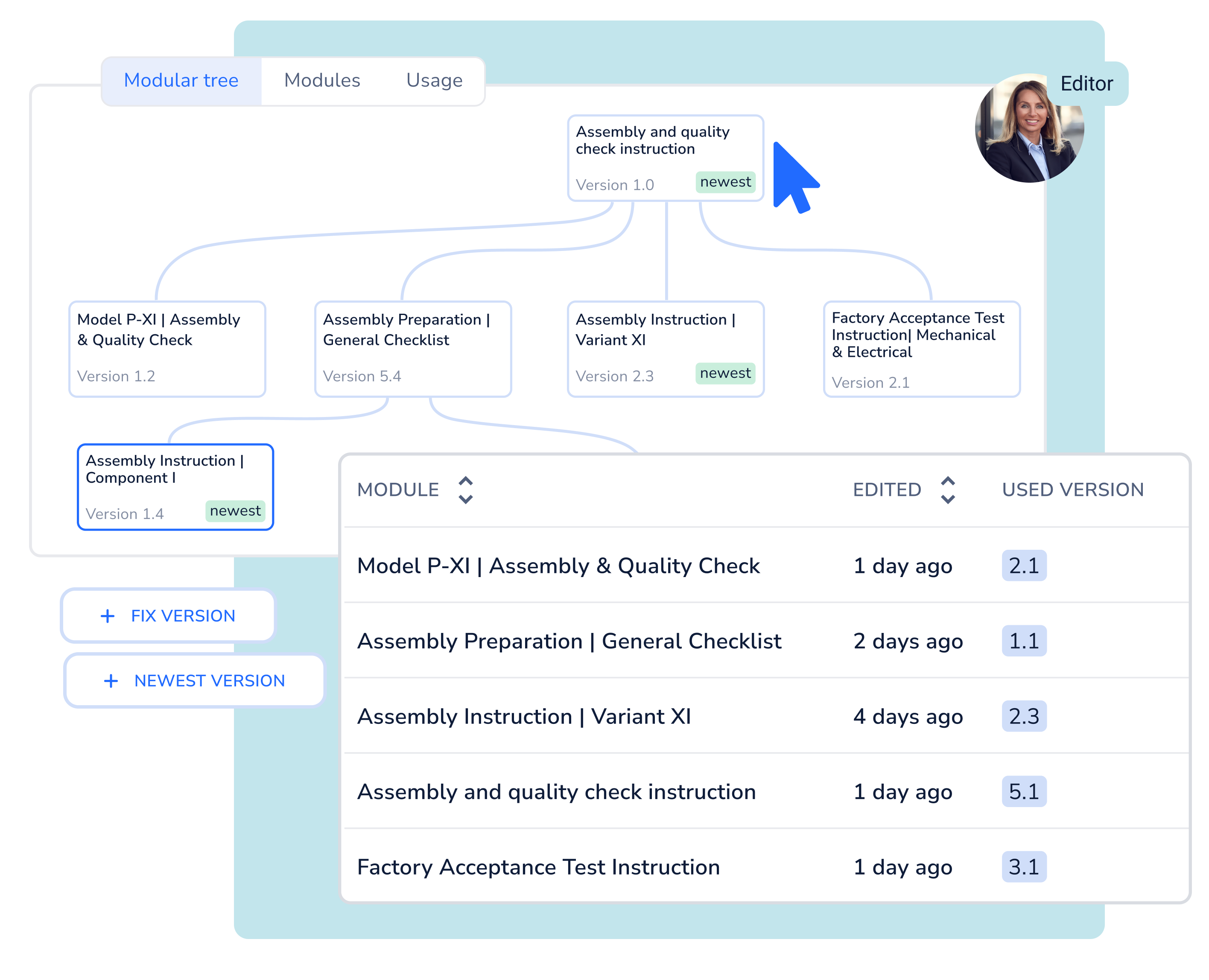
Improvements quickly documented and implemented
Be faster than paper allows and strengthen your CIP process with digital task and document management.
Employee feedback, errors and incidents captured digitally
Use of process data to derive improvement measures
Work instructions and checklists quickly updated and published
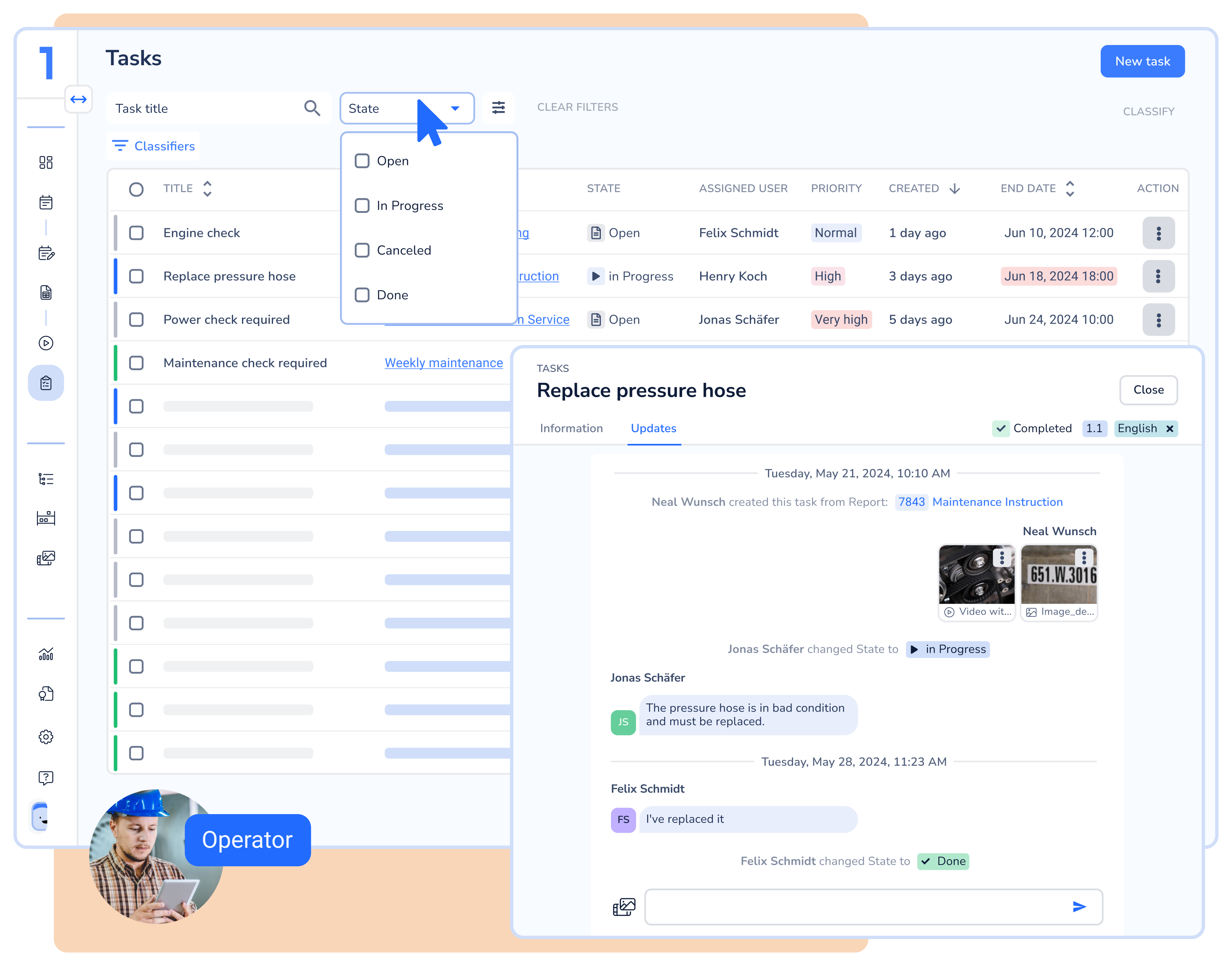
The reduction in training times by 67% with Operations1 results in annual savings of over € 2.2 million.
Head of Future Projects / REFA, POLIPOL
Faster achievement of target productivity
The POLIPOL Group uses digital checklists to reduce the training time for new employees.
Reduction of the training period from 12 to 3 months
Increasing employee satisfaction and productivity
Watch our demo video
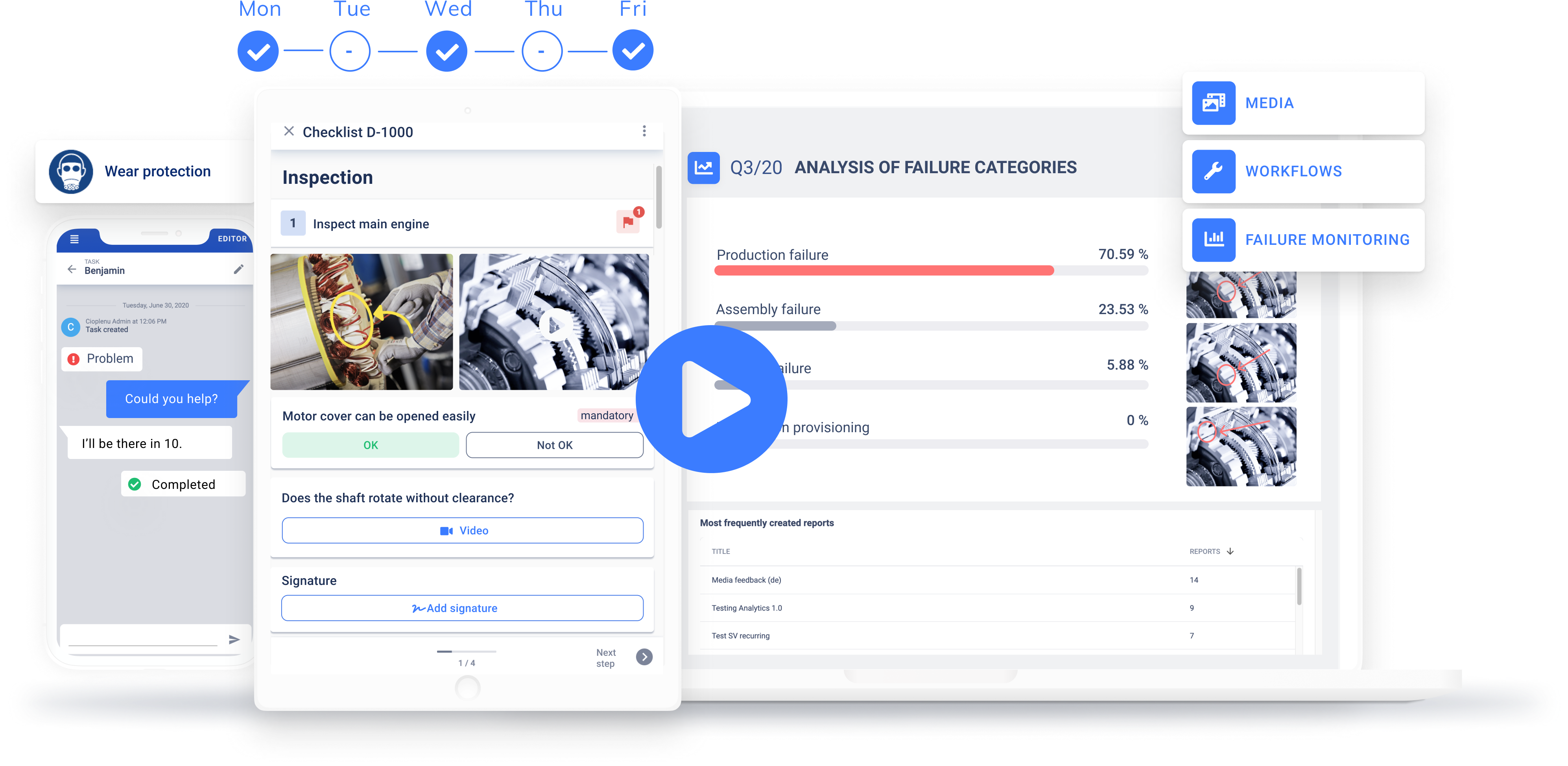
Get to know our software in just 7 minutes.
Fill out the form and get access to the video.