Leading companies use Operations1 for their operational processes
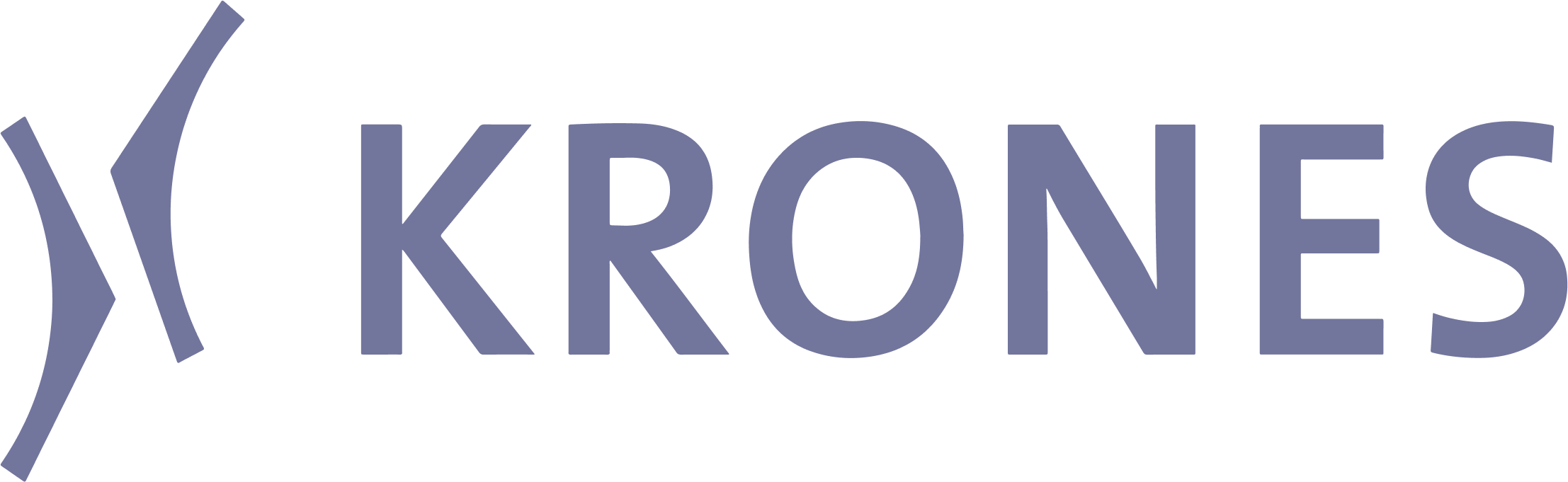
Logistics processes are still often handled and documented on paper. In incoming goods inspection and outgoing goods inspection, quantities and conditions of goods are thus recorded manually and findings are laboriously documented separately using a digital camera. With Operations1, you eliminate all complexity in the inspection process and increase your productivity.
Loss of goods or damage often occurs during transport. This can result in enormous goodwill costs or even complaints. Thanks to the seamless documentation of digital goods receipt and digital goods issue with Operations1, you always have control over goodwill and complaint services.
In Zeiten des Fachkräftemangels und stetigen Wandels ist es von enormer Bedeutung, Wissen zu sichern und Prozesse unabhängig von einzelnen Mitarbeitern sicher durchführen zu können. Mit Operations1 leiten Sie Ihre Mitarbeiter Schritt für Schritt sicher und intuitiv durch Ihre operativen Prozesse und verkürzen Anlernzeiten.
With Operations1's leading platform, you digitally map your goods receipt and goods issue processes end-to-end: from the creation of documents and the intuitive execution of inspection processes to the evaluation and generation of reports. In addition, connect Operations1 to your inventory systems such as ERP, MES or DMS.
Get an overview of the functionalities and application areas of Operations1.
No-code editor
Create your test documents in the drag-and-drop construction kit and choose from various interaction options
Integrated instruction
Use checklists and test instructions in one document and increase comprehensibility with images and videos
Version control & release
Share your documents digitally. All documents retain the same ID across different versions, enabling consistent analysis.
Change notifications
Change notifications in review documents are given to employees at the beginning of the process. Ask your employees for confirmation.
Multilingualism
Use your test documents in all common languages. You can even work on one protocol in different languages at the same time.
Central media library
Organize and edit media such as images and videos centrally. Provide a central point of truth for your documents.
Automatic test reports
You create test reports automatically after completing the test checklist and find them in no time using the search function.
Error image analysis
Analyze findings photos and videos systematically and thus increase the significance of your test findings.
Progress monitoring
Keep an eye on the progress of your inspection processes in a clear dashboard and react faster to incidents.
Offline capability
Use the software offline as well. As soon as you are online again, you can make your digital test reports centrally available.
Organisation
Use structure classes for your locations, teams, products or machines. This allows you to easily organize your logs.
Modular test protocols
Create test report templates and use them as modules. Finish the copy-and-paste work.
Order management
Schedule inspection tasks and attach relevant inspection documents. Ensure that all tasks are completed.
Analytics
Visualize your inspection statistics in a simple way and increase the significance with locally captured images and videos.
If-then conditions integrate if-then conditions to respond contextually and dynamically to inputs
Hardware connection Integrate external hardware such as scales, thermometers or other sensors into checklists in real time
We would be happy to show you the functions of Operations1 in an individual live demo and answer your questions.
There are many reasons to choose Operations1. The reasons most often cited by our customers are these.