Digital checklists are electronic versions of traditional paper-based checklists. They are used to record, organise and document tasks or steps in a process. Digital checklists provide an efficient way to ensure that operational work, such as assembly activities or maintenance tasks, are carried out properly.
Digital checklists for industry leaders
With the Operations1 software, you provide your employees with intuitive and flexible software that makes any inspection process simple, efficient and insightful. Watch our demo video to learn more about the functionality.
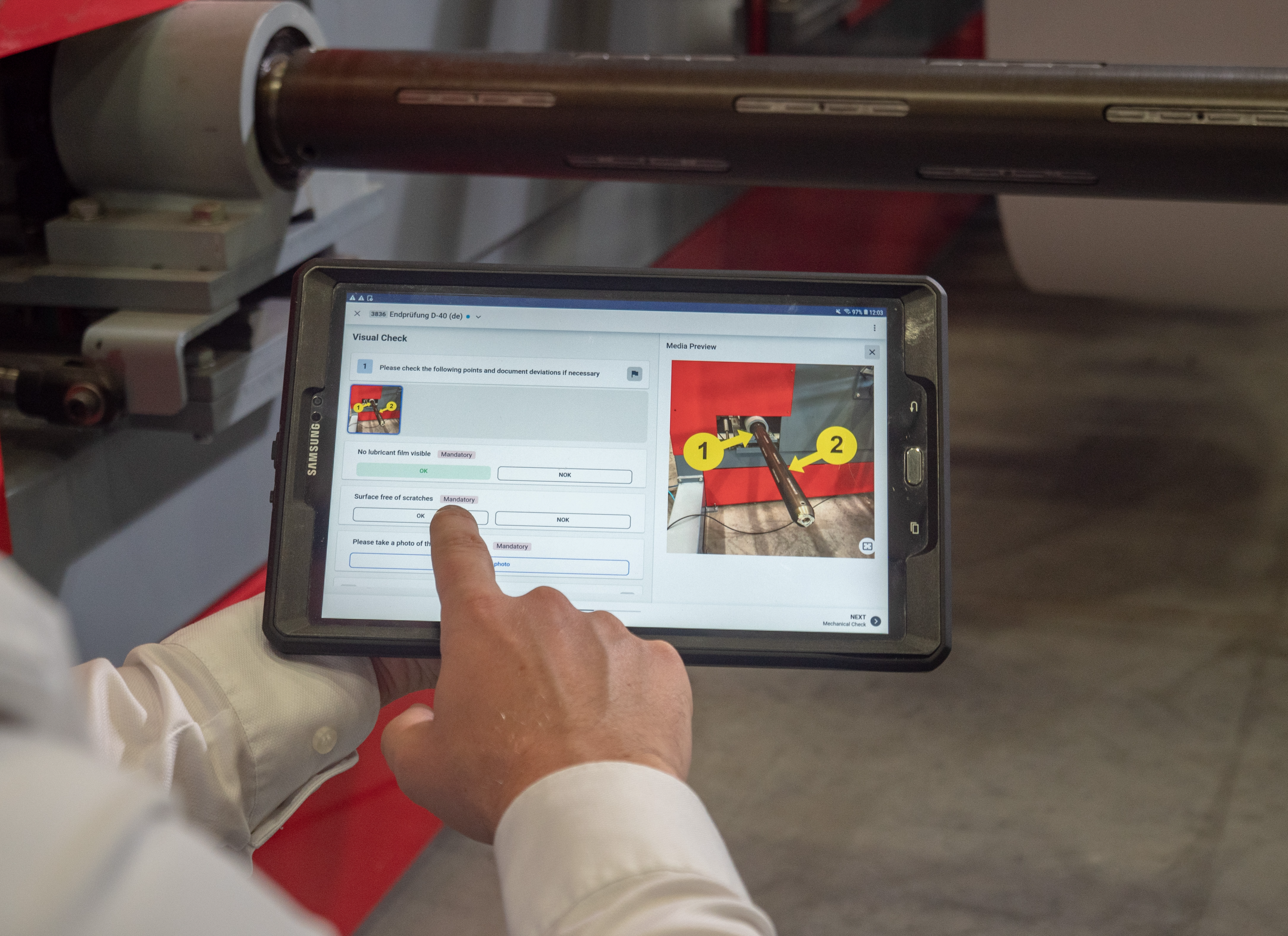
- +21% higher productivity
- -95% effort for documentation
- 100% transparency
Digital checklists for your teams
Whether in machine maintenance, quality inspection, incoming goods, audits or worker self-inspections in assembly: digital checklists are based on a wide range of use cases. Use Operations1 to create and organise digital checklists and reduce error rates and increase productivity.
See how you can digitize your checklists with Operations1
Get to know the software in just 7 minutes
Get an overview of the functionalities and application areas of Operations1.

Contact our experts!
Arrange a non-binding appointment with our team. Our experts will be happy to advise you on the next steps on your way to digital checklists based on your individual use case!
Features developed on the requirements of market leaders
Various interactions
Intuitive process guidance through predefined interactions such as checks, multiple choice, value comparison or sensor queries
Variant-compliant testing
Minimal documentation effort due to variant-compliant test protocols and modular design
Error image recording
Increased information content of findings through easy recording and editing of images and videos in the process
Automatic reports
No post-processing of test procedures necessary due to automatic report generation and archiving
Test logics
Intuitive process guidance for your employees for faster execution and valid information in your reports
Full integration capability
Order connection and feedback to all common ERP, MES and CAQ systems via standardized interfaces
Digital checklists: FAQ
What are digital checklists?
What are the advantages of digital checklists?
Updating and adaptation Digital checklists can be updated, adapted and edited quickly and easily. This enables flexible and agile adaptation of checklists to changing requirements
Cross-location use Digital checklists can be easily edited across different locations and countries on a common platform. This facilitates the establishment of a company-wide standard.
Automation and integration Digital checklists can be linked to automation functions to trigger specific actions. In addition, digital checklists can be seamlessly integrated with other digital systems to facilitate data exchange and optimise workflow.
Traceability and analysis Digital checklists enable detailed tracking. This allows progress to be monitored, performance statistics to be generated and analysis reports to be produced. This data can be helpful in identifying bottlenecks, making improvements and optimising workflow effectiveness.
Why do you need digital checklists?
Increasing efficiency Digital checklists enable processes to be carried out in a more efficient and structured way. They help capture, organise and check off key steps, greatly minimising potential errors or omissions.
Recurring activities Digital checklists provide a structured way to ensure that recurring processes are carried out consistently and accurately. By using digital checklists, organisations can improve quality assurance and ensure that no important steps are overlooked.
Traceability Digital checklists allow detailed tracking of tasks performed and provide clear evidence of compliance with regulations and standards. This can be helpful during audits, inspections or when meeting regulatory requirements.
Access and mobility With digital checklists, users have the ability to access them from different devices and locations. Mobile apps allow access on the go, which is particularly convenient when tasks need to be completed on site.